Quality Control
(Created page with "Defects and errors in construction projects have been subject to attention in the medias and debates through out the years. A general consensus of a lack of quality on the con...") |
|||
(164 intermediate revisions by one user not shown) | |||
Line 1: | Line 1: | ||
− | Defects and errors in construction projects have been subject to attention in the | + | ''Developed by Silja Tea Nielsen'' |
− | Building defects in Danish construction: project characteristics influencing the occurrence of defects at handover"</ref>. When managing quality in a project an important aspect is Quality Control (QC), which is the | + | |
+ | |||
+ | Defects and errors in construction projects have been subject to attention in the media and debates throughout the years. A general consensus of a lack of quality on the construction sites exists, thus an increasing effort have been made to improve the quality of construction projects by a number of political initiatives<ref name="art1Kir">Schultz, Casper S.; Jørgensen, Kirsten; Bonke, Sten and Rasmussen, Grane M. G.; Architectural Engineering and Design Management; Taylor and Francis Group; 2015, "Building defects in Danish construction: project characteristics influencing the occurrence of defects at handover"</ref>. When managing quality in a project an important aspect is Quality Control (QC), which is the focus of this article. First the definition of QC is elaborated and examples of process QC and product QC is given, in order to clarify the difference between the two types of QC. The standard DS/ISO 21500 outlines different aspects that have to be considered when performing QC, why these are mentioned in the article. Different QC policies and techniques exist and their objectives, advantage and disadvantages are elucidated. At last limiting conditions when performing QC are stated. | ||
=Definition of Quality Control= | =Definition of Quality Control= | ||
− | + | The aim of QC in construction projects is to assure high quality of the construction being built and the individual processes within the project. In this content “high quality” denotes fulfilling standards and the established quality requirements of the specific project <ref name="winch">Winch, Graham M.; Wiley-Blackwell; 2010; "Managing Construction Projects; Second edition "</ref>. It is important to investigate the causes of the arising problems, as well as finding ways to eliminate unsatisfactory performance when performing QC, thus corrective, preventive and predictive QC policies are essential. QC is a part of managing conformance in construction projects, and QC can continuously be improved by [[Total Quality Management]]. | |
== Product Quality Control vs. Process Quality Control == | == Product Quality Control vs. Process Quality Control == | ||
− | [[File:Processdefinition.png|thumb||350px|'''Figure 1:''' Examples of input and output parameters in a process | + | [[File:Processdefinition.png|thumb||350px|'''Figure 1:''' Examples of input and output parameters in a process <ref name="TQMOakland">Oakland, John S., Quality and Reliability Engineering International, volume 9, issue 6, 1993, "Total quality management"</ref>]] |
− | QC deals with the specific products as well as the processes as mentioned. A certain understanding of the process or product is needed in order to perform QC | + | QC deals with the specific products as well as the processes as mentioned above. A certain understanding of the process or product is needed in order to perform QC. A process is the transformation from a set of inputs to the desired output. The inputs can e.g. be materials, procedures and knowledge as illustrated on Figure 1. Each process in a construction project can be analyzed by itself and afterward actions can be determined in order to improve the process, thus the process QC become preventive <ref name="STC">Oakland, John S., Rutledge Taylor and Francis Group, 2008, "Statistical Process Control", Sixth edition</ref>. |
Examples of process QC can for example by: | Examples of process QC can for example by: | ||
* Measuring the temperature of the concrete during casting and check if it fulfills specifications. | * Measuring the temperature of the concrete during casting and check if it fulfills specifications. | ||
− | * Controlling the | + | * Controlling the QC process by checking if the QC methods agreed upon are carried out <ref name="IRMI">IRMI, "Construction Quality Management", access: 12-06-2017,https://www.irmi.com/articles/expert-commentary/construction-quality-management</ref>. |
− | + | ||
− | QC of | + | QC of a product concerns the quality of the output/result of the process instead. It can be a product of a process in the design phase as well as in the construction phase. The output does not have to be a physical product but can just as well be a service, information or conducted paperwork as illustrated by Figure 1. Examples of defects that product QC deals with are: |
* Missing information in drawing material | * Missing information in drawing material | ||
* Moisture damage of a construction element | * Moisture damage of a construction element | ||
− | |||
= Performing Quality Control= | = Performing Quality Control= | ||
Line 24: | Line 24: | ||
{| class="wikitable floatright" style="margin-left: auto; margin-right: auto; border: none;" | {| class="wikitable floatright" style="margin-left: auto; margin-right: auto; border: none;" | ||
|- | |- | ||
− | |+ style="text-align:center;"|'''Table 1''': Primary inputs and outputs when performing quality control<ref name="ISO21500">Danish Standards, 2013, "DS/EN 21500: Guidance on project management, | + | |+ style="text-align:center;"|'''Table 1''': Primary inputs and outputs when performing quality control<ref name="ISO21500">Danish Standards Foundation, 2013, "DS/EN 21500: Guidance on project management", Second edition</ref> |
! scope="col" style="width: 225px;" |Primary inputs | ! scope="col" style="width: 225px;" |Primary inputs | ||
! scope="col" style="width: 225px;" |Primary outputs | ! scope="col" style="width: 225px;" |Primary outputs | ||
Line 47: | Line 47: | ||
Corretive actions | Corretive actions | ||
|} | |} | ||
− | + | Tools and inspection procedures are needed, in order to perform QC. These inspection procedures and QC tools are specified in the part of the conformance management called [[Quality assurance methods in project management | Quality Assurance]] <ref name="winch">Winch, Graham M.; Wiley-Blackwell; 2010; "Managing Construction Projects; Second edition "</ref>. The primary inputs and outputs when performing QC in construction projects given by the standard DS/ISO 21500 <ref name="ISO21500">Danish Standards Foundation, 2013, "DS/EN 21500: Guidance on project management", Second edition</ref> are shown in Table 1. Here it is shown that QC is highly dependent of good planning, as the primary inputs are a result of planning the quality in the project. The primary outputs indicate, that checking if requirements are being meet is not satisfactory alone, but QC includes documentation, communication and analysis as well. Furthermore it is shown that QC also has to prevent defects and non-conformance from taking place. | |
− | The standard DS/ISO 21500 <ref name="ISO21500">Danish Standards, 2013, "DS/EN 21500: Guidance on project management, | + | |
+ | The standard DS/ISO 21500 <ref name="ISO21500">Danish Standards Foundation, 2013, "DS/EN 21500: Guidance on project management", Second edition</ref> states that QC should be performed during the whole project life cycle and that it includes following aspects: | ||
*Monitoring the quality of the processes and detect defects. | *Monitoring the quality of the processes and detect defects. | ||
− | * | + | *Analyzing of the causes of defects and non-conforming performance. |
*Eliminate unsatisfactory performance by identifying preventive actions and change requests. | *Eliminate unsatisfactory performance by identifying preventive actions and change requests. | ||
− | * | + | *Communicating the changed requests and necessary corrective actions to project organization members. |
− | Documentation is not mentioned directly by the standard, but it is implied in the last aspect "communication" as it is impossible to tell the craftsman which corrective actions that have to be | + | Documentation is not mentioned directly by the standard, but it is implied in the last aspect "communication" as it is impossible to tell the craftsman, which corrective actions that have to be accomplished, without documentation. The documentation can be carried out with control tables, but in large construction projects digital quality documentation is preferred as many parts perform QC. By using digital documentation the position and date of the defect can be noted on the layout drawing, so the craftsmen get a clear outline of the defects <ref name="BigReport">Jørgensen, Kirsten; Schultz, Casper S.; Bonke, Sten, Technical University of Denmark, 2013, "Processer og metoder i det fejlfrie byggeri: Erfaringer og anbefalinger fra projektledere i entreprenørbranchen"</ref>. |
= Correct, prevent & predict= | = Correct, prevent & predict= | ||
− | With the increased focus on minimizing non-conformance in construction projects the main goal of QC | + | With the increased focus on minimizing non-conformance in construction projects the main goal of QC has shifted from a corrective to a predictive policy as illustrated on Figure 2. The intention of this shift is to predict the errors and defect, and thereby prevent them from happen. By achieving predictive and preventive QC the cost of the project will be decreased and time can be saved. |
[[File:CPP.png||center|thumb|400px||'''Figure 2:''' Quality Control policies and associated actions]] | [[File:CPP.png||center|thumb|400px||'''Figure 2:''' Quality Control policies and associated actions]] | ||
− | + | In the other industries the shift from corrective to preventive/predictive QC has already been seen, while different issues puts limits to the shift in the construction industry. Graham M. Winch mention four issues that slow down the development<ref name="winch">Winch, Graham M.; Wiley-Blackwell; 2010; "Managing Construction Projects; Second edition "</ref>: | |
− | + | ||
− | + | *Construction projects are often unique, and this limits the value of experience and knowledge gained, as the project does not last long enough to achieve zero defects | |
+ | *It is hard to implement statistical approaches to improve the processes, as the processes in the project only are repeated a limited number of times | ||
+ | *There are no rewards for the designer to make error free drawings, as this mostly benefits the contractor. So why should the designer invest time and money in QC of their drawings? | ||
+ | *The partners involved in construction project do not have a common goal, why is it hard to manage conformance for everyone. | ||
− | + | In following the three QC policies (corrective, preventive and predictive) will be clarified. | |
− | + | ||
− | + | ==Corrective Quality Control== | |
+ | [[File:Failureillustration.png|thumb||200px|'''Figure 3<ref name="Failure">The church of Jesus Christ of latter-day saints, "Helaman 1–6", access: 12-06-2017,https://www.lds.org/manual/book-of-mormon-teacher-resource-manual/helaman-1-6?lang=eng</ref>:''' Corrective QC alerts after defects occur .]] | ||
− | + | Corrective QC is necessary when non-conformance or a fatal event has occurred, thus corrective QC is defined as a reactive approach. This approach of QC is necessary because unexpected events and defect always will occur in construction projects. The ideal project where all problems are prevented is hard to establish, since many people, partners and processes are involved in the project. Questions like “have we met the requirements?” and “what went wrong?” are frequently asked, when using corrective QC. | |
− | + | ||
− | + | This type of quality control can be expensive, due to the fact that rework can be very comprehensive<ref name="art1Kir">Schultz, Casper S.; Jørgensen, Kirsten; Bonke, Sten and Rasmussen, Grane M. G.; Architectural Engineering and Design Management; Taylor and Francis Group; 2015, "Building defects in Danish construction: project characteristics influencing the occurrence of defects at handover"</ref>. Correcting serious errors can also be time consuming depending on how many parts that have to be involved in the rework, likewise new material deliveries can result in delays. | |
− | + | In order to correct errors, knowledge of the causes to the problem has to be obtained. Performing corrective QC can be accomplished with different techniques, and one technique is “cause and effects diagrams”, which is elaborated in following. | |
− | + | ==Preventive Quality Control== | |
+ | [[File:Preventmistakes.png|thumb||200px|'''Figure 4 <ref name="prevent">T&W Church solutions, "The Top 7 Mistakes Made by Church Building Committees and How to Prevent Them!!!", access: 12-06-2017, http://www.tw-church.com/The-Top-7-Mistakes-Made-by-Chur.html</ref>:''' Preventive QC alerts before errors occur.]] | ||
− | = | + | By changing the strategy of QC from corrective to preventive the questions are changed to "can we do the job correctly" and "are we doing the job correctly" <ref name="TQMOakland">Oakland, John S., Quality and Reliability Engineering International, volume 9, issue 6, 1993, "Total quality management"</ref>. A certain amount of knowledge and experience is required in order to answer the questions, and thereby prevent failures and non-conformance from happening. It is a common problem that the people trying to control procedures do not have the necessary competencies to do so. For this reason [https://en.wikipedia.org/wiki/W._Edwards_Deming W. Edwards Deming], a guru of quality management, came with the advice <ref name="STC">Oakland, John S.; Rutledge Taylor and Francis Group, 2008, "Statistical Process Control", Sixth edition</ref>: |
− | |||
− | + | <div class="center" style="width: auto; margin-left: auto; margin-right: auto;">'' "Don't just do something, sit here and think" ''</div> | |
− | |||
− | + | One way to increase preventive QC in construction projects is to make specifications, recommendations and regulations of work procedures, thus the people involved in the project can get a clear overview of which aspects of the procedure to focus on in order to prevent non-conformance. | |
− | + | ||
− | == | + | ===Continuous, delivery and start-up control === |
− | + | ||
− | + | A qualitative analysis of processes and methods in flawless construction projects, which is based on experience from project managers, showed that continuous QC, delivery QC and start-up QC are very import in order to prevent fatal errors <ref name="BigReport">Jørgensen, Kirsten; Schultz, Casper S.; Bonke, Sten, Technical University of Denmark, 2013, "Processer og metoder i det fejlfrie byggeri: Erfaringer og anbefalinger fra projektledere i entreprenørbranchen"</ref>: | |
− | + | A way to prevent expensive corrective actions is to perform continuous QC. This can for example include thermo graphic measurements of the first room finished, and if non-conforming performance is found, then preventive actions can be made to assure the quality of the remaining rooms. | |
− | + | ||
− | + | QC at delivery of materials e.g. reinforcement and concrete elements are essential, as these elements often are hidden, thus later control is impossible. Poor quality of these elements could be fatal as it can result in construction failure. | |
− | + | Start-up QC at the shift between contractors can prevent errors from occurring. This way the quality of the previous work is assured and the following work is not going to hide defects. The hidden defects can potentially result in critical errors, which will be very expensive and time consuming to correct. This concept is also called "stop the line" in lean construction, where the following work are set on hold until all errors from previous work are corrected <ref name="LEAN">Simonsen, Rolf, Værdiskabende Byggeproces, 2017, "Lean Construction & | |
+ | Last Planner System"</ref>. | ||
− | + | ==Predictive Quality Control== | |
+ | [[File:Predict.png|thumb||200px|'''Figure 5<ref name="predicts">Skipprichard Leadership insights, "The Surprising Predictive Power of Analytics", access: 12-06-2017, https://www.skipprichard.com/the-surprising-predictive-power-of-analytics/</ref>:''' Predictive QC alerts at trends of possible failure.]] | ||
− | = | + | Predictions of possible failures is necessary, in order to determine preventive actions. Graham M. Winch states<ref name="winch">Winch, Graham M.; Wiley-Blackwell; 2010; "Managing Construction Projects; Second edition "</ref>: |
− | + | ||
+ | <div class="center" style="width: auto; margin-left: auto; margin-right: auto;">'' "Little progress can be made in understanding the roots of quality problems unless the outputs from the process are measured and analyses" ''</div> | ||
− | |||
− | + | This means predictions should be based upon analysis of data and well-founded arguments thus unnecessary actions are not initiated. Using the predictive QC policy it is important that the problem leave digital footprints before it occurs, otherwise predictions can not be made<ref name="maintance">Cyient, 2016, "Engineering solutions for predictive maintenance in rail"</ref>. Valuable predictions can be made by modern technology, that makes it possible to collect and analyze large amounts of data from different systems. Monitoring processes makes it possible to perform real-time control and predict failures before they occur <ref name="sensors2">Navon, Ronie; Elsevier, Automation in Construction 14, 2005, "Automated project performance control of construction projects" </ref>. Various advanced sensor systems is developed and can be integrated as a part of the inspection procedures on the construction site. These systems create the opportunity of frequently gathering "as-built" data. The collected data have to be carefully analyzed and compared frequently with specifications and "as-designed" models. If divisions are found it has to be evaluated, if it will induce defects later on. | |
− | + | === Monitoring === | |
+ | By applying a sensor system of laser scanners it becomes possible to produce a three-dimensional model of the complete construction or construction parts, as it is built. The three-dimensional model makes it easier to control if the work performed corresponds to the model made in the design phase. Using laser scanners to produce "as-bulit" models can be quite comprehensive, as the scanners deliver point clouds that have to be transformed into objects. This increases the efficiency of the sensor system in order to obtain a real-time model <ref name="sensors">Akincia, Burcu; Boukampa, Frank; Gordona, Chris; Huberb, Daniel; Lyonsb, Catherine; Parkc, Kuhn; Elsevier, Automation in Construction 15, 2006, "A formalism for utilization of sensor systems and integrated project models for active construction quality control" </ref>. | ||
− | |||
− | + | Temperature sensors make it possible to provide real-time data of the temperature development in processes. It can for example be used to predict the maturity and thereby the strength of concrete during hardening. This way framework will not be removed too early, and thereby defects or even critical failures can be prevented. By mounting strain-gages on structural elements the strains in the element during a process can be measured. If a large element e.g. a bridgedeck is going to be transported to another location, it can be relevant to ensure that no damages occurred during the move. By using this sensor system mounting of a damaged bridge deck can be prevented, which can be very expensive and time consuming to repair. | |
− | |||
− | + | When monitoring processes it is crucial to predict what kind of damage that might occur, in order to choose the right sensor system, as you only receive the data that you "asked for". Another important aspect during monitoring is to prevent technical failures such as cut wires and filled data loggers <ref name="sensors">Akincia, Burcu; Boukampa, Frank; Gordona, Chris; Huberb, Daniel; Lyonsb, Catherine; Parkc, Kuhn; Elsevier, Automation in Construction 15, 2006, "A formalism for utilization of sensor systems and integrated project models for active construction quality control" </ref>. | |
− | + | =Quality control techniques= | |
− | + | Various techniques and tools to perform QC are developed through time. Frequently used tools are Ishikawa's seven tools <ref name="IshikawaBook">Ishikawa, Kauro, Tokyo 3A Corporation, 1990, "Introduction to Quality Control "</ref>: Cause-and-effect diagram, Check sheet, Control chart, Histogram, Pareto chart, Scatter diagram, Flow charts. In the following two of the tools (Cause-and-effect diagrams and Flow charts) will be described in relation to QC in construction projects. | |
− | + | ||
− | Cause and effect diagrams | + | == Cause-and-effect diagrams == |
+ | [[File:CauseEffectDiagram.png|thumb||400px|'''Figure 6''': Structure of a cause effect diagram with six chosen categories of causes, which all have an influence on the overall problem. The secondary cause are attached to the primary causes by small arrows <ref name="CED">Wikipedia, "Ishikawa diagram ", access: 11-06-2017, https://en.wikipedia.org/wiki/Ishikawa_diagram</ref>.]] | ||
− | + | Cause-and-effect diagrams also go under the names “fishbone diagram” (due to the shape) and “Ishikawa diagram” (after the inventor of the technique). The diagram separates the problem (the effect of the causes) from the causes. The basic idea of the technique is to work back from the problem by asking: “why did it occur”, thus finding the different roots to the problem <ref name="winch">Winch, Graham M.; Wiley-Blackwell; 2010; "Managing Construction Projects; Second edition "</ref>. Each cause is thereby found by using a form of brainstorm technique, and they are grouped under different categories. A cause can either be a primary cause or a secondary cause. The structure of the diagram is shown on Figure 6. | |
− | |||
− | = | + | A cause-and-effect diagram shows that there often are several roots to problem, and that several corrective/preventive actions have to be performed. This allegation becomes clear by grouping the causes under different categories, because it illustrates the difficulties of complex processes. The categories often include people, process/methods, equipment/machines, material, environment and management, as these are some of the essential elements in construction projects <ref name="CED">Wikipedia, "Ishikawa diagram ", access: 11-06-2017, https://en.wikipedia.org/wiki/Ishikawa_diagram</ref>. |
− | + | ==Value stream mapping (Flow charts)== | |
− | + | [[File:Valuestreammapping.png|thumb||400px|'''Figure 8'''<ref name="VSMpic">Lean homebuilding, "Value stream mapping ", access: 13-06-2017, https://leanhomebuilding.wordpress.com/2010/04/14/value-stream-maps-visualizing-waste/</ref>, With value stream mapping you can identify elements in a current process that generates non-conformance, and thereby improve the process for future state.]] | |
− | + | Value stream mapping (VSM) is a preventive QC technique, that focus on understanding the details of all the discrete elements in a process <ref name="winch">Winch, Graham M.; Wiley-Blackwell; 2010; "Managing Construction Projects; Second edition "</ref>. The current value stream of the process can be visualized and in this way sources that produces non-conformance are discovered and eliminated. This method helps individuals to understand the process instead of focusing on the result of the process alone. This can increase the overall efficiency the process. Value-stream mapping makes it possible to identify effective testing equipment, testing strategies and quality control loops <ref name="QVSM">Haefnera, Benjamin; Kraemera, Alexandra; Staussa, Torsten; Lanzaa, Gisela, Variety Management in Manufacturing. Proceedings of the 47th CIRP Conference on Manufacturing Systems, 2014, "Quality Value Stream Mapping "</ref>. Figure 8 is an illustration of the overall structure of a VSM. It is shown that the VSM takes form as a flow chart, which identifies the flow of materials and information. | |
− | + | ||
− | + | ||
− | + | ||
− | + | ||
− | + | ||
− | + | ||
− | + | ||
− | + | ||
− | + | ||
− | + | ||
− | + | ||
− | + | ||
− | + | ||
− | + | ||
− | + | ||
− | + | ||
− | + | ||
− | Value stream mapping (VSM) is a preventive QC technique, that focus on understanding the details of all the discrete elements in a process <ref name="winch">Winch, Graham M. | + | |
Line 168: | Line 148: | ||
1. Map the process at current state. | 1. Map the process at current state. | ||
− | 2. Rate the value of each step of the process | + | 2. Rate the value of each step of the process and identify opportunities of improvement. |
3. Remap the process for the ideal future state. | 3. Remap the process for the ideal future state. | ||
− | + | In the first step it is important to gather all the persons involved in the process, in order to get a correct picture of the current state and prevent assumptions about the process. Sometimes it can be an advantage to observe and collect actual data of the process. When identifying the ways of improvement, it is very important to have the outcome in mind to improve the quality <ref name="QVSM">Haefnera, Benjamin; Kraemera, Alexandra; Staussa, Torsten; Lanzaa, Gisela, Variety Management in Manufacturing. Proceedings of the 47th CIRP Conference on Manufacturing Systems, 2014, "Quality Value Stream Mapping "</ref>. VSM is only relevant for processes that are repeated, which are fairly limited in construction projects compared to other industries. However the number of repeated processes are increasing due to standardization and pre-assembly are more common <ref name="winch">Winch, Graham M.; Wiley-Blackwell; 2010; "Managing Construction Projects; Second edition "</ref>. | |
= Limitations = | = Limitations = | ||
− | + | As stated in the beginning of the article the aim of performing QC is to ensure that the requirements are fulfilled. If the requirements made by the client are unclear, then it is difficult to perform good quality control. The requirements have to be clear to every partner (designers, entrepreneurs and craftsmen) involved in the project to avoid misunderstandings and carelessness. | |
+ | |||
+ | |||
+ | QC has to be adjusted to each project, since most construction projects are unique due to the post-modern construction culture. Experience gained in previous projects might therefore not be useful. Many uncertainties can have an impact on the planning of the QC, since it can be difficult to define the need requirements. One important parameter is experience anothor just as important parameter is knowledge. First of all it is important that people understand the process before controlling it, thus preventive actions can be made <ref name="TQMOakland">Oakland, John S., Quality and Reliability Engineering International, volume 9, issue 6, 1993, "Total quality management"</ref>. Secondly knowledge can be used to prevent errors e.g. prevent craftsmen from trying to construct something, that cannot be build, even though it is designed by the engineers or architects. | ||
+ | |||
− | + | Another limiting aspect is available resources. Often the client choses the lowest tender price, which might not be the cheapest solution in the end. If there are not enough resources available to perform good QC, fatal errors are more prevalent at the end of the project. By investing in good QC solutions, where continuous or real-time control is performed instead of monthly inspections, the overall cost of the project can often be lowered. Time is also a crucial factor to consider, and if a reason amount of time is not included in the planning of the project, it is impossible to ensure the required quality. If enough time are devoted to make the minor corrections as the problems occur, then comprehensive rework in the end can be prevented <ref name="BigReport">Jørgensen, Kirsten; Schultz, Casper S.; Bonke, Sten, Technical University of Denmark, 2013, "Processer og metoder i det fejlfrie byggeri: Erfaringer og anbefalinger fra projektledere i entreprenørbranchen"</ref>. | |
− | + | = Annotated bibliography = | |
+ | The following literature related to the topic can be recommended: | ||
− | + | '''Books:''' | |
− | + | Oakland, John S., Rutledge Taylor and Francis Group, 2008, "Statistical Process Control", Sixth edition, ISBN-13: 978-0-7506-6962-7. | |
+ | ::: As the title indicates this book concerns "Statistical Process Control" which is a QC technique. The purpose of the technique is to improve processes. The book covers subjects as six-sigma process quality and how to manage processes, that are out of control. Furthermore it looks into how the technique can be implemented. | ||
− | |||
− | + | '''Articles:''' | |
− | + | Haefnera, Benjamin; Kraemera, Alexandra; Staussa, Torsten; Lanzaa, Gisela; Variety Management in Manufacturing. Proceedings of the 47th CIRP Conference on Manufacturing Systems, 2014, "Quality Value Stream Mapping " | |
+ | ::: This article gives a brief introduction to the classical "Value Stream Mapping" method and furthermore it introduces a new method called "Quality Value Stream Mapping". The purpose of the method is to make a systematical visualization, analysis and optimization of multistage processes. An example of how to implement the method is given. | ||
− | |||
− | |||
− | + | Akincia, Burcu; Boukampa, Frank; Gordona, Chris; Huberb, Daniel; Lyonsb, Catherine; Parkc, Kuhn; Elsevier, Automation in Construction 15, 2006, "A formalism for utilization of sensor systems and integrated project models for active construction quality control" | |
+ | ::: The focus of the article is active QC on the construction site. A new approach is purposed in the article, where advanced sensor systems and integrated project models are the tools to perform the active control. It describes the necessary steps in an active control approach and have a good literature review of reason present approaches, that include sensor systems. | ||
− | |||
− | + | '''Research:''' | |
− | + | Jørgensen, Kirsten; Schultz, Casper S.; Bonke, Sten; Technical University of Denmark, 2013, "Processer og metoder i det fejlfrie byggeri: Erfaringer og anbefalinger fra projektledere i entreprenørbranchen" | |
+ | ::: This report contains a qualitative study based upon interviews with experienced project managers. The aim of the study was to find out how to make construction projects that end up with no defects. With other words the report outlines what "best practise" is from the managers point of view. | ||
=References = | =References = | ||
<references/> | <references/> |
Latest revision as of 13:46, 19 November 2018
Developed by Silja Tea Nielsen
Defects and errors in construction projects have been subject to attention in the media and debates throughout the years. A general consensus of a lack of quality on the construction sites exists, thus an increasing effort have been made to improve the quality of construction projects by a number of political initiatives[1]. When managing quality in a project an important aspect is Quality Control (QC), which is the focus of this article. First the definition of QC is elaborated and examples of process QC and product QC is given, in order to clarify the difference between the two types of QC. The standard DS/ISO 21500 outlines different aspects that have to be considered when performing QC, why these are mentioned in the article. Different QC policies and techniques exist and their objectives, advantage and disadvantages are elucidated. At last limiting conditions when performing QC are stated.
Contents |
[edit] Definition of Quality Control
The aim of QC in construction projects is to assure high quality of the construction being built and the individual processes within the project. In this content “high quality” denotes fulfilling standards and the established quality requirements of the specific project [2]. It is important to investigate the causes of the arising problems, as well as finding ways to eliminate unsatisfactory performance when performing QC, thus corrective, preventive and predictive QC policies are essential. QC is a part of managing conformance in construction projects, and QC can continuously be improved by Total Quality Management.
[edit] Product Quality Control vs. Process Quality Control

QC deals with the specific products as well as the processes as mentioned above. A certain understanding of the process or product is needed in order to perform QC. A process is the transformation from a set of inputs to the desired output. The inputs can e.g. be materials, procedures and knowledge as illustrated on Figure 1. Each process in a construction project can be analyzed by itself and afterward actions can be determined in order to improve the process, thus the process QC become preventive [4].
Examples of process QC can for example by:
- Measuring the temperature of the concrete during casting and check if it fulfills specifications.
- Controlling the QC process by checking if the QC methods agreed upon are carried out [5].
QC of a product concerns the quality of the output/result of the process instead. It can be a product of a process in the design phase as well as in the construction phase. The output does not have to be a physical product but can just as well be a service, information or conducted paperwork as illustrated by Figure 1. Examples of defects that product QC deals with are:
- Missing information in drawing material
- Moisture damage of a construction element
[edit] Performing Quality Control
Primary inputs | Primary outputs |
---|---|
Progress data Deliverables Quality plan |
Quality control measurements Verified deliverables Inspection reports Change requests Corretive actions |
Tools and inspection procedures are needed, in order to perform QC. These inspection procedures and QC tools are specified in the part of the conformance management called Quality Assurance [2]. The primary inputs and outputs when performing QC in construction projects given by the standard DS/ISO 21500 [6] are shown in Table 1. Here it is shown that QC is highly dependent of good planning, as the primary inputs are a result of planning the quality in the project. The primary outputs indicate, that checking if requirements are being meet is not satisfactory alone, but QC includes documentation, communication and analysis as well. Furthermore it is shown that QC also has to prevent defects and non-conformance from taking place.
The standard DS/ISO 21500 [6] states that QC should be performed during the whole project life cycle and that it includes following aspects:
- Monitoring the quality of the processes and detect defects.
- Analyzing of the causes of defects and non-conforming performance.
- Eliminate unsatisfactory performance by identifying preventive actions and change requests.
- Communicating the changed requests and necessary corrective actions to project organization members.
Documentation is not mentioned directly by the standard, but it is implied in the last aspect "communication" as it is impossible to tell the craftsman, which corrective actions that have to be accomplished, without documentation. The documentation can be carried out with control tables, but in large construction projects digital quality documentation is preferred as many parts perform QC. By using digital documentation the position and date of the defect can be noted on the layout drawing, so the craftsmen get a clear outline of the defects [7].
[edit] Correct, prevent & predict
With the increased focus on minimizing non-conformance in construction projects the main goal of QC has shifted from a corrective to a predictive policy as illustrated on Figure 2. The intention of this shift is to predict the errors and defect, and thereby prevent them from happen. By achieving predictive and preventive QC the cost of the project will be decreased and time can be saved.
In the other industries the shift from corrective to preventive/predictive QC has already been seen, while different issues puts limits to the shift in the construction industry. Graham M. Winch mention four issues that slow down the development[2]:
- Construction projects are often unique, and this limits the value of experience and knowledge gained, as the project does not last long enough to achieve zero defects
- It is hard to implement statistical approaches to improve the processes, as the processes in the project only are repeated a limited number of times
- There are no rewards for the designer to make error free drawings, as this mostly benefits the contractor. So why should the designer invest time and money in QC of their drawings?
- The partners involved in construction project do not have a common goal, why is it hard to manage conformance for everyone.
In following the three QC policies (corrective, preventive and predictive) will be clarified.
[edit] Corrective Quality Control
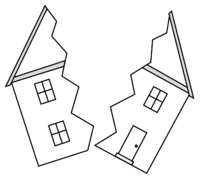
Corrective QC is necessary when non-conformance or a fatal event has occurred, thus corrective QC is defined as a reactive approach. This approach of QC is necessary because unexpected events and defect always will occur in construction projects. The ideal project where all problems are prevented is hard to establish, since many people, partners and processes are involved in the project. Questions like “have we met the requirements?” and “what went wrong?” are frequently asked, when using corrective QC.
This type of quality control can be expensive, due to the fact that rework can be very comprehensive[1]. Correcting serious errors can also be time consuming depending on how many parts that have to be involved in the rework, likewise new material deliveries can result in delays.
In order to correct errors, knowledge of the causes to the problem has to be obtained. Performing corrective QC can be accomplished with different techniques, and one technique is “cause and effects diagrams”, which is elaborated in following.
[edit] Preventive Quality Control
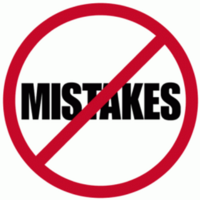
By changing the strategy of QC from corrective to preventive the questions are changed to "can we do the job correctly" and "are we doing the job correctly" [3]. A certain amount of knowledge and experience is required in order to answer the questions, and thereby prevent failures and non-conformance from happening. It is a common problem that the people trying to control procedures do not have the necessary competencies to do so. For this reason W. Edwards Deming, a guru of quality management, came with the advice [4]:
One way to increase preventive QC in construction projects is to make specifications, recommendations and regulations of work procedures, thus the people involved in the project can get a clear overview of which aspects of the procedure to focus on in order to prevent non-conformance.
[edit] Continuous, delivery and start-up control
A qualitative analysis of processes and methods in flawless construction projects, which is based on experience from project managers, showed that continuous QC, delivery QC and start-up QC are very import in order to prevent fatal errors [7]:
A way to prevent expensive corrective actions is to perform continuous QC. This can for example include thermo graphic measurements of the first room finished, and if non-conforming performance is found, then preventive actions can be made to assure the quality of the remaining rooms.
QC at delivery of materials e.g. reinforcement and concrete elements are essential, as these elements often are hidden, thus later control is impossible. Poor quality of these elements could be fatal as it can result in construction failure.
Start-up QC at the shift between contractors can prevent errors from occurring. This way the quality of the previous work is assured and the following work is not going to hide defects. The hidden defects can potentially result in critical errors, which will be very expensive and time consuming to correct. This concept is also called "stop the line" in lean construction, where the following work are set on hold until all errors from previous work are corrected [10].
[edit] Predictive Quality Control
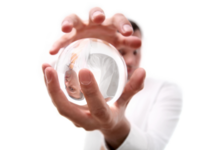
Predictions of possible failures is necessary, in order to determine preventive actions. Graham M. Winch states[2]:
This means predictions should be based upon analysis of data and well-founded arguments thus unnecessary actions are not initiated. Using the predictive QC policy it is important that the problem leave digital footprints before it occurs, otherwise predictions can not be made[12]. Valuable predictions can be made by modern technology, that makes it possible to collect and analyze large amounts of data from different systems. Monitoring processes makes it possible to perform real-time control and predict failures before they occur [13]. Various advanced sensor systems is developed and can be integrated as a part of the inspection procedures on the construction site. These systems create the opportunity of frequently gathering "as-built" data. The collected data have to be carefully analyzed and compared frequently with specifications and "as-designed" models. If divisions are found it has to be evaluated, if it will induce defects later on.
[edit] Monitoring
By applying a sensor system of laser scanners it becomes possible to produce a three-dimensional model of the complete construction or construction parts, as it is built. The three-dimensional model makes it easier to control if the work performed corresponds to the model made in the design phase. Using laser scanners to produce "as-bulit" models can be quite comprehensive, as the scanners deliver point clouds that have to be transformed into objects. This increases the efficiency of the sensor system in order to obtain a real-time model [14].
Temperature sensors make it possible to provide real-time data of the temperature development in processes. It can for example be used to predict the maturity and thereby the strength of concrete during hardening. This way framework will not be removed too early, and thereby defects or even critical failures can be prevented. By mounting strain-gages on structural elements the strains in the element during a process can be measured. If a large element e.g. a bridgedeck is going to be transported to another location, it can be relevant to ensure that no damages occurred during the move. By using this sensor system mounting of a damaged bridge deck can be prevented, which can be very expensive and time consuming to repair.
When monitoring processes it is crucial to predict what kind of damage that might occur, in order to choose the right sensor system, as you only receive the data that you "asked for". Another important aspect during monitoring is to prevent technical failures such as cut wires and filled data loggers [14].
[edit] Quality control techniques
Various techniques and tools to perform QC are developed through time. Frequently used tools are Ishikawa's seven tools [15]: Cause-and-effect diagram, Check sheet, Control chart, Histogram, Pareto chart, Scatter diagram, Flow charts. In the following two of the tools (Cause-and-effect diagrams and Flow charts) will be described in relation to QC in construction projects.
[edit] Cause-and-effect diagrams
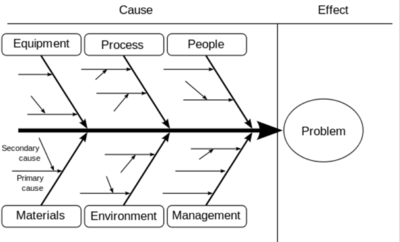
Cause-and-effect diagrams also go under the names “fishbone diagram” (due to the shape) and “Ishikawa diagram” (after the inventor of the technique). The diagram separates the problem (the effect of the causes) from the causes. The basic idea of the technique is to work back from the problem by asking: “why did it occur”, thus finding the different roots to the problem [2]. Each cause is thereby found by using a form of brainstorm technique, and they are grouped under different categories. A cause can either be a primary cause or a secondary cause. The structure of the diagram is shown on Figure 6.
A cause-and-effect diagram shows that there often are several roots to problem, and that several corrective/preventive actions have to be performed. This allegation becomes clear by grouping the causes under different categories, because it illustrates the difficulties of complex processes. The categories often include people, process/methods, equipment/machines, material, environment and management, as these are some of the essential elements in construction projects [16].
[edit] Value stream mapping (Flow charts)
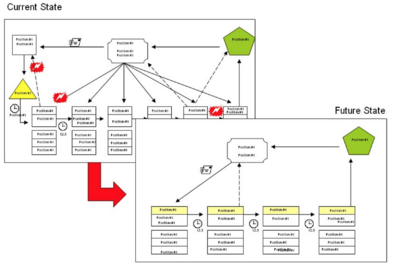
Value stream mapping (VSM) is a preventive QC technique, that focus on understanding the details of all the discrete elements in a process [2]. The current value stream of the process can be visualized and in this way sources that produces non-conformance are discovered and eliminated. This method helps individuals to understand the process instead of focusing on the result of the process alone. This can increase the overall efficiency the process. Value-stream mapping makes it possible to identify effective testing equipment, testing strategies and quality control loops [18]. Figure 8 is an illustration of the overall structure of a VSM. It is shown that the VSM takes form as a flow chart, which identifies the flow of materials and information.
The technique requires following steps to be carried out:
1. Map the process at current state.
2. Rate the value of each step of the process and identify opportunities of improvement.
3. Remap the process for the ideal future state.
In the first step it is important to gather all the persons involved in the process, in order to get a correct picture of the current state and prevent assumptions about the process. Sometimes it can be an advantage to observe and collect actual data of the process. When identifying the ways of improvement, it is very important to have the outcome in mind to improve the quality [18]. VSM is only relevant for processes that are repeated, which are fairly limited in construction projects compared to other industries. However the number of repeated processes are increasing due to standardization and pre-assembly are more common [2].
[edit] Limitations
As stated in the beginning of the article the aim of performing QC is to ensure that the requirements are fulfilled. If the requirements made by the client are unclear, then it is difficult to perform good quality control. The requirements have to be clear to every partner (designers, entrepreneurs and craftsmen) involved in the project to avoid misunderstandings and carelessness.
QC has to be adjusted to each project, since most construction projects are unique due to the post-modern construction culture. Experience gained in previous projects might therefore not be useful. Many uncertainties can have an impact on the planning of the QC, since it can be difficult to define the need requirements. One important parameter is experience anothor just as important parameter is knowledge. First of all it is important that people understand the process before controlling it, thus preventive actions can be made [3]. Secondly knowledge can be used to prevent errors e.g. prevent craftsmen from trying to construct something, that cannot be build, even though it is designed by the engineers or architects.
Another limiting aspect is available resources. Often the client choses the lowest tender price, which might not be the cheapest solution in the end. If there are not enough resources available to perform good QC, fatal errors are more prevalent at the end of the project. By investing in good QC solutions, where continuous or real-time control is performed instead of monthly inspections, the overall cost of the project can often be lowered. Time is also a crucial factor to consider, and if a reason amount of time is not included in the planning of the project, it is impossible to ensure the required quality. If enough time are devoted to make the minor corrections as the problems occur, then comprehensive rework in the end can be prevented [7].
[edit] Annotated bibliography
The following literature related to the topic can be recommended:
Books:
Oakland, John S., Rutledge Taylor and Francis Group, 2008, "Statistical Process Control", Sixth edition, ISBN-13: 978-0-7506-6962-7.
- As the title indicates this book concerns "Statistical Process Control" which is a QC technique. The purpose of the technique is to improve processes. The book covers subjects as six-sigma process quality and how to manage processes, that are out of control. Furthermore it looks into how the technique can be implemented.
Articles:
Haefnera, Benjamin; Kraemera, Alexandra; Staussa, Torsten; Lanzaa, Gisela; Variety Management in Manufacturing. Proceedings of the 47th CIRP Conference on Manufacturing Systems, 2014, "Quality Value Stream Mapping "
- This article gives a brief introduction to the classical "Value Stream Mapping" method and furthermore it introduces a new method called "Quality Value Stream Mapping". The purpose of the method is to make a systematical visualization, analysis and optimization of multistage processes. An example of how to implement the method is given.
Akincia, Burcu; Boukampa, Frank; Gordona, Chris; Huberb, Daniel; Lyonsb, Catherine; Parkc, Kuhn; Elsevier, Automation in Construction 15, 2006, "A formalism for utilization of sensor systems and integrated project models for active construction quality control"
- The focus of the article is active QC on the construction site. A new approach is purposed in the article, where advanced sensor systems and integrated project models are the tools to perform the active control. It describes the necessary steps in an active control approach and have a good literature review of reason present approaches, that include sensor systems.
Research:
Jørgensen, Kirsten; Schultz, Casper S.; Bonke, Sten; Technical University of Denmark, 2013, "Processer og metoder i det fejlfrie byggeri: Erfaringer og anbefalinger fra projektledere i entreprenørbranchen"
- This report contains a qualitative study based upon interviews with experienced project managers. The aim of the study was to find out how to make construction projects that end up with no defects. With other words the report outlines what "best practise" is from the managers point of view.
[edit] References
- ↑ 1.0 1.1 Schultz, Casper S.; Jørgensen, Kirsten; Bonke, Sten and Rasmussen, Grane M. G.; Architectural Engineering and Design Management; Taylor and Francis Group; 2015, "Building defects in Danish construction: project characteristics influencing the occurrence of defects at handover"
- ↑ 2.0 2.1 2.2 2.3 2.4 2.5 2.6 Winch, Graham M.; Wiley-Blackwell; 2010; "Managing Construction Projects; Second edition "
- ↑ 3.0 3.1 3.2 Oakland, John S., Quality and Reliability Engineering International, volume 9, issue 6, 1993, "Total quality management"
- ↑ 4.0 4.1 Oakland, John S., Rutledge Taylor and Francis Group, 2008, "Statistical Process Control", Sixth edition
- ↑ IRMI, "Construction Quality Management", access: 12-06-2017,https://www.irmi.com/articles/expert-commentary/construction-quality-management
- ↑ 6.0 6.1 6.2 Danish Standards Foundation, 2013, "DS/EN 21500: Guidance on project management", Second edition
- ↑ 7.0 7.1 7.2 Jørgensen, Kirsten; Schultz, Casper S.; Bonke, Sten, Technical University of Denmark, 2013, "Processer og metoder i det fejlfrie byggeri: Erfaringer og anbefalinger fra projektledere i entreprenørbranchen"
- ↑ The church of Jesus Christ of latter-day saints, "Helaman 1–6", access: 12-06-2017,https://www.lds.org/manual/book-of-mormon-teacher-resource-manual/helaman-1-6?lang=eng
- ↑ T&W Church solutions, "The Top 7 Mistakes Made by Church Building Committees and How to Prevent Them!!!", access: 12-06-2017, http://www.tw-church.com/The-Top-7-Mistakes-Made-by-Chur.html
- ↑ Simonsen, Rolf, Værdiskabende Byggeproces, 2017, "Lean Construction & Last Planner System"
- ↑ Skipprichard Leadership insights, "The Surprising Predictive Power of Analytics", access: 12-06-2017, https://www.skipprichard.com/the-surprising-predictive-power-of-analytics/
- ↑ Cyient, 2016, "Engineering solutions for predictive maintenance in rail"
- ↑ Navon, Ronie; Elsevier, Automation in Construction 14, 2005, "Automated project performance control of construction projects"
- ↑ 14.0 14.1 Akincia, Burcu; Boukampa, Frank; Gordona, Chris; Huberb, Daniel; Lyonsb, Catherine; Parkc, Kuhn; Elsevier, Automation in Construction 15, 2006, "A formalism for utilization of sensor systems and integrated project models for active construction quality control"
- ↑ Ishikawa, Kauro, Tokyo 3A Corporation, 1990, "Introduction to Quality Control "
- ↑ 16.0 16.1 Wikipedia, "Ishikawa diagram ", access: 11-06-2017, https://en.wikipedia.org/wiki/Ishikawa_diagram
- ↑ Lean homebuilding, "Value stream mapping ", access: 13-06-2017, https://leanhomebuilding.wordpress.com/2010/04/14/value-stream-maps-visualizing-waste/
- ↑ 18.0 18.1 Haefnera, Benjamin; Kraemera, Alexandra; Staussa, Torsten; Lanzaa, Gisela, Variety Management in Manufacturing. Proceedings of the 47th CIRP Conference on Manufacturing Systems, 2014, "Quality Value Stream Mapping "