Critical Chain Project Management
(→Discussion) |
(→History) |
||
Line 7: | Line 7: | ||
Proponents of CCPM have attested that the benefits over PERT and/or CRM is that application of the Theory of Constraints focuses on how upper management are handling human behavior while envisioning the project network and in managing it afterwards, in constrast to dealing solely with specific technical aspects as the before mentioned methods.<ref name=GKRand/> | Proponents of CCPM have attested that the benefits over PERT and/or CRM is that application of the Theory of Constraints focuses on how upper management are handling human behavior while envisioning the project network and in managing it afterwards, in constrast to dealing solely with specific technical aspects as the before mentioned methods.<ref name=GKRand/> | ||
− | |||
− | |||
− | |||
=== Theory of Constraints === | === Theory of Constraints === | ||
Line 19: | Line 16: | ||
# Elevate the system's constraint(s). | # Elevate the system's constraint(s). | ||
# If, in the previous steps, a constraint has been broken, go back to step 1, and do not allow inertia to cause a system's constraint. | # If, in the previous steps, a constraint has been broken, go back to step 1, and do not allow inertia to cause a system's constraint. | ||
+ | |||
+ | The benefits of applying TOC varies from project to project. A review of the use in the industry show a clear positive effect for the companies involved. The results of 82 companies, ranging in size and industry, were aggregated and analysed. The results are shown in figure 2 and 3. Lead-Times, Cycle-Times and Inventory Levels were reduced by respectively 70%, 65% and 49%. Meanwhile were Due-Date-Performance, Revenue/Throughput and the Combined Financial Variable increased by respectively 44%, 63% and 76%.<ref name=Hallmark> ''Mabin, Victoria, J., and Steven J. Balderstone. The World of the Theory of Constraints: A Review of the International Literature. Boca Raton, FL: St. Lucie Press, 2000.'' </ref> The conclusion in this review was clear recommendation of TOC principles even applied to various degrees. Over 100 cases showed no failures or disappointing results.<ref name=Hallmark/> | ||
= Concept = | = Concept = |
Revision as of 23:17, 1 December 2014
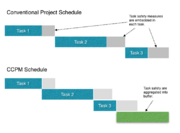
Critical Chain Project Management (CCPM) is a method of managing projects, where the attention is focused on the resources needed to execute various project tasks. In comparison to traditional project management methods that have its origins in critical path and PERT algorithms, where the emphasis is put on the order of tasks and strict schedules. [2] The typical critical chain project network attempt to keep resources levelly loaded, but requires that they are flexible in start times. Additionally a quick switch between tasks and task chains is desirable to make sure the project is on schedule. A simplified comparison between traditional project management planning and Critical Chain Project Management is shown in figure 1.
Contents |
History
CCPM was developed by Eliyahu M. Goldratt and introduced in 1997 in his book, Critical Chain.[3] Critical Chain Project Management is facilitated through algorithms and methods based on the principles of the Theory of Constraints.[2] The theory is outlined in the following segment.
Proponents of CCPM have attested that the benefits over PERT and/or CRM is that application of the Theory of Constraints focuses on how upper management are handling human behavior while envisioning the project network and in managing it afterwards, in constrast to dealing solely with specific technical aspects as the before mentioned methods.[2]
Theory of Constraints
Theory of Constraints, noted TOC in the article, is a description of how repetitive production systems, with the factor that every system exhibits a certain constraint and overall system performance can only be enhanced by improving the performance of the particular resource constraining the system. The critical chain technique is the realizing component to the theoretical TOC.[4] The Theory of Constraints is typically applied through five steps:[2]
- Identify the system's constraint(s).
- Decide how to exploit the system's constraint(s).
- Subordinate everything else to the above decision.
- Elevate the system's constraint(s).
- If, in the previous steps, a constraint has been broken, go back to step 1, and do not allow inertia to cause a system's constraint.
The benefits of applying TOC varies from project to project. A review of the use in the industry show a clear positive effect for the companies involved. The results of 82 companies, ranging in size and industry, were aggregated and analysed. The results are shown in figure 2 and 3. Lead-Times, Cycle-Times and Inventory Levels were reduced by respectively 70%, 65% and 49%. Meanwhile were Due-Date-Performance, Revenue/Throughput and the Combined Financial Variable increased by respectively 44%, 63% and 76%.[5] The conclusion in this review was clear recommendation of TOC principles even applied to various degrees. Over 100 cases showed no failures or disappointing results.[5]
Concept
Using traditional project management methods, around 30% of the lost time and/or resources are typically used in wasteful techniques such as bad multitasking, student syndrome, in-box delays and/lack of prioritization.[6]
When the critical chain methodology is applied in project management, the critical chain is the sequence of both resource-dependent and pre-exisitent elements that prevents a project from being completed in a shorter time under the condition of finite resources. If resources are accessable in infinite quantities at any given time, the project’s critical chain is identical to its critical path.[4]
Critical chain are used as an alternative to critical path analysis. There are four dominant features that differentiate critical chain from critical path. Those four are:[7]
- The inherent lack of quest for an optimal (shortest) critical path/chain. Typically a sufficient solution is the goal. This comes down to firstly, that there is no analytical method that computes the absolute optimal (shortest) critical chain. Secondly, there is a default uncertainty in effect, where estimates are by nature more volatile than the eventual difference between a optimal and near-optimal solution.[1]
- The use of (implicit) dependencies between resources. These dependencies can often be found by checking the resource requirements, yet they are not included in the project network.
- Identification and insertion of buffers; project buffer, feeding buffers and resource buffers.
- The critical chain method monitors project progress and overall status by looking at the consumption rate of buffers rather than single task performance across from the schedule.
Critical Chain Project Management creates a flexible plan by aggregating the amount of safety time included in separate tasks within the project to buffers. This is done to keep up the due-date performance and avoid wasting the given safety time to circumstances like Parkinson’s Law and inefficiently synchronized integration.[7]
Critical Chain Project Management make use of buffer management instead of for example earned value management, EVM, to measure the performance of a given project. This is done on the basis that earned value management can give a false picture of the status, because a clear distinction isn’t made between progress on the project constraint (the critical chain) and progress on non-constraining factors. In order to determine the size of project or resource buffers, the Event Chain Methodology can be utilized.[8]
Planning
Similarly to the critical path method, the planning phase is initiated by the creation of a project plan or work breakdown structure. The plan is typically designed working backwards from a requested completion date with each task starting as late as possible.
Each task is given a duration. In the implementation of CCPM, through software or other solutions, it is common to designate a best guess duration and a safe guess duration, which is deemed to be highly probable. Another way to implement it is by assigning a fixed percentage to be removed and aggregated into the buffers. [7]
Resources are then given to each task. The plan is resource leveled, i.e. start and finish dates are adjusted based on resource constraints to achieve balance, by utilizing the durations set. The longest sequence of tasks that lead from beginning to the end of the project is identified as the critical chain.[3]
Critical chain project management then applies buffers to monitor project schedule and financial performance. The variance duration between safe and best guess estimates are buffered at the end of the project. In a similar fashion, buffers are collected at the end of each sequence of tasks that feed into the critical chain. Typically the date at the end of the project buffer is used as the delivery date to external stakeholders.[7]
An alternative method for estimating duration over the project is by using probability-based quantification using for example Monte Carlo simulation. In can give a more broaden or in-depth perspective on certain areas of interest depending on the use case.[9]
Execution
Entering the execution phase is possible after the plan is complete. The project network is fixed and the size of the buffers are locked down and used to monitor the project schedule and overall performance and should therefore not be changed during the project.[3]
With little to no slack in the duration of individual tasks, resources are motivated to spend time on the task at hand in order to complete it and then hand it off to the next person. The goal is to mitigate poor multitasking. One initiative is to provide prioritized information to all resources. A relay race works as an analogy. While each component in the project is encouraged to proceed as fast as possible, they should be focused on the current task and finishing it as fast as possible without distractions. The analogy is even realized in some cases by having a physical baton to signal critical chain work is currently being performed and shouldn’t be interrupted. The result is minimizing the tendency to delay work. This is in contrast to traditional project management where tasks are mainly monitored against deadlines. In Critical Chain Project Management, it is encouraged to proceed as fast as possible, without attention to a given deadline. Planning task duration at 50% probability gives an intrinsic pressure on resources to finish critical chain tasks as quickly as possible. [3][4]
Monitoring
Proponents of Critical Chain Project Management typically deem monitoring as the greatest advantage of using the method. Tasks will inevitably vary in duration from the opening 50% estimate, which in turn removes the reason to force tasks to complete “on time”. Monitoring the buffers created during the planning stage will give a more useful result by utilizing chart or graphs that shows how much the buffer has been used as a function of the project completion. If buffer usage is little to none, the project must be on target. If buffer usage is exceeding the pace of the project, leaving insufficient amounts at the end, corrective actions must be taken to recover or stear the project on right course.[2] Similarly if buffer usage are surely done faster than project progress, ultimately resulting in late completion, relevant measures must be taken.[3]
Industry experience
Discussion
Since the introduction of Critical Chain Project Management it has gained in popularity as a novel approach to project management.[4] At the same time it has been met with various degrees of criticism dismissing the approach as hype and proposing that the novelty of CCPM to be in terms of terminology rather than substance.[1]
One of the criticisms is of one of the underlining theories behind CCPM. In the designation of CCPM it is said that task owners will overestimate the duration of the tasks and the eventual actual duration is simply the outcome of the deadline itself. This assumption is said to be unfounded in scientific evidence by the methods opponents. They give the example of a study from 2000 actually showing the opposite patterns, where upwards of 60% of task’s duration were actually less than the estimation. The second point in this criticism is the expectation given to project managers estimation of the safety factor. The point the critics are making is that since no absolute task duration estimation effort exist and if such a method existing it would naturally superseed the effect and be used as its own solution.[1]
Another criticism is about CCPM’s use of buffer in the planning and monitoring phase. Again it is questioned where CCPM is sufficiently based in evidence as no scientific or objective tool for determining the buffer size is provided. One key aspect here is the feeding chain concept. The concept is assuming that the project network consists of parallel paths starting at somewhat the same time and proceeds to merge into each other and eventually leading to the final resolution and outcome of the project.[7] This is presumably well fitting for assembly, construction and integration tasks, where tasks are narrowing towards the final task. A lot of other project however will exhibit a bell curve shape, starting initially with a few main activities, which then divides into multiple streams of tasks, before again merging as the project has intermediate deliverables. These complex flow are not optimally compatible with deriving a feeding chain with accompanying buffer. It will typically result in a schedule which is more or less indistinguishable from a traditional critical path.[1]
The TOC terminology is presenting the constraining resource as the key element to tackle appropriately. However at any given point in time, ideally there could be a multitude of constraining resources which each leads to a different schedule. In addition at different points in time, it will be various resources exhibiting constraining behavior. This would mean conflicting schedule and an overall conflict with the steady state view. It is proposed that steady state isn’t realistic in most project environments, which means that the applicability of CCPM can be questioned.[1] This is also a factor when looking at the approach to multitasking. CCPM is trying to achieve improved performance by limiting each resource to one task. How plausible this is in modern organisations is still undecided and other studies have shown a positive effect of the matrix organisation with up to 3 tasks given to a single resource. There is value in alerting resources to important opportunities for early-start of tasks in the critical chain activities, but the benefits of CCPM are seen more as a supplement rather than a substitute for traditional methods.[1]
The criticism, published in the Project Management Journal[1], entered the sphere along with other articles pointing out the same flaws/concerns about CCPM. Other articles focused on a balanced discussion of merits and pitfalls[7], while some focused on the proposed novelty of the methodology.[10] [4] A direct critical review of the main critical article pointed out amongst other arguments, the statistics mentioned earlier from the "hallmark of TOC literature"[5].[11]
References
- ↑ 1.0 1.1 1.2 1.3 1.4 1.5 1.6 1.7 Raz, Tzvi, R. Barnes, and D. Dvir. "A Critical Look At Critical Chain Project Management.” Project Management Journal 34.4 (2004): 24-32.
- ↑ 2.0 2.1 2.2 2.3 2.4 Rand, Graham K. "Critical chain: the theory of constraints applied to project management." International Journal of Project Management 18.3 (2000): 173-177.
- ↑ 3.0 3.1 3.2 3.3 3.4 Goldratt, Eliyahu M. Critical chain. Great Barrington, MA: North River Press, 1997.
- ↑ 4.0 4.1 4.2 4.3 4.4 Steyn, Herman. "An investigation into the fundamentals of critical chain project scheduling." International Journal of Project Management 19.6 (2001): 363-369.
- ↑ 5.0 5.1 5.2 Mabin, Victoria, J., and Steven J. Balderstone. The World of the Theory of Constraints: A Review of the International Literature. Boca Raton, FL: St. Lucie Press, 2000.
- ↑ Maylor, Harvey. "Beyond the Gantt chart:: Project management moving on." European Management Journal 19.1 (2001): 92-100.
- ↑ 7.0 7.1 7.2 7.3 7.4 7.5 Herroelen, Willy, and Roel Leus. "On the merits and pitfalls of critical chain scheduling." Journal of operations management 19.5 (2001): 559-577.
- ↑ ‘’Virine, Lev, and Trumper, Michael. “Event Chain Methodology In Details.” Project Decisions.
- ↑ Robert, Christian P., and George Casella. Monte Carlo statistical methods. Springer, 1999.
- ↑ Lechler, Thomas G., Boaz Ronen, and Edward A. Stohr. "Critical chain: a new project management paradigm or old wine in new bottles?." Engineering Management Journal 17.4 (2005): 45.’’
- ↑ “http://public.wsu.edu/~engrmgmt/holt/em530/ButtonEM540ResearchPaper.pdf”.