Continuous Improvement (CI)
(→Abstract) |
|||
(103 intermediate revisions by one user not shown) | |||
Line 1: | Line 1: | ||
+ | ''Written by Xenofon Apostolou'' | ||
== '''Abstract''' == | == '''Abstract''' == | ||
− | |||
− | = | + | Continuous Improvement (CI) is a transformation philosophy that is correlated directly with certain methodologies and strategies executed that provide with constant enhancement and development of services, products, and processes <ref name="CIbook2" /> . Also, the possibility of applying CI in every company that is eager to implement the transformation philosophy makes it a broad concept. Hence, there are multiple systems, methods, philosophies, tools, techniques, theories and strategies by which Continuous Improvement can be achieved. Due to the length limitation of this article, the Kaizen philosophy/method and the Just-In-Time production system have been chosen for investigation. The correlation of those with application in Project, Program or Portfolio management is high due to the consideration of Kaizen as a long-term Project having as deliverables a complete transformation in the company by eliminating the old and traditional concepts and granting significant improvement in product/service quality in addition to reducing costs. The concept of a Program is exhibited through application of the Kaizen activities. All activities correlated with Kaizen compose a portfolio that needs to managed effectively as these need to executed properly in a manner of time, person in charge and area of application. Methods such as Six Sigma, Theory of Constraints (ToC) and Agile also possess major significance in applying Continuous Improvement but will not be examined in this article. Firstly, a historical analysis along with defining Continuous Improvement is provided to comprehend the base level and the historical evolution. Secondly, the Kaizen theory (concepts) and application (systems) are investigated thoroughly followed by an example to clarify any gaps. Thirdly, the limitations are explained to understand the benefits and drawbacks that come along with it as well as the ideal conditions in regard to when to use Kaizen. Lastly, the assessed annotated bibliography is specified through making individual remarks for each of them as they provided with important information that led to the composition of this article. |
− | '' | + | __TOC__ |
+ | |||
+ | == '''History and definition''' == | ||
+ | [[File:Shewhart cyclical concept(1).jpg|right|thumb|200px|'''Figure 1''': Shewhart’s cycle <ref name="Circle"/> ]] | ||
+ | Continuous Improvement (CI) is a transformation philosophy that is correlated directly with certain methodologies and strategies executed that provide with constant enhancement and development of services, products, and processes <ref name="CIbook2" />. It also aims at maximizing cost reduction for companies and businesses and eliminating root causes of problems. This concept often named as Continuous Improvement Process (CIP) is implemented to increase the company’s profit and competitiveness in the short term in addition to sustain these in the long term <ref name="CIbook2" />. [https://en.wikipedia.org/wiki/W._Edwards_Deming William Edwards Deming] (October 14, 1900 – December 20, 1993) is generally considered the father of Continuous Improvement, however the person behind the first breakthrough correlated with CI was [https://en.wikipedia.org/wiki/Walter_A._Shewhart Walter Shewhart]. He is considered one of the first pioneers of Total Quality Management (TQM) <ref name="Shewhart"/>. He developed the straight-line process in 1939 in terms of statistical control for specification, production and finally inspection regarding quality control (QA) for products. The method was transformed to a circular model called Shewhart’s cycle the same year <ref name="Shewhart"/>. | ||
+ | The model was then modified by William Edwards to the Deming Wheel that himself presented in 1950 to an eight-day seminar in Japan sponsored by the Japanese Union of Scientists and Engineers (JUSE) <ref name="Circle"/>. | ||
+ | [[File:Deming's wheel (2).jpg|center|thumb|350px|'''Figure 2''': Deming's wheel <ref name="Circle"/> ]] | ||
+ | [https://en.wikipedia.org/wiki/Masaaki_Imai Masaaki Imai] the famous inventor of Ky-zen (good-change in English) states in his book ‘’ Kaizen (Ky’zen), the Key to Japan’s Competitive Success’’ that Japanese executives reformed Demings wheel to the Plan-Design-Check-Act (PDCA) tool <ref name="Imai"/>. Deming, nonetheless, kept himself distant from the tool and after thirty years in 1980 he introduced the Plan-Do-Study-Act (PDSA) cycle <ref name="Circle"/>. | ||
+ | While Continuous Improvement can be broad and abstract, it has its roots in manufacturing. Other concepts that it can be affiliated to are quality control, operations analysis, management and mostly anything that includes processes. Finally, CI is defined by Aristide van Aartsengel and Selahattin Kurtoglu as ''‘any state of “being” beyond the state of “becoming.” It is the highest stage of maturity that an enterprise business as a whole can attain. Attaining this highest stage of maturity does not happen overnight; it takes time!''' <ref name="CIbook1" /> | ||
+ | |||
+ | == '''Kaizen''' == | ||
+ | ==='''Introduction'''=== | ||
+ | |||
+ | Kai-zen (change-good translates to improvement in Japanese) is defined both as a philosophy and a method. It originates from Masaaki Imai in Japan while being one of the most famous CI methods globally in lean production. This philosophy can be applied to all corporate functions in a company although being closer to design, production and market <ref name="Imai"/>. | ||
+ | [[File: Kaizen,design,production, market.jpg|center|thumb|350px|'''Figure 3''': Position of Kaizen in corporate functions <ref name="Imai"/>]] | ||
+ | Masaaki Imai defines it as ''our way of life be it our working life, our social life, or our home life deserves to be constantly improved'' <ref name="Imai"/>. It targets ongoing/continuous improvement involving all levels of hierarchy (top management to workers) <ref name="Imai"/>. The development of Kaizen is gradual or inch by inch rather than executing major steps. In addition, it does not require huge investment capitals yet calls for extensive continuous effort and considerable commitment that can entail positive results. Lastly, the management principles that are commonly known as Total Quality Control (TQC), Zero Defects (ZD), Just-in-time (JIT) and Kanban (signboard) are used constantly under the Kaizen way of life and are important tools for the application of Kaizen. | ||
+ | |||
+ | ==='''Important concepts'''=== | ||
+ | |||
+ | Management should be in state to implement the following significant concepts to apply the Kaizen strategy by introducing a very concise policy statement. <ref name="Gemba"/> | ||
+ | |||
+ | *'''Kaizen and Management'''. | ||
+ | |||
+ | The two important functions that management should attend regarding Kaizen is maintenance and improvement. Maintenance is achieved through executing activities that sustain the current situation as well following the SOPs (standard operating procedures). On the other hand, improvement relates to all the actions taken to enhance the current standards. Moreover, improvement is classified as Kaizen or Innovation. The former refers to minor constant improvements over time, which is the philosophy followed in the east, while the latter is a result of breakthrough investment in technology or equipment followed mostly by the west. | ||
+ | |||
+ | *'''Process vs Result'''. | ||
+ | |||
+ | Another important principle is the consideration of imperfection in processes in terms of always having space for improvement. In addition to the process-oriented mentality adopted, Kaizen strictly considers that firstly a process must be improved to get better results. This approach should accompany every tool application. | ||
+ | |||
+ | *'''Executing the Plan-Do-Check-Act (PDCA) cycle and Standardize-Check-Do-Act (SCDA) cycle'''. | ||
+ | |||
+ | Kaizen uses two very identical and important tools to serve as maintaining and improving factors regarding the standards. As any process must be initially standardized to be in a state of improvement, the use of the SCDA cycle achieves stabilization in the process. In the famous words of Taiichi Ohno ‘Where there is no standard, there can be no Kaizen’. In other words, the SDCA cycle is applied when there is no available standard. While the outcome of a process can be known, lacking standards results in inconsistency and instability in the process itself. Hence, the SDCA cycle contributes to the creation and maintenance of standards and processes. | ||
+ | [[File:SDCA cycle.jpg|center|thumb|350px|'''Figure 4''': SDCA cycle <ref name="Gemba"/> ]] The figure above explains the SDCA cycle. ‘Standardize’ refers to establishment of the standards that are to be achieved. This action is executed collectively by all employees responsible for the task or the process. The formal writing of the standard is done by the supervisor or the team leader. Next, the step ‘Do’ refers to the execution of the second step, namely the standard <ref name="Gemba"/>. After that, the evaluation of the previous application in terms of meeting expectations is ‘Check’. In the book ‘Gemba kaizen a common-sense approach to a continuous improvement strategy’ <ref name="Gemba"/> when a deviation from the standards occurs, this procedure is also followed by questions as ‘Did it happen because we did not have a standard?’, ‘Did it happen because the standard was not followed?’, ‘Did it happen because the standard was not adequate?’. These questions lead to proper establishment of the standards. Lastly, in ‘Act’ reviewing, assessment of the deviations and implementation of the corrections occurs. | ||
+ | |||
+ | [[File:PDCA improvement.jpg|center|thumb|350px|'''Figure 5''': PDCA cycle <ref name="Gemba"/> ]] | ||
+ | |||
+ | Consequently, when the current process or task has been standardized and is in a state of control, the execution of the PDCA cycle occurs to improve the current performance of the process and create new standards for application. Firstly, ‘Plan’ is the action taken regarding the initialization of the target for improvement. ‘Do’ and ‘Check’ are performed in the same manner as in SDCA cycle. Finally, ‘Act’ is the wide-scale application to prevent the initial problem from happening and/or defining the goals for new improvements <ref name="Gemba"/>. | ||
+ | |||
+ | *'''Prioritizing quality'''. | ||
+ | |||
+ | Out of the three most important KPIs of quality, cost and delivery (OCD) in a product or a service handling, quality should always possess the strongest priority. This is an immediate result of the importance of delivering high quality to customers in regard to enhancing competitiveness due to that. Making compromises in delivery times or costs should not be considered as a solution. That, however, requires resilient dedication from the management as the aforementioned options can be considered as alternatives risking as such the assurance of the high-quality deliverables of the product and the company’s life. <ref name="Gemba"/> | ||
+ | |||
+ | *'''Speak with data'''. | ||
+ | |||
+ | Kaizen identifies itself as a problem- solving procedure. The gathering along with the analyzation of the data must be implemented to fully recognize the situation and be in a state for the situation to be solved correctly by the company. Intuitive approaches such as hunches or feelings are not considered relevant thus lacking science in approaching the problem. The starting point in improvement begins in the collection of data clarifying the focus area that needs to be addressed. <ref name="Gemba"/> | ||
+ | |||
+ | *'''Considering the customer as the next process'''. | ||
+ | |||
+ | The axiom ‘the next process is the customer’ <ref name="Gemba"/> means that the next process should be always considered for the customer. All tasks are a series of processes and every process has a supplier and a customer. As customers two types are identified. Internal which are within the company and external which belong out in the market <ref name="Gemba"/>. The majority of people working in a company will relate to internal customers. The axiom mentioned before creates a commitment that a defective part or handling of inaccurate information should never proceed to the next process. The end-result concluded by following this concept is that the external customer receives a high-quality product or service. | ||
== '''Application''' == | == '''Application''' == | ||
− | '' | + | ==='''Important kaizen systems'''=== |
+ | To achieve the kaizen strategy, the following systems should be introduced and executed. | ||
+ | *'''Total Quality Control/Total Quality Management (TQC/TQM)'''. | ||
+ | |||
+ | These two systems do not only affiliate as quality-control activities but as strategies to help management in augmenting competitiveness and profitability by improving all aspects of the business. In these systems quality inherits the highest importance. However, there are more variables to be considered as cost and delivery. Furthermore, everybody is involved in the organization by the TQC/TQM systems and that is expressed by the ‘T’ which means total. On the other hand, ‘C’ expresses control or process control. The key processes must be realized and then establish control and continuous improvement in order to achieve better results. The management should set up a plan to check the process versus the result to improve the process, not to criticize the process judging from the result. Activities that belong to TQC/TQM are policy deployment, building quality assurance systems, standardization, training and education, cost management and quality circles. <ref name="Gemba"/> | ||
+ | |||
+ | *'''Just-in-Time Production System'''. | ||
+ | |||
+ | This system was originally created by [https://en.wikipedia.org/wiki/Taiichi_Ohno Taiichi Ohno] at Toyota Motor company. It is defined as ''‘bringing the exact number of required units to each successive stage of production to the appropriate time’'' <ref name="Imai"/>. The purpose of it is the direct elimination of all kinds of waste (Muda) or non-value adding activities while structuring a lean production system with the ability to deal with uncertainties regarding customer quotes. Muda can be classified as: | ||
+ | |||
+ | '''1.''' Waste time spent at the machine. | ||
+ | |||
+ | '''2.''' Waste involved in the transportation of units. | ||
+ | |||
+ | '''3.''' Waste in processing. | ||
+ | |||
+ | '''4.''' Waste in taking inventory. | ||
+ | |||
+ | '''5.''' Waste of motion. | ||
+ | |||
+ | '''6.''' Waste in the form of defective units. | ||
+ | |||
+ | '''7.''' Overproduction. | ||
+ | |||
+ | Kanban is used as a communication tool in this system. Kanban also known as signboard, is a visual card attached to each box of parts headed to the assembly line. Upon delivering all components, is returned to the previous task or workstation serving as a record of implemented work and ordering of new parts. Moreover, principles included in the system is to never pass defective work to the next station along with ‘Jidhoka’ <ref name="Imai"/> which inherits tasks such as the closure of the line whenever a defective part is identified. Toyota has achieved that via possessing machines with automatic stop mechanisms <ref name="Imai"/>. For example, ''‘Throughout the Toyota plants, the visitor will notice large signboards hung from the ceiling. When an individual machine has stopped, the machine's identification number is lit up on the signboard so that the operator knows which machine needs attention’''<ref name="Imai"/>. The advantages of this system relate to shortened lead-time, reduced time spent on non-process work, reduced inventory, better balance between different processes and problem clarification<ref name="Imai"/>. Representing as such the efforts for continuous improvement in production and inventory resulting in Toyota having a capital turnover ratio ten times bigger compared to American manufacturers. <ref name="Gemba"/> | ||
+ | |||
+ | *'''Suggestion System for Improvements'''. | ||
+ | |||
+ | Another significant system that is adopted in kaizen, is the fact that there is a suggestion system incorporated in the company’s structure. Distribution of rewards for employees that try to tackle daily problems and obtain savings from these suggestions or meet managerial criteria is a commonality. These criteria can be grouped to Process-Oriented and Results-Oriented as mentioned in the Kaizen book <ref name="Imai"/>. The Process-oriented criteria is a mirroring of the significance being given in effort by the Japanese culture except than outstanding results. Process-Oriented criteria can be attendance in meetings, willingness of participation, total number of problems solved and report submissions. | ||
+ | |||
+ | *'''Total Productive Maintenance'''. | ||
+ | |||
+ | TQM was introduced as a system before referring to the overall improvement of performance and quality. Now TPM stresses the importance of improving equipment quality. Simplified, is about ‘''maximization of equipment efficiency through a total system of preventive maintenance spanning the lifetime of the equipment''’<ref name="Gemba"/>. TQM includes everyone related to the company, however TPM correlates with people involved in the plant. A major continuous improvement activity affiliated with the system is the 5S which is analysed below. | ||
+ | |||
+ | '''1.''' Seiri (Sort): Distinguish between necessary and unnecessary items in the Gemba and discard the latter. Start by removing all items from your work area. Inspect the equipment and identify those items that are critical to the success of the function performed at the workstation. Eliminate any duplicates, unnecessary equipment, infrequently used items, and trash. Identify the non-essential items as either waste or valuable but not critical. Store the non-critical items outside of the workstation area. This saves time, space, and labour costs, while enhancing productivity. <ref name="Gemba"/> | ||
+ | |||
+ | '''2.''' Seiton (Straighten): Arrange all items remaining after seiri in an orderly manner. Whatever equipment is deemed critical to the operation must now be organized. Assign positions for all equipment, work in progress, and raw materials, keeping ease of reach, identification, and proximity to work surface in mind as you do. The goal is to maximize the efficiency of the workstation layout. On a smaller scale, it’s the same concept as warehouse layout. The most frequently used tools should be the most convenient to grab. This eliminates wasted time from excess motion and searching. <ref name="Gemba"/> | ||
+ | |||
+ | '''3.''' Seiso (Scrub): Keep machines and working environments clean. Keep everything clean, every day. Doing this keeps things ready to be used when needed. A clean workspace is a productive workspace, and Seiso literally means “to clean or shine.” Clean the floors, the walls and the equipment, and ensure all items are restored to their designated place. Make sure the workstation is well lit. This should be a part of your daily tasks and should not be postponed until idle time is available. <ref name="Gemba"/> | ||
+ | |||
+ | '''4.''' Seiketsu (Systemize): Extend the concept of cleanliness to oneself, and continuously practice the preceding three steps. Make a habit of properly maintaining correct procedures to avoid backsliding. Implementing these steps is a continuous process. It is important to ensure that they are done each day to prevent slipping into old habits. Commit to performing these steps every shift and make sure that any changes to your product or process are compensated for at your workstation and problems are alleviated as quickly as they are created. <ref name="Gemba"/> | ||
+ | |||
+ | '''5.''' Shitsuke (Standardize): Build self -discipline and make a habit of engaging in 5S by establishing standards. Ensure conditions of work area do not return to the original, disorganized state. Make the previous three S’s part of your standard procedures each day. Implement them with the help of signs, banners, shadow boards, tool holders, etc. Make sure all workers understand their responsibilities and are empowered to perform all of the tasks. <ref name="Gemba"/> | ||
+ | [[File:The_five_steps_of_5S.jpg|center|thumb|350px|'''Figure 6''': The five steps of 5S <ref name="Gemba"/> ]] | ||
+ | |||
+ | *'''Policy Deployment'''. | ||
+ | |||
+ | The process of 'hoshin kanri'<ref name="Gemba"/> in Japanese or Policy Deployment refers to setting a long-term strategy that breaks down to medium-term and annual strategies. The strategy should pass all levels of management until it reaches down to the shop floor or front-end. However, the strategy should include all the necessary actions or activities for the implementation of it as it cascades down to the lower levels of management. An example of policy deployment is setting a target of cutting costs by ten percent. The front-end or shop floor must acquire the activities that lead to reducing inventory, increasing productivity and improving the line configurations leading to the achievement of the target. | ||
+ | |||
+ | *'''Small-Group Activities'''. | ||
+ | |||
+ | Kaizen in group work is executed via Small-Group Activities. Some examples of the activities are Zero Defects (ZD), Mini Think Tanks, Safety Groups, Productivity Committees and the most popular one is the Quality Circles (QC). These activities present a nonconfrontational and informal way of solving problems while proposing improvements <ref name="Imai"/>. The groups are formed to tackle problems or carry out tasks in a workshop environment while using statistical tools such as histograms, pareto charts, cause and effect diagrams, run charts, scatter diagrams, flow charts and control charts. In addition, the PDCA cycle is executed, however, as not only the identification of problems but also the identification of root causes takes place there is another PDCA cycle implemented in the 'Do' step of the first one. This defines the procedure as problem-solving and decision-making one. | ||
+ | [[File:QC.jpg|center|thumb|350px|'''Figure 7''': PDCA inside PDCA <ref name="Imai"/> ]] | ||
+ | Moreover, in Japanese plants there is always a workplace situated for the execution of these activities. QC were invented in 1962 as studying groups firstly, having foremen and workers study together to get knowledge and techniques on quality control<ref name="Gemba"/>. Now, it possesses a more problem-solving structure. | ||
+ | |||
+ | == '''A Kaizen example''' == | ||
+ | There are numerous ways by which Kaizen can be applied in a company, a scenario will be proposed in a company that is expected to have an increase of twenty percent in demand. Accordingly, the head of production or the plant manager wants to upgrade the productivity rate by twenty percent to meet the demand. He decides to organize a two-day Kaizen event on line ‘1’ that has a bottleneck structuring a clear target for achievement. Hence, he gathers key employees (stakeholders) such as line managers, supervisors, staff, team leaders and operators. To keep the production running and not distort customer satisfaction he decides to organize these events during the night between shifts. Meetings will be conducted beforehand to discuss the application of Kaizen in the work area referring to the 'Plan' step. After that the new application will be explained to the operators. Then, the team members make notes upon the new operation implemented and come up with ideas and structure a plan to execute them. Small-Group Activities such as QC can take place. A pareto or a cause-effect diagram can be used along with the seven statistical tools to develop solutions. The team leader decides among the ideas which one to implement the next day. The operators get the instructions of the plan, implement them ('Do' step) and are strongly encouraged to speak up regarding difficulties they face in their work ('Check' step). That is the input that results to the finalization of the plan ('Act' step). When the plan is finalized then there is a new standard for the process. The solutions for debottlenecking the line could be to re-build the line, so it supports the takt time, to eliminate the Muda (waste) from the plant following Taiichi’s Ohno Just-in-Time system to comprehend the categories of it and then applying the 5S system to reduce them. Develop work procedures that can be written into standardized work including conditions of work, handling of parts and combination of motion. All the aforementioned are related to the 'Act' step. Then the application of the proposed solutions will trigger a new iteration for SDCA/PDCA cycles. Hence, continuously implement the SDCA cycle to stabilize the new process and create the new standard. When that is done proceed with the application of the PDCA cycle to improve the current standard way of implementing and running of the line. Below the outcome of the whole process is illustrated. | ||
+ | [[File:KAIZENline1.jpg|center|thumb|650px|'''Figure 8''': Kaizen implementation <ref name="Imai"/> ]] | ||
+ | |||
+ | That is just a simple example of how Kaizen can be applied in a manufacturing plant. There are many different ways of applying Kaizen and it's respective systems and tools. The choice of those, length of training, structuring of the plan and solutions can very much differ depending on the size the target needed to be achieved. Nonetheless, Kaizen always proposes the application of small and steady targets. | ||
== '''Limitations''' == | == '''Limitations''' == | ||
− | + | Kaizen can be applied everywhere there are operations, processes and tasks in all corporate functions. The most important aspect it improves is product/service quality however, there are more aspects that extend to creating a safer working environment, engaging everyone in the company that leads to higher employee morale, reduction in costs via limiting waste. Moreover, Small-Group Activities result in bringing people together to brainstorm, finding out problems and root causes enhancing communication and employee skills. All the benefits that can be obtained with Kaizen conclude in incrementally developing customer satisfaction in a positive manner. Nonetheless, Kaizen should not be approached as short-term project nor be implemented in an environment that is not entirely committed to the cause as it is one of the main criteria for the successful application of it. A major risk that also needs to be addressed is the fact that employees sometimes tend to be against change in organizational environments and Kaizen requires diminishing the old way of thinking. There is no end-goal, just Continuous Improvement in everything. Also, it involves everyone hence, distorting the entire management system while requiring resources to run Kaizen activities and training. | |
== '''Annotated Bibliography''' == | == '''Annotated Bibliography''' == | ||
− | |||
+ | '''Imai, Masaaki - Kaizen (Ky’zen), the Key to Japan’s Competitive Success (1986).''' <ref name="Imai"/> | ||
+ | |||
+ | The importance of this book is major as Masaaki Imai defines kaizen for the first time globally as a concept. That is done via merging the management philosophies, theories and tools that are implemented in Japan. Moreover, provides with theory, examples and application that is accessible to the western managers for the first time to apply kaizen to their working environment. More than one hundred examples and fifteen case studies are presented creating a concise interpretation of kaizen. | ||
+ | |||
+ | '''(Management for Professionals) Aristide van Aartsengel, Selahattin Kurtoglu - A Guide to Continuous Improvement (2013).''' <ref name="CIbook1"/> | ||
+ | |||
+ | Presents Continuous Improvement as a necessity in today's environment in addition to providing with theory, definitions and applications for CI that distance from the traditional kaizen ones giving a more holistic view for CI. | ||
+ | |||
+ | '''Imai, Masaaki - Gemba kaizen, a common-sense approach to a continuous improvement strategy (2012).''' <ref name="Gemba"/> | ||
+ | |||
+ | It is a continuation of the first kaizen book from Masaaki Imai. It provides with real world applications of continuous process improvements that adjust to the new market and implementation structures that changed after fifteen years since publishing the first edition book. Analyzes kaizen more in-depth while adapting the old systems into a new era in production and service businesses. Methods as 5S, visual management are introduced in addition to analyzing Taiichi’s Ohno waste management while transforming the original QCS (quality - cost - scheduling) principle from kaizen to QCD (quality - cost - delivery) principle in Gemba kaizen. | ||
+ | |||
+ | '''Ronald D. Moen, Clifford L. Norman – Circling Back, clearing up myths about the Deming Cycle and seeing how it keeps evolving (2010). ''' <ref name="Circle"/> | ||
+ | It provides with concise information about the evolution of Deming's wheel and clarifies the difference between the PDSA and the PDCA cycle and other myths around it. Also, gives a historical overview about continuous improvement tools in a timely manner. | ||
== '''Bibliography''' == | == '''Bibliography''' == | ||
+ | <references> | ||
+ | <ref name="Circle"> Ronald D. Moen, Clifford L. Norman – Circling Back, clearing up myths about the Deming Cycle and seeing how it keeps evolving. (2010) </ref> | ||
+ | <ref name="Shewhart"> Walter Shewhart – Statistical Method from the viewpoint of Quality Control , first edition (2011) </ref> | ||
+ | <ref name="Imai"> Imai, Masaaki - Kaizen (Ky’zen), the Key to Japan’s Competitive Success (1986) </ref> | ||
+ | <ref name="CIbook2"> Aristide van Aartsengel, Selahattin Kurtoglu - Handbook on Continuous Improvement Transformation The Lean Six Sigma Framework and Systematic Methodology for Implementation-Springer-Verlag Ber (2013) </ref> | ||
+ | <ref name="CIbook1"> (Management for Professionals) Aristide van Aartsengel, Selahattin Kurtoglu - A Guide to Continuous Improvement (2013) </ref> | ||
+ | <ref name="Gemba"> Imai, Masaaki - Gemba kaizen a common sense approach to a continuous improvement strategy (2012) </ref> | ||
+ | <ref name="Circle"> Ronald D. Moen, Clifford L. Norman – Circling Back, clearing up myths about the Deming Cycle and seeing how it keeps evolving. (2010) </ref> | ||
+ | <references> |
Latest revision as of 15:46, 30 March 2022
Written by Xenofon Apostolou
[edit] Abstract
Continuous Improvement (CI) is a transformation philosophy that is correlated directly with certain methodologies and strategies executed that provide with constant enhancement and development of services, products, and processes [1] . Also, the possibility of applying CI in every company that is eager to implement the transformation philosophy makes it a broad concept. Hence, there are multiple systems, methods, philosophies, tools, techniques, theories and strategies by which Continuous Improvement can be achieved. Due to the length limitation of this article, the Kaizen philosophy/method and the Just-In-Time production system have been chosen for investigation. The correlation of those with application in Project, Program or Portfolio management is high due to the consideration of Kaizen as a long-term Project having as deliverables a complete transformation in the company by eliminating the old and traditional concepts and granting significant improvement in product/service quality in addition to reducing costs. The concept of a Program is exhibited through application of the Kaizen activities. All activities correlated with Kaizen compose a portfolio that needs to managed effectively as these need to executed properly in a manner of time, person in charge and area of application. Methods such as Six Sigma, Theory of Constraints (ToC) and Agile also possess major significance in applying Continuous Improvement but will not be examined in this article. Firstly, a historical analysis along with defining Continuous Improvement is provided to comprehend the base level and the historical evolution. Secondly, the Kaizen theory (concepts) and application (systems) are investigated thoroughly followed by an example to clarify any gaps. Thirdly, the limitations are explained to understand the benefits and drawbacks that come along with it as well as the ideal conditions in regard to when to use Kaizen. Lastly, the assessed annotated bibliography is specified through making individual remarks for each of them as they provided with important information that led to the composition of this article.
Contents |
[edit] History and definition
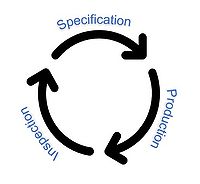
Continuous Improvement (CI) is a transformation philosophy that is correlated directly with certain methodologies and strategies executed that provide with constant enhancement and development of services, products, and processes [1]. It also aims at maximizing cost reduction for companies and businesses and eliminating root causes of problems. This concept often named as Continuous Improvement Process (CIP) is implemented to increase the company’s profit and competitiveness in the short term in addition to sustain these in the long term [1]. William Edwards Deming (October 14, 1900 – December 20, 1993) is generally considered the father of Continuous Improvement, however the person behind the first breakthrough correlated with CI was Walter Shewhart. He is considered one of the first pioneers of Total Quality Management (TQM) [3]. He developed the straight-line process in 1939 in terms of statistical control for specification, production and finally inspection regarding quality control (QA) for products. The method was transformed to a circular model called Shewhart’s cycle the same year [3]. The model was then modified by William Edwards to the Deming Wheel that himself presented in 1950 to an eight-day seminar in Japan sponsored by the Japanese Union of Scientists and Engineers (JUSE) [2].
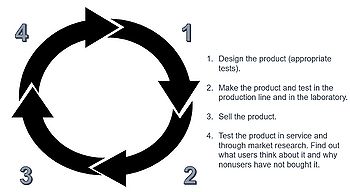
Masaaki Imai the famous inventor of Ky-zen (good-change in English) states in his book ‘’ Kaizen (Ky’zen), the Key to Japan’s Competitive Success’’ that Japanese executives reformed Demings wheel to the Plan-Design-Check-Act (PDCA) tool [4]. Deming, nonetheless, kept himself distant from the tool and after thirty years in 1980 he introduced the Plan-Do-Study-Act (PDSA) cycle [2]. While Continuous Improvement can be broad and abstract, it has its roots in manufacturing. Other concepts that it can be affiliated to are quality control, operations analysis, management and mostly anything that includes processes. Finally, CI is defined by Aristide van Aartsengel and Selahattin Kurtoglu as ‘any state of “being” beyond the state of “becoming.” It is the highest stage of maturity that an enterprise business as a whole can attain. Attaining this highest stage of maturity does not happen overnight; it takes time!' [5]
[edit] Kaizen
[edit] Introduction
Kai-zen (change-good translates to improvement in Japanese) is defined both as a philosophy and a method. It originates from Masaaki Imai in Japan while being one of the most famous CI methods globally in lean production. This philosophy can be applied to all corporate functions in a company although being closer to design, production and market [4].

Masaaki Imai defines it as our way of life be it our working life, our social life, or our home life deserves to be constantly improved [4]. It targets ongoing/continuous improvement involving all levels of hierarchy (top management to workers) [4]. The development of Kaizen is gradual or inch by inch rather than executing major steps. In addition, it does not require huge investment capitals yet calls for extensive continuous effort and considerable commitment that can entail positive results. Lastly, the management principles that are commonly known as Total Quality Control (TQC), Zero Defects (ZD), Just-in-time (JIT) and Kanban (signboard) are used constantly under the Kaizen way of life and are important tools for the application of Kaizen.
[edit] Important concepts
Management should be in state to implement the following significant concepts to apply the Kaizen strategy by introducing a very concise policy statement. [6]
- Kaizen and Management.
The two important functions that management should attend regarding Kaizen is maintenance and improvement. Maintenance is achieved through executing activities that sustain the current situation as well following the SOPs (standard operating procedures). On the other hand, improvement relates to all the actions taken to enhance the current standards. Moreover, improvement is classified as Kaizen or Innovation. The former refers to minor constant improvements over time, which is the philosophy followed in the east, while the latter is a result of breakthrough investment in technology or equipment followed mostly by the west.
- Process vs Result.
Another important principle is the consideration of imperfection in processes in terms of always having space for improvement. In addition to the process-oriented mentality adopted, Kaizen strictly considers that firstly a process must be improved to get better results. This approach should accompany every tool application.
- Executing the Plan-Do-Check-Act (PDCA) cycle and Standardize-Check-Do-Act (SCDA) cycle.
Kaizen uses two very identical and important tools to serve as maintaining and improving factors regarding the standards. As any process must be initially standardized to be in a state of improvement, the use of the SCDA cycle achieves stabilization in the process. In the famous words of Taiichi Ohno ‘Where there is no standard, there can be no Kaizen’. In other words, the SDCA cycle is applied when there is no available standard. While the outcome of a process can be known, lacking standards results in inconsistency and instability in the process itself. Hence, the SDCA cycle contributes to the creation and maintenance of standards and processes.
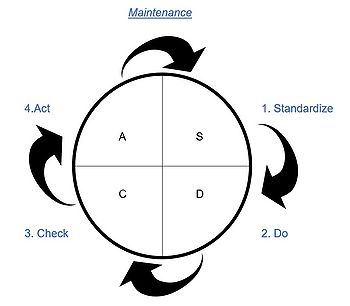
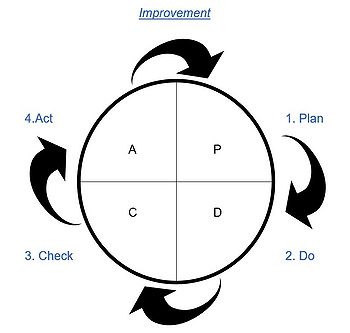
Consequently, when the current process or task has been standardized and is in a state of control, the execution of the PDCA cycle occurs to improve the current performance of the process and create new standards for application. Firstly, ‘Plan’ is the action taken regarding the initialization of the target for improvement. ‘Do’ and ‘Check’ are performed in the same manner as in SDCA cycle. Finally, ‘Act’ is the wide-scale application to prevent the initial problem from happening and/or defining the goals for new improvements [6].
- Prioritizing quality.
Out of the three most important KPIs of quality, cost and delivery (OCD) in a product or a service handling, quality should always possess the strongest priority. This is an immediate result of the importance of delivering high quality to customers in regard to enhancing competitiveness due to that. Making compromises in delivery times or costs should not be considered as a solution. That, however, requires resilient dedication from the management as the aforementioned options can be considered as alternatives risking as such the assurance of the high-quality deliverables of the product and the company’s life. [6]
- Speak with data.
Kaizen identifies itself as a problem- solving procedure. The gathering along with the analyzation of the data must be implemented to fully recognize the situation and be in a state for the situation to be solved correctly by the company. Intuitive approaches such as hunches or feelings are not considered relevant thus lacking science in approaching the problem. The starting point in improvement begins in the collection of data clarifying the focus area that needs to be addressed. [6]
- Considering the customer as the next process.
The axiom ‘the next process is the customer’ [6] means that the next process should be always considered for the customer. All tasks are a series of processes and every process has a supplier and a customer. As customers two types are identified. Internal which are within the company and external which belong out in the market [6]. The majority of people working in a company will relate to internal customers. The axiom mentioned before creates a commitment that a defective part or handling of inaccurate information should never proceed to the next process. The end-result concluded by following this concept is that the external customer receives a high-quality product or service.
[edit] Application
[edit] Important kaizen systems
To achieve the kaizen strategy, the following systems should be introduced and executed.
- Total Quality Control/Total Quality Management (TQC/TQM).
These two systems do not only affiliate as quality-control activities but as strategies to help management in augmenting competitiveness and profitability by improving all aspects of the business. In these systems quality inherits the highest importance. However, there are more variables to be considered as cost and delivery. Furthermore, everybody is involved in the organization by the TQC/TQM systems and that is expressed by the ‘T’ which means total. On the other hand, ‘C’ expresses control or process control. The key processes must be realized and then establish control and continuous improvement in order to achieve better results. The management should set up a plan to check the process versus the result to improve the process, not to criticize the process judging from the result. Activities that belong to TQC/TQM are policy deployment, building quality assurance systems, standardization, training and education, cost management and quality circles. [6]
- Just-in-Time Production System.
This system was originally created by Taiichi Ohno at Toyota Motor company. It is defined as ‘bringing the exact number of required units to each successive stage of production to the appropriate time’ [4]. The purpose of it is the direct elimination of all kinds of waste (Muda) or non-value adding activities while structuring a lean production system with the ability to deal with uncertainties regarding customer quotes. Muda can be classified as:
1. Waste time spent at the machine.
2. Waste involved in the transportation of units.
3. Waste in processing.
4. Waste in taking inventory.
5. Waste of motion.
6. Waste in the form of defective units.
7. Overproduction.
Kanban is used as a communication tool in this system. Kanban also known as signboard, is a visual card attached to each box of parts headed to the assembly line. Upon delivering all components, is returned to the previous task or workstation serving as a record of implemented work and ordering of new parts. Moreover, principles included in the system is to never pass defective work to the next station along with ‘Jidhoka’ [4] which inherits tasks such as the closure of the line whenever a defective part is identified. Toyota has achieved that via possessing machines with automatic stop mechanisms [4]. For example, ‘Throughout the Toyota plants, the visitor will notice large signboards hung from the ceiling. When an individual machine has stopped, the machine's identification number is lit up on the signboard so that the operator knows which machine needs attention’[4]. The advantages of this system relate to shortened lead-time, reduced time spent on non-process work, reduced inventory, better balance between different processes and problem clarification[4]. Representing as such the efforts for continuous improvement in production and inventory resulting in Toyota having a capital turnover ratio ten times bigger compared to American manufacturers. [6]
- Suggestion System for Improvements.
Another significant system that is adopted in kaizen, is the fact that there is a suggestion system incorporated in the company’s structure. Distribution of rewards for employees that try to tackle daily problems and obtain savings from these suggestions or meet managerial criteria is a commonality. These criteria can be grouped to Process-Oriented and Results-Oriented as mentioned in the Kaizen book [4]. The Process-oriented criteria is a mirroring of the significance being given in effort by the Japanese culture except than outstanding results. Process-Oriented criteria can be attendance in meetings, willingness of participation, total number of problems solved and report submissions.
- Total Productive Maintenance.
TQM was introduced as a system before referring to the overall improvement of performance and quality. Now TPM stresses the importance of improving equipment quality. Simplified, is about ‘maximization of equipment efficiency through a total system of preventive maintenance spanning the lifetime of the equipment’[6]. TQM includes everyone related to the company, however TPM correlates with people involved in the plant. A major continuous improvement activity affiliated with the system is the 5S which is analysed below.
1. Seiri (Sort): Distinguish between necessary and unnecessary items in the Gemba and discard the latter. Start by removing all items from your work area. Inspect the equipment and identify those items that are critical to the success of the function performed at the workstation. Eliminate any duplicates, unnecessary equipment, infrequently used items, and trash. Identify the non-essential items as either waste or valuable but not critical. Store the non-critical items outside of the workstation area. This saves time, space, and labour costs, while enhancing productivity. [6]
2. Seiton (Straighten): Arrange all items remaining after seiri in an orderly manner. Whatever equipment is deemed critical to the operation must now be organized. Assign positions for all equipment, work in progress, and raw materials, keeping ease of reach, identification, and proximity to work surface in mind as you do. The goal is to maximize the efficiency of the workstation layout. On a smaller scale, it’s the same concept as warehouse layout. The most frequently used tools should be the most convenient to grab. This eliminates wasted time from excess motion and searching. [6]
3. Seiso (Scrub): Keep machines and working environments clean. Keep everything clean, every day. Doing this keeps things ready to be used when needed. A clean workspace is a productive workspace, and Seiso literally means “to clean or shine.” Clean the floors, the walls and the equipment, and ensure all items are restored to their designated place. Make sure the workstation is well lit. This should be a part of your daily tasks and should not be postponed until idle time is available. [6]
4. Seiketsu (Systemize): Extend the concept of cleanliness to oneself, and continuously practice the preceding three steps. Make a habit of properly maintaining correct procedures to avoid backsliding. Implementing these steps is a continuous process. It is important to ensure that they are done each day to prevent slipping into old habits. Commit to performing these steps every shift and make sure that any changes to your product or process are compensated for at your workstation and problems are alleviated as quickly as they are created. [6]
5. Shitsuke (Standardize): Build self -discipline and make a habit of engaging in 5S by establishing standards. Ensure conditions of work area do not return to the original, disorganized state. Make the previous three S’s part of your standard procedures each day. Implement them with the help of signs, banners, shadow boards, tool holders, etc. Make sure all workers understand their responsibilities and are empowered to perform all of the tasks. [6]
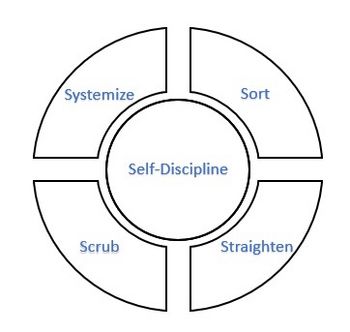
- Policy Deployment.
The process of 'hoshin kanri'[6] in Japanese or Policy Deployment refers to setting a long-term strategy that breaks down to medium-term and annual strategies. The strategy should pass all levels of management until it reaches down to the shop floor or front-end. However, the strategy should include all the necessary actions or activities for the implementation of it as it cascades down to the lower levels of management. An example of policy deployment is setting a target of cutting costs by ten percent. The front-end or shop floor must acquire the activities that lead to reducing inventory, increasing productivity and improving the line configurations leading to the achievement of the target.
- Small-Group Activities.
Kaizen in group work is executed via Small-Group Activities. Some examples of the activities are Zero Defects (ZD), Mini Think Tanks, Safety Groups, Productivity Committees and the most popular one is the Quality Circles (QC). These activities present a nonconfrontational and informal way of solving problems while proposing improvements [4]. The groups are formed to tackle problems or carry out tasks in a workshop environment while using statistical tools such as histograms, pareto charts, cause and effect diagrams, run charts, scatter diagrams, flow charts and control charts. In addition, the PDCA cycle is executed, however, as not only the identification of problems but also the identification of root causes takes place there is another PDCA cycle implemented in the 'Do' step of the first one. This defines the procedure as problem-solving and decision-making one.
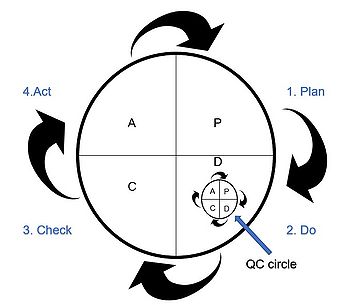
Moreover, in Japanese plants there is always a workplace situated for the execution of these activities. QC were invented in 1962 as studying groups firstly, having foremen and workers study together to get knowledge and techniques on quality control[6]. Now, it possesses a more problem-solving structure.
[edit] A Kaizen example
There are numerous ways by which Kaizen can be applied in a company, a scenario will be proposed in a company that is expected to have an increase of twenty percent in demand. Accordingly, the head of production or the plant manager wants to upgrade the productivity rate by twenty percent to meet the demand. He decides to organize a two-day Kaizen event on line ‘1’ that has a bottleneck structuring a clear target for achievement. Hence, he gathers key employees (stakeholders) such as line managers, supervisors, staff, team leaders and operators. To keep the production running and not distort customer satisfaction he decides to organize these events during the night between shifts. Meetings will be conducted beforehand to discuss the application of Kaizen in the work area referring to the 'Plan' step. After that the new application will be explained to the operators. Then, the team members make notes upon the new operation implemented and come up with ideas and structure a plan to execute them. Small-Group Activities such as QC can take place. A pareto or a cause-effect diagram can be used along with the seven statistical tools to develop solutions. The team leader decides among the ideas which one to implement the next day. The operators get the instructions of the plan, implement them ('Do' step) and are strongly encouraged to speak up regarding difficulties they face in their work ('Check' step). That is the input that results to the finalization of the plan ('Act' step). When the plan is finalized then there is a new standard for the process. The solutions for debottlenecking the line could be to re-build the line, so it supports the takt time, to eliminate the Muda (waste) from the plant following Taiichi’s Ohno Just-in-Time system to comprehend the categories of it and then applying the 5S system to reduce them. Develop work procedures that can be written into standardized work including conditions of work, handling of parts and combination of motion. All the aforementioned are related to the 'Act' step. Then the application of the proposed solutions will trigger a new iteration for SDCA/PDCA cycles. Hence, continuously implement the SDCA cycle to stabilize the new process and create the new standard. When that is done proceed with the application of the PDCA cycle to improve the current standard way of implementing and running of the line. Below the outcome of the whole process is illustrated.
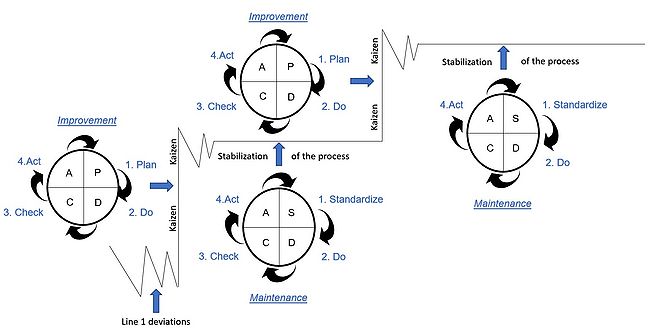
That is just a simple example of how Kaizen can be applied in a manufacturing plant. There are many different ways of applying Kaizen and it's respective systems and tools. The choice of those, length of training, structuring of the plan and solutions can very much differ depending on the size the target needed to be achieved. Nonetheless, Kaizen always proposes the application of small and steady targets.
[edit] Limitations
Kaizen can be applied everywhere there are operations, processes and tasks in all corporate functions. The most important aspect it improves is product/service quality however, there are more aspects that extend to creating a safer working environment, engaging everyone in the company that leads to higher employee morale, reduction in costs via limiting waste. Moreover, Small-Group Activities result in bringing people together to brainstorm, finding out problems and root causes enhancing communication and employee skills. All the benefits that can be obtained with Kaizen conclude in incrementally developing customer satisfaction in a positive manner. Nonetheless, Kaizen should not be approached as short-term project nor be implemented in an environment that is not entirely committed to the cause as it is one of the main criteria for the successful application of it. A major risk that also needs to be addressed is the fact that employees sometimes tend to be against change in organizational environments and Kaizen requires diminishing the old way of thinking. There is no end-goal, just Continuous Improvement in everything. Also, it involves everyone hence, distorting the entire management system while requiring resources to run Kaizen activities and training.
[edit] Annotated Bibliography
Imai, Masaaki - Kaizen (Ky’zen), the Key to Japan’s Competitive Success (1986). [4]
The importance of this book is major as Masaaki Imai defines kaizen for the first time globally as a concept. That is done via merging the management philosophies, theories and tools that are implemented in Japan. Moreover, provides with theory, examples and application that is accessible to the western managers for the first time to apply kaizen to their working environment. More than one hundred examples and fifteen case studies are presented creating a concise interpretation of kaizen.
(Management for Professionals) Aristide van Aartsengel, Selahattin Kurtoglu - A Guide to Continuous Improvement (2013). [5]
Presents Continuous Improvement as a necessity in today's environment in addition to providing with theory, definitions and applications for CI that distance from the traditional kaizen ones giving a more holistic view for CI.
Imai, Masaaki - Gemba kaizen, a common-sense approach to a continuous improvement strategy (2012). [6]
It is a continuation of the first kaizen book from Masaaki Imai. It provides with real world applications of continuous process improvements that adjust to the new market and implementation structures that changed after fifteen years since publishing the first edition book. Analyzes kaizen more in-depth while adapting the old systems into a new era in production and service businesses. Methods as 5S, visual management are introduced in addition to analyzing Taiichi’s Ohno waste management while transforming the original QCS (quality - cost - scheduling) principle from kaizen to QCD (quality - cost - delivery) principle in Gemba kaizen.
Ronald D. Moen, Clifford L. Norman – Circling Back, clearing up myths about the Deming Cycle and seeing how it keeps evolving (2010). [2]
It provides with concise information about the evolution of Deming's wheel and clarifies the difference between the PDSA and the PDCA cycle and other myths around it. Also, gives a historical overview about continuous improvement tools in a timely manner.
[edit] Bibliography
- ↑ 1.0 1.1 1.2 Aristide van Aartsengel, Selahattin Kurtoglu - Handbook on Continuous Improvement Transformation The Lean Six Sigma Framework and Systematic Methodology for Implementation-Springer-Verlag Ber (2013)
- ↑ 2.0 2.1 2.2 2.3 2.4 Ronald D. Moen, Clifford L. Norman – Circling Back, clearing up myths about the Deming Cycle and seeing how it keeps evolving. (2010)
- ↑ 3.0 3.1 Walter Shewhart – Statistical Method from the viewpoint of Quality Control , first edition (2011)
- ↑ 4.00 4.01 4.02 4.03 4.04 4.05 4.06 4.07 4.08 4.09 4.10 4.11 4.12 4.13 4.14 Imai, Masaaki - Kaizen (Ky’zen), the Key to Japan’s Competitive Success (1986)
- ↑ 5.0 5.1 (Management for Professionals) Aristide van Aartsengel, Selahattin Kurtoglu - A Guide to Continuous Improvement (2013)
- ↑ 6.00 6.01 6.02 6.03 6.04 6.05 6.06 6.07 6.08 6.09 6.10 6.11 6.12 6.13 6.14 6.15 6.16 6.17 6.18 6.19 6.20 6.21 Imai, Masaaki - Gemba kaizen a common sense approach to a continuous improvement strategy (2012)