Continuous Improvement / Kaizen
(37 intermediate revisions by one user not shown) | |||
Line 1: | Line 1: | ||
− | == | + | == Introduction == |
− | [[File:Concept of Continuous Improvement.png|thumb| | + | [[File:Concept of Continuous Improvement.png|thumb|600px|right|Figure 1: Concept of Continuous Improvement<ref name="CI Concept">M. Helmold, Lean Management and Kaizen - Fundamentals from Cases and Examples in Operations and Supply Chain Management, Springer, 2020. </ref> ]] |
− | Continuous Improvement, also referred to as Kaizen, is a concept that is related to principles, methods and activities that have the target of continuously improving the performance of an organization or individual. Continuous Improvement focuses on incremental steps that eventually lead to big improvements over time, rather than breakthrough changes. In a wider and more cultural sense, the concept is based on the assumption that the world is steadily changing and can always be improved. The concept of Kaizen is Japanese and means kai = change, zen = to good (see figure 2). Although there are slight definitional differences, continuous improvement and kaizen are fundamentally similar. Hence the two terms are generally used synonymously<ref name="main">J. L. Garcia-Alcaraz, M. Oropesa-Vento and A. A. Maldonado-Macias, Kaizen, Planning, Implementing and Controlling, Springer International Publishing, 2017.</ref>. | + | Continuous Improvement, also referred to as Kaizen, is a concept that is related to principles, methods and activities that have the target of continuously improving the performance of an organization or individual. In contrast to Innovation, Continuous Improvement focuses on incremental steps that eventually lead to big improvements over time, rather than breakthrough changes. In a wider and more cultural sense, the concept is based on the assumption that the world is steadily changing and can always be improved. The concept of Kaizen is Japanese and means kai = change, zen = to good (see figure 2). Although there are slight definitional differences, continuous improvement and kaizen are fundamentally similar. Hence the two terms are generally used synonymously<ref name="main">J. L. Garcia-Alcaraz, M. Oropesa-Vento and A. A. Maldonado-Macias, Kaizen, Planning, Implementing and Controlling, Springer International Publishing, 2017.</ref>. |
− | In an organizational context, Continuous improvement is a strategic and long-term effort to enhance competitiveness by improving quality, cost and time. The | + | In an organizational context, Continuous improvement is a strategic and long-term effort to enhance competitiveness by improving quality, cost and time. The efforts are usually directed towards achieving certain objectives. Continuous Improvement is therefore different to the concept of idea management, that revolves around collecting, implementing and rewarding diverse ideas of employees<ref name="inno">innolytics.ag, "The Complete Guide to the Continuous Improvement Process," [Online]. Available: https://innolytics-innovation.com/continuous-improvement-process/. [Accessed 28 February 2022].</ref>. Improvement is achieved by applying an iterative process of constantly observing the current situation and implementing improvements. Improvements should then be standardized and disseminated to other areas. The concept of Continuous Improvement is illustrated in figure 1. Furthermore, Continuous Improvement tries to involve employees from all hierarchy levels of an organization in the improvement process. Therefore, it is a popular concept in industry as it is easy and cheap to implement and not limited to any industry and organizational size<ref name="main">J. L. Garcia-Alcaraz, M. Oropesa-Vento and A. A. Maldonado-Macias, Kaizen, Planning, Implementing and Controlling, Springer International Publishing, 2017.</ref>. The main differences between Continuous Improvement and the general process of organizational innovation are listed in the table below. |
+ | |||
+ | {| class="wikitable" | ||
+ | !colspan="2"|Main Differences between Continuous Improvement and Innovation<ref name="CI Concept">M. Helmold, Lean Management and Kaizen - Fundamentals from Cases and Examples in Operations and Supply Chain Management, Springer, 2020. </ref> | ||
+ | |- | ||
+ | !colspan="1"|Continuous Improvement | ||
+ | !colspan="1"|Innovation | ||
+ | |- | ||
+ | | | ||
+ | * Small incremental steps | ||
+ | |||
+ | * Low expenditure | ||
+ | |||
+ | * No risk | ||
+ | |||
+ | * Involvement of all employees | ||
+ | |||
+ | * Short Term | ||
+ | |||
+ | * Team decision (approved by management) | ||
+ | |||
+ | | | ||
+ | * Major changes | ||
+ | |||
+ | * High expenditure | ||
+ | |||
+ | * Entrepreneurial risk | ||
+ | |||
+ | * Specialized Team | ||
+ | |||
+ | * Long Term | ||
+ | |||
+ | * Management decision | ||
+ | |} | ||
== History of Continuous Improvement == | == History of Continuous Improvement == | ||
− | [[File:Kaizen Symbol.jpg|thumb|370px|right|Figure 2: Symbol of Kaizen]] | + | [[File:Kaizen Symbol.jpg|thumb|370px|right|Figure 2: Symbol of Kaizen<ref name="symbol">caterfly, "Kaizen - rejuvenating your organisation," [Online]. Available: https://caterfly.co.uk/kaizen-rejuvenating-your-organisation/. [Accessed 18 March 2022].</ref>]] |
Continuous Improvement first appeared in Japan during the second world war. It was an answer to the numerous and serious damages that the country had suffered. The concept was used by authorities in order to reconstruct the country. Furthermore, the development of continuous improvement was supported by the use of the U.S. training program Training with Industry (TWI Inc.), which aimed at developing training programs for Japanese companies. The small-step approach was preferred, as resources were scarce and major change initiatives could not be afforded. | Continuous Improvement first appeared in Japan during the second world war. It was an answer to the numerous and serious damages that the country had suffered. The concept was used by authorities in order to reconstruct the country. Furthermore, the development of continuous improvement was supported by the use of the U.S. training program Training with Industry (TWI Inc.), which aimed at developing training programs for Japanese companies. The small-step approach was preferred, as resources were scarce and major change initiatives could not be afforded. | ||
− | Even though elements of continuous improvement such as suggestion systems or quality systems were regularly used in Japanese industry, the concept only got further attention with the development of the oil crisis in 1973. In a period of financial constraints, companies such as Toyota have used the concept to achieve cost reductions with little expenditure of resources. Parallel the company Canon was able to gain large benefits of up to 200 million US Dollar by launching a continuous improvement campaign. As the profits did not go unnoticed, | + | Even though elements of continuous improvement such as suggestion systems or quality systems were regularly used in Japanese industry, the concept only got further attention with the development of the oil crisis in 1973. In a period of financial constraints, companies such as Toyota have used the concept to achieve cost reductions with little expenditure of resources. Parallel, the company Canon was able to gain large benefits of up to 200 million US Dollar by launching a continuous improvement campaign. As the profits did not go unnoticed, Continuous Improvement made its way into the western economy in the 1980s. Remarkable benefits could be achieved by companies such as Xerox, Motorola, Harley Davidson, and General Electrics<ref name="main">J. L. Garcia-Alcaraz, M. Oropesa-Vento and A. A. Maldonado-Macias, Kaizen, Planning, Implementing and Controlling, Springer International Publishing, 2017.</ref>. |
== Continuous Improvement in Relation to Project, Program and Portfolio Management == | == Continuous Improvement in Relation to Project, Program and Portfolio Management == | ||
− | Continuous Improvement was originally created to improve production processes and is today commonly used in that area. And even though Continuous Improvement focuses on the constant challenge to improve standards<ref name="main">J. L. Garcia-Alcaraz, M. Oropesa-Vento and A. A. Maldonado-Macias, Kaizen, Planning, Implementing and Controlling, Springer International Publishing, 2017.</ref>, it is applicable in any organizational area including project, program and portfolio management. Although projects are always unique to some degree, different projects in an organization often involve recurring activities, methods and processes that can be constantly improved. Furthermore, projects can be embedded in organizational processes that | + | Continuous Improvement was originally created to improve production processes and is today commonly used in that area. And even though Continuous Improvement focuses on the constant challenge to improve standards<ref name="main">J. L. Garcia-Alcaraz, M. Oropesa-Vento and A. A. Maldonado-Macias, Kaizen, Planning, Implementing and Controlling, Springer International Publishing, 2017.</ref>, it is applicable in any organizational area including project, program and portfolio management. Although projects are always unique to some degree, different projects in an organization often involve recurring activities, methods and processes that can be constantly improved. Furthermore, projects can be embedded in organizational processes that structures the frame within projects are being carried out. In a Project Environement, Continuous Improvement needs to be seen as a learning effect that is achieved project by project and can be transferred into the organizational knowledge base. |
− | The project management standard ISO21500 recommends that Continuous Improvement | + | The project management standard ISO21500 recommends that Continuous Improvement, should influence thinking and behavior in the governance and management of projects. Furthermore, knowledge gained must be documented and shared throughout the organization, also to increase performance in future projects<ref name="ISO">International Organizations for Standardization, DS/ISO 21500:2021 - Project, programme and portfolio management - Context and concepts, 2021.</ref>. |
== Key Concept and Benefits == | == Key Concept and Benefits == | ||
− | The idea of Continuous Improvement is part of the bigger concept of Lean Management, which has its origins in the Toyota production System. The term | + | The idea of Continuous Improvement is part of the bigger concept of Lean Management, which has its origins in the Toyota production System. The term lean is defined by Krajewski, who describes lean systems as systems that maximize the added value of each activity in an organization, by eliminating waste and delays<ref name="definition 2">L. Krajewski, L. Ritzman and M. MK, Operations management: processes and supply chains, Pearson, 2013.</ref>. Continuous Improvement is thus aiming at incrementally improving organizational activities by using less of everything or reducing waste or generally non-value adding work. Since customer orientation is a central component of Continuous Improvement, the value from the customer's point of view is considered in all activities<ref name="main">J. L. Garcia-Alcaraz, M. Oropesa-Vento and A. A. Maldonado-Macias, Kaizen, Planning, Implementing and Controlling, Springer International Publishing, 2017.</ref>. |
− | + | ||
− | + | ||
− | In his 1986 book Kaizen: The Key to Japan's Competitive Success, Imai Masaaki, who is seen as the father of the concept among others, summarizes how this | + | [[File:PDCA Cycle.png|thumb|400px|right|Figure 3: Illustration of the Plan-Do-Check-Act Cycle (PDCA)<ref name="lean pd">L. G. Trabasso and M. V. P. Pessoa, The Lean Product Design and Development Journey, Springer International Publishing, 2016.</ref>]] |
+ | In his 1986 book ''Kaizen: The Key to Japan's Competitive Success'', Imai Masaaki, who is seen as the father of the concept among others, summarizes how this can be achieved with basic principles<ref name="CI process">M. Imai, Kaizen: The key to Japan's competitive success, Random House Business, 1986.</ref>. | ||
'''Feedback:''' Improvement starts by the reflection of processes | '''Feedback:''' Improvement starts by the reflection of processes | ||
Line 32: | Line 64: | ||
'''Evolution:''' Continuous Improvement is focused on incremental steps not major change initiatives<ref name="CI process">M. Imai, Kaizen: The key to Japan's competitive success, Random House Business, 1986.</ref> | '''Evolution:''' Continuous Improvement is focused on incremental steps not major change initiatives<ref name="CI process">M. Imai, Kaizen: The key to Japan's competitive success, Random House Business, 1986.</ref> | ||
− | The following are some key features of Continuous Improvement | + | The following points are some key features of Continuous Improvement |
* Since ideas for improvement can come from all employees, they are often small in scope and therefore quick and easy to implement | * Since ideas for improvement can come from all employees, they are often small in scope and therefore quick and easy to implement | ||
Line 46: | Line 78: | ||
* The collaborative approach promotes teamwork and thus increases the motivation of employees<ref name="CI process">M. Imai, Kaizen: The key to Japan's competitive success, Random House Business, 1986.</ref> | * The collaborative approach promotes teamwork and thus increases the motivation of employees<ref name="CI process">M. Imai, Kaizen: The key to Japan's competitive success, Random House Business, 1986.</ref> | ||
− | A | + | |
+ | A key idea of Continuous Improvement can be found in the PDCA Cycle, that was designed by William Edwards Deming. The Cycle describes an iterative process of continuous learning. It consists of the four Phases Plan, Do, Check, Act. The four phases should be followed for each problem to achieve sustainable improvement. Because of its iterative nature, the cycle must be repeated until the problem is effectively solved. The PDCA Cycle is the fundament of Continuous Improvement and should therefore be taken into consideration in all activities<ref name="lean pd">L. G. Trabasso and M. V. P. Pessoa, The Lean Product Design and Development Journey, Springer International Publishing, 2016.</ref>. The principle of the PDCA Cycle is illustrated in figure 3. | ||
'''Plan:''' | '''Plan:''' | ||
Line 62: | Line 95: | ||
---- | ---- | ||
− | The successful implementation of Continuous Improvement provides numerous benefits. Some benefits are named in the following table: | + | The successful implementation of Continuous Improvement provides numerous benefits for organizations and individuals. Some of these benefits are named in the following table: |
{| class="wikitable" | {| class="wikitable" | ||
− | !colspan="2"|Benefits of Continuous Improvement | + | !colspan="2"|Benefits of Continuous Improvement<ref name="main">J. L. Garcia-Alcaraz, M. Oropesa-Vento and A. A. Maldonado-Macias, Kaizen, Planning, Implementing and Controlling, Springer International Publishing, 2017.</ref> |
|- | |- | ||
|'''Quality Improvements''' | |'''Quality Improvements''' | ||
Line 89: | Line 122: | ||
|- | |- | ||
|'''Higher Responsibility of employees''' | |'''Higher Responsibility of employees''' | ||
− | |As problems are solved in multidisciplinary teams, all participating employees (from all hierarchy levels) are responsible for a certain task | + | |As problems are solved in multidisciplinary teams, all participating employees (from all hierarchy levels) are responsible for a certain task. |
|- | |- | ||
|} | |} | ||
− | == | + | == Requirements and Implementation == |
Continuous Improvement can be implemented in an organization in different ways and to different extends. Whether the concept is implemented within a large campaign or in a more slow and organic manner depends on the needs and capabilities of each individual organization. It is important however, that the introduction of Continuous Improvement is not seen as a project, but as an ongoing process. The following chapter will present recommendations on how to implement Continuous Improvements as well as considerations that should be taken into account for both the preparation or implementation and actual execution phase. | Continuous Improvement can be implemented in an organization in different ways and to different extends. Whether the concept is implemented within a large campaign or in a more slow and organic manner depends on the needs and capabilities of each individual organization. It is important however, that the introduction of Continuous Improvement is not seen as a project, but as an ongoing process. The following chapter will present recommendations on how to implement Continuous Improvements as well as considerations that should be taken into account for both the preparation or implementation and actual execution phase. | ||
− | [[File:Target Condition Continuous Improvement.png|thumb| | + | [[File:Target Condition Continuous Improvement.png|thumb|550px|right|Figure 4: Reaching a target condition through incremental improvement steps<ref name="lean pd">L. G. Trabasso and M. V. P. Pessoa, The Lean Product Design and Development Journey, Springer International Publishing, 2016.</ref>]] |
'''Describing a clear target condition:''' A first fundamental step in implementing continuous improvement is to define a target condition that describes a desired future situation. Describing a vision assures that all improvement efforts are clearly directed towards it. Change is only considered improvement when it is directed towards a common goal. The target conditions functions as guide for all involved people. The target condition should be medium to long term but can be supplemented by short term goals. By eliminating causes of hurdles on the way towards the vision, improvement is achieved step by step (see figure 4). Expressing the target state in terms of key indicators ensures a common understanding of the target and allows a clear statement on the extent to which improvements have been made [7]. The target condition is often already included in a company’s vision or strategy. | '''Describing a clear target condition:''' A first fundamental step in implementing continuous improvement is to define a target condition that describes a desired future situation. Describing a vision assures that all improvement efforts are clearly directed towards it. Change is only considered improvement when it is directed towards a common goal. The target conditions functions as guide for all involved people. The target condition should be medium to long term but can be supplemented by short term goals. By eliminating causes of hurdles on the way towards the vision, improvement is achieved step by step (see figure 4). Expressing the target state in terms of key indicators ensures a common understanding of the target and allows a clear statement on the extent to which improvements have been made [7]. The target condition is often already included in a company’s vision or strategy. | ||
Line 104: | Line 137: | ||
'''Human Resources Training:''' With potentially all employees being included in continuous improvement, a certain knowledge level is required to effectively apply the concept. The level of knowledge depends on the different roles in the organization, however basic in problem solving methods (Fishbone, 5-Why, Pareto Analysis) are recommended<ref name="main">J. L. Garcia-Alcaraz, M. Oropesa-Vento and A. A. Maldonado-Macias, Kaizen, Planning, Implementing and Controlling, Springer International Publishing, 2017.</ref>. | '''Human Resources Training:''' With potentially all employees being included in continuous improvement, a certain knowledge level is required to effectively apply the concept. The level of knowledge depends on the different roles in the organization, however basic in problem solving methods (Fishbone, 5-Why, Pareto Analysis) are recommended<ref name="main">J. L. Garcia-Alcaraz, M. Oropesa-Vento and A. A. Maldonado-Macias, Kaizen, Planning, Implementing and Controlling, Springer International Publishing, 2017.</ref>. | ||
− | '''Problem Detection:''' The | + | '''Problem Detection:''' The actual process of Continuous Improvement starts with the detection of problems in organizational processes. A classical way of analysing processes is by conducting a value stream mapping. Within value stream mapping, the companies workflow, including all activities and people that contribute to delivering value to the customer wihtin the project are mapped out. This is done by separating a project into single value streams. The result is a visualization of the process with key information regarding material and information flows. The visualization can then be used for further analysis, with the goal of identifying parts of the workflow that require resources but do not create value for the customer<ref name="CI Concept">M. Helmold, Lean Management and Kaizen - Fundamentals from Cases and Examples in Operations and Supply Chain Management, Springer, 2020. </ref>. Workshops or Circles, such as a Kaizen Event, are a suitable tool to examine the visualized processes and workflows in the team. Another possibility is to address problems in regular (e.g. daily morning meeting). It’s important to clearly define, where the current situation deviates from the targeted condition. Again, it’s beneficial if this can be expressed through Key Indicators [2]. |
− | '''Problem Solving in Interdisciplinary Teams:''' To benefit from the different capabilities and expertise, multidisciplinary teams should be used as much as possible in the problem-solving process. The solution generation can also be examined within the initial workshop. Within this process, problem solving techniques such as 5-Why or Ishikawa should be used (See Chapter Tools and Methods in Continuous Improvements). By evaluating and prioritizing solutions in terms of suitability, a clear plan of measures is created. The implementation of measures works accordingly to the PDCA Cycle. The Team needs to be kept updated about the successful implementation improvement measures. Furthermore, the team needs to be acknowledged for their achievements<ref name="main">J. L. Garcia-Alcaraz, M. Oropesa-Vento and A. A. Maldonado-Macias, Kaizen, Planning, Implementing and Controlling, Springer International Publishing, 2017.</ref>. | + | In the early stages of Continuous Improvement it is recommended to start with a pilot. Depending on the organizational environment that projects are carried out in, this can for instance be a single department. By limiting the scope of the initial activities, it is easy for all employees involved to clearly see the benefits. This also ensures that the organization has the necessary resources to implement all defined measures and thus maintain motivation. |
+ | |||
+ | '''Problem Solving in Interdisciplinary Teams:''' To benefit from the different capabilities and expertise, multidisciplinary teams should be used as much as possible in the problem-solving process. The solution generation can also be examined within the initial workshop. Within this process, problem solving techniques such as 5-Why or Ishikawa should be used (See Chapter Tools and Methods in Continuous Improvements). By evaluating and prioritizing solutions in terms of suitability, a clear plan of measures is created. The implementation of measures works accordingly to the PDCA Cycle. The Team needs to be kept updated about the successful implementation improvement measures in regular follow ups. Furthermore, the team needs to be acknowledged for their achievements<ref name="main">J. L. Garcia-Alcaraz, M. Oropesa-Vento and A. A. Maldonado-Macias, Kaizen, Planning, Implementing and Controlling, Springer International Publishing, 2017.</ref>. | ||
== Tools and Methods == | == Tools and Methods == | ||
− | Within the Concept of Continuous Improvement, several Tools can be used | + | Within the Concept of Continuous Improvement, several Tools can be used in the improvement process. The following chapter will introduce commonly used tools for problem analysis as well as list of further helpful tools. |
[[File:Ishikawa.png|thumb|550px|left|Figure 5: Concept of the Ishikawa Diagram<ref name="QM-Tools">R. K. Sharma, "Quality management tools and standards," in Quality Management Practices in MSME Sectors, Springer Science and Business Media Deutschland GmbH, 2021, pp. 25-62.</ref>]] | [[File:Ishikawa.png|thumb|550px|left|Figure 5: Concept of the Ishikawa Diagram<ref name="QM-Tools">R. K. Sharma, "Quality management tools and standards," in Quality Management Practices in MSME Sectors, Springer Science and Business Media Deutschland GmbH, 2021, pp. 25-62.</ref>]] | ||
==== Ishikawa Diagram ==== | ==== Ishikawa Diagram ==== | ||
− | A tool commonly used tool in connection with Continuous Improvement is the Ishikawa Diagram. The tool is also known as Root-Cause or Fishbone Diagram. The Ishikawa Diagram is a systemic approach to identify causes for a problem at hand. The main goal of the Ishikawa diagram is to reveal and break down the various causes that contribute to a problem. The identified causes are then addressed through mitigation measures. | + | A tool commonly used tool in connection with Continuous Improvement is the Ishikawa Diagram. The tool is also known as Root-Cause or Fishbone Diagram. The Ishikawa Diagram is a systemic approach to identify causes for a problem at hand. The main goal of the Ishikawa diagram is to reveal and break down the various causes that contribute to a problem. The identified causes are then addressed through mitigation measures. |
− | Figure 1 shows a typical model of the Ishikawa Diagram. A problem is usually written on the right side of the model which is then connected to potential main causes. The main causes build the “bones” of the model. For the main causes, the 5M (Material, Machine, Manpower, Method and Milieu) are often used as a starting point. Afterwards, sub causes are added to the main causes. Theses sub causes are represented by the horizontal lines attach to main causes. The causes are usually identified in brainstorming activities, conducted by multidisciplinary teams. The subdivision of causes is done, til the problem at hand has been understood completely<ref name="QM-Tools">R. K. Sharma, "Quality management tools and standards," in Quality Management Practices in MSME Sectors, Springer Science and Business Media Deutschland GmbH, 2021, pp. 25-62.</ref>. The causes are then tested for validity until the desired effect has occurred | + | |
− | + | Figure 1 shows a typical model of the Ishikawa Diagram. A problem is usually written on the right side of the model which is then connected to potential main causes. The main causes build the “bones” of the model. For the main causes, the 5M (Material, Machine, Manpower, Method and Milieu) are often used as a starting point. Afterwards, sub causes are added to the main causes. Theses sub causes are represented by the horizontal lines attach to main causes. The causes are usually identified in brainstorming activities, conducted by multidisciplinary teams. The subdivision of causes is done, til the problem at hand has been understood completely<ref name="QM-Tools">R. K. Sharma, "Quality management tools and standards," in Quality Management Practices in MSME Sectors, Springer Science and Business Media Deutschland GmbH, 2021, pp. 25-62.</ref>. The causes are then tested for validity by executing the improvement actions until the desired effect has occurred, i.e. the problem has been solved. The effectiveness of the measures is usually confirmed by comparing the previously considered key figures. | |
− | + | ||
− | + | ||
− | + | ||
− | + | ||
Line 134: | Line 165: | ||
==== 5-Why Analysis ==== | ==== 5-Why Analysis ==== | ||
− | Another tool that is used in Continuous Improvement is the 5-Why. The tool tries to tackle the same issue as the Ishikawa Diagram, identifying the root cause of a problem, so that it does not occur again. The tool is applied by looking at a symptom (problem) and asking why it happened. The answer to why is then questioned 5 times. The process can usually be terminated if the why questions do not yield any new insights. Similarly, the why question can be asked more than five times<ref name="5-Why">O. Serrat, "The 5-Whys Technique," February 2009. [Online]. Available: https://www.adb.org/publications/five-whys-technique.</ref>. The principle is illustrated as an example in figure 6. | + | Another tool that is used in Continuous Improvement is the 5-Why Analysis. The tool tries to tackle the same issue as the Ishikawa Diagram, identifying the root cause of a problem, so that it does not occur again. The tool is applied by looking at a symptom (problem) and asking why it happened. The answer to ''why'' is then questioned ''5 times''. The process can usually be terminated if the why questions do not yield any new insights. Similarly, the why question can be asked more than five times<ref name="5-Why">O. Serrat, "The 5-Whys Technique," February 2009. [Online]. Available: https://www.adb.org/publications/five-whys-technique.</ref>. The principle is illustrated as an example in figure 6. |
+ | |||
The advantage of this systematic approach is that it is simple, easy to implement and can be used for most problems. However, there are some conditions that should be met for effective use of the tool. First, the problem at hand must be described in sufficient detail to allow conclusions to be drawn about causes. Second, questions must be answered truthfully. And last, it must be desired to analyze the problem down to the root cause and not to force symptom fighting in order to be able to achieve quick but not sustainable improvements. Identical to the Ishikawa Model, the 5 Why Method can be used individually, but works best when conducted by a multidisciplinary team<ref name="5-Why">O. Serrat, "The 5-Whys Technique," February 2009. [Online]. Available: https://www.adb.org/publications/five-whys-technique.</ref>. | The advantage of this systematic approach is that it is simple, easy to implement and can be used for most problems. However, there are some conditions that should be met for effective use of the tool. First, the problem at hand must be described in sufficient detail to allow conclusions to be drawn about causes. Second, questions must be answered truthfully. And last, it must be desired to analyze the problem down to the root cause and not to force symptom fighting in order to be able to achieve quick but not sustainable improvements. Identical to the Ishikawa Model, the 5 Why Method can be used individually, but works best when conducted by a multidisciplinary team<ref name="5-Why">O. Serrat, "The 5-Whys Technique," February 2009. [Online]. Available: https://www.adb.org/publications/five-whys-technique.</ref>. | ||
A practical application of the tool could look like the following: | A practical application of the tool could look like the following: | ||
Line 152: | Line 184: | ||
---- | ---- | ||
==== Further Tools ==== | ==== Further Tools ==== | ||
− | Further Tools that can be used with the objective of solving problems in a sustainable way are the following: | + | Further Tools connected to Continuous Improvement that can be used with the objective of solving problems in a sustainable way are the following: |
* '''Pareto Analysis:''' Problem solving technique, where the different causes compete for attention under limited resources (https://en.wikipedia.org/wiki/Pareto_analysis). | * '''Pareto Analysis:''' Problem solving technique, where the different causes compete for attention under limited resources (https://en.wikipedia.org/wiki/Pareto_analysis). | ||
Line 164: | Line 196: | ||
* '''Value Stream Mapping:''' Lean-Management method that helps analyzing the current state of process as well as designing a future state. Follows the path of the value in its partial steps until it reaches the customer (https://en.wikipedia.org/wiki/Value-stream_mapping). | * '''Value Stream Mapping:''' Lean-Management method that helps analyzing the current state of process as well as designing a future state. Follows the path of the value in its partial steps until it reaches the customer (https://en.wikipedia.org/wiki/Value-stream_mapping). | ||
− | == Limitations | + | == Limitations and Drawbacks == |
Even though Continuous Improvement is an easy and cheap concept for organizations, some limitations must be taken into account. | Even though Continuous Improvement is an easy and cheap concept for organizations, some limitations must be taken into account. | ||
* '''Only suitable for consolidated Processes:''' Continuous Improvement can not be applied in a steadily changing environment. A company for instance that is specialized in delivering projects as a service, might experience a high diversity in their services. When standards are applied only to a low extend, then continuous has no base from which improvement can be achieved. The more the process idea is anchored in project management, the better continuous improvement can be implemented. | * '''Only suitable for consolidated Processes:''' Continuous Improvement can not be applied in a steadily changing environment. A company for instance that is specialized in delivering projects as a service, might experience a high diversity in their services. When standards are applied only to a low extend, then continuous has no base from which improvement can be achieved. The more the process idea is anchored in project management, the better continuous improvement can be implemented. | ||
Line 182: | Line 214: | ||
The book covers lean product design best practices that are designed to improve product development in an organization. Throughout the book, the lean philosophy is followed. Further, the books covers the important role of Continuous Improvement as the motor for applying lean concepts. The Concept is presented as a process that prevents getting stuck or slipping back. | The book covers lean product design best practices that are designed to improve product development in an organization. Throughout the book, the lean philosophy is followed. Further, the books covers the important role of Continuous Improvement as the motor for applying lean concepts. The Concept is presented as a process that prevents getting stuck or slipping back. | ||
− | |||
== References == | == References == | ||
<references /> | <references /> |
Latest revision as of 21:52, 27 March 2022
Contents |
[edit] Introduction
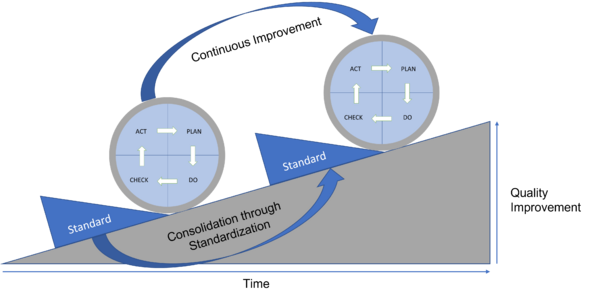
Continuous Improvement, also referred to as Kaizen, is a concept that is related to principles, methods and activities that have the target of continuously improving the performance of an organization or individual. In contrast to Innovation, Continuous Improvement focuses on incremental steps that eventually lead to big improvements over time, rather than breakthrough changes. In a wider and more cultural sense, the concept is based on the assumption that the world is steadily changing and can always be improved. The concept of Kaizen is Japanese and means kai = change, zen = to good (see figure 2). Although there are slight definitional differences, continuous improvement and kaizen are fundamentally similar. Hence the two terms are generally used synonymously[2].
In an organizational context, Continuous improvement is a strategic and long-term effort to enhance competitiveness by improving quality, cost and time. The efforts are usually directed towards achieving certain objectives. Continuous Improvement is therefore different to the concept of idea management, that revolves around collecting, implementing and rewarding diverse ideas of employees[3]. Improvement is achieved by applying an iterative process of constantly observing the current situation and implementing improvements. Improvements should then be standardized and disseminated to other areas. The concept of Continuous Improvement is illustrated in figure 1. Furthermore, Continuous Improvement tries to involve employees from all hierarchy levels of an organization in the improvement process. Therefore, it is a popular concept in industry as it is easy and cheap to implement and not limited to any industry and organizational size[2]. The main differences between Continuous Improvement and the general process of organizational innovation are listed in the table below.
Main Differences between Continuous Improvement and Innovation[1] | |
---|---|
Continuous Improvement | Innovation |
|
|
[edit] History of Continuous Improvement
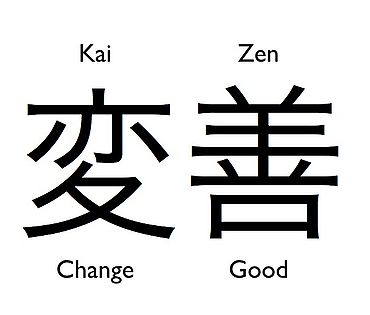
Continuous Improvement first appeared in Japan during the second world war. It was an answer to the numerous and serious damages that the country had suffered. The concept was used by authorities in order to reconstruct the country. Furthermore, the development of continuous improvement was supported by the use of the U.S. training program Training with Industry (TWI Inc.), which aimed at developing training programs for Japanese companies. The small-step approach was preferred, as resources were scarce and major change initiatives could not be afforded.
Even though elements of continuous improvement such as suggestion systems or quality systems were regularly used in Japanese industry, the concept only got further attention with the development of the oil crisis in 1973. In a period of financial constraints, companies such as Toyota have used the concept to achieve cost reductions with little expenditure of resources. Parallel, the company Canon was able to gain large benefits of up to 200 million US Dollar by launching a continuous improvement campaign. As the profits did not go unnoticed, Continuous Improvement made its way into the western economy in the 1980s. Remarkable benefits could be achieved by companies such as Xerox, Motorola, Harley Davidson, and General Electrics[2].
[edit] Continuous Improvement in Relation to Project, Program and Portfolio Management
Continuous Improvement was originally created to improve production processes and is today commonly used in that area. And even though Continuous Improvement focuses on the constant challenge to improve standards[2], it is applicable in any organizational area including project, program and portfolio management. Although projects are always unique to some degree, different projects in an organization often involve recurring activities, methods and processes that can be constantly improved. Furthermore, projects can be embedded in organizational processes that structures the frame within projects are being carried out. In a Project Environement, Continuous Improvement needs to be seen as a learning effect that is achieved project by project and can be transferred into the organizational knowledge base.
The project management standard ISO21500 recommends that Continuous Improvement, should influence thinking and behavior in the governance and management of projects. Furthermore, knowledge gained must be documented and shared throughout the organization, also to increase performance in future projects[5].
[edit] Key Concept and Benefits
The idea of Continuous Improvement is part of the bigger concept of Lean Management, which has its origins in the Toyota production System. The term lean is defined by Krajewski, who describes lean systems as systems that maximize the added value of each activity in an organization, by eliminating waste and delays[6]. Continuous Improvement is thus aiming at incrementally improving organizational activities by using less of everything or reducing waste or generally non-value adding work. Since customer orientation is a central component of Continuous Improvement, the value from the customer's point of view is considered in all activities[2].
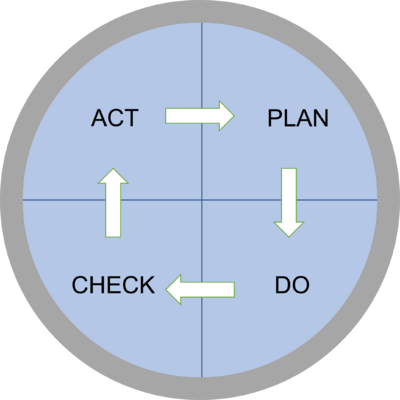
In his 1986 book Kaizen: The Key to Japan's Competitive Success, Imai Masaaki, who is seen as the father of the concept among others, summarizes how this can be achieved with basic principles[8].
Feedback: Improvement starts by the reflection of processes
Efficiency: Identification, reduction and elimination of non-value adding work in processes are the core activities and main purpose of Continuous Improvement
Evolution: Continuous Improvement is focused on incremental steps not major change initiatives[8]
The following points are some key features of Continuous Improvement
- Since ideas for improvement can come from all employees, they are often small in scope and therefore quick and easy to implement
- These ideas of smaller scale require little financial effort to implement
- The suggestions come from the employees who work in the process and therefore have expert knowledge. This is also more cost-effective than an analysis by specially assigned employees.
- The system motivates employees at all levels to continuously look for potential for improvement
- The system promotes employees' sense of responsibility towards their work
- The collaborative approach promotes teamwork and thus increases the motivation of employees[8]
A key idea of Continuous Improvement can be found in the PDCA Cycle, that was designed by William Edwards Deming. The Cycle describes an iterative process of continuous learning. It consists of the four Phases Plan, Do, Check, Act. The four phases should be followed for each problem to achieve sustainable improvement. Because of its iterative nature, the cycle must be repeated until the problem is effectively solved. The PDCA Cycle is the fundament of Continuous Improvement and should therefore be taken into consideration in all activities[7]. The principle of the PDCA Cycle is illustrated in figure 3.
Plan: The planning phase consists of the two major steps observation of the situation and proposing a hypothesis why the targeted situation can not be reached. Here, causes that prevent the desired situation from being reached need to be identified, e. g. with a Ishikawa Diagram or 5-Why Analysis. The first step also focuses on clarifying the desired future situation besides observing the current state.
Do: The Do phase revolves around the development and testing of countermeasures for the identified root causes.
Check: In this phase the data obtained by performing the countermeasure is analyzed. The result of this analysis should be the acceptance or rejection of the hypothesis. Gained insights should be documented.
Act: This step contains the actual implementation of the countermeasure. Countermeasures should now be standardized and monitored. A reflection about leasons learned is recommended. If the hypothesis test failed, a new one needs to be proposed[7].
The successful implementation of Continuous Improvement provides numerous benefits for organizations and individuals. Some of these benefits are named in the following table:
Benefits of Continuous Improvement[2] | |
---|---|
Quality Improvements | Quality issues are a focus of Continuous Improvement. Deviations in quality are analyzed in detail to prevent errors from recurring. |
Increased Productivity/Less Waste | Continuous Improvement fosters the efficient use of available resources, resulting in less need of resources for a given output. |
Employee skills improve | Continuous Improvement is not only aimed at improving standards and processes, but also human resources. Especially, since Continuous Improvement seeks to involve employees in various activities, they are continuously educated. Raising awareness of potential improvements, making employees understand their work better. |
Fostering a holistic view | Problems are often tackled in interdisciplinary work groups, thus assuring that different perspectives and interests are met. |
Customer Satisfaction increases | Improvement can be translated into customer satisfaction. For instance, quality improvement, end of project is reached faster, cost reduction. |
Higher motivation of employees/Increased participation | Through Continuous Improvement employees have the chance to actively contribute to organizational improvement. Seeing their ideas having an impact, can be factor for employee motivation. Furthermore, Continuous Improvement involves all employees meaning that combined organizational knowledge can be used. |
Increased employee self-esteem | Continuous Improvement can create a learning environment for all employees. As professional self-esteem depends on knowledge and experience, it grows as improvements continue over time. |
Higher Responsibility of employees | As problems are solved in multidisciplinary teams, all participating employees (from all hierarchy levels) are responsible for a certain task. |
[edit] Requirements and Implementation
Continuous Improvement can be implemented in an organization in different ways and to different extends. Whether the concept is implemented within a large campaign or in a more slow and organic manner depends on the needs and capabilities of each individual organization. It is important however, that the introduction of Continuous Improvement is not seen as a project, but as an ongoing process. The following chapter will present recommendations on how to implement Continuous Improvements as well as considerations that should be taken into account for both the preparation or implementation and actual execution phase.
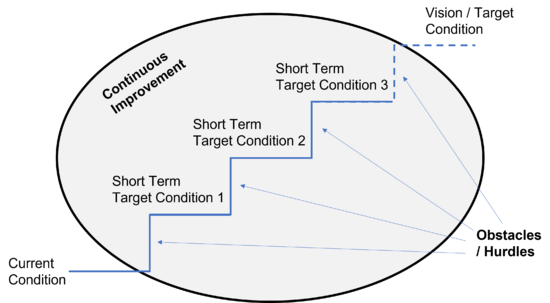
Describing a clear target condition: A first fundamental step in implementing continuous improvement is to define a target condition that describes a desired future situation. Describing a vision assures that all improvement efforts are clearly directed towards it. Change is only considered improvement when it is directed towards a common goal. The target conditions functions as guide for all involved people. The target condition should be medium to long term but can be supplemented by short term goals. By eliminating causes of hurdles on the way towards the vision, improvement is achieved step by step (see figure 4). Expressing the target state in terms of key indicators ensures a common understanding of the target and allows a clear statement on the extent to which improvements have been made [7]. The target condition is often already included in a company’s vision or strategy.
Securing Management Commitment: Continuous Improvement is a long-term effort that provides numerous benefits, but also requires the use resources. Furthermore, management is responsible for developing a culture, that fosters employee participation and therefore boost change and improvement. A Management that does not try to implement solutions directly or generally does not fully support the initiatives, risks that the actions fizzle out due to demotivation. Management should also empower internal working groups to implement their ideas[2].
Human Resources Training: With potentially all employees being included in continuous improvement, a certain knowledge level is required to effectively apply the concept. The level of knowledge depends on the different roles in the organization, however basic in problem solving methods (Fishbone, 5-Why, Pareto Analysis) are recommended[2].
Problem Detection: The actual process of Continuous Improvement starts with the detection of problems in organizational processes. A classical way of analysing processes is by conducting a value stream mapping. Within value stream mapping, the companies workflow, including all activities and people that contribute to delivering value to the customer wihtin the project are mapped out. This is done by separating a project into single value streams. The result is a visualization of the process with key information regarding material and information flows. The visualization can then be used for further analysis, with the goal of identifying parts of the workflow that require resources but do not create value for the customer[1]. Workshops or Circles, such as a Kaizen Event, are a suitable tool to examine the visualized processes and workflows in the team. Another possibility is to address problems in regular (e.g. daily morning meeting). It’s important to clearly define, where the current situation deviates from the targeted condition. Again, it’s beneficial if this can be expressed through Key Indicators [2].
In the early stages of Continuous Improvement it is recommended to start with a pilot. Depending on the organizational environment that projects are carried out in, this can for instance be a single department. By limiting the scope of the initial activities, it is easy for all employees involved to clearly see the benefits. This also ensures that the organization has the necessary resources to implement all defined measures and thus maintain motivation.
Problem Solving in Interdisciplinary Teams: To benefit from the different capabilities and expertise, multidisciplinary teams should be used as much as possible in the problem-solving process. The solution generation can also be examined within the initial workshop. Within this process, problem solving techniques such as 5-Why or Ishikawa should be used (See Chapter Tools and Methods in Continuous Improvements). By evaluating and prioritizing solutions in terms of suitability, a clear plan of measures is created. The implementation of measures works accordingly to the PDCA Cycle. The Team needs to be kept updated about the successful implementation improvement measures in regular follow ups. Furthermore, the team needs to be acknowledged for their achievements[2].
[edit] Tools and Methods
Within the Concept of Continuous Improvement, several Tools can be used in the improvement process. The following chapter will introduce commonly used tools for problem analysis as well as list of further helpful tools.
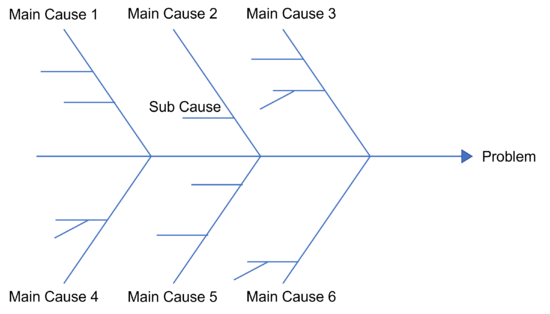
[edit] Ishikawa Diagram
A tool commonly used tool in connection with Continuous Improvement is the Ishikawa Diagram. The tool is also known as Root-Cause or Fishbone Diagram. The Ishikawa Diagram is a systemic approach to identify causes for a problem at hand. The main goal of the Ishikawa diagram is to reveal and break down the various causes that contribute to a problem. The identified causes are then addressed through mitigation measures.
Figure 1 shows a typical model of the Ishikawa Diagram. A problem is usually written on the right side of the model which is then connected to potential main causes. The main causes build the “bones” of the model. For the main causes, the 5M (Material, Machine, Manpower, Method and Milieu) are often used as a starting point. Afterwards, sub causes are added to the main causes. Theses sub causes are represented by the horizontal lines attach to main causes. The causes are usually identified in brainstorming activities, conducted by multidisciplinary teams. The subdivision of causes is done, til the problem at hand has been understood completely[9]. The causes are then tested for validity by executing the improvement actions until the desired effect has occurred, i.e. the problem has been solved. The effectiveness of the measures is usually confirmed by comparing the previously considered key figures.
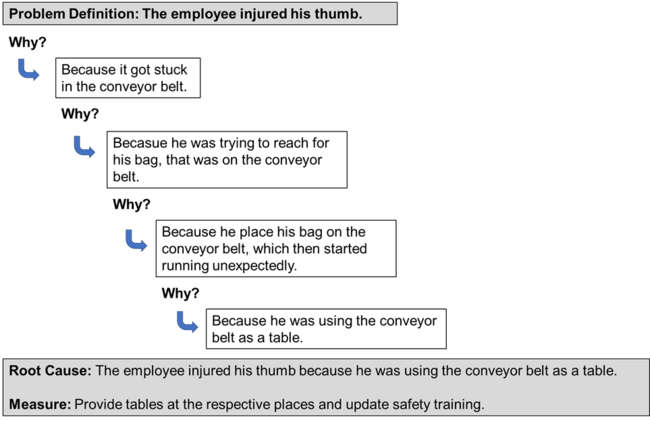
[edit] 5-Why Analysis
Another tool that is used in Continuous Improvement is the 5-Why Analysis. The tool tries to tackle the same issue as the Ishikawa Diagram, identifying the root cause of a problem, so that it does not occur again. The tool is applied by looking at a symptom (problem) and asking why it happened. The answer to why is then questioned 5 times. The process can usually be terminated if the why questions do not yield any new insights. Similarly, the why question can be asked more than five times[10]. The principle is illustrated as an example in figure 6.
The advantage of this systematic approach is that it is simple, easy to implement and can be used for most problems. However, there are some conditions that should be met for effective use of the tool. First, the problem at hand must be described in sufficient detail to allow conclusions to be drawn about causes. Second, questions must be answered truthfully. And last, it must be desired to analyze the problem down to the root cause and not to force symptom fighting in order to be able to achieve quick but not sustainable improvements. Identical to the Ishikawa Model, the 5 Why Method can be used individually, but works best when conducted by a multidisciplinary team[10]. A practical application of the tool could look like the following:
1. Team development and problem description.
2. Brainstorming in the Team for potential causes (answers the first why).
3. Following the different answers/paths with further why questions.
4. Discussion of the different logical paths and search for systemic root causes. Team decision for the most probable cause. Showing the result to other uninvolved parties can ensure that the result has a comprehensible logic.
5. Development and initiation of mitigation measures. The development should also take place as a team action[10].
Despite many advantages, there are also some shortcomings to the method. For example, if the problem is not broken down in enough detail, only symptoms are addressed instead of root causes. In particular, inexperienced users are susceptible to this error. Furthermore, the repeatability of the results is relatively low. Different teams often arrive at different results and therefore also at different corrective measures[10]. The tool is usually less of an indepth analysis in comparison with the ishikawa but can be used in combination with it.
[edit] Further Tools
Further Tools connected to Continuous Improvement that can be used with the objective of solving problems in a sustainable way are the following:
- Pareto Analysis: Problem solving technique, where the different causes compete for attention under limited resources (https://en.wikipedia.org/wiki/Pareto_analysis).
- Eight Disciplines Problem Solving: Method to identify, correct and eliminate problems. It combines different tools such as fishbone, histogram etc. and works as a guideline towards solving a problem (https://en.wikipedia.org/wiki/Eight_disciplines_problem_solving).
- Histogram: Tool used to represent the distribution of data e. g. failures (https://en.wikipedia.org/wiki/Histogram).
- Flowchart: Diagram that visualizes process and workflows. Can be used as a foundation for the analysis of processes (https://en.wikipedia.org/wiki/Flowchart).
- Value Stream Mapping: Lean-Management method that helps analyzing the current state of process as well as designing a future state. Follows the path of the value in its partial steps until it reaches the customer (https://en.wikipedia.org/wiki/Value-stream_mapping).
[edit] Limitations and Drawbacks
Even though Continuous Improvement is an easy and cheap concept for organizations, some limitations must be taken into account.
- Only suitable for consolidated Processes: Continuous Improvement can not be applied in a steadily changing environment. A company for instance that is specialized in delivering projects as a service, might experience a high diversity in their services. When standards are applied only to a low extend, then continuous has no base from which improvement can be achieved. The more the process idea is anchored in project management, the better continuous improvement can be implemented.
- Delivering only small changes: Continuous Improvement does not guarantee long lasting sustainable success. Even though the concept helps working towards an organization’s visions or long-term strategic targets, there is no certainty that this will happen by applying it. In certain situations, major, complex changes and realignments or needed. Continuous Improvement will not be able to provide that [7].
- Risk of Demotivation: Continuous Improvement is a concept that is often referred to as a booster for employee participation and motivation. However, while the concept certainly offers this benefit to companies, an improper application can also lead to the opposite effect. When ideas and suggestions from employees are not implemented or at least considered, this can be perceived as disinterest. Employees may then limit their participation because the effort is not seen as worthwhile. Similarly, needed resources for implementation of measures need to be provided to keep the motivation level high.
- Stakeholder Collaboration: Continuous Improvement requires the collaboration of different individuals, departments and areas within an organization. In addition, the successful application of the concept also means a change in the situation for various employees. As, different individuals and departments have different objectives, interest and needs, effective collaboration can be challenging[11].
[edit] Annotated Bibliography
J. L. Garcia-Alcaraz, M. Oropesa-Vento and A. A. Maldonado-Macias, Kaizen, Planning, Implementing and Controlling, Springer International Publishing, 2017.
The Book Kaizen – Planning, Implementing and Controlling investigates the concept of Kaizen in terms of it’s industrial application, key activities, critical success factors and gained benefits. The Concept is divided in the three phases, planning implementation and control. In a study of more 400 managers in Mexican maquiladoras, the different activities of each phase are analyzed. Furthermore, the activities are linked to the benefits gained through structural equation models, allowing to highlight the most important factors for successful Continuous Improvement.
L. G. Trabasso and M. V. P. Pessoa, "Continuous Improvement," in Lean Product Design and Development Journey, Springer International Publishing, 2016.
The book covers lean product design best practices that are designed to improve product development in an organization. Throughout the book, the lean philosophy is followed. Further, the books covers the important role of Continuous Improvement as the motor for applying lean concepts. The Concept is presented as a process that prevents getting stuck or slipping back.
[edit] References
- ↑ 1.0 1.1 1.2 M. Helmold, Lean Management and Kaizen - Fundamentals from Cases and Examples in Operations and Supply Chain Management, Springer, 2020.
- ↑ 2.0 2.1 2.2 2.3 2.4 2.5 2.6 2.7 2.8 J. L. Garcia-Alcaraz, M. Oropesa-Vento and A. A. Maldonado-Macias, Kaizen, Planning, Implementing and Controlling, Springer International Publishing, 2017.
- ↑ innolytics.ag, "The Complete Guide to the Continuous Improvement Process," [Online]. Available: https://innolytics-innovation.com/continuous-improvement-process/. [Accessed 28 February 2022].
- ↑ caterfly, "Kaizen - rejuvenating your organisation," [Online]. Available: https://caterfly.co.uk/kaizen-rejuvenating-your-organisation/. [Accessed 18 March 2022].
- ↑ International Organizations for Standardization, DS/ISO 21500:2021 - Project, programme and portfolio management - Context and concepts, 2021.
- ↑ L. Krajewski, L. Ritzman and M. MK, Operations management: processes and supply chains, Pearson, 2013.
- ↑ 7.0 7.1 7.2 7.3 L. G. Trabasso and M. V. P. Pessoa, The Lean Product Design and Development Journey, Springer International Publishing, 2016.
- ↑ 8.0 8.1 8.2 M. Imai, Kaizen: The key to Japan's competitive success, Random House Business, 1986.
- ↑ 9.0 9.1 R. K. Sharma, "Quality management tools and standards," in Quality Management Practices in MSME Sectors, Springer Science and Business Media Deutschland GmbH, 2021, pp. 25-62.
- ↑ 10.0 10.1 10.2 10.3 10.4 O. Serrat, "The 5-Whys Technique," February 2009. [Online]. Available: https://www.adb.org/publications/five-whys-technique.
- ↑ Ý. Gunnarsdóttir, "Five Barriers to Continuous Improvement," Process Excellence Network, 8 May 2014. [Online]. Available: https://www.processexcellencenetwork.com/lean-six-sigma-business-performance/articles/five-barriers-to-continuous-improvement-vote-for-t#:~:text=Here%20are%20what%20I%20consider%20the%20main%20barriers,Lean%20%2F%20SixSigma%20specialists%2C%20Quality%20Ma. [Accessed 9 March 2022].