Modularisation: A modern process for project management
(→Automotive Industry) |
(→Modular Construction) |
||
Line 164: | Line 164: | ||
== Modular Construction == | == Modular Construction == | ||
− | [[File:Prefab.jpg|250px|thumb|right|Figure | + | [[File:Prefab.jpg|250px|thumb|right|Figure 7: 85% of industry players today are using prefabrication and modularization on some projects<ref name="Smart"></ref>]] |
Besides the automotive industry, the concept of modularization becomes relevant for other industries. Construction projects consist of a large number of activities that need to be set from the preliminary planning phases. They also have to be well-communicated through the several stakeholders as well as delivered in a cost-effective way. There are many factors that affect the outcome of a construction project and it is out of the scope of this report to outline each one of them. Therefore, this section focuses on how modularization is applicable to construction industry from a scheduling point of view. | Besides the automotive industry, the concept of modularization becomes relevant for other industries. Construction projects consist of a large number of activities that need to be set from the preliminary planning phases. They also have to be well-communicated through the several stakeholders as well as delivered in a cost-effective way. There are many factors that affect the outcome of a construction project and it is out of the scope of this report to outline each one of them. Therefore, this section focuses on how modularization is applicable to construction industry from a scheduling point of view. |
Revision as of 03:29, 29 September 2015
Nearly all projects are characterized by a certain degree of complexity and uncertainty. However, every project is unique and its success depends on various product development and management processes vital for the current rapidly changing business environment. Within this context, it has become increasingly important for companies with vast product portfolio to be able to manage the project complexity in order to increase efficiency and ensure competitive advantage in the long run.
Modularization is a process that breaks down complex systems into small and solvable parts. By dividing the product structure into modules, companies seek to optimize the way they function and operate in terms of transforming their products in a more flexible and accurate way. Modularization has gained momentum over the years as it helps projects achieve significant benefits by removing underperforming processes, products and parts. Since it is still a relatively new field outside the automotive and aircraft industry where it initially evolved, there is a growing interest in the development process of the modular patterns.
The purpose of this article is to explore the potential of modularization as a proactive strategy and product development tool for managing effectively the complexity derived from project and portfolio management processes. The article comes along with a detailed analysis on product modularization.
Keywords: complexity management; product modularity; modularization;
Contents |
History
This section refers to the evolution of modularization in order to get an understanding of the origins of the concept. The term module comes originally from the Latin term modulus and it is the diminutive of the term modus which means measure. Several meanings of the term module exist but the most important range from “a standard or unit for measuring” to a separable component that is “interchangeable” with others for assembly into units of different size, complexity or function.[1]
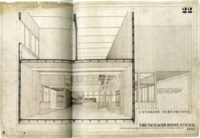
In architecture, modules were associated with the Bauhaus philosophy leading to the configuration of the so –called “building blocks” (Baukasten)[3] being individual functional units in buildings, easy to be assembled. Purpose was that modules were used as an arbitrary unit adopted to regulate the dimensions and proportions of parts of the building system for better design and coordination. As shown in figure 1, one extraordinary project example of industrialized building blocks was the industrialized modular housing “The Packaged House”[2] designed by well-known architects Konrad Wachsmann and Walter Gropius. It described a modular system comprising of a coordinated set of elements that allowed an infinite number of interactions for the final configuration and satisfied the housing needs for functionality, quality, uniformity and precision. However, it was not realized in practice, but the designs reflect the conceptualization of modularity.
Product Architecture
This section presents some background material in order to provide the context for subsequent analysis in product modularization. Considering the architectural structure of a system, such as its functionality, its function sharing, the clustering of elements and the interactions between the clusters of the system, is fundamental in order to achieve effective comprehension and management of the modular systems.
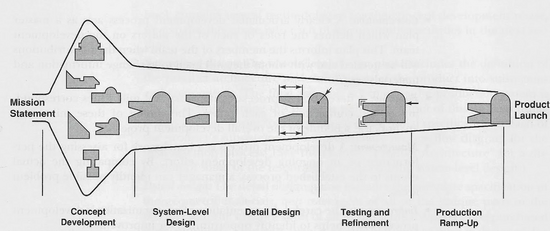
Product architecture is defined as the arrangement of functional elements, the mapping from functional elements to physical components and the specification of the interfaces among interacting physical components. Product architecture is determined early in the development process. Ulrich and Eppinger [4] provided a detailed analysis of the design process. The generic development process is composed of the following phases as shown in figure 2:
- concept development, which deals with defining the market segments, evaluating the feasibility of product concepts, developing the design concepts and testing the prototypes
- system-level design, in which a plan for product options and extended product family is developed, alternative product architectures are generated and major sub-systems and interfaces are defined
- detail design, which defines the part geometry, materials are chosen and assignment of tolerances takes place
- testing and refinement, in which reliability testing, life testing and performance is assessed as well as design changes are implemented
- Production ramp-up, in which the evaluation of early production output is done.
Integrated Architecture vs Modular Architecture
To give a deeper understanding of the importance of modularity in any kind of product system, it is important to make the distinction between the two types of product architecture. Modular architecture refers to a system composed of separate components that can be connected together. The opposite definition applies to integrated architecture, in which no clear divisions exist between components.
The following table summarizes the characteristics of modular and integrated architectures based on Ulrich and Eppinger[4].
“Products are rarely strictly modular or integrated; rather, they involve some degree of modularity.” [5]
Integrated Architecture | Modular Architecture |
A collection of components that implement some functions of a product is called a block. | A collection of components that implement some functions of a product is called a module. |
The functional elements of a product are implemented using more than one block | Same as an integrated architecture. |
A single block implements many functional elements. | A module implements one or a few functional elements in their entirety. |
The interactions between blocks are ill-defined and may be incidental to the primary functions of the products. | The interactions between modules are well defined and are generally fundamental to the primary function of the product. |
Product performance can be enhanced through an integrated architecture. | Product performance may not be enhanced by an modular architecture. |
Changing a block in an integrated product may influence many functional elements and require changes to several related blocks. | Changing a few isolated functional elements of a product may not affect the design of other modules |
Conventional Product Development
Traditionally the development of a product begins with the concept. As shown in figure 3, when the step of idea generation is completed, there is a sequential development of the design activities which ensures that technology and component development activities are resolved in every stage[6]. Components interfaces are not specified in detail in the early design phase, but later in the process. The process repeats until all components are fully developed. The output of the development process is the final product which defines as well the product architecture.
The drawback in this conventional process lies in the dependency of the development of components and interfaces. An alteration in the technology of a component will cause significant technical difficulties as well as uncertainties for the outcome of the final product. Since, all components are dependent with each other; a change in one part may be translated into a ‘domino effect’ of redesigning components or even worse replacing some of the component development processes.
Modular Products and Methods
This section focuses on modularity as the key to associate product development with modularization from the beginning of the design process. A short introduction is given for some of the methods that are typically being used in order to address modularization and structure the design process on the basis of modular synthesis.
Modular products refer to products, assemblies and components that fulfill various functions through the combination of distinct building blocks (modules) [7] Modules are different from building blocks in terms of the degree of possessed functionality compared to the final product. Building blocks are stand-ins for modules.[3]. They have a standardized interface which allows assembly by combinations, even though they are characterized by a very limited functionality compared to the construction of which they are a part. However, modules possess a significant amount of functionality and can configure the final product by using building blocks which contain specifications of both interface and functionality and allow the combination with other modules.[3]
The idea to design a system with a modular focus lies on the multiple benefits of making available to the customer a variety of choices regarding the final product. Many new products were made possible by creating flexible solutions through plugging in a new module to the existing one, leading to the creation of a large product portfolio among companies.
Modular Product Development
An important characteristic of product architecture is its modularity. Modular product architecture is the concept that defines the different components as modular elements and combines them together to make product families more flexible. A modular architecture allows changes to be made on one or a few elements without affecting the rest of the system. Therefore, it is essential that all functions of the product are split accurately in terms of elements being implemented by one module and with well-defined interractions between the different modules.[4].
Compared to the aforementioned conventional development process, modular product architecture fully defines the specifications of the component interfaces and the constraints regarding component development. In this model (figure 4), there is a complete structure in the flow of information which is well controlled with the decoupling points and defines the desired output prior to the development and detailed design of components. The main advantage is that product architecture is defined at design stage and does not change during development allowing the leveraging of multiple new product variations.
Modular Function Deployment (MFD)
Modular Function Deployment (MFD) is five-step process for translating the customer requirements into a modular architecture while taking into account the strategic intentions of the company. The method offers a systematic way for creating modular product design by investigating which part of the architecture should be modularized and which should be standardized according to the product properties. According to Errixon Gunnar's notes [8], the steps as shown in figure 5 are mentioned below:
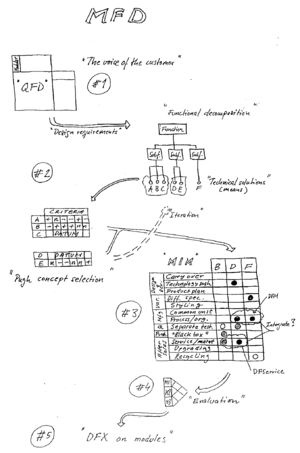
1. Clarification of product specifications using the Quality Function Deployment (QFD) matrix, with "modularity" put in as the first design requirement. QFD is a visual decision-making tool which is used on the basis of customer satisfaction, in terms of matching customer needs with existing and proposed measures of a process.
2. Functional decomposition, analysis of functions and selection of technical solutions
3. Identification of potential modules using the Module Indication Matrix (MIM). MIM is a fundamental part of MFD method and is mainly used for testing the interrelationships between module drivers and technical solutions. [9] It indicates which subfunctions could become modules. The causes of modularity are contained in the rows, and the partial subsystems are contained in the columns of the matrix.
The appropriate weighting scale is defined for evaluation of causes of modularity, containing the following values: 9 (strong cause), 3 (medium cause), 1 (insignificant cause). Evaluation of the weighted amount depends on how much a cause of modularity/specification affects the technical solution. At the end, the evaluations of the respective technical solutions are added up, and the technical solutions that achieve the highest number of points become candidates for modules. The technical solutions that achieve the lowest number of points could be related to one of the candidates for modules. The number of modules in a product is approximately equal to the value of the square root of the total number of parts in a variant of such product.
4. Evaluation of concepts by testing the interfaces between modules.
5. Improvements for each module
MDF method can be applied in product design across the entire life cycle of a product. Based on its simplicity, companies using the method can deliver satisfactory product results by considering systematically the customer requirements.
Design Structure Matrix (DSM)
The DSM is tool often mentioned in System Thinking: provides a compact and clear representation of a complex system and a capture method for the interactions/interdependencies/interfaces between system elements (i.e. sub-systems and modules). The DSM is used to structure the process because it has a lot of advantages in process modeling and analysis. Process modularization is the term that describes the activity of structuring the process in terms of a module and allows a manager to deal effectively with complexity problems in product development. The overall idea is to identify and capture the interdependencies across all design activities.
The Design Structure Matrix is also known as[10]:
- The dependency structure matrix
- The problem solving matrix (PSM)
- Design precedence matrix
The DSM is also a Project Management Tool[10] as it provides a project representation that allows for feedback and cyclic task dependencies. This is extremely important since most engineering applications exhibit such a cyclic property. This DSM project representation results in an improved and more realistic execution schedule for the corresponding design activities.
This method can be focused on improving the modular processes and can be combined with the aforementioned tools for product development. The advantages of the method are as follows[11]:
- DSM helps to reduce long reworks by reordering the tasks
- Challenges the status quo task ordering, while respecting task dependencies
- Facilitates understanding of the current processes
Application in Industry
This section focuses on the application of modularization which is related to almost any project, covering a wide range of industries. It gives a clear idea of how can projects be analyzed and modularized in order to support comprehension and modification during their life cycle.
Automotive Industry
In the automotive industry, the focus is on combining the common components, procedures and designs with the widest possible range of products. Modularization is playing a vital role in achieving this task in order to deal with the growing complexities associated with product portfolios, cost, time and quality. Maximising the use of commonnalities is one way of increasing manufacturing efficiencies.
Optimum efficiencies of scale and manufacturability, along with the widest possible variations to satisfy an ever-increasing variety of vehicle offerings can offer the design and development of modular vehicle stations.[12] Modular development of vehicle systems allows automakers to rely on the collective expertise of their component suppliers. For example, rather than having a supplier provide just seats, it can be called upon to supply the entire interior, including cockpit modules (incorporating the instrument panel, air bags, gauges, console and pedals), seat systems, door inners and the headliner. The idea is that the scale economies inherent in modular component supply will come from an increase in engineering efficiencies and labor productivity, lower material costs, investment costs, and greater speed to market.
When considering a new module strategy, it is essential to consider the following aspects[12]:
- Defining requirements of current and future vehicles projects;
- Identifying commonality across vehicles and defining module clusters and their specs;
- Specifying a base module and its variants and conducting cost/benefit analysis;
- Developing module fact sheet and fact book and building module hierarchy.
Modular Construction
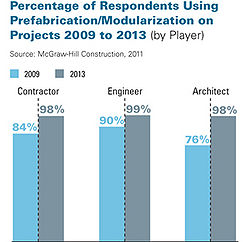
Besides the automotive industry, the concept of modularization becomes relevant for other industries. Construction projects consist of a large number of activities that need to be set from the preliminary planning phases. They also have to be well-communicated through the several stakeholders as well as delivered in a cost-effective way. There are many factors that affect the outcome of a construction project and it is out of the scope of this report to outline each one of them. Therefore, this section focuses on how modularization is applicable to construction industry from a scheduling point of view.
To deal with project uncertainty in construction, it is significant to consider all the available information. However, in the beginning of a project, as there is limited information available, uncertainty is further increased. To deal effectively with this problem, modularization needs to be considered by incorporating uncertainty in the scheduling process.[14]
In the building sector, modularization as a term is often associated with prefabrication, therefore when we refer to modular elements, we mean prefabricated elements. Prefabrication/modularization yields significant benefits for the industry players in terms of reduced project schedule.
It is not surprising that 85% of industry players today are using prefabrication and modularization on some projects—including 90% of engineers, 84% of contractors and 76% of architects – and by 2013 nearly all players (98%) expect to be using some prefabrication and modularization on some projects[13].
Modular smartphones
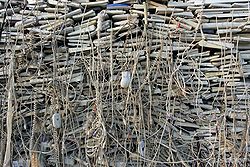
The concept is rather simple and is based on building your own perfect smartphone. “How modularization can be applied in the mobile industry?” It represents a rethinking of the mobile phone, a reshape of the mobile landscape. That is translated into a consumer product being a modular phone made from detachable blocks, which are all connected to the base of the phone.
“Why is it important?”
Mobile phones have a lifecycle of less than 2 years in developed countries which reflect that electronic devices are not designed to last very long. Electronic waste (e-waste) is considered as one of the fastest growing component of the municipal solid waste stream with approximately 20-50 million tons of electronic waste generated each year [15]. In general, the life cycle of the numerous electronic gadgets is getting shorter increasing the solid waste problem.
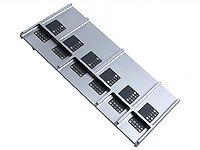
The design concept was originally conceptualized from Phonebloks as a means of reducing e-waste. Phonebloks main vision is to make a “phone worth keeping”. Google also wants to be part of software transformation by undertaking the Project Ara with the desired goal of reducing hardware prices and allowing any manufacturer/developer to contribute hardware modules and add-ons that could be sold via an online marketplace/platform [17].
Users will be able to choose their own smartphone experience by simply replacing the discrete blocks that affect negatively the performance of the phone and suit their desired needs. For example, if the phone is getting a little slow, the user can upgrade the block that affects the speed (this refers to the replacement of a component). If there is a broken piece, then it can also be replaced or updated with the latest version offered by the industry developers.
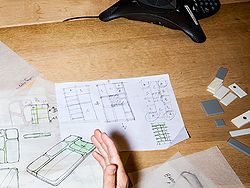
Modularization offers variety which contributes to meeting customer’s needs in the end. Modular smartphones offer vast opportunities with regards to customization, configurability and personalization. The user will be able to replace any block according to his present preferences (e.g. upgrade camera, swap/replace storage battery block, etc.) or even develop his own blocks.
Modularization is currently shaping the mobile industry by offering to the users the chance to create their own phone with easy and flexible modifications of the core components (processor, camera, etc.). However, modular smartphone as a product still remains a challenge to be solved. As all projects are complex, developing such a device is a wicked task as many factors should be taken into account in order to be both commercially and technically successful.
Benefits offered by Modularisation
Modularization is trying to optimize the product development processes by bridging the gap between product differentiation and economies of scale. Modularization offers a high variety of product standardization along with a flexible way of rapid product development in order to identify and fit customer needs. Some of the potential benefits of modularization according to a number of researchers [18] are summarized as follows:
- Economies of scale
Natural economies of scale arise as modules will be produced in relatively large quantities.
- Increased feasibility of product/component change
Since each module interface is strictly specified, changes can be made to a module independently of other modules, provided the interfaces remain within specifications.
- Increased product variety
The use of modules means that a great product variety can be achieved using different combinations of modules.
- Reduced order lead-time
Since modules are manufactured in relatively large volume, the logistics of production can be organized so as to reduce manufacturing lead time. Hence, the order lead time can be reduced.
- Decoupling tasks
Since the interfaces and modules have been standardized, their interfaces enable design tasks and production tasks to be decoupled. This decoupling can result in reduced task complexity and in the ability to complete tasks in parallel.
- The ease of product upgrade, maintenance, repair and disposal
Since a product is decomposed into modules, only certain modules need to be replaced when repair is done. For the same reason, upgrades, maintenance, and disposal are also made simpler.
6 RE Philosophy
As companies have to play a significant role in mitigating and adapting to climate change, a holistic modular approach needs to be considered in life cycle engineering. Modularization is increasingly becoming more and more relevant as a modeling technique that can assist companies achieve their sustainability goals.
“Sustainability has become a component of business success and project management is one of the ways to get there” (Joel Makower, the Oakland, California, USA-based author of Strategies for the Green Economy) [19].
By embedding sustainability into the product portfolio management, companies could deliver environmental, social and financial benefits to the business meeting the rising global demands covered in the concept of a Triple Bottom Line. [20]
As one of the most important properties of modules is their interchangeability, modularization addresses product life cycle concerns and should be integrated across the company’s product portfolio. Creation of an ecosystem with modules translates into a concept that has effects on the life cycle of the product. By modularizing a product, companies can identify the hot spots and integrate the environmental considerations where necessary. Modules, as being detachable units can be maintained, upgraded, reused, recycled offering a wide range of advantages and enhancing the objectives for life cycle thinking.
Modular design is more essential than ever as organizations can design for functionality and generate solutions modular enough to reduce the environmental impacts associated with the life cycle of the product. From the product life cycle perspective, modularization may also have relevant application to the eco-design principles and what is called the “6 RE Philosophy” .[21]
6 RE Philosophy | Applicability in modularization |
*Re-think the product and its functions e.g. how the product may be used more efficiently. | Modular design decomposes a product into separate modules. These modules can be designed taking into consideration energy efficiency requirements. Modular design can help by grouping into one module components that undergo similar life cycle processes.[22] |
*Re-duce energy and material consumption through a product’s life cycle. | Modular design decomposes a product into separate modules. These modules can be designed taking into consideration energy efficiency requirements. |
*Re-place harmful substances with more environmentally friendly alternatives. | Same concept as before. |
*Re-cycle. Select materials that can be recycled, and build the product in a way that it can be easily disassembled for recycling. | Modular design facilitates the recycling process by separating and sorting the variety of materials which require different recycling or disposal methods [23]. Therefore, material compatibility is necessary to be considered when designing in a modular way. |
*Re-use. Design the product so parts can be reused. | The life duration of components is not always the same, thereby some components may be usable again or re-manufactural upon retirement. Thereby, modular design allows to group components into easily detachable modules such that they can be easily reused or remanufactured .[23] |
*Re-pair. Make the product easy to repair so that the product does not yet need to be replaced. | Same concept as before. |
On this context, the configuration of a modular product that is part of an engineering system should be evaluated from the early design stage – representing the most crucial phase for the system to be properly developed and its functions to be determined. Organizations are called to transform their operations, products and services in order to contribute to sustainable development and climate change.
It is important to note that modularization can be a way for organizations to deliver more responsibility towards the realization of environmental advancements. Organizations that implement modularization within their operations, not only can manage more effectively the assessment of the environmental impacts of their products but can potentially achieve more economic benefits, both in the product and also in the organization.
Limitations and Further Development
The purpose of adopting a modular product strategy lies in the number of important benefits that can be achieved such as flexibility, mass customization, greater product variety, faster technological upgrade of products, cost reduction, etc.
Modularization is quite broad topic and cannot be clustered in a procedure or method, therefore this article was primarily limited by the type in order to control the flow to a certain level and keep the reader's focus. A greater depth of information may have been obtained by analyzing both product and process modularization, as well the combination of these two. Considering multiple cases where modularization has been viewed as a solution to customer needs may be useful to understand better the connection.
This article did not only seek to investigate the overall effectiveness of modularization in product development as a means to supporting companies decide on modular product strategies. This article gives an account of these and provides insights into several aspects of modularization as a concept in terms of project and portfolio management. Taking into account the necessary requirements for all stages of a product’s life cycle, it makes easy for modularization to be flexible and modified, in case complexity increases or a requirement changes.
Furthermore, comprehension is one of the most important limiting factors for the efficient integration of modularization. Not all organizational structures can adopt product modularization. As for a company’s product portfolio to benefit from a modular strategy, the concept of modularization described in this article needs to be implemented from the beginning to all components, analyze the product architecture, define the design principles for the organization, make use the modular-based processes/techniques throughout the entire organization.
Finally, modularization is still under development and there is still room for improvement in terms of making modularization simpler and more flexible.
Quoting Edsger Dijkstra, “Simplicity is a great virtue but it requires hard work to achieve it and education to appreciate it. And to make matters worse: complexity sells better”.
It has been shown in this article that modularization is not only applied in one industry, however there can be taken many different approaches with regards to its application. It is rather a concept than a process, however it is recommended as a tool for solving complex problems and managing specific indrustry situations. Further improvements require all industry players to collaborate towards an integrated use of modularization. Operational implementation and coordination of processes should also be considered.
Annotated Bibliography
Lampel, J. and Mintzberg, H., (1996) "Customizing Customization," Sloan Management review. Fall 1996, pp. 21 – 30 Erixon, G. (1998) Modular Function Deployment - A Method for Product Modularisation, Doc. Thesis., KTH, Dept. of Manufacturing systems, Stockholm, Sweden. Blackenfeldt, M.. (2001) Managing complexity by product modularisation: Balancing technology and business during the design process , Doc. Thesis, KTH, Dept. of Machine Design, Stockholm, Sweden. [1] The Option Value of Modularity in Design, Harvard Business School
References
- ↑ "module." “Online Etymology Dictionary”. Douglas Harper, Historian. 19 Sep. 2015. <Dictionary.com http://dictionary.reference.com/browse/module>.
- ↑ 2.0 2.1 Alicia Imperiale, Temple University “An American Wartime Dream: THE PACKAGED HOUSE SYSTEM OF KONRAD WACHSMANN AND WALTER GROPIUS”, 2012 ACSA Fall Conference, 39-43.
- ↑ 3.0 3.1 3.2 Miller, TD & Pedersen, PEE 1998, “Defining Modules, Modularity and Modularization: Evolution of the Concept in a Historical Perspective”. IKS, Lyngby.
- ↑ 4.0 4.1 4.2 4.3 Karl T. Ulrich and Steven D. Eppinger, “Product Design and Development”. First Edition, Mcgraw-Hill College, 1995.
- ↑ Chun-Che Huang*, 2000/05, "Overview of modular product development, (Invited review paper)" Proceedings of the National Science Council, R.O.C., Part A: Physical Science and Engineering, Volume 24, Number 3, 2000, pp.149-165.
- ↑ 6.0 6.1 6.2 Kenneth Eskildsen (2011) “Modularization” International Technology Management, Aalborg Universtity – Copenhagen (2011).
- ↑ PahL G. and Beitz, W. (1988). “Engineering Design: A Systematic Approach”, SpringerVeriag, NY, Edited by Ken Wallace.
- ↑ 8.0 8.1 Gunnar Erixon: “Modular Function Deployment – A Method for Product Modularisation”, Ph.D. Thesis [1], The Royal Institute of Technology, Stockholm, 1998. TRITA-MSM R-98-1, ISSN 1104-2141, ISRN KTH/MSM/R-98/1-SE.
- ↑ K.Osman, N. Bojčetić and D. Marjanović, “Implementation of Modular Architecture of Cooling Generators”, International Design Conference - Design 2008, Dubrovnik - Croatia, May 19 - 22, 2008., 465-474.
- ↑ 10.0 10.1 DSMweb.org, “Design Structure Matrix (DSM)” , http://www.dsmweb.org/ Retrieved on 28 September 2015.
- ↑ Ming Fai, “DSM: A useful tool for process improvement efforts” , http://workitsmart.blogspot.dk/2012/12/dsm-useful-tool-for-process-improvement.html Retrieved on 28 September 2015.
- ↑ 12.0 12.1 12.2 Ralf Kalmbach, Mahesh Lunani, "Implementing a Modularization Strategy", Roland Berger Strategy Consultants, Retrieved 28 September, 2015, http://66.192.79.249/columns/0405strat.html>
- ↑ 13.0 13.1 John Gudgel, (results from) “SmartMarket Report: Prefabrication and Modularization: Increasing Productivity in the Construction Industry”, McGraw-Hill Construction, (2011) Retrieved September 28, 2015. http://www.dodge.construction.com/Analytics/marketdynamics/2011/jul_feature.asp
- ↑ EnviroSep, “Improve Construction Schedule and Impress Your Client”, Retrieved September 28, 2015.http://www.envirosep.com/2014/04/improve-construction-schedule-impress-client/
- ↑ 15.0 15.1 Greenpeace International, “The e-waste problem”, Retrieved September 28, 2015 http://www.greenpeace.org/international/en/campaigns/detox/electronics/the-e-waste-problem/
- ↑ 16.0 16.1 Wired.com, “Three Big Ideas in Google’s Modular Phone That No One’s Talking About”, Retrieved September 28, 2015 http://www.wired.com/2014/04/google-ara-new-deal/
- ↑ Pocket-lint, “Google's Project Ara modular smartphone: Everything you need to know” Retrieved September 28, 2015. http://www.pocket-lint.com/news/127564-google-s-project-ara-modular-smartphone-everything-you-need-to-know
- ↑ Schuh, G.; Rudolf, S.; Vogels, T. (2014) ‘Development of Modular Product Architectures’ Procedia CIRP vol. 20 p. 120-125.
- ↑ Project Management Institute, “The Bottom Line on Sustainability”, Retrieved September 28, 2015, https://www.pmi.org/Business-Solutions/~/media/PDF/Business-Solutions/The%20Bottom%20Line%20on%20Sustainability_FINAL.ashx
- ↑ 1 Elkington J. Cannibals With Forks: The Triple Bottom Line of 21st Century Business. Capstone, 1997/ New Society, 1998.
- ↑ UNEP Guide to Life Cycle Management
- ↑ Umeda, Yasushi; Fukushige, Shinichi; Tonoike, Keita; Kondoh, Shinsuke (2008) ‘Product modularity for life cycle design’, CIRP Annals - Manufacturing Technology vol. 57 (1) p. 13-16
- ↑ 23.0 23.1 Gu, P.; Sosale, S. (1999) ‘Product modularization for life cycle engineering’, Robotics and Computer-Integrated Manufacturing, vol. 15, (5), p. 387-401