Value Stream Analysis and Mapping for Project Management
(→Application) |
(→Application) |
||
Line 206: | Line 206: | ||
** '''Dig deep (only) when you must:''' Only when analyzing critical problems and looking for solutions do further work collecting enough data. | ** '''Dig deep (only) when you must:''' Only when analyzing critical problems and looking for solutions do further work collecting enough data. | ||
*'''Evaluate how value is created.''' | *'''Evaluate how value is created.''' | ||
+ | ** In detailed maps, specifically on lower level maps, non-value-added tasks may appear. Non-value-added activities may be hifing inside of value-added tasks, so try to add more detail to your map. | ||
+ | Although this can lead to an unefficient way to find them, it is a good way to begin with. For deeper understanding about how to evaluate value refer to the | ||
==Discussion== | ==Discussion== |
Revision as of 21:09, 22 September 2016
Value Stream Analysis and Mapping (VSA/M) is a tool for business process improvement.[1] Value Stream Analysis (VSA) is a method that implements lean principles for the examination of business processes. The tool, focus on the development of tasks which add value to the final product, efficiently linked together to form a continuously flowing stream of value.[1]
Contents |
History
In order to understand its origins we must look back into the early 40s. By then, Toyota was trying to compete with the American automobile market by productivity means. Taiichi Ohno in 1956 traveled to the US in order to visit the automobile plants and see how could he improve its production system back in Japan. Despite what he saw on those production plants, what catches his attention is the self-service supermarkets in which he could choose exactly what he wanted and how much of it. That idea was efficient as well as timely saver for him and where to become later the fundamentals for pursuing manufacturing improvements. Along the next years Ohno will develop this production system on a systematic framework based on Lean and Just-In-Time principles. Toyota defined six elementary rules[2]:
- Never send defective products downstream to the next process
- Each process only orders what it currently needs from the upstream process
- Each process only produces the quantity ordered by the downstream process
- Maintain a level rate of production
- Use Kanban to fine-tune the rate of production
- Work to reach a stable rate of production
These first studies where focused mainly on manufacturing processes in spite of process design. But the principles can still be applied either to shop floor and non-shop floor activities. And as Womack and Jones describe it, the main principles of lean for product development are[3][4]:
- Value: providing the customer with the right product, for the right price, at the right time.
- Value Stream: the set of actions that bring a product from concept to realization, order to delivery, or raw material to finished good
- Flow: seamless movement through value-creating steps.
- Pull: acting only to satisfy customer needs, rather than forcing, or pushing, a product upon the marketplace.
- Perfection: continuously and relentlessly improving the value, value stream, flow, and pull in business operations.
Methodology
The value stream must be analyzed and mapped thoroughly to reduce waste along processes and enable flow. Also to move the processes towards a more rapid response for customer pull. On a product development context, this means rapid response towards customer needs when it comes either to new products or permutations of the existing ones.[1]
On a manufacturing environment
Fundamentally, the method consists on mapping the current state of the process and apply lean techniques. This enables an improved future state of the process. In order to do so, non-value-added tasks are identified. Then, the tasks considered to support the true value-added tasks such as, set-ups, reviews, etc..., are Type I waste. While completely unnecessary tasks such as waiting in the inventory are Type II waste.[4] A number of techniques are then applied once cathegorised these types of waste. Which in the lean manufacturing pcontext include manufacturing cells, Just-In-Time deliveries, aparts supermarkets, etc... Once established the future state map, it is implementet thorough a plan. Which leads to a an improved state that ideally is used to generate further future states. As seen, the process is being continuously improved.
On a Program Management environment
According to the product development team at MIT's Lean Aerospace Initiative[1], the value of the Product Development (PD) process is "a capability delivered at the right time, for the right price, as defined by the end user." Now this value stream is effectively emboided on a notional product designed package. Therefore, as the outcome of a value stream it can be evaluated as a PD value stream, like the manufacturing value stream is done. This way fitting with other activities around the business cycle to define an overall value as we can see on the Figure 1.
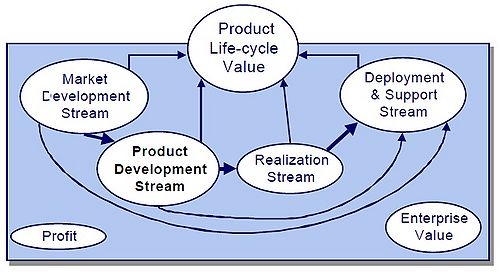
In order to extrapolate the VSM under manufacturing principles to a Program Management environment, how does the flow thorough the PD process translates into? In this case it is information. Information flows thorough the PD process like on the manufacturing environment material does.[1] The quality of the information flow is characterized by its Form, Fit, Function and Timelines (FFFT). However, PD value not only comes as a function of the FFFT within the design package, it also comes as the degree the design package allows the end product to match the desires of the customer.
As information flows through the PD process, tasks add value to the information. Since the flows in PD are made of information instead of physical materials. Using the next seven info-wastes should enable to identify wastes associates with the information flows[5]:
Types of Information Waste | Examples | Causes |
---|---|---|
Waiting
Idle time due to unavailable information |
People waiting for information |
|
Information waiting for people |
| |
Inventory
Information that is unused or is “work in progress” |
Too much information |
|
Multiple/redundant sources |
| |
Outdated/obsolete information |
| |
“Just-in-case” information |
| |
Excessive Processing
Information processing beyond requirements |
Excessive/custom formatting |
|
Numerous, fragmented reports |
| |
Unnecessary serial processing |
| |
Excessive approvals for information release |
| |
Over Production
Producing, distributing more information than needed |
Unnecessary detail and accuracy |
design |
Pushing, not pulling data, information |
| |
Over-dissemination |
participant’s needs
rather than to meet specific needs | |
Transportation
Unnecessary movement of information between people, organizations, or systems |
Information handled by multiple people before arriving at user |
|
Information hunting |
| |
Data re-formatting or reentry |
| |
Switching computers (e.g., CAD to PC) to access information |
| |
UnnecessaryMotion
Unnecessary human movement (physical or user movement between tools or system) |
Walking to information, retrieving printed materials |
|
Excessive keyboard, mouse operations |
| |
Poor physical arrangement or organization |
| |
Defects
Erroneous data, information, reports |
Errors in data reporting/entries |
|
Errors in information provided to customers |
| |
Information does not make sense to user |
|
Application
Some tools which are useful but were not intended for Value Stream Mapping will be described friefly.
In order to build up a value stream map in a coherent way, we must take into consideration three main steps[5]:
- Arrange the process steps (tasks) and information flows.
- Follow the work: To uncover the true value stream, trap yourself to the product.
- Collect the information yourself: Try to walk the process, talk to participants, have them send you examples of documents or information regarding what they produce and handle.
- Exploit existing process information resources, cautiously: It is needed to understand the process personally but if someone helped collecting reliable data, use it.
- Map "in pencil": Make process maps easy, low-investment, adaptable and simple formats.
- Map the whole value stream: Have everyone work on the entire value stream and do not partition it right away. The goal is a holistic picture.
- Collect performance data on the tasks, sometimes information flows as well.
- Concentrate on what you need: If the problem is quality, look for errors and try to correlate them with their root cause.
- Exploit what you can find: Sometimes the data is not the primary purpose of the document, instead it may be usefull dates on reports as a record for cycle time.
- Make do with what you have: The data may be imperfect but if the data leads to the critical problem, it is usefull.
- Be honest: Make data reliable by putting asside possible biases.
- Dig deep (only) when you must: Only when analyzing critical problems and looking for solutions do further work collecting enough data.
- Evaluate how value is created.
- In detailed maps, specifically on lower level maps, non-value-added tasks may appear. Non-value-added activities may be hifing inside of value-added tasks, so try to add more detail to your map.
Although this can lead to an unefficient way to find them, it is a good way to begin with. For deeper understanding about how to evaluate value refer to the
Discussion
Value Stream Mapping can be thought as a tool which facilitates the transformation from a traditional manufacturing company to a Lean Enterprise. It is a planning tool to target ideal processes and roadmaps to desired improvements.[6]
Advantages
Limitations
Related Articles
The lessons from Toyota for product development had been captured by Fujimoto and Clark[7] and Ward and Sobek.[8][1] Follow the references for further study.
Most of the VSM work that has been acomplished is around the manufacturing context. For practical implementation of VSA/M on manufacturing operations please refer to .[9]
Understanding how to break the PD process down into stages:[10]
Key references
- ↑ 1.0 1.1 1.2 1.3 1.4 1.5 1.6 http://dspace.mit.edu/bitstream/handle/1721.1/7333/Value%20Stream%20Analysis%20and%20Mapping.pdf?sequence=1
- ↑ http://world-class-manufacturing.com/Kanban/kanban.html
- ↑ http://www.lean.org/Bookstore/ProductDetails.cfm?SelectedProductId=160
- ↑ 4.0 4.1 http://web.mit.edu/esd.83/www/notebook/WomackJones.PDF
- ↑ 5.0 5.1 http://dspace.mit.edu/bitstream/handle/1721.1/81908/PDVSM_V.1_2005.pdf?sequence=1
- ↑ http://citeseerx.ist.psu.edu/viewdoc/download?doi=10.1.1.201.6852&rep=rep1&type=pdf
- ↑ https://books.google.fr/books?id=7cCAASTW6IQC&hl=es
- ↑ https://books.google.dk/books/about/Principles_that_Shape_Product_Developmen.html?id=ZbYGtwAACAAJ&redir_esc=y
- ↑ https://www.amazon.es/Learning-See-Eliminate-Enterprise-Institute/dp/0966784308
- ↑ https://www.amazon.com/Product-Design-Development-Karl-Ulrich/dp/0070658110