Including Risk Management in Construction Projects
(→Implementing a Risk management process in a project) |
|||
Line 330: | Line 330: | ||
==References== | ==References== | ||
<references/> | <references/> | ||
+ | |||
+ | [[Category:Project Management]][[Category:Uncertaity]][[Category:Risk]][[Category:Risk Management]][[Category:Construction Industry]] |
Revision as of 14:25, 23 November 2018
Introduction
Construction is an inherently risky domain, as its projects are submitted to several contingencies, from the weather that may delay the project’s completion to limited involvement of some stakeholders or even accidents. Contrarily to other industries however, Construction have not really implemented structured risks management methods to handle those threats to each and every project.
The following article will try to offer a solution to that issue. As such it will define a risk and point out that risk management methods are really necessary within the management of a construction project. A short review of the methods currently used for managing the risks in the Construction buisness will point out that what is currently used is very unsatisfaying.
To adress this lack, we will then see the process used in general to treat risks within a project, and then list a few usefull tools, like the risk matrix or the Gantt chart. Those tools will not be explained (on how to use them) as other articles on this Wiki do it, but their benefits for a project will be detailled. To find a detailled explaination of how to use such tools or to implement them, links will be provided within the article, as its main goal is more to provide a list of usefull tools for a construction manager than precisely explain those tools.
In order to ease the application of the overview presented in the article, a kind of template to implement risk management on a project is presented as a detailled example.
Finally the limitations of risk management and its benefits will be detailled in the conclusion.
Definition of a risk
Risk itself is not always well defined[1] , but is used as a tool used to measure safety or the deviation from an objective. An overall definition can be that risk depends on the consequences, often negative or undesirable, of future activities with respect to something human being values, and the likelihood of those consequences.
A mathematical definition of a risk would be Risk = Probability of occurrence x Consequences.[2]
As a general concept, safety is the freedom to potential harm. Being totally free from potential harm is impossible, and so there is no 0 risk. The object of risk management is consequently to determine the risks and try to mitigate them in order to make the risk acceptable (which implies the creation of acceptance criteria).
However, a risk is not always negative, as using them is a major part of an entrepreneurship activity. It indeed may generate profit or innovations, as long as the risks are mastered alongside the process and not let alone to go astray.
"The biggest risk is not taking any risk... In a world that changing really quickly, the only strategy that is guaranteed to fail is not taking risks." Mark Zuckerberg.
"I think there's a difference between a gamble and a calculated risk." Edmund H. North
As pointed out above[3], the whole point with risks is taking some as they are necessary for a company to succeed, but not take them unwisely: hence the risk management process.
Quick overview of risks faced by the industry
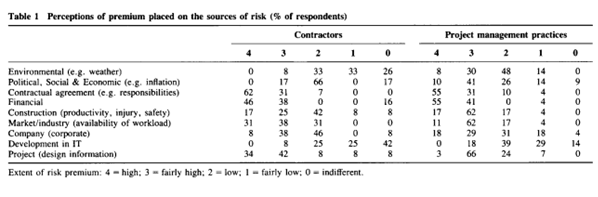
Several factors may endanger a construction project, and as such may harm a construction company. A construction project is usually complicated to manage[4] , with the need to handle some complexity (not always in the technicity of the project itself but more in its realisation), all the participants, who often have different when not divergent goals, and many other points listed below. As the project evolves constantly, with its completion advancing but also all the changes imposed by the field’s reality, numerous feedback and decisions must be processed, often in a short period of time. Usually Construction industry stakeholders are well aware of the numerous risks that may threaten their projects [5] , as pointed out in Figure 1. They tend to point out Contractual and financial risks as the main ones, but they are far from being the only ones !
All those phenomenons makes that historically construction has been a risky domain, with often projects not being completed in time or within the original budget, high level of conflicts and litigations between the stakeholders, most of the profits being generated based upon some risks (hence creating a low margin), and a bad record concerning health and safety.
The 2008 crisis didn’t improve the situation at all[6], as it reduced the number of contracts being awarded and so increased the concurrence between companies. This consequently tended to decrease quality to improve costs and delay, and generated more risks for all the stakeholders. It also put even more pressure to save time and money to generate profits upon the money invested in the project, as well as on the workers’ health and safety. Here are some of the of those risks, in different domains.
The following parts will quickly list the major risks a construction project may face throughout its lifecycle to illustrate the importance of risk management in such projects.
Organizational risks
Those risks are mainly around Costs, Time and Quality, and may be created mostly in the early phases of a project. They impact a company as a whole, not individuals.
• The first risk to take into account is the technical feasibility of the project, and the design issues. They can impact the whole construction process with high consequences upon the schedule or costs. The same risk may be created if the construction method is not adapted.
• The commercial benefits of a project may as well be a risk factor for the client. If for example the building is technically obsolete or has been built with a low quality, the advantages expected from the project may not be available.
• For the contractor one of the main risk is about coordination and communication with the other stakeholders of the project. He must as such ensure a good commitment from every partner, and be ready to face potential failures, both from a subcontractor or supplier and from the client (lack of fund to ensure the cash flow for a given milestone for example).
• During the tendering phase of the projects, setting up an unrealistic schedule or budget can also create a risk for the company and the client, upon the costs and or the schedule.
All those risks may as well impact the reputation of the company and then endanger not only the project but the whole business strategy.
Personnel, Health and Safety risks
They are the most obvious risks when studying construction risks. Even if some safety progress has been made, this is still a serious issue when planning a project, as more than 1300 death per year are still registered in link with Construction in the EU alone. Statistics shows that 90% of those construction-related deaths could have been avoided. [7].
The Safety risk is also important for people external to the project, for example the neighbours that may be endangered or hit by a site issue, like the fall of a crane.
Some personnel-related risks can also occur during the project. They can include strikes, sicknesses or holidays that could prevent the workers from being on site and so delay the progress of the construction process as well as a lack of commitment from the employees, either on the field or from the consultants' workers.
Events beyond direct controls
To conclude this quick overview of the risks a construction project may face, here are some events that may damage its process but that one can’t directly control:
• Dependencies between a new project and other projects. If two projects with different stakeholders interfere with one another it can impact the two of them but it may be really hard to address the issue.
• Some physical events can also present a risk. The weather is an obvious one, as concrete cannot be casted if the temperature is below 0, but it may also involve earthquake, wind, sandstorm,… which may be usual in some areas.
• Legal risks: depending on the country the project is to be carried out in, some specific legislation may be applied and can impact the project if they were unknown beforehand. They can also be created in some unstable countries with change of political regimes and their consequences (like nationalizations in Cuba with Castro’s arrival).
Those were some of the many risks a construction project may face. How are they dealt with in the Construction industry as of now ?
Methods currently used to face those risks.
Studies conducted both in the early 1990s [8] and, more recently, in 2008 and 2009 [9] (just before and after the 2008 crisis) showed that the methods used to deal with those risks in the construction domain have not really evolved, and that there is a real lack of methodology in their treatment.
As represented on Figure 2, most of those risks are treated either by creating some contingencies reserve or warranties or by transferring them to another party, insurance or project partner.
For those using some risk management methods, most of those techniques are not scientifically demonstrated and objectives ones, but are based upon experiences and the past. That kind of methods, useful to a certain extent, are however limited upon the knowledge of the employees and as each project is specific. They as a consequence can’t be enough to manage risks on themselves.
As those studies showed, risk management is not a developed field in the Construction industry, and there has not been any real progress in this domain in 20 years. Figure 3 point out for example that the huge majority of risk management processes are based upon past experience and documentations from previous projects, when risk management is even applied.
The following parts of this article will as a consequence present some methods to try and manage risks in a Construction Project.
General Process to deal with risks.
The whole process of risk management, which may be represented on a scheme like on Figure 4, begins with a risk assessment phase. It will require to analyse the risks, i.e. to identify them, and to quantify them using some methods presented below, in order to determine the risk as a mathematical entity.[10]
Once this process is complete, one has a list of risks and their probable impact and likelihood. The question is now to determine whether those risks are acceptable (“calculated risks”) and as such can be accepted, or if they should be somehow mitigated and controlled. This is the risk evaluation phase. During this step, the project manager should compare the risks he has identified beforehand with the acceptance criteria he established. Those criteria may be a company policy, let to the decision of each project manager, agreed with the other stakeholders, … It’s always a balance between the costs of the risk reducing policy required and the benefits of those measures on the risk. Once this comparison has been made, he gets the list of risk that he is ready to take, and others that need mitigating.
Hence the risk control process takes its turn. During this phase, the project manager finds out ways to limit the risks that were not considered acceptable in the risk evaluation phase. Four big techniques are mainly used:
• Avoid risk: This implies to change the methods used or remove the source of the risk. It’s not always possible but it is the best way to ensure a perfect control of the risk. A good example is the use of a toxic chemical: its utilisation generates risks. If this chemical can be replaced by another not toxic (for a reasonable cost), then the toxic risk can be avoided.
• Transfer risk: The main method currently used in construction projects, as seen before. This does not control the risk itself but mitigates its consequence for the company as somebody else is to take the consequences should something go wrong. Most of the time it consists on insurances warranties or the use of a subcontractor to take the risk in the company’s stead. This however leaves the risk existent and it may still harm the project, for example through unscheduled delays.
• Reduce exposure: This consist on reducing the risk by limiting the exposition to its source. It may for example be limiting the use of a crane to the really needing tasks to limit the risks of a load falling and injuring workers: it does not delete the risk but reduces it by acting on its probability of occurrence.
• Accept risk: Finally, when there is no other option whatsoever, the last remaining choice is to accept the risk. This should only be considered for acceptable risks as defined in the risk assessment process, as the risk will remain unmitigated (but should not be left unchecked however) during the whole project.
Once the mitigation methods have been decided, the last phase of control and monitoring may begin. It includes, in the preparation phase, the choice of risk response methods, which should be recorded in a document to allow a good and efficient application throughout the project. During the construction process itself, the risks should be monitored, to ensure that the first no one was forgotten during the preparation process and second that the assessment was correct and that a risk is not more important than expected.
This monitoring process must if necessary lead to some corrective measures to always keep the risks on track and mastered.
Figure 5 on the right highlights the main process to be deployed in an efficient risk management process: it should start by planning ahead of the actual construction, to determine the risks and their mitigation methods. Then, during the building process, those method should be applied, and monitored. If the control process shows anything wrong, it's important to immediatly react, it's the "act". This process is to be applied for the whole lifecyle of the project, and for each and every project, to successfully manage risks.
Tools applicable for Construction project
The following part will list some of the risk management tools that are well adapted to be used in risk management for a Construction project. In order to use the Wiki principle fully, the functioning principles of those tools will not be detailed here but there will be links sending to some detailed articles (when they exist) about each tool. However, for each point of the list, a short summary of the benefits and potential uses of the tool will be granted.
Qualitative methods
Those are, for some, the methods currently used in the industry. They include:
• Brainstorming. It is an intuitive method which uses the ideas of several people around the project in order to list possible problematic aspects (or possible advantages as a risk may be an opportunity) affecting the project. This can be used in order to gather as many risk as possible during the risk identification process, but it is mainly based upon people’s experience and imagination and as such may not be exhaustive or accurate, especially since every construction project is unique. The Deplhi Technique is also a brainstorming process but which keeps participants anonymous while each can see the results of the process. It may be a way to encourage participation and “crazy” ideas which may prove useful for the process. Using a SWIFT (structured what if technque) process during the brainstorming may help explore more paths and gather more risks, due to its methodology designed to make new ideas arise. Without the use of a SWIFT process, this method is really a basic one and may miss some of the risks that will appear during the realisation of the project.
• Interviews . This method is based upon the experience of the people being interviewed, either directly or through a paper questionnaire. This method has basically the same interest and flaw that the other qualitative method, as it is based upon people and experience as well. It's only recommended to use as a complement to more extensive methods.
• Check-lists. Using once again previous experiences, this tool aims to create a list gathering all the possible risks, their consequences and the mitigation methods. It may be used to be sure that no risk known from previous project have been forgotten and that the measures are correctly enforced (during the monitoring process). This is more a usefull tool as part of a documentation process (documenting the risks determined by other means) and of the control phase that a real risk identification tool, even if some companies use it as such.
• Scenario analysis . This method is based upon scenarios of possible future as imagined by the participants. They will then try to determine the necessary conditions to reach this future and the corresponding risks. This tool is really useful to determine the possible catastrophic events (like the fall of a crane for example) but is not really applicable to analyse a full project, as it's really time-consumming and will focus mostly on the main risks.
The result of the risk identification process, no matter how it was done (through brainstorming, check-lists or whatever) should be listed on a document like the one showed in Figure 6 to keep track of the process and ensure maximum efficiency.
Semi-Qualitative methods
They are methods using some qualitative process through an organized pattern.
• FMEA/FMECA(Failure modes and effects (and criticality) analysis. They are tools creating a map of possible failures and, for FMECA, their outcomes, to identify the critical failures. It may prove useful to determine critical tasks in a construction project and so to be able to pay special attention in monitoring the risks in those tasks. This is a useful tool to provide an overall analysis of a whole project as it starts from the failure of a small component and determines its consequences for the whole project. It should be performed at least for the critical tasks to ensure no risk have been forgotten.
• Cause-consequence analysis. It combines a FTA (fault-tree analysis) and an ETA (event-tree analysis) to determine the possible paths leading to a specific event. It may be used to determine the probability of an event and as such may prove useful to mitigate the risks linked to this event. It may lead to a bow-tie representation of the result, with the event central, the causes on the left and the consequences on the right, for a better visual comprehension of the study. This is really useful to use in case of an accident or incident to determine the errors and learn from them. However, it's quite time consumming like the scenario-analysis and as such can not really be applied to a whole project, but mostly to the major tasks.
• HAZOP (Hazard and operability study). Its main goal is to study a given activity to determine the involved risks. May prove useful during the risk identification process to list all the risk linked to a phase of the project. Like the FMEA method, this is one of the most powerful hazard identification tool as it provides a good and as exhaustive risk overview as possible. As such it should be applied at least on the major tasks of the project, if not on the whole project, depending on the commitment of the company in the risk management process.
• Decision tree analysis . This tool is mostly used as a forecast process, to be able to determine in advance the consequences of a change in the Construction project (mainly during the building phase on site). It may be completed with a MCDA (or Multi Criteria Decision Analysis) which allows to find out the best solution using objective and transparent criteria. This tool is mostly useful as a complement of a previous risk analysis, in case of a change of plan, to determine the change's consequences on the project and the possible risks it may create.
• Risk index. This is mainly the consequence of the risk identification process. It lists all the risk determine and ranks them using some normalized scale. It may take the form of an individual document for each risk like Figure 6, all the document being put together to create the index.
• Risk matrix. This tool is very useful when assessing the risk as it allows a visual representation of the consequence and the probability of the risk, and therefore its acceptance or not. A risk matrix may for example be built through the FSE (Fuzzy synthetic evaluation), which uses some qualitative and quantitative criteria to assess the risks identified beforehand.
• Gantt charts. Gantt Charts allows a good representation of the whole planning of a project and the critical path linking the different tasks, and as such permits an easy identification of the consequences of a delay or incident on the planning, easing the shedule risks. Some softwares used to create Gantt charts include ressources or costs in the chart, to make it more comprehensive and global. The Gantt chart is powerful to determine the critical path of a project and the interactions between it tasks, but cannot be considered as a risk identification method for the whole project on its own.
• HACCP (Hazard Analysis and critical control points). It allows a good overview of the phases of a project where a mistake may cause losses (of quality, time, money,…) and as such ease the monitoring control by focusing it on vital areas. This method is to be used to determine control points throughout the construction process to ease the monitoring process.
• SCI (Sneak Circuit Analysis). It allows a good identification of design errors that may endanger the good completion of the project and as such can prove useful when reviewing the early phases of a project, like the tendering and design phases. This tool is to be less useful in the future, when the use of BIM technics will already remove most of the design mistakes.[11]
Quantitative method
This is a more complex method that requires a mathematical approach to study the risks a project may face. Other methods exist but are not adapted to construction, like the Markov analysis (as it is useful only when the final state of a system depends on its current state, while a construction project depends on many factors).
• Monte-Carlo Simulation. This tools permits the simulation of a complex system (like a construction project) and is useful to determine the effects of uncertainty on such a system. It however requires a good investment as it uses probabilities mathematics and a numerical simulation. As such it may be reserved for big projects who justify such an investment.
Implementing a Risk management process in a project
The following part will illustrate the previous points by presenting an example of the implementation of a risk management process.[12] Consider a project for which the company wants to use risk management techniques, for example due to its high importance and sensibility.
Risk Analysis
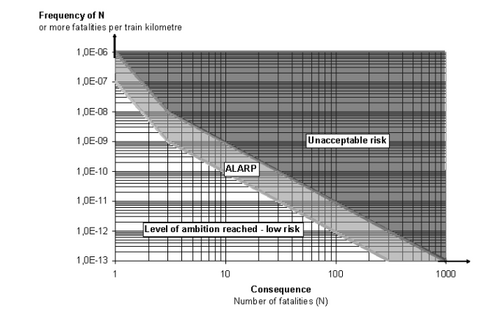
The first step of a risk management process. It may begin with a brainstorming involving all the stakeholders (as communication between different partners is really important if not vital in a construction project, and a lack of it often leads to delays, conflicts or worse). During this first approach of the risk analysis, a risk index listing all the possible risks generated in or by the project should be created.
This however is not sufficient, as some of the risks may very well be forgotten. As such, an HAZOP or SWIFT study completed with the realisation of a Gantt chart should be considered. The first tool will ensure that most of the major risks are included in the risk index, while the second one will provide useful informations on the consequences of potential risks on the completion of the project.
The aim of this analysis is to make sure (as sure as possible at least) that no risk is forgotten and that they won't come as a surprise during the project's realization.
Risk Assessment
The second phase of the risk management will be to evaluate the gravity and the importance of the risks listed beforehand, to determine which ones should be controlled somehow and which ones are acceptable.
A good first approach would be to create a risk matrix with the risks presented in the risk index. This will determine on which risks to focus the rest of the assessment, as the ones in the green part of the matrix can be accepted as such. To determine the criteria to use in the matrix, or maybe to complete it, it is possible to use some international standards, like the ALARP method (As low as reasonably achievable), which determines some limits to draw the acceptability of a risk. Other criteria exist, such as the MEM (Minimum Endogenous Mortality) or GAMAB (Globally as least as good, or Globalement au moins aussi bon in French) amongst several. When setting up the acceptance criteria, it is important not to forget that total safety doesn't exist (and so a 0 risk tolerance is unachievable), and that risk mitigation comes at a price: it's a question of Cost/Benefits balance, and as such some criteria may simply be unrealistic within the budget if set to low.
Another process to determine the acceptability and consequences of a risk, which is requiered in this phase, is to draw some cause-consequence diagram, maybe as a bow-tie, so that the risk assessment phase it accurate and as complete as possible. All the results of the assessment should be added in the risk index, which will be a comprehensive document to use during the construction phases.
Mitigation process
During this process, the focus will be on determining the mitigation methods to apply for each risk. It may be as simple as removing a dangerous raw material, or complex by modifying completly the construction methods. All the risks indicated as requiering risk mitigation should be studied and treated in this phase. The mitigation phases may not use some of the tools presented above as each project and risk are specific. This process relies mostly on employees' experience and imagination, and should take into account field's constraints to offer realistic and achievable solutions.
Once again it is really important to list all the solutions adopted in the risk index so that they may be correctly implemented afterwards.
Control process
This is the last step in our risk management process. During the whole life of the project, it consists in surveying that the risks discovered earlier were correctly assessed and that the mitigation technics are indeed applied. It's also necessary to follow the project progress so that potential new risks that may appear are immediatly detected and treated.
Conclusion and limitations
The Construction industry has to face several risks during all its projects. However, currently those risks are (more often than not) not well studied and forecasted, when forecasted at all. The methods to deal with them, usually transfer them to another party, is not a good one either.
Having determined that, this article presented the general path to ensure a good management of the risks. It also listed other ways to deal with a risk than transferring it to someone else. In order to promote risk management in Construction projects, it finally summarized some of the methods that may prove useful to determine and assess risks. A general risk management process has been detailled afterwards, using some of those tools, to explain its implementation, and may be used as a template for companies willing to implement risk management.
If the benefits of a risk management are real as it may reduce several losses, in both health, finance, schedule or reputation, this method is not infallible. It requires first of all an investment, like shown in Figure 9, in time, money but also a real commitment of all the stakeholders to make the analysis as comprehensive as possible[13]. The competences to handle a risk management process, whose lack usually prevent the process from being implemented, must be developed. Moreover, the management should be important in the early phases in the project (to avoid or reduce the risks beforehand) but must not disappear as it moves on: the enforcing and monitoring processes are where the benefits of risk management are made. Those constraints may explain the poor use of risk management in the industry today, but are not so important compared to the benefits of risk management.
Implementing such management may prove a little bit hard at the beginning, but with experience the benefits will be real for the company. In that risk management is comparable to BIM processes: relatively new and not well known, but with lots of benefits when correctly used. BIM may actually also be used to reduce risks in construction, as it is a formidable tool to improve communication between the stakeholders and visualize potential flaws in the project.
Annotated Bibliography
• Risk Management, Scott CULLEN, Hanscomb Consulting, 2014
This article presents some of the risks a Construction project may face, and their root causes. It also presents some of the methods to face analyse those risks.
• Construction Safety, Peter G. FURST, International Risk Management Institute, 2010
Presents the general history of risk management in the Construction Industry, and how risk may impact the project. Lists the communication issues that may be a source of risk in a construction project as well as the controls ensured by a good risk management policy.
• Risk analysis and management in construction, A.S. AKINTOYE and M.J. MACLEOD, International Journal of Project Management, 1996.
A presentation of the results of a study conducted in the UK in the early 1990s to determine how risk management was used. Also details the methods used in risk management and the reasons why it is not really a developed domain.
• Risk management in Construction project management, Martin SCHIEG, Journal of Business Economics and Management, 2006
Details the costs and benefits of a risk management process in a construction project. Defines the general steps of risk management and illustrates how risks should be addressed during all the phases of the project.
• Risk Management in Construction projects, N. BANAITIENE and A. BANAITIS, INTECH, 2012.
Presents the results of a study conducted between 2008 and 2011 about risk management methods used by companies. Lists some feedback from those companies on some aspects of risk management, as costs, methods or reasons justifying their limited use.
• Risk Management in Construction, Author unknown, Stakeholder Map, 2009.
Details some of the risks a construction project may face as well as some tools one can use in order to assess risks and monitor the risk mitigation process.
• Lecture Notes, Igor KOZINE, DTU course 42171 System Safety and Reliability Engineering, 2016.
Introduces some definitions of risks, safety,… and presents the general approach to study and manage risk in a system or in a project in the first notes. The following notes explains some of the tools widely used in risk management.
Possible additionnal readings
• BIM advantages on construction projects
This article from the APPPM Wiki detailled some of the advantages of using BIM technologies in a construction project, as BIM has been considered a few times in this article. It focuses on time management, as contruction projects are very often behind schedule.
• BIM as a project management tool
This article from the APPPM Wiki detailled some of the advantages of using BIM technologies in a construction project, as BIM has been considered a few times in this article. It offers a broader overview of the benefits offered by the use of BIM than the previous article.
Video
Video showing a global approach to risk management in a construction project as well as some tools that may be usefull in a risk management process. It is to be considered as an example of the many possible risk management process in a construction project, and it is here listed as an illustration of the article.
References
- ↑ ROSA 2010, SLOVIC 1999, ISO 31000, SRA Glossary provide several definitions of a risk
- ↑ ISO 31000
- ↑ http://www.brainyquote.com/quotes/keywords/risk.html
- ↑ Flanagan R, Norman G, Chapman R. Risk management and construction. 2 nd ed. Oxford: Blackwell Pub; 2006. and Mills A. A systematic approach to risk management for construction. St Surv 2001 ;19:245–252.
- ↑ Risk analysis and management in construction Akintola S Akintoye and Malcolm J MacLeod, International Journal of Project Management Vol. 15, 1996
- ↑ Risk Management in Construction projects, N. BANAITIENE and A. BANAITIS, INTECH, 2012. Example of the impact of the 2008 crisis on the Lituanian Construction industry.
- ↑ Brian Cooke & Peter Williams, 2004, Construction Planning, Programming and Control, Oxford: Blackwell Publishing.
- ↑ Risk analysis and management in construction Akintola S Akintoye and Malcolm J MacLeod, International Journal of Project Management Vol. 15, 1996
- ↑ Risk Management in Construction Projects, Nerija Banaitiene and Audrius Banaitis, INTECH, 2012
- ↑ Lecture Notes, Igor KOZINE, DTU course 42171 System Safety and Reliability Engineering, 2016.
- ↑ http://apppm.man.dtu.dk/index.php/BIM_as_a_project_management_tool_on_construction_projects
- ↑ http://www.stakeholdermap.com/risk/risk-management-construction.html A table summarizing the different phases of the Risk management process is available under the Risk Assessments part
- ↑ Risk management in Construction project management, Martin SCHIEG, Journal of Business Economics and Management, 2006