Modularisation: A modern process for project management
Nearly all projects are characterized by a certain degree of complexity and uncertainty. However, every project is unique and its success depends on various product development and management processes vital for the current rapidly changing business environment. Within this context, it has become increasingly important for companies with vast product portfolio to be able to manage the project complexity in order to increase efficiency and ensure competitive advantage in the long run.
Modularization is a process that breaks down complex systems into small and solvable parts. By dividing the product structure into modules, companies seek to optimize the way they function and operate in terms of transforming their products in a more flexible and accurate way. Modularization has gained momentum over the years as it helps projects achieve significant benefits by removing underperforming processes, products and parts. Since it is still a relatively new field outside the automotive and aircraft industry where it initially evolved, there is a growing interest in the development process of the modular patterns.
The purpose of this article is to explore the potential of modularization as a proactive strategy and product development tool for managing effectively the complexity derived from project and portfolio management processes. The article comes along with a detailed analysis on product modularization.
Keywords: complexity management; product modularity; modularization;
Contents |
History
This section refers to the evolution of modularization in order to get an understanding of the origins of the concept. The term module comes originally from the Latin term modulus and it is the diminutive of the term modus which means measure. Several meanings of the term module exist but the most important range from “a standard or unit for measuring” to a separable component that is “interchangeable” with others for assembly into units of different size, complexity or function.
In architecture, modules were associated with the Bauhaus philosophy leading to the configuration of the so –called “building blocks” (Baukasten) being individual functional units in buildings, easy to be assembled. Purpose was that modules were used as an arbitrary unit adopted to regulate the dimensions and proportions of parts of the building system for better design and coordination. One extraordinary project example of industrialized building blocks was the industrialized modular housing “The Packaged House” designed by well-known architects Konrad Wachsmann and Walter Gropius. It described a modular system comprising of a coordinated set of elements that allowed an infinite number of interactions for the final configuration and satisfied the housing needs for functionality, quality, uniformity and precision. However, it was not realized in practice, but the designs reflect the conceptualization of modularity.
Product architecture
Product architecture is defined as the arrangement of functional elements, the mapping from functional elements to physical components and the specification of the interfaces among the physical components. Product architecture is determined early in the development process. Ulrich and Eppinger provided a detailed analysis of the design process. In the following figure, the generic development process is composed of the following phases: concept development, system-level design, detail design, testing and refinement and production ramp-up.
Integrated Architecture vs Modular Architecture
“The characteristics of modular and integrated architectures are compared in the following table based on Ulrich and Eppinger (1995). Products are rarely strictly modular or integrated; rather, they involve some degree of modularity.”
Integrated Architecture | Modular Architecture |
A collection of components that implement some functions of a product is called a block. | A collection of components that implement some functions of a product is called a module. |
The functional elements of a product are implemented using more than one block | Same as an integrated architecture. |
A single block implements many functional elements. | A module implements one or a few functional elements in their entirety. |
The interactions between blocks are ill-defined and may be incidental to the primary functions of the products. | The interactions between modules are well defined and are generally fundamental to the primary function of the product. |
Product performance can be enhanced through an integrated architecture. | Product performance may not be enhanced by an modular architecture. |
Changing a block in an integrated product may influence many functional elements and require changes to several related blocks. | Changing a few isolated functional elements of a product may not affect the design of other modules |
Conventional Product Development
Traditionally the development of a product begins with the concept. As soon as the step of idea generation is completed, there is a sequential development of the design activities which ensures that technology and component development activities are resolved in every stage. Components interfaces are not specified in detail in the early design phase, but later in the process. The process repeats until all components are fully developed. The output of the development process is the final product which defines as well the product architecture.
The drawback in this conventional process lies in the dependency of the development of components and interfaces. An alteration in the technology of a component will cause significant technical difficulties as well as uncertainties for the outcome of the final product. Since, all components are dependent with each other; a change in one part may be translated into a ‘domino effect’ of redesigning components or even worse replacing some of the component development processes.
Modular Products
Modules
Modules are different from building blocks in terms of the degree of possessed functionality compared to the final product. Building blocks are stand-ins for modules. They have a standardized interface which allows assembly by combinations, even though they are characterized by a very limited functionality compared to the construction of which they are a part. However, modules possess a significant amount of functionality and can configure the final product by using building blocks which contain specifications of both interface and functionality and allow the combination with other modules.
Modular design
The idea to design a system with a modular focus lies on the multiple benefits of making available to the customer a variety of choices regarding the final product. Many new products were made possible by creating flexible solutions through plugging in a new module to the existing one, leading to the creation of a large product portfolio among companies.
Modular Product Development
Compared to the conventional development process, modular product architecture fully defines the specifications of the component interfaces and the constraints regarding component development. In this model, there is a complete structure in the flow of information which is well controlled with the decoupling points and defines the desired output prior to the development and detailed design of components. The main advantage is that product architecture is defined at design stage and does not change during development allowing the leveraging of multiple new product variations.
Tools
Modular Function Deployment (MFD)
Modular Function Deployment tool is used as a step by step process of how to investigate which part of the architecture should be modularised and which should be standardised.
Modular Function Deployment (MFD) is five-step process for translating the customer requirements into a modular architecture while taking into account the strategic intentions of the company. Modular Function Deployment (MFD) tool is used as a step by step process of how to investigate which part of the architecture should be modularized and which should be standardized according to the product properties.
1. Clarification of product specifications
2. Functional decomposition, analysis of functions and selection of technical solutions
3. Identification of potential modules
4. Evaluation of concepts
5. Improvements for each module
Design Structure Matrix
A module is defined as a group of activities which are divided by split or merge points in a process flow. The design structure matrix (DSM) is used to structure the process because it has a lot of advantages in process modeling and analysis. Process modularization is the term that describes the activity of structuring the process in terms of a module and allows a manager to manage and deal effectively with complexity problems in product development. The overall idea is to identify and capture the interdependencies across all design activities.
Application
This section focuses on the application of modularization which is related to almost any project, covering a wide range of industries. It gives a clear idea of how can projects be analyzed and modularized in order to support comprehension and modification during their life cycle.
Automotive Industry
Modular Construction
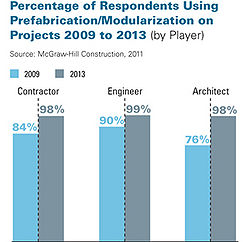
Besides the automotive industry, the concept of modularization becomes relevant for other industries. Construction projects consist of a large number of activities that need to be set from the preliminary planning phases. They also have to be well-communicated through the several stakeholders as well as delivered in a cost-effective way. There are many factors that affect the outcome of a construction project and it is out of the scope of this report to outline each one of them. Therefore, this section focuses on how modularization is applicable to construction industry from a scheduling point of view.
To deal with project uncertainty in construction, it is significant to consider all the available information. However, in the beginning of a project, as there is limited information available, uncertainty is further increased. To deal effectively with this problem, modularization needs to be considered by incorporating uncertainty in the scheduling process .
In the building sector, modularization as a term is often associated with prefabrication, therefore when we refer to modular elements, we mean prefabricated elements. Prefabrication/modularization yields significant benefits for the industry players in terms of reduced project schedule.
Permanent Modular Construction
Modular smartphones
The concept is rather simple and is based on building your own perfect smartphone. How modularization can be applied in the mobile industry? It represents a rethinking of the mobile phone, a reshape of the mobile landscape. That is translated into a consumer product being a modular phone made from detachable blocks, which are all connected to the base of the phone.
Why is it important?
Mobile phones have a lifecycle of less than 2 years in developed countries which reflect that electronic devices are not designed to last very long. Electronic waste (e-waste) is considered as one of the fastest growing component of the municipal solid waste stream with approximately 20-50 million tons of electronic waste generated each year . In general, the life cycle of the numerous electronic gadgets is getting shorter increasing the solid waste problem.
The design concept was originally conceptualized from Phonebloks as a means of reducing e-waste. Phonebloks main vision is to make a “phone worth keeping”. Google also wants to be part of software transformation by undertaking the Project Ara with the desired goal of reducing hardware prices and allowing any manufacturer/developer to contribute hardware modules and add-ons that could be sold via an online marketplace/platform .
Users will be able to choose their own smartphone experience by simply replacing the discrete blocks that affect negatively the performance of the phone and suit their desired needs. For example, if the phone is getting a little slow, the user can upgrade the block that affects the speed (this refers to the replacement of a component). If there is a broken piece, then it can also be replaced or updated with the latest version offered by the industry developers.
Modularization offers variety which contributes to meeting customer’s needs in the end. Modular smartphones offer vast opportunities with regards to customization, configurability and personalization. The user will be able to replace any block according to his present preferences (e.g. upgrade camera, swap/replace storage battery block, etc.) or even develop his own blocks.
Modularization is currently shaping the mobile industry by offering to the users the chance to create their own phone with easy and flexible modifications of the core components (processor, camera, etc.). However, modular smartphone as a product still remains a challenge to be solved. As all projects are complex, developing such a device is a wicked task as many factors should be taken into account in order to be both commercially and technically successful.
Benefits offered by Modularisation
Modularization is trying to optimize the product development processes by bridging the gap between product differentiation and economies of scale. Modularization offers a high variety of product standardization along with a flexible way of rapid product development in order to identify and fit customer needs. Some of the potential benefits of modularization according to a number of researchers are summarized in the following table:
- Economies of scale
Natural economies of scale arise as modules will be produced in relatively large quantities.
- Increased feasibility of product/component change
Since each module interface is strictly specified, changes can be made to a module independently of other modules, provided the interfaces remain within specifications.
- Increased product variety
The use of modules means that a great product variety can be achieved using different combinations of modules.
- Reduced order lead-time
Since modules are manufactured in relatively large volume, the logistics of production can be organized so as to reduce manufacturing lead time. Hence, the order lead time can be reduced.
- Decoupling tasks
Since the interfaces and modules have been standardized, their interfaces enable design tasks and production tasks to be decoupled. This decoupling can result in reduced task complexity and in the ability to complete tasks in parallel.
- The ease of product upgrade, maintenance, repair and disposal
Since a product is decomposed into modules, only certain modules need to be replaced when repair is done. For the same reason, upgrades, maintenance, and disposal are also made simpler.
Sustainability and Life cycle
As companies have to play a significant role in mitigating and adapting to climate change, a holistic modular approach needs to be considered in life cycle engineering. Modularization is increasingly becoming more and more relevant as a modeling technique that can assist companies achieve their sustainability goals.
‘’Sustainability has become a component of business success and project management is one of the ways to get there’’ (Joel Makower, the Oakland, California, USA-based author of Strategies for the Green Economy) Put it to the right
By embedding sustainability into the product portfolio management, companies could deliver environmental, social and financial benefits to the business meeting the rising global demands covered in the concept of a Triple Bottom Line
As one of the most important properties of modules is their interchangeability, modularization addresses product life cycle concerns and should be integrated across the company’s product portfolio. Creation of an ecosystem with modules translates into a concept that has effects on the life cycle of the product. By modularizing a product, companies can identify the hot spots and integrate the environmental considerations where necessary. Modules, as being detachable units can be maintained, upgraded, reused, recycled offering a wide range of advantages and enhancing the objectives for life cycle thinking.
Modular design is more essential than ever as organizations can design for functionality and generate solutions modular enough to reduce the environmental impacts associated with the life cycle of the product. From the product life cycle perspective, modularization may also have relevant application to the eco-design principles and what is called the “6 RE Philosophy” .
6 RE Philosophy | Applicability in modularization |
* Re-think the product and its functions e.g. how the product may be used more efficiently. | Modular design decomposes a product into separate modules. These modules can be designed taking into consideration energy efficiency requirements. Modular design can help by grouping into one module components that undergo similar life cycle processes. |
* Re-duce energy and material consumption through a product’s life cycle. | Modular design decomposes a product into separate modules. These modules can be designed taking into consideration energy efficiency requirements. |
* Re-place harmful substances with more environmentally friendly alternatives. | Same concept as before. |
* Re-cycle. Select materials that can be recycled, and build the product in a way that it can be easily disassembled for recycling. | Modular design facilitates the recycling process by separating and sorting the variety of materials which require different recycling or disposal methods . Therefore, material compatibility is necessary to be considered when designing in a modular way. |
* Re-use. Design the product so parts can be reused. | The life duration of components is not always the same, thereby some components may be usable again or re-manufactural upon retirement. Thereby, modular design allows to group components into easily detachable modules such that they can be easily reused or remanufactured . |
* Re-pair. Make the product easy to repair so that the product does not yet need to be replaced. | Same concept as before. |
Changing a block in an integrated product may influence many functional elements and require changes to several related blocks. | Changing a few isolated functional elements of a product may not affect the design of other modules |
On this context, the configuration of a modular product that is part of an engineering system should be evaluated from the early design stage – representing the most crucial phase for the system to be properly developed and its functions to be determined. Organizations are called to transform their operations, products and services in order to contribute to sustainable development and climate change.
It is important to note that modularization can be a way for organizations to deliver more responsibility towards the realization of environmental advancements. Organizations that implement modularization within their operations, not only can manage more effectively the assessment of the environmental impacts of their products but can potentially achieve more economic benefits, both in the product and also in the organization.
Limitations
Further Development
Modularization is still under development...
Annotated Bibliography
Lampel, J. and Mintzberg, H., (1996) "Customizing Customization," Sloan Management review. Fall 1996, pp. 21 – 30 Erixon, G. (1998) Modular Function Deployment - A Method for Product Modularisation, Doc. Thesis., KTH, Dept. of Manufacturing systems, Stockholm, Sweden. Blackenfeldt, M.. (2001) Managing complexity by product modularisation: Balancing technology and business during the design process , Doc. Thesis, KTH, Dept. of Machine Design, Stockholm, Sweden. [1] The Option Value of Modularity in Design, Harvard Business School
References
References are still under development...