Contracting as a PM
The purpose of this article is to reflect on possible methodologies that can be used by a main contractor in large construction programs. The main contractor is expected to oversee and involve subcontractors and suppliers, along with managing the overall project. This article aims to discuss a few concepts and methods from supply chain management (SCM), that can be used by contractors in civil engineering projects. The hypothesis of this article is, that it is possible to use supply chain management tools in order to manage, involve and oversee large construction projects. The article will draw parallels between SCM and contracting concepts, finding similarities and differences from a contracting perspective.
Contents |
General
Flow of products, supplies, information, and resources is essential in order to successfully create and plan a project. Logistics provides a solid framework for flow-based plans, such as manufacturing and development facilities. Supply Chain Management (SCM) builds upon this framework, and seeks to manage upstream and downstream relationships with suppliers and the client, in order to achieve enhanced value in the final market with less cost to the supply chain as a whole [1]. The goal of supply chain management differs from each chain, but it could include a wish to reduce buffers in warehousing, by sharing information and co-ordinating the suppliers. The focus of a supply chain is to establish co-operation and trust between suppliers and clients, in order to optimize the final output.
Contracting
The term contracting often describes the act of entering a formal and/or legally binding agreement. In civil engineering, management contracting is the agreement that the work is carried out by several different work contractors, who are either contracted to the client or a management contractor (main contractor). The various different work contractors may include suppliers, manufacturers, retailers or workers, and it is the job of the main contractor to manage them all and ensure that the project goes according to the project plan.
A general contractor (main contractor, management contractor) is responsible for the coordination of a construction project, and will oversee the daily progress at the site. The contractor will manage and be responsible for turnkey -, main -, and individual trade contracts[2], and ensure communication between suppliers, traders and the client throughout the course of the project. The client employs the contractor after a bidding process; where an estimated price is presented. The price should cover cost of overhead, materials and equipment needed. The client should choose a contractor based price, quality and/or reputation, so it is important for the contractor to have either a value - or cost advantage. During the project, the main contract will transfer the project management from the client to the general contractor. The general contractor will then (depending on the contract) fully manage the suppliers of materials and equipment, as well as labour and services needed for the project. The general contractor may hire subcontractors to deliver turnkey projects, which are fully functional upon delivery. He/she will also be responsible for safety on the construction site, managing personnel, and applying for the necessary permits. In most cases, the management contractor will find himself as a program manager, as he has to oversee many projects performed by subcontractors, along with the overall project of the construction.
The client may choose to coordinate and manage the program themselves, by not hiring a general contractor, but by entering contracts with several individual trade contractors. The client could also choose to split the management of the project by making grouped contracts, which allow related trades to coordinate their work. By using grouped contracts, the client will have fewer contracts to manage contrary to the individual trade contracts.[2]
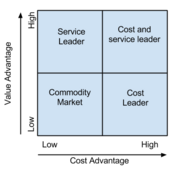
Management of a Network
The work of a management contractor can in many ways resemble the work of a supply chain manager, as both are responsible for overseeing a network of connected and interdependent organisations, suppliers, subcontractors and/or resources. This network must be managed in such a way, that the enteties work together to manage and improve the flow of materials and information. In supply chain management there are several theories and methods to optimize and manage the network flow. The managing contractor relies mostly on the contracts of his suppliers, and has very few tools to help him optimize the resource and information flow. Furthermore, often unlike a supply chain manager, the management contractor works within a finite amount of time. Construction projects often have a finite timespan, in which the building must be designed, built and made habitable. A supply chain manager usually has an infinite amount of time, as his work often based on a market pull-strategy and covers several project portfolios.
As companies often aim to be succesful, they will seek to achieve a position on the market, where they can offer both a cost advantage and a value advantage. As seen on the logistics and competitive advantage matrix[1], it is suggested to have a cost and service leader in order to achieve a competitive advantage on the market. This also applies to civil engineering companies, where a large project can either save a company from bankruptcy or put them in the grave. Obtaining both cost leadership and service leadership, will put an organisation in a leading position within the market. To accomplish this, it is critical to have an experienced managing contractor leading big projects. But even an experienced managing contractor may find himself in need of methods, theories and tools, in order to oversee a project. This article seeks to briefly discuss the similarities between some key concepts of supply chain management and contracting projects.
Methodologies
Supply chain management and contracting have several resembling activities and duties, that can be analyzed. The most obvious and important parallels include management of suppliers and Stakeholder Management, and having to deal with late refreshment of equipment or resources. These can be considered to be some of the most critical tasks for the manager during the project, as the rest of the network rely strongly on either suppliers, stakeholders and/or resources. There are different tools and theories used to manage these activities in both/either SCM and general contracting.
Stakeholder Management
Managing the stakeholders is critical for a construction project, as the project can have both internal and external stakeholders, on either the demand side, the supply side, the public sector and the private sector. All these stakeholders must be managed accordingly, and there are several different methods in doing so. The first step to stakeholder management in both supply chain management and contracting is to do a Stakeholder Analysis, in order to point out the different stakeholders and their attributes.
Mapping Stakeholders
In construction projects, the managing contractor often maps the stakeholders in a Winch-Bonke framework(REF). This map focuses on the project mission, and stakeholders can be considered to have a problem with the mission, and to have a solution that will resolve the problem. If the solution is inconsistent with the client's wishes, then the stakeholders can be defined as being in opposition to the project. The managing constructor should seek to turn opponents into supporters. This can be done by offering appropriate changes to the project mission, ensuring that both the stakeholder and the client are satisfied. At the same time, the managing contractor should ensure that supporters do not turn into opponents by offering to incorporate their proposed problem solutions.
The Stakeholder Matrix
Managing the Bull whip-effect
Discussion
Conclusion
Notes
21-09-15: Please note that this article will be renamed on the 23rd of September, 2015.