Critical-Chain Approach
(→Traditional Scheduling vs. CCPM Scheduling - Example) |
(→Traditional Scheduling vs. CCPM Scheduling - Example) |
||
Line 143: | Line 143: | ||
<div><ul> | <div><ul> | ||
− | <li style="display: inline-block;"> [[Image:8A.jpg| | + | <li style="display: inline-block;"> [[Image:8A.jpg|600px|thumb|right|Figure 8A: "Project Schedule without resources"]] </li> |
− | <li style="display: inline-block;"> [[Image:8B.jpg| | + | <li style="display: inline-block;"> [[Image:8B.jpg|600px|thumb|right|Figure 8B: "Gantt chart without resources"]] </li> |
</ul></div> | </ul></div> | ||
Revision as of 13:59, 16 September 2016
Critical Chain Project Management (CCPM) is a methodology for planning, executing and managing projects. The focus is on the project schedule and to reduce project changes and cost overruns by taking into account resource allocations and time uncertainties of activities.
The method was developed by an Israeli physicist, Eliyahu M. Goldratt, who introduced it in his Theory of Constraint (TOC) book “Critical Chain” in1997, which later became the foundation of CCPM. It was developed to reengineer the project planning and management practices in order to eliminate common issues and problems that can lead to poor project results, such as increased cost, fewer deliverables than expected and frequently missed deadlines due to longer than expected durations of activities.
CCPM differs from other traditional project planning methods that have its origin in critical path and PERT algorithms in several ways. The emphasis is on resources available, flexible starting times, interim milestones in projects and the use of resource-, feeding- and project- buffers but not order of tasks and strict schedules. The CCPM attempts to level out the resources available where a switch between project tasks are often needed to make sure the project is on schedule.
The focus of this article is to introduce and explain the background and concept of the CCPM approach when planning and scheduling a project together with benefits and limitations of the method. Undesired effects of more traditional planning and scheduling methods will be discussed, followed by how to prevent these effects by using the CCPM approach.
Contents |
The Author and the history
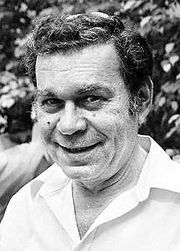
Author
Eliyahu M. Goldratt (1947 – 29111) was born in Israel and over his life he worked as a lecturer, researcher, scientists, and a business leader. Goldratt completed a Master of Science and a Doctors degree in Philosophy both obtained at Bar-Ilan University in Israel [1].
He is known for developing the groundbreaking Theory of Constraints (TOC), which he introduced in his book “Critical Chain” in 1997. The book reveals the reasons for why projects are unable to finish on time or within budget. In response to that, the TOC method was introduced [2] . This method reengineers the project planning and management practices in order to eliminate issues and problems that lead to poor project results. In addition he is the innovator behind several TOC tools such as “the thinking process”, “drum-buffer-rope” and the “Critical Chain Project Management” (CCPM) [1].
History
The importance of projects in today’s global and chaotic environment is becoming significant and will continue to grow in the future. All businesses have projects and they are turning to project management as a way to improve project results in order to stay ahead of the competition. Despite of precise planning and strict schedules through PERT/CPM approaches, lack of efficiency in project management has been a big issue in the last decades. The Theory of Constraints approach (TOC) to project management strives to eliminate this lack of efficiency by using the Critical Chain method when planning, scheduling and monitoring projects [3].
It all started with Eliyahu Goldratt’s first book, “The Goal”, a non-traditional approach to share knowledge. The book is a business textbook written in a novel form, disguised as a love story and tells a story of a manager in problems due to his poorly run manufacturing plant [1]. According to Goldratt, interdependency of elements influences the ability of businesses to do what should be done and that manufacturing plants can be controlled by three main measures; throughput (TH), operating expenses and inventory. Based on this, he described the Drum-Buffer-Robe (DRB) approach, which is to produce only what is needed. In his second book “It’s not Luck” he extended this method for marketing and distribution and the extended method became known as The Theory of Constraint (TOC). In his third book “The Critical Chain” he applied the TOC method to Project Management and this method is now know as Critical Chain Project Management (CCPM) [3]. The critical chain refers to the longest string of dependencies that are present in a project. The term chain is used instead of path, because the critical path is only linked to technical dependencies and not resource dependencies [4].
Theory of Constraints
Theory of Constraint (TOC) is a change method that focuses on identifying constraints or bottlenecks in processes and systems, to enable appropriate action to be taken to improve performance to gain more profit [5]. Goldratt applied this theory to marketing and distribution in his second book “It’s not Luck” published in 1994 [2]. According to him organizational performance is dependent on bottlenecks, which prevent the organization to maximize its performance and reach the objective, which is normally to increase profit [6].
These bottlenecks can include information, equipment, work force, and supplies and can be both internal and external to an organization. The fundamental concept of the theory is that, every business has at least one constraint, that is, any factor that limits the output of the organization and prevents it to improve the performance. In other word the weakest link in the chain. The theory also states that the processes or systems can only have one weakest link at a time, and that other weaknesses are not constraining until they become the weakest link. The theory can be used in various situations and is based on five steps to improve productivity [6].
The five steps of theory of constraint
The aim is to keep the constraint or the bottleneck as efficient as possible, because, only the efficiency of the bottleneck is a critical factor to the overall performance. There are five important steps to improve performance of a chain. Each step will be explained with an example in production planning terms [7].
- Identify constraints of the process or the system: It is important to identify the bottleneck. If the bottleneck is a machine, the maximum utilization must be achieved, ensuring there is always work to do for this particular machine [7].
- Determine how to exploit these constraints: Find ways to ensure the maximum utilization of the bottleneck. This could mean reducing the number of changeovers, offload work that can be done on another machine or reduce setup times to create additional capacity [5].
- Subordinate system’s constraints: It is meaningless to run other machines with a higher production rate than the bottleneck. Therefore every other decision must be subordinated to keep the bottleneck running [5].
- Elevate constraints to a new level of productivity: Concentrate all resources and efforts on the bottleneck to increase throughput rate or output. One way to do this is to run the bottleneck machine for extra hours every day, this increases the capacity of the machine [7]. The different between step 2 and 4 relates to the amount of investment required [5].
- Start again on step on: With increased capacity of the machine, there might be a new bottleneck, which needs to be addressed and the process of improvement must be repeated. Make sure inertia does not cause a system constraint [7].
Traditional approaches
Critical Path Method (CPM) is a traditional scheduling and planning method used in project management. The method is based on estimates of time required to complete project activities that lie on the critical path. The critical path is the sequence of interdependent activities in a project that add up to the longest overall duration [4].
Program Evaluation and Review Technique (PERT) is another traditional scheduling and planning methods and is identical to the CPM method. The difference between PERT and CPM, is that PERT assumes that each project activity duration has a range that follows a statistical distribution. PERT uses three estimated durations for activities to calculate the overall project duration [4].
Problems with PERT/CPM approaches
Several problems are related to the use of PERT and CPM, the traditional approaches, when scheduling and planning projects. These factors have one thing in common; they can all cause delays in the project completions.
Variability of task duration and convergence points
Most projects have a multiple tasks that converge to another tasks in the critical path, see figure 3 where activities A and B converges to activity C. This means that both A and B must be completed before activity C can be started. Due to variability of task durations, the start date of activity C (the dependent task) may be incorrect. The impact of this problem can be escalated, because all projects have paths that merge into one end node. Both PERT and CPM approaches fail to take into account the variability of task durations [3].
Scheduling to a specific time
Traditional approaches make use of start date and task durations when planning and scheduling resources. This means that if activity A is completed early, activity B will still start on the earliest start date, in this example day 4,see figure 3. However, if activity A is completed late, activity B will start late, since the activities are sequential. Both PERT and CPM do not link the start of activity B to the real finishing time of activity A [3]. In addition, scheduling to a specific date can increase the probability of two unfortunate syndromes occurring, both of them leading to a failure of completing activities early.
Sandbagging: In project management, sandbagging refers to the practice of holding a complete work until the true due date arrives. This can produce poor picture of where the project and the organisation really stands [3].
Parkinson’s Law: This occurs when an activity is completed before deadline but resources are still improving the work until the due date is reached. A good example is when a worker is given a task that takes only a few hours to complete, but was allocated a few days of work in the schedule. The time spent on the activity is often expanded and finished at the last minute. This can also be adapted to budgets and other constraints [3].
Self-protection: The concept when workers fail to report early completion of activities out of fear that management team will adjust future standards and demand more next time. This means that if a worker estimates that an activity will take 5 days to complete but delivers the work in 3 days. Next time the manager might want to trim the estimate based on past performance [4].
Increasing the estimated duration time of tasks
This is an extension to problem 2. A path has 40% certainty to be completed at the earliest finish date, in day 12. However, this is not reliable enough, so the resource manager increases the time estimate by 25%. This means that activity B can now start on day 5, the earliest, and is scheduled to finish in day 15, instead of day 12. This means, that the path is more reliable, but an extra day is needed to complete the project [3].
Consuming slack early in the process
Considering a non-critical path with a total slack of 5 days and the management practice of delaying the activities of the non-critical path to save money. This means that activity A will start during day 5 and the whole slack is spent in the beginning of the sequence A-C-F. The slack is therefore no longer protecting the sequence if anything unexpected happens [3].
Student syndrome: The student syndrome is a common student behaviour to postpone the homework to the last possible start time, while at first working with a high level of slack. In project management, this syndrome can jeopardize the due date. This can be caused by, poor project management, unclear requirements, human nature etc. [8].
Resource issues
Neither PERT or CPM approaches do not take into account that resources might be needed at the same time. E.g. assume that activities C1 and C2 need the same resource C. If C1 starts first, C2, which is part of the critical path, will be late and therefore the whole project will be delayed. If C2 starts, activity C1 will be late and the non-critical path will become critical. Either way the project will not be finished on time [3]. Another big resource issue is the phenomenon of multitasking.
Multitasking and safety times: The performance of multiple project activities done at the same time is called multitasking, dividing time between multiple project tasks and shifting from one activity to another if there is no prioritization of activities. Multitasking is often thought of as a good way to improve efficiency of resources. However, the focus on local efficiency can damage the over all performance. This issue can easily be explained by comparing two project paths, see figure 4. Path 1 prioritizes the work of activity A and the activity will be completed in 10 days. Multitasking is used in path 2, where activity A is completed in 20 days but the total duration of both paths are 30 days. Another issue caused by multitasking is the increase in lead-time caused by increase in setup changeovers. This can often result in project managers adding extra time for each activity to be on the safe side in terms of project delivery time [8].
Dropped baton: This refers to the impact of poor coordination. If an activity is completed early and the resources for the new dependent activity is not ready, the time gained by completing the activity early, is lost. Inflexible resource schedules can cause this problem [4].
CCPM as a solution to these problems
CCPM was developed to reengineer the project planning and management practices, in order to eliminate the problems mentioned above, which existing methods, expensive software and tools had not been able to solve. These problems lead to poor project results such as increased cost, fewer deliverables than expected and frequently missed deadlines due to unrealistic estimates of activity durations. The biggest potential for improvements are connected to the common cause variation which the CCPM takes advantage of.
Dr. W. Edwards Deming, an American engineer and a management consultant, developed the theory of Common Cause Variation and defined two types of variations:
- Common Cause Variation: is caused by unknown factors resulting in steady but random distribution of outputs around the average of the data. This type of variation is inherent in the system and is a measure of how well the process can perform when the special cause variation is removed.
- Special Cause Variation: is a shift in outputs caused by specific factors such as environmental conditions or a specific machine. This type of variation can be accounted for and possibly removed.
All project activities have common cause variations in the time of activities, which represent uncertainty in performance. Traditional planning and scheduling methods estimate the impact of common cause variations and settle the problem by adding safety time for each activity [8]. CCPM deals with common cause variation by insisting on using estimates of 50% chance of completion before time, instead of 80-90% chance like traditional methods. In addition to shorten time estimates of activities the method uses strategically located buffers, which aggregates the safety time and protects the chain. There are three types of buffers used in CCPM:
- Project buffer: Due to common cause variations in time, the project duration is unclear. To tackle this, project buffer is added to the expected project duration.
- Feeder buffers: Buffers are added to the schedule where non-critical paths merge with the critical chain.
- Resource buffers: Additional time buffers are inserted where scarce resources are needed for a project activity.
Insisting on using 50/50 estimates will discourage Parkinson’s law, student syndrome and self-protection because there is less slack in the chain. Productivity will increase due to less slack and the method also provides resource buffers to protect activities from unavailable resources. This means the likelihood of dropped baton effect will be reduced [4].
As long as resources start the activity as soon as necessary inputs are received, work on an activity without multitasking, and passes on the activity output to the next activity as soon as it is completed, CCPM does not criticize performances that overrun the estimated activity durations.
CCPM allows the project team to focus on completing the project as soon as possible by only providing start dates for the whole activity chain and the end date of the project buffer. During the project, the plan only provides approximate start times and estimated activity durations for each project activity [8].
Critical Chain Project Management
Planning
The first step in CCPM is to create a project schedule. In order to do so, it is necessary to define all project activities that needs to be performed along with estimated activity durations, interdependencies between tasks and availability of resources. Availability of resources is a crucial part when applying CCPM and since a part of the resources have limited availability, the resulting schedule is likely to be longer than a schedule obtained by applying traditional methods.
After resource levelling, it is possible to identify the critical chain, which yields the project completion date. Resources that are allocated to activities that are part of the critical chain are referred to as critical resources. At this stage, the approach is identical to the approach of Levelled Critical Path.
The next step in the planning phase is to shortening activity durations based on the 50/50 chance of completing before time estimate. This means removing the safety margin, added by the worker who provided the estimate, from all the critical activities. The difference between the two project schedules, with and without safety margins for each activity, is called a project buffer and should now be displayed as a separate project activity in the end of the updated schedule, see figure 5. Notice that, it is assumed that only half the critical activities will exceed the estimated time duration and the other half will be completed early.
This step is now repeated for all non-critical activities and a safety margin removed. A safety buffer is now only placed where the non-critical path merges into the critical chain, this type of buffer is called feeding buffer, see figure 6. Notice that the non-critical path can still have slack.
The final step of the planning phase is to account for scarce resources. The third type of buffer used in CCPM is called resource buffer and located prior to critical activities that require critical resources. The buffer acts as a signal for the critical resources and notifies them that a critical activity is soon to be started [9]. This type of buffer protects the chain from resource bottlenecks, by causing critical resources to complete non-critical activities and to be ready to start working on the critical activity [4].
Execution
During the execution of the project plan it is expected that resources:
- Work on critical activities continuously without multitasking
- They complete the critical activity as soon as possible, regardless of schedule
- When the critical activity is complete, they start immediately on the activity’s successor
If an activity is not completed on time, based on the time estimate in the schedule, there is no reason for concern since the buffer in the chain will absorb the delays. During the project, the CCPM schedule will be recalculated and buffer sizes adjusted in order to keep the final due date [9].
Control
The approach of CCPM uses the three types of buffers to monitor and control the project time performance. The monitoring process is based on buffer consumptions and is divided into three zones, OK (green zone), Watch and Plan (yellow zone) and Act (red zone), see figure 7. As the buffer consumption begins to decrease and move towards the second zone (Watch and Plan) signals are set off in order to seek corrective actions. However, this warning mechanism is not used to its full potential unless the buffer consumption is compared with the actual progress of the project. As an example, if the project is 75% complete and the buffer consumption is 50%, there is nothing to worry about. Conversely, if the project is only 25% complete and the buffer consumption is 50%, appropriate and immediate actions must be taken [4].
Traditional Scheduling vs. CCPM Scheduling - Example
This comparing example between traditional scheduling methods and CCPM is used to illustrate how CCPM approach affects planning and scheduling in Project Management. The problem will first be solved by using traditional methods and then solved by using the CCPM approach.
Figure 8A, shows the planned project network without taking into account the necessary resources, this means that project activities are assumed to be independent of each other and resources will be made available. In Figure 8B, the correspondent gantt chart is shown. Dark grey bars represent the estimated durations of critical activities, the light grey bars represents the estimated duration of non-critical activities, and the colourless bars represent slack. Notice that the duration of the project is 45 days and the critical path is: A-D-F-G-H.
After resources have been added to the schedule, see Figure 8C it is clear that there are resource conflicts between project activities, since Ryan is the resource for activities A, C and F. By adding Ryan in the gantt chart in Figure 8B, it is clear that activities C and F overlap by 5 days, which is an impossible solution. This means that activities C and F, which at first were assumed to be independent have now become depended on each other. This must be solved. The gantt chart in Figure 8D, reflects the updated network schedule, where the solution to the over allocation of Ryan has been solved. The new schedule shows changed slack for certain activities, and more importantly, the critical path has changed and is now, A-C-F-G-H. In addition, the new project end date is 50 days instead of 45.
Applying the CCPM approach to the same project will lead another result. Figure 9A, shows the CCPM network, and notice that the estimated durations for activities are now representing the 50/50 chance rule. Two other observations are that the activities in the critical chain are all technically linked and both feeding buffers and project buffer have been added to the network.
The corresponding gantt chart is shown in Figure 9B. When using the traditional method, the non-critical activities were scheduled to start immediately after activity A, which is the earliest start date for those activities. Now they are scheduled later in the project and a three-day feeding buffer has been added at the end of each of the non-critical activities in order to absorb any delays that might occur. Finally, the project is estimated to take 27 days with a project buffer of 10 days instead of 50 days as the traditional method estimated.
This example is also a good way of explaining the difference between buffers and slack in projects. Slack is spare time of non-critical activities in the schedule. Buffers, on the other hand, are time blocks reserved for any unpredictable act that might occur and if they are note needed subsequent project activities can proceed on schedule [4].
Benefits
The CCPM approach is a network scheduling technique that modifies the project schedule in order to take into account limited resources by mixing deterministic and probabilistic approaches. The method aims to shorten project durations with better activity prioritization and efficient resource management, where availability of resources is taken into account. The most important advantage of this method is the ability to deliver projects on time or even before due date. The approach has a strong record of increasing the performance and reduce the time durations, good examples are: • Harris Semiconductor built a new automated wafer fabrication facility in less than 13 months by using the approach of CCPM, while the standard industry for such a facility is 26-36 months • The Israeli aircraft industry used CCPM techniques in order to reduce the maintenance work on aircrafts from two months to two weeks [4].
CCPM exploits the advantages of planning and control processes, such as resolve bottlenecks to improve performance, inherited from TOC, reduce waste inherited from Lean methodologies and finally reduce variation, inherited from Sig Sigma [10].
As mentioned earlier, the CCPM method helps overcome, Parkinson’s Law, student syndrome and self-protection due to less slack in the chain. With less slack in the chain and use of resource buffers, productivity will increase which protects the chain from the undesired effects of dropped baton [4]. Furthermore, by avoiding multitasking, the WIP level in the system is reduced, which can speed up work completion [11].
CCPM does not schedule to specific dates, which reduced the work of re-planning during the execution stage. This allows the project manager to focus on managing variations in activity durations. Also, with less re-planning the project manager, project workers and other stakeholders have a better overview of the progress, and by taking a look at buffer consumption it is easy to see whether the project is on time or not [11]. The use of buffers and buffer monitoring techniques, such as fever chart for monitoring project time performance, clearly identifies risk associated with each task and its impact on the project completion. This helps management identify when they must take action and what actions to take [5].
Criticism and limitations
The method of CCPM concludes that all activity durations are overestimated and includes a safety factor. The method suggests that all project activity durations are overestimated and should all be reduced by the same percentage, usually 33%. However, there is no scientific evidence supporting this and recent studies have shown that the amount of overestimation is individual dependent and based on personalities, past experiences, nature of the activity etc. Furthermore, project managers that know their estimates will be reduced have the tendency to encourage activity owners to add larger safety margins than before. This means that, still after the time reduction they have their preferred safety margins.
Buffers play a crucial role in the method of CCPM. The project buffers should protect the critical chain against the sum of uncertainty of the activity durations of the critical chain, and the feeding buffers should reflect the appropriate safety for the chains feeding into the critical chain. The size of the buffers needs to be less than the sum of the safety margins. Again, there is no scientific basis for how to estimate the buffer sizes.
The third criticism is in regard to the resource utilization or multitasking. Studies in terms of effectiveness of matrix organizations have shown that there is a correlation between the number of projects to which R&D personnel were assigned and KPIs of the organization. To be more precise, it showed that it is optimal to assign personnel with two projects at a time. Therefore the benefits of eliminating multitasking are not clear at all and the need for more studies in regard to this is necessary.
Project management success is not necessarily the same as project success. Most customers links success to whether the project contributes to the goals of their organization, while the project manager thinks of success in terms of scheduling, budged and scope commitments. Like traditional project management approaches, CCPM tends to focus on project management success rather than project success from the customer’s point of view.
In addition to this, CCPM is introduced as a revolutionary concept to replace current project management practices. However, the approach is hard to adapted within a team because the approach is not sufficiently integrated with the accepted body of knowledge and practices [9]. The method also requires strong commitment from stakeholders, project managers and the project team. This can help explain why the CCPM approach is not so widely used in businesses.
References
- ↑ 1.0 1.1 1.2 Van Vliet, V.(2011) "Eliyahu Goldratt.", Retrieved on 11 September 2016 from http://www.toolshero.com/toolsheroes/eliyahu-goldratt/
- ↑ 2.0 2.1 TOC Goldratt.(2011) " Biography of Dr. Eliyahu M. Goldratt.", Retrieved on 11 September 2016 from https://www.toc-goldratt.com/tocweekly/biography-of-dr-eliyahu-m-goldratt/
- ↑ 3.0 3.1 3.2 3.3 3.4 3.5 3.6 3.7 3.8 Abreu, A., & Correia, F.(2011) "An overview of Critical Chain applied to Project Management.”, 4th International Conference on Manufacturing Engineering, Quality and Production Systems, Meqaps – Proceedings, 261-267
- ↑ 4.00 4.01 4.02 4.03 4.04 4.05 4.06 4.07 4.08 4.09 4.10 Gray, C. F., & Larson, E. W. (2011). “Project Management, The Managerial Process.” McGraw-Hill/Irwin, NY
- ↑ 5.0 5.1 5.2 5.3 5.4 Rand, G.K.(2000) "Critical chain: the theory of constraints applied to project management", International Journal of Project Management 18(3), 173-177
- ↑ 6.0 6.1 Mind Tools Editorial Team (2016) "The Theory of Constraints (TOC) - Strengthening Your "Weakest Link".", Retrieved on 11 September 2016 from https://www.mindtools.com/pages/article/toc.htm
- ↑ 7.0 7.1 7.2 7.3 McKellen. C.(2004) "Theory of Constraints", Metalworking Production. 148(6), 9-9
- ↑ 8.0 8.1 8.2 8.3 Leach, L.P.(2000) "Critical Chain Project Management Improves Project Performance", Project Management Journal 30(2), 39-51
- ↑ 9.0 9.1 9.2 Raz, T., Barnes, R., & Dvir, D. (2001). “A Critical Look at Critical Chain Project Management.” Article in IEEE Engineering Management Review (2004)
- ↑ The Project Management Hut (2008) "Advantages of The Critical Chain Project Management (CCPM)", Retrieved on 16 September 2016 from http://www.pmhut.com/advantages-of-the-critical-chain-project-management-ccpm
- ↑ 11.0 11.1 Pinnacle Strategies. (2016). “Critical Chain and Critical Path, Can they coexist?” Retrieved on 16 September 2016 from http://3escp33iuwsj485tugc1mb91.wpengine.netdna-cdn.com/wp-content/uploads/bsk-pdf-manager/2016/02/CPM-and-CCPM-a-Compare-and-Contrast-Pinnacle-Strategies.pdf