Kanban framework
Kanban can be referred to as either a method within process improvement or a visual method in Just-in-Time and Lean manufacturing, following article will be focusing on its uses in process improvement.
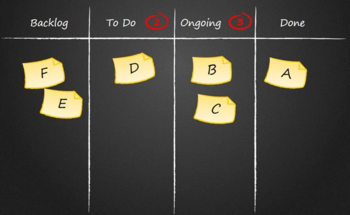
The Kanban methodology originates from Japan and is therefore a Japanese word that can be translated to “signboard”. Kanban is a framework that is used in teams that is following the agile methodology, which has gained popularity throughout the software development industry, since the adaption by David Anderson back in 2010. To practice Kanban, it is essential to acquire a lean thinking mindset, which focuses on the improvement of processes and elimination of waste, called Muda in Japanese [2]. To understand more about Lean manufacturing visit following link: Lean in Project Management.
When teams want to implement lean and a lean mindset, Kanban can work as a beneficial method to bring exactly this to the team, which is explained by David Anderson in following quote.
“The Kanban Method introduces a complex adaptive system that is intended to catalyze a Lean outcome within an organization. Complex adaptive systems have initial conditions and simple rules that are required in order to seed complex, adaptive, emergent behavior.” – David Anderson [3]
In general, Kanban helps project managers to keep an overview of their projects and the tasks involved in them, it also increases collaboration between the team members that is involved within the projects, mainly because visualization with the use of Kanban boards, creates project transparency. How exactly Kanban works will be the focus of this article with an overview of the historical development of this specific method, an elaboration on its uses in project management and its features will also be enlightened, where the final point of the article will define some of the limitations that is linked to the use of Kanban.
Contents |
Historical State of the Art
In the Japanese Edo period, which spanned from the 17th to the middle of the 19th century, Japan experienced stability and economic growth throughout the country, after several decades of war and instability. Through this growth, local shops and street markets gained popularity and to attract eventual customers the shops started using different signs and boards to attract potential buyer’s attention, this was the birth of Kanban. Kanban’s of that time tried to tell the buyers a message by clearly communicate what the shops would sell, which is also applicable for the use of Kanban to this day, by being a way to communicate content to the user visually and clearly. Cite error: Invalid <ref>
tag;
invalid names, e.g. too many
In the mid 1940’s Japan faced a post-war shortage on materials and low volumes of production, this meant that it was necessary to utilize the materials in the most effective way and hereby raise the productivity to achieve a higher volume of production. This was also applicable for the Japanese car industry that was greatly stagnating. One of these car producers were Toyota, which at the time made economic losses and could not compete with other global carmakers. This changed by Taiichii Ohno, who at that time was an industrial engineer at Toyota. He sought inspiration for changes by studying an American supermarket, which only replenished its stocks when customers had bought the available products and hereby work as a pull system, where the demand and pull of products directly affected the supply of products. This inventory system was called “Just-in-Time” and was a great effector on the reduction of waste which leads to low throughput and low performance. Taiichii Ohno implemented this system to Toyota and called it Kanban, because of its new way of signal demand throughout the factory and the foundation for the “Toyota Production System” were made. Toyota Production System is acknowledged as the predecessor to the more generic Lean manufacturing. (Kilde: Lean bogen, https://kanbantool.com/kanban-guide/kanban-history og https://getnave.com/blog/kanban-history/)
In 2010 David Anderson wrote his book “Kanban – Successful Evolutionary Change for Your Technology Business”, where he enlightens a new way to introduce Lean ideas and methodology into technology development and IT operations with the use of a new Kanban method that utilizes the Kanban system which is known from the Lean methodology. He did this based on his work and observations at Microsoft where he worked as a development manager. The book describes how he sought a solution to overcome deadlines that were set by managers with no regard to possible complexity, risk and size of project. There was a need for a change that would increase productivity and quality, together with a new norm on working schedules and work commitments, it was described that there was a need for protection of the demands towards the software teams and for a sustainable work pace. The initial findings Anderson made, were through the use of a pull system called “Drum-Buffer-Rope” which is an application for flow problems and an approach in the “Theory of Constraints” framework developed by Eliyahu M. Goldratt. One of the side effects using the Drum-Buffer-Rope system and in general a pull system is that it limits work-in-progress and hereby limits overloading of workers. The implementation of the system showed great result in productivity and in lowering of lead times, therefore a success. The transition to another pull system, Kanban, happened simply because it was found that implementing a Kanban system the results would have been the same, but also because of its easy access and because it has a wider acknowledge than the Drum-Buffer-Rope system. (Kilde: Kanban bog, learning agile)
Kanban in Project Management
Not a methodology for project management, but has an important relationship to it.
”Kanban is not a software development lifecycle methodology or an approach to project management. It requires that some process is already in place so that Kanban can be applied to incrementally change the underlying process.” (Kilde: Kanban by David Anderson)
- Start with what you do know
- Agree to pursue incremental, evolutionary change
- Initially, respect current roles, responsibilities and job titles
Kanban can be used in the context of Scrum in Scrumban
Use ref: Managing Successful Projects with PRINCE2 2017 Edition
Features of the Kanban framework
Visualize Workflow
- Describe kanban cards and boards
Limit Work-in-Progress
- Stay to the script
Measure and manage flow
- Use of CDFs and WIP area charts
Make process policies explicit
- Securing a common understanding
Use models to recognize improvement opportunities
Limitations of the Kanban framework
- Describe what limitations there has been found when working with the Kanban framework
- Use of Scrumban can cover some of the limitations
Annotated Biography
References
- ↑ The kanban method. (2022). How to implement kanban. [1]
- ↑ Stellman, A., & Greene, J. (2015). Learning Agile: 1st edition. O'Reilly Media
- ↑ Anderson, D. (2010). Kanban Successful Evolutionary Change for Your Technology Business. Blue Hole Press
Other notable references not yet used: Books:
- Learning Agile: Understanding Scrum, XP, Lean and Kanban. By Andrew Stellman & Jennifer Greene
- Kanban: Successful evolutionary change for your technology business. By David J. Anderson
- The Lean Toolbox: A handbook for lean transformation. By John Bicheno & Matthias Holweg
Websites:
Articles:
- Identification of criteria affecting software project monitoring task of Agile Kanban method. By Hamzah Alaidaros, Mazni Omar and Rohaida Romli
- https://aip-scitation-org.proxy.findit.cvt.dk/doi/pdf/10.1063/1.5055423
- Collaborative Work Management with a Highly-Available Kanban Board. By Annette Bieniusa, Peter Zeller, and Shraddha Barke
- file:///Users/JakobWeber/Downloads/5bd0583fd9001d01d4104a4f.pdf