Last Planner System as a project management tool
Chrisitane (Talk | contribs) (→Advantages and Disadvantages) |
|||
(30 intermediate revisions by one user not shown) | |||
Line 1: | Line 1: | ||
− | + | ''Developed by Christian Vindegaard Grønberg'' | |
− | + | ||
− | + | ||
− | + | ||
− | + | ||
− | + | ||
− | + | ||
+ | |||
+ | In managing construction projects implementation of Lean Construction for a better building phase is a great tool to optimize the processes. A way to implement Lean Construction is to use the Last Planner System (LPS) developed by Lean Construction DK<ref>[''http://leanconstruction.dk/''] ''Lean Construction DK''</ref>. The Last Planner System aims for a more even workflow, by simulation and planning by the craftsmen on the construction site. When implementing lean construction four different plans is made, these extend over several time periods, has various detail levels and different purposes. When using the LPS tool it is important that all craftsmen participates and agrees on the decisions made to achieve the a goal of less errors and a more effectively workflow. The tool has the benefits that it discovers misleading information and makes sure the work is done in the right order and is planned as effectively as possible - especially these points is where the LPS tool has an effect on reducing change orders. With that in mind the tool has to be implemented right or no results will show. One of the typical situations is when the project manager or the craftsman is dominating leading to bad cooperation in the group. | ||
+ | Precautions like this is important to be aware of when using the Last Planner System. | ||
__TOC__ | __TOC__ | ||
=Overview= | =Overview= | ||
==Background== | ==Background== | ||
− | In 1992 | + | In 1992 the Last Planner System (LPS) developed by Glenn Ballard. The idea behind the LPS was to improve the productivity, but during development the focus was changed to improving the work flows reliability \textcolor{red}{work flow reliability?}. The change was a result of the knowledge that Glenn Ballard had about manufacturing in revolutionary Lean Production and the thoughts that Lauri Koskelas had about the use of production theories in the construction sector<ref name="Ballard"> Herman Glenn Ballard, ''The Last Planner System of production control'', Doktorafhandling ved University of Birmingham, 2000</ref>. |
− | LPS is composed of several different researchers' theories, criteria and principles. Lauri Koskela | + | LPS is composed of several different researchers' theories, criteria and principles. A principal component is Lauri Koskela's five design criteria for a production control system, which can be seen below.<ref name="Ballard"></ref>. |
− | *Ensure healthy activities. This | + | *Ensure healthy activities. This means that a work task shouldn't be initiated until all preconditions are met. |
− | *The realization of | + | *The realization of tasks should be measured and monitored. This will be explained in detail in section Weekly Work Plan. |
− | *Reasons for a task to be realized must be investigated and causes removed. This will result in continuous improvement. | + | *Reasons for a task to be realized must be investigated and causes removed. This will result in continuous improvement. |
− | *Proposal to maintain a buffer of healthy activities are met in a planning with a time frame of 3-4 weeks. This is a pull system, which | + | *Proposal to maintain a buffer of healthy activities are met in a planning with a time frame of 3-4 weeks. This is a pull system, which ensures that all prerequisites are available for the activities. Furthermore, it helps to ensure that no excessive stock material on the spot. |
==About LPS== | ==About LPS== | ||
− | Overall | + | Overall the LPS is a tool used in Lean Construction, which has been developed specifically for the construction industry. It is designed to create a better predictability and dependable schedules. This is done by involving all the people in the building process, which results in better communication, clarity and flow. Furthermore it will lead to better compliance with time schedules, better economy and security, and greater job satisfaction. |
− | The whole LPS is divided into three levels: Phase Schedule, Look-Ahead Schedule and Weekly Work Plan | + | The whole LPS is divided into three levels: Phase Schedule, Look-Ahead Schedule and Weekly Work Plan. Each phase is elobaread in section 2. |
− | To get an overview of the various schedules and their functions which are used in LPS look at Table | + | To get an overview of the various schedules and their functions which are used in LPS look at Table 1. |
{| class="wikitable" | {| class="wikitable" | ||
− | |+ Overview of the various schedules in LPS <ref name="Rolf">Rolf Simonsen & Jakob Lemming, ''Lean Construction & Last Planner System'', Lean Construction, DK, 2015</ref> | + | |+ Table 1: Overview of the various schedules in LPS <ref name="Rolf">Rolf Simonsen & Jakob Lemming, ''Lean Construction & Last Planner System'', Lean Construction, DK, 2015</ref> |
!Style="width: 20%"|''Schedule'' | !Style="width: 20%"|''Schedule'' | ||
!Style="width: 50%"|''Function'' | !Style="width: 50%"|''Function'' | ||
Line 68: | Line 65: | ||
|} | |} | ||
− | It will be necessary to know the sequence of activities and the duration of each activity to prepare a proper level. However, it | + | It will be necessary to know the sequence of activities and the duration of each activity to prepare a proper level. However, it is impossible to know all the activities of a build-process from the beginning and therefore not possible to map it out in the correct order from the start. But it is possible to estimate the duration of an activity, as there will be several conditions that must be met. |
− | The Master Schedule in a traditional construction process is different from the Master Schedule in LPS. In a traditional construction Master Schedule | + | The Master Schedule in a traditional construction process is different from the Master Schedule in LPS. In a traditional construction the Master Schedule has the purpose to map several areas while the purpose in the Master Schedule for LPS is to make an overall activity plan for the whole project. For a traditional construction process is the purpose in the Master Schedule to map the following<ref>Sven Bertelsen, ''Håndbog i Trimmet Byggeri'', 1. version, Foreningen Lean Construction-DK, 2007</ref>: |
*When construction work shall be performed | *When construction work shall be performed | ||
*How should the construction process be implemented | *How should the construction process be implemented | ||
Line 79: | Line 76: | ||
*Which stages the construction process has | *Which stages the construction process has | ||
− | One of the problems with this type of planning is, that they are trying to identify and show | + | One of the problems with this type of planning is, that they are trying to identify and show too many things in one plan. Furthermore, is it impossible to plan ahead, because the construction process is very chaotic and unpredictable. |
This is the reason why the LPS is working on plans at various levels as well as working with the seven flows, that determines whether a given activity is healthy. Below will the four activities in the LPS be descibed. | This is the reason why the LPS is working on plans at various levels as well as working with the seven flows, that determines whether a given activity is healthy. Below will the four activities in the LPS be descibed. | ||
− | =Master Schedule= | + | =The four types of schedules= |
− | The Master Schedule indicates which types of activities, that has to be done in the construction process and is also an agreement between the client and the other stakeholders of what must be done. It includes an overall time- and activity plan which gives an overview of the important deadlines and milestones in the project. This schedule is not used for planning, but just as a guideline to evaluate whether the project is going in the right direction and | + | ==Master Schedule== |
+ | The Master Schedule indicates which types of activities, that has to be done in the construction process and is also an agreement between the client and the other stakeholders of what must be done. It includes an overall time- and activity plan which gives an overview of the important deadlines and milestones in the project. This schedule is not used for planning, but just as a guideline to evaluate whether the project is going in the right direction and therefore the single most important part of the Master Schedule is the delivery date. | ||
− | =Phase Schedule= | + | ==Phase Schedule== |
− | The purpose of the Phase Schedule is to | + | The purpose of the Phase Schedule is to determine the ideal building process in relation to the order and time spent within the limits set by the Master Schedule. |
+ | The Phase Schedule is prepared by the process manager and the chairmen of the subcontractors. The process manager is a new feature in construction management when we are talking about Lean Construction. The process manager is a leader who typically focus on production, the task is to ensure that everyone has an opportunity to take action if there is a failure or delay. Furthermore, the process manager is the one which controls the preparation of the Phase Schedule, who coordinate the term planning and the Weekly Work Plan. | ||
+ | However, it is important that the project manager and process manager isn't the same person. This is because the project manager is the person which carries out contractual matters related to the subcontractors while the process manager streamlines processes and creates a good vibe in the production conditions. So in short terms it means that the project manager is the subcontractors counter-part while the process manager is their team player. | ||
− | There are several different ways to finalize the Phase Schedule. It can for instance be prepared for the whole performance | + | There are several different ways to finalize the Phase Schedule. It can for instance be prepared for the whole performance, it can be compiled for each phase continuously throughout the project or it could be prepared for parts of the construction process, if there is several repetitive processes. However, one should keep in mind that the entire construction process has to be determined, thus there is a breakdown of the time available. During the process, there should be a special focus on the points where there will be several subcontractors on the construction site at the same time, since this could potentially create conflicts. |
− | It is often seen that the Phase Schedule is prepared as a Post-It plan see Figure | + | It is often seen that the Phase Schedule is prepared as a Post-It plan see Figure 1. In this way, is it possible for all subcontractors to record their activities on each Post-It. All the Post-It will be put up in chronological order. To make it more manageable, each subcontractor gets their own color of the Post-It. |
− | ''' | + | [[File:phase.jpg | 500px |center | thumb| |'''Figure 1:''' Example of Phase Schedule <ref name="Rolf"></ref>(click to zoom) ]] |
− | Afterwards | + | Afterwards the time for each activity specified and thus it is possible to develop a plan indicating when and how activities should be carried out. However, it is important to have in mind that it is not possible to follow the Phase Schedule 100%, as there always are unexpected complications in the construction process. Though there will not be changes in the Phase Schedule unless there are significant changes in the construction. |
− | =Look-Ahead Schedule= | + | ==Look-Ahead Schedule== |
− | To identify and remove any obstacles in the process | + | To identify and remove any obstacles in the process the Look-Ahead Schedule used. This will be reviewed as the work on the construction site is started. This will either be reviewed at the weekly site meeting with masters and constructors or at the weekly planning meeting with the chairmen of the construction site. |
The Look-Ahead Schedule are typically used every week to look six weeks forward in the schedule and then afterwards make small obstacle analysis on each of the upcoming activities. | The Look-Ahead Schedule are typically used every week to look six weeks forward in the schedule and then afterwards make small obstacle analysis on each of the upcoming activities. | ||
− | For each upcoming activity a constraint analysis is performed relative to The 7 Flows Figure | + | For each upcoming activity a constraint analysis is performed relative to The 7 Flows Figure 2, and examined whether there are any obstacles to the activities. |
− | + | [[File:SevenFlow.png | 300px |center | thumb| |'''Figure 2:''' Example of The 7 Flows (click to zoom)]] | |
− | + | ||
− | + | So before the activity starts will it be asked: Are the materials ordered? Is the previous activities completed? In order to avoid that this process becomes too unmanageable the constraints are only discussed when it is necessary. So materials to an activity is usually discussed 5-6 weeks ahead, because of the delivery time, whereas space is usually not discussed until 1 week prior to the activity. Figure 3 shows a typically Look-Ahead Schedule where solved constraints are marked and critical constraints are assigned a responsible for solving them. Parallel to The Look-Ahead Schedule two weeks of activities that are ready to be carries out are always ensured and the constraints list is updated. | |
− | =Weekly Work Plan= | + | [[File:LookAhead.PNG | 500px |center | thumb| |'''Figure 3:''' Look-Ahead Schedule <ref name="Rolf"></ref>(click to zoom)]] |
+ | |||
+ | ==Weekly Work Plan== | ||
On the weekly Work Plan meeting it is agreed and coordinated how the work is for the coming week. This is planned with short notice because it helps to secure the implementation of the plan. This meeting is involving a foreman from each subject at the construction site. | On the weekly Work Plan meeting it is agreed and coordinated how the work is for the coming week. This is planned with short notice because it helps to secure the implementation of the plan. This meeting is involving a foreman from each subject at the construction site. | ||
− | Before a meeting each subject has to | + | Before a meeting each subject has to think about what they can and will do in the upcoming week. The meeting is therefore used to coordinate with the other subjects, so they know if it is possible to implement their Weekly Work Plan. However, only activities that are clear of obstacles can be written on the Weekly Work Plan. |
− | There are many different ways to make a Weekly Work Plan. Some would rather fill a common form on a computer, while others draw it onto a building blueprints where they will be working in the coming week and some | + | There are many different ways to make a Weekly Work Plan. Some would rather fill a common form on a computer, while others draw it onto a building blueprints where they will be working in the coming week and some choose to fill out a simple form by hand. |
− | It is important that is the | + | It is important that it is the people on the construction site that fill out and discuss the work for the upcoming week. Since it is at this meeting where agreements on when you start and when you're done is reviewed, so there is space for the next team. The most important thing in this process is to comply with the agreements. However, in the case that the agreement can not be met, they have to inform their colleagues with plenty of notice. The meetings typically takes an hour and an agenda might look like this: |
*Reviewing the last week's Weekly Work Plans | *Reviewing the last week's Weekly Work Plans | ||
*Reviewing obstacle list | *Reviewing obstacle list | ||
Line 122: | Line 123: | ||
*Creating and coordinate the upcoming week's activities (The Weekly Work Plan) | *Creating and coordinate the upcoming week's activities (The Weekly Work Plan) | ||
− | ==Percent Planned Completed== | + | ===Percent Planned Completed=== |
− | Percent Planned Completed PPC is a way to describe how well the planners | + | Percent Planned Completed (PPC) is a way to describe how well the planners can plan together and thereby create a steady flow at the construction site. PPC helps to specify how many activities that have been carried out as planned, expressed as a percentage. Only when a task is fully implemented it can be described as completed, which means that there only is answers as yes and no when asked whether an activity is performed. It is then possible to calculate the value for PPC using the entire Weekly Work Plan by the equation below '''\ref{eg:PPC}''' from <ref name="Rolf"></ref> |
− | |||
− | + | <math>PPC=\frac{Total\ yes}{Total\ activities}</math> | |
− | PPC should not be | + | An example would be if there were 25 activities and 20 activities are carried out as planned, then the PPC would result in 80\%. |
+ | |||
+ | Furthermore, the purpose of PPC in LPS is also to create a motivation among each crew to improve the construction process, rather than only to improve efficiency internally. On a normal construction site the PPC indicator is often 50\% while at a construction site where LPS is used the indicator is at 80-90\%. This makes PPC a measure of the degree to which the chairmen and the crew must realize the promises and not an indication of whether the Master Schedule is followed<ref name="Rolf"></ref>. | ||
+ | |||
+ | PPC should not be constructed as a negative criticism but instead as positively criticism, which aims to improve the construction process in the future, so that the failure in the workflow can be improved. It is also important that PPC doesn't lead to the planners plan less than they can, in order to achieve a high PPC<ref name="Rolf"></ref>. | ||
=Discussion= | =Discussion= | ||
==Advantages and Disadvantages== | ==Advantages and Disadvantages== | ||
− | For any system there will always be advantages and disadvantages. As mentioned earlier, | + | For any system there will always be advantages and disadvantages. As mentioned earlier, the use of LPS achieves less waste, improves earnings and better job satisfaction. By use of the Phase Schedule it is possible to remove accompanied, if appropriate, obstacles in good time and thereby achieve a better flow at the construction site, since it is possible for the crew to work without interruption, which will result in less waste of time and resources. Earnings will also be increased by taking advantage of getting better at the construction site through better scheduling. Furthermore, it will mean that the construction project will be completed faster than normal, which will mean fewer overheads and salaries. Finally, LPS help to reduce the number of defects as more bugs will be discovered using the hurdle list. Therefore, errors will be updated continuously and can be rectified in time. Since there will be an increased planning and communication at the site this will help to reduce workplace accidents by about 36\%. LPS also helps to increase job satisfaction for all project participants, as the crew get more influence and the build management will achieve a better production<ref name="Rolf"></ref>. |
So as it can be seen there are plenty of advantages by making use of LPS and only few direct disadvantages. One of the disadvantages, is however that it can be difficult to take advantage of the LPS if the system is only known by a minimum of the work force beforehand<ref>Graham M. Winch, ''Managing Construction Projects - An Information Processing Approach'', The University og Manchester, UK, 2010</ref>. | So as it can be seen there are plenty of advantages by making use of LPS and only few direct disadvantages. One of the disadvantages, is however that it can be difficult to take advantage of the LPS if the system is only known by a minimum of the work force beforehand<ref>Graham M. Winch, ''Managing Construction Projects - An Information Processing Approach'', The University og Manchester, UK, 2010</ref>. | ||
=References= | =References= | ||
+ | <references/> | ||
=Annotated Bibliography= | =Annotated Bibliography= | ||
− | |||
− | + | * Alan Mossman (2013). ''Last Planner 5+1 crucial & collaborative conversations for predictable design & construction delivery''. The Change Business Ltd. | |
+ | ** ''Provides a more in-depth explanation of the different parts of the Last Planner and explains why construction people chose to use LPS.'' | ||
+ | * ''Lean Construction DK''''http://leanconstruction.dk/'' | ||
+ | ** ''A Danish company which are working with Lean Construction. This page has different kinds of guides, articles etc. which are explaning the concept.'' | ||
+ | * Rolf Simonsen & Jakob Lemming, ''Lean Construction & Last Planner System'', Lean Construction, DK, 2015 | ||
+ | ** ''Gives a good description of Lean Construction and how the Last Planner System works.'' |
Latest revision as of 13:46, 18 December 2018
Developed by Christian Vindegaard Grønberg
In managing construction projects implementation of Lean Construction for a better building phase is a great tool to optimize the processes. A way to implement Lean Construction is to use the Last Planner System (LPS) developed by Lean Construction DK[1]. The Last Planner System aims for a more even workflow, by simulation and planning by the craftsmen on the construction site. When implementing lean construction four different plans is made, these extend over several time periods, has various detail levels and different purposes. When using the LPS tool it is important that all craftsmen participates and agrees on the decisions made to achieve the a goal of less errors and a more effectively workflow. The tool has the benefits that it discovers misleading information and makes sure the work is done in the right order and is planned as effectively as possible - especially these points is where the LPS tool has an effect on reducing change orders. With that in mind the tool has to be implemented right or no results will show. One of the typical situations is when the project manager or the craftsman is dominating leading to bad cooperation in the group.
Precautions like this is important to be aware of when using the Last Planner System.
Contents |
[edit] Overview
[edit] Background
In 1992 the Last Planner System (LPS) developed by Glenn Ballard. The idea behind the LPS was to improve the productivity, but during development the focus was changed to improving the work flows reliability \textcolor{red}{work flow reliability?}. The change was a result of the knowledge that Glenn Ballard had about manufacturing in revolutionary Lean Production and the thoughts that Lauri Koskelas had about the use of production theories in the construction sector[2].
LPS is composed of several different researchers' theories, criteria and principles. A principal component is Lauri Koskela's five design criteria for a production control system, which can be seen below.[2].
- Ensure healthy activities. This means that a work task shouldn't be initiated until all preconditions are met.
- The realization of tasks should be measured and monitored. This will be explained in detail in section Weekly Work Plan.
- Reasons for a task to be realized must be investigated and causes removed. This will result in continuous improvement.
- Proposal to maintain a buffer of healthy activities are met in a planning with a time frame of 3-4 weeks. This is a pull system, which ensures that all prerequisites are available for the activities. Furthermore, it helps to ensure that no excessive stock material on the spot.
[edit] About LPS
Overall the LPS is a tool used in Lean Construction, which has been developed specifically for the construction industry. It is designed to create a better predictability and dependable schedules. This is done by involving all the people in the building process, which results in better communication, clarity and flow. Furthermore it will lead to better compliance with time schedules, better economy and security, and greater job satisfaction.
The whole LPS is divided into three levels: Phase Schedule, Look-Ahead Schedule and Weekly Work Plan. Each phase is elobaread in section 2.
To get an overview of the various schedules and their functions which are used in LPS look at Table 1.
Schedule | Function | Related to LPS |
---|---|---|
Master Schedule | Master Schedule
Sets project deadlines Is not used for managing What must be done |
Must |
Phase Schedule | Activity plan
Used for planning How and in what order should activities be carried out |
Should |
Look-Ahead Schedule | Moving schedule
5-8 week look-ahead Make activities ready through constraints analysis Decides when activities can be carried out |
Can |
Weekly Work Plan | Detailed work plan for upcoming week
Made by the trades Includes only sound and predictable activities When activities will be carried out |
Will |
It will be necessary to know the sequence of activities and the duration of each activity to prepare a proper level. However, it is impossible to know all the activities of a build-process from the beginning and therefore not possible to map it out in the correct order from the start. But it is possible to estimate the duration of an activity, as there will be several conditions that must be met.
The Master Schedule in a traditional construction process is different from the Master Schedule in LPS. In a traditional construction the Master Schedule has the purpose to map several areas while the purpose in the Master Schedule for LPS is to make an overall activity plan for the whole project. For a traditional construction process is the purpose in the Master Schedule to map the following[4]:
- When construction work shall be performed
- How should the construction process be implemented
- Who should perform the parts of the building
- When individual entrepreneurs has to start and end
- When the individual activities has to be performed
- When to deliver materials and supplies
- Which stages the construction process has
One of the problems with this type of planning is, that they are trying to identify and show too many things in one plan. Furthermore, is it impossible to plan ahead, because the construction process is very chaotic and unpredictable.
This is the reason why the LPS is working on plans at various levels as well as working with the seven flows, that determines whether a given activity is healthy. Below will the four activities in the LPS be descibed.
[edit] The four types of schedules
[edit] Master Schedule
The Master Schedule indicates which types of activities, that has to be done in the construction process and is also an agreement between the client and the other stakeholders of what must be done. It includes an overall time- and activity plan which gives an overview of the important deadlines and milestones in the project. This schedule is not used for planning, but just as a guideline to evaluate whether the project is going in the right direction and therefore the single most important part of the Master Schedule is the delivery date.
[edit] Phase Schedule
The purpose of the Phase Schedule is to determine the ideal building process in relation to the order and time spent within the limits set by the Master Schedule. The Phase Schedule is prepared by the process manager and the chairmen of the subcontractors. The process manager is a new feature in construction management when we are talking about Lean Construction. The process manager is a leader who typically focus on production, the task is to ensure that everyone has an opportunity to take action if there is a failure or delay. Furthermore, the process manager is the one which controls the preparation of the Phase Schedule, who coordinate the term planning and the Weekly Work Plan. However, it is important that the project manager and process manager isn't the same person. This is because the project manager is the person which carries out contractual matters related to the subcontractors while the process manager streamlines processes and creates a good vibe in the production conditions. So in short terms it means that the project manager is the subcontractors counter-part while the process manager is their team player.
There are several different ways to finalize the Phase Schedule. It can for instance be prepared for the whole performance, it can be compiled for each phase continuously throughout the project or it could be prepared for parts of the construction process, if there is several repetitive processes. However, one should keep in mind that the entire construction process has to be determined, thus there is a breakdown of the time available. During the process, there should be a special focus on the points where there will be several subcontractors on the construction site at the same time, since this could potentially create conflicts.
It is often seen that the Phase Schedule is prepared as a Post-It plan see Figure 1. In this way, is it possible for all subcontractors to record their activities on each Post-It. All the Post-It will be put up in chronological order. To make it more manageable, each subcontractor gets their own color of the Post-It.
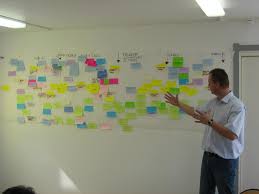
Afterwards the time for each activity specified and thus it is possible to develop a plan indicating when and how activities should be carried out. However, it is important to have in mind that it is not possible to follow the Phase Schedule 100%, as there always are unexpected complications in the construction process. Though there will not be changes in the Phase Schedule unless there are significant changes in the construction.
[edit] Look-Ahead Schedule
To identify and remove any obstacles in the process the Look-Ahead Schedule used. This will be reviewed as the work on the construction site is started. This will either be reviewed at the weekly site meeting with masters and constructors or at the weekly planning meeting with the chairmen of the construction site.
The Look-Ahead Schedule are typically used every week to look six weeks forward in the schedule and then afterwards make small obstacle analysis on each of the upcoming activities.
For each upcoming activity a constraint analysis is performed relative to The 7 Flows Figure 2, and examined whether there are any obstacles to the activities.
So before the activity starts will it be asked: Are the materials ordered? Is the previous activities completed? In order to avoid that this process becomes too unmanageable the constraints are only discussed when it is necessary. So materials to an activity is usually discussed 5-6 weeks ahead, because of the delivery time, whereas space is usually not discussed until 1 week prior to the activity. Figure 3 shows a typically Look-Ahead Schedule where solved constraints are marked and critical constraints are assigned a responsible for solving them. Parallel to The Look-Ahead Schedule two weeks of activities that are ready to be carries out are always ensured and the constraints list is updated.
[edit] Weekly Work Plan
On the weekly Work Plan meeting it is agreed and coordinated how the work is for the coming week. This is planned with short notice because it helps to secure the implementation of the plan. This meeting is involving a foreman from each subject at the construction site.
Before a meeting each subject has to think about what they can and will do in the upcoming week. The meeting is therefore used to coordinate with the other subjects, so they know if it is possible to implement their Weekly Work Plan. However, only activities that are clear of obstacles can be written on the Weekly Work Plan.
There are many different ways to make a Weekly Work Plan. Some would rather fill a common form on a computer, while others draw it onto a building blueprints where they will be working in the coming week and some choose to fill out a simple form by hand.
It is important that it is the people on the construction site that fill out and discuss the work for the upcoming week. Since it is at this meeting where agreements on when you start and when you're done is reviewed, so there is space for the next team. The most important thing in this process is to comply with the agreements. However, in the case that the agreement can not be met, they have to inform their colleagues with plenty of notice. The meetings typically takes an hour and an agenda might look like this:
- Reviewing the last week's Weekly Work Plans
- Reviewing obstacle list
- Review of the Phase Schedule (if this isn't discussed at the construction meetings)
- Creating and coordinate the upcoming week's activities (The Weekly Work Plan)
[edit] Percent Planned Completed
Percent Planned Completed (PPC) is a way to describe how well the planners can plan together and thereby create a steady flow at the construction site. PPC helps to specify how many activities that have been carried out as planned, expressed as a percentage. Only when a task is fully implemented it can be described as completed, which means that there only is answers as yes and no when asked whether an activity is performed. It is then possible to calculate the value for PPC using the entire Weekly Work Plan by the equation below \ref{eg:PPC} from [3]
An example would be if there were 25 activities and 20 activities are carried out as planned, then the PPC would result in 80\%.
Furthermore, the purpose of PPC in LPS is also to create a motivation among each crew to improve the construction process, rather than only to improve efficiency internally. On a normal construction site the PPC indicator is often 50\% while at a construction site where LPS is used the indicator is at 80-90\%. This makes PPC a measure of the degree to which the chairmen and the crew must realize the promises and not an indication of whether the Master Schedule is followed[3].
PPC should not be constructed as a negative criticism but instead as positively criticism, which aims to improve the construction process in the future, so that the failure in the workflow can be improved. It is also important that PPC doesn't lead to the planners plan less than they can, in order to achieve a high PPC[3].
[edit] Discussion
[edit] Advantages and Disadvantages
For any system there will always be advantages and disadvantages. As mentioned earlier, the use of LPS achieves less waste, improves earnings and better job satisfaction. By use of the Phase Schedule it is possible to remove accompanied, if appropriate, obstacles in good time and thereby achieve a better flow at the construction site, since it is possible for the crew to work without interruption, which will result in less waste of time and resources. Earnings will also be increased by taking advantage of getting better at the construction site through better scheduling. Furthermore, it will mean that the construction project will be completed faster than normal, which will mean fewer overheads and salaries. Finally, LPS help to reduce the number of defects as more bugs will be discovered using the hurdle list. Therefore, errors will be updated continuously and can be rectified in time. Since there will be an increased planning and communication at the site this will help to reduce workplace accidents by about 36\%. LPS also helps to increase job satisfaction for all project participants, as the crew get more influence and the build management will achieve a better production[3].
So as it can be seen there are plenty of advantages by making use of LPS and only few direct disadvantages. One of the disadvantages, is however that it can be difficult to take advantage of the LPS if the system is only known by a minimum of the work force beforehand[5].
[edit] References
- ↑ [http://leanconstruction.dk/] Lean Construction DK
- ↑ 2.0 2.1 Herman Glenn Ballard, The Last Planner System of production control, Doktorafhandling ved University of Birmingham, 2000
- ↑ 3.0 3.1 3.2 3.3 3.4 3.5 3.6 Rolf Simonsen & Jakob Lemming, Lean Construction & Last Planner System, Lean Construction, DK, 2015
- ↑ Sven Bertelsen, Håndbog i Trimmet Byggeri, 1. version, Foreningen Lean Construction-DK, 2007
- ↑ Graham M. Winch, Managing Construction Projects - An Information Processing Approach, The University og Manchester, UK, 2010
[edit] Annotated Bibliography
- Alan Mossman (2013). Last Planner 5+1 crucial & collaborative conversations for predictable design & construction delivery. The Change Business Ltd.
- Provides a more in-depth explanation of the different parts of the Last Planner and explains why construction people chose to use LPS.
- Lean Construction DK'http://leanconstruction.dk/
- A Danish company which are working with Lean Construction. This page has different kinds of guides, articles etc. which are explaning the concept.
- Rolf Simonsen & Jakob Lemming, Lean Construction & Last Planner System, Lean Construction, DK, 2015
- Gives a good description of Lean Construction and how the Last Planner System works.