The Last Planner System in Construction Projects
The manufacturing industry has for a long time been dealing with waste and inefficient production. To manage this, lean management has been used to make the production more efficient. The lean ideology has now been adjusted to the construction industry and is called Lean Construction (LC). But LC did not become popular in the construction projects until the Last Planner System (LPS) was introduced as a lean management tool. LPS is a tool that covers both project management and planning in a way that those who do the work also plan it. All managers are activated in the planning process which ensures that teamwork is one of the main focuses. The idea behind LPS is to create a steady flow by minimizing waste and constantly implementing reformation, all in order to increase the value for the customer.
Before the Last Planner System is described in detail it is important to understand that the construction industry is different from manufacturing and that lean management does not work the same in both. This article will first go over characteristics of the construction industry compared to the manufacturing industry. After that, the LPS tool will be described in detail and a framework for its implementation in construction projects will be given. In the end, benefits and challenges due to implementation of the LPS tool are listed.
Contents |
Characteristics of the Construction Industry
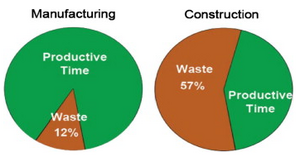
In the last couple of years, many construction organisations have changed their management so it is more similar to what is customary in manufacturing industries in order to increase productivity. In most cases it does not work out since there is a fundamental difference between these industries. One of the biggest difference is that manufacturing is based on stability while construction is based on variability. Construction projects have to deal with one-off production with variable resources and projects with long delivery time. They usually have clear start and end point which is usually defined in a signed contract between the contractor and buyer. Another thing that is different between these two is that construction often takes place outside where it is exposed to external influences and it normally requires labour intensive processes. Manufacturing processes are usually planned before fabrication starts while in construction they are usually planned during fabrication [3]. This makes it hard for construction managers to learn from mistakes that are made during projects, also since projects are usually one-off. This is not the problem in manufacturing since they have the opportunity to constantly learn from their mistakes during design, process planning and production.
There is a lot of waste in the construction industry. Waste can be defined as: “Anything different from the absolute minimum amount of resources of materials, equipment and manpower, necessary to add value to the product.” [1] As can be seen in Figure 1, 57% of all the time used in a construction project is not productive and is therefore not value adding for the client, which makes it a waste. At the same time, waste in manufacturing is only around 12%.
The Last Planner System
The LPS tool was custom-made for construction projects by Glenn Ballard and Gregory Howell around last turn of the century. The goal was to reduce waste by using ideology from lean management. The LPS tool is a mix of both project- and production management and is supposed to convert what should happen to what can happen by letting those who are closest to the work also plan it. That is why it is called the last planner. That person is supposed to have control over men power and resources because he has the best overview over what can be done with the resources available at the time. In effect, the last planner says that he will work on some specific tasks. This forms the basis for weekly work plans that control the production. Then it needs to be checked what was actually done and while doing that it has to be kept in mind what can be done on order to improve processes, planning and waste. Therefore, it is the change from what should happen to what can happen, will happen and what was done that makes the foundation of the LPS tool [4].
The Four Phases of the LPS Tool
The LPS tool consists of four phases. These phases can be seen on Figure 2 and how their internal connection makes the whole LPS process. In the first phase there is a lot of uncertainty which reduces with going down the figure. The same goes for details that have to be reckoned with, it is not done much in the first phase but increases with every step down. It is also necessary to keep in mind that when going between phases it is important to revalue what should be done with what can be done [5].
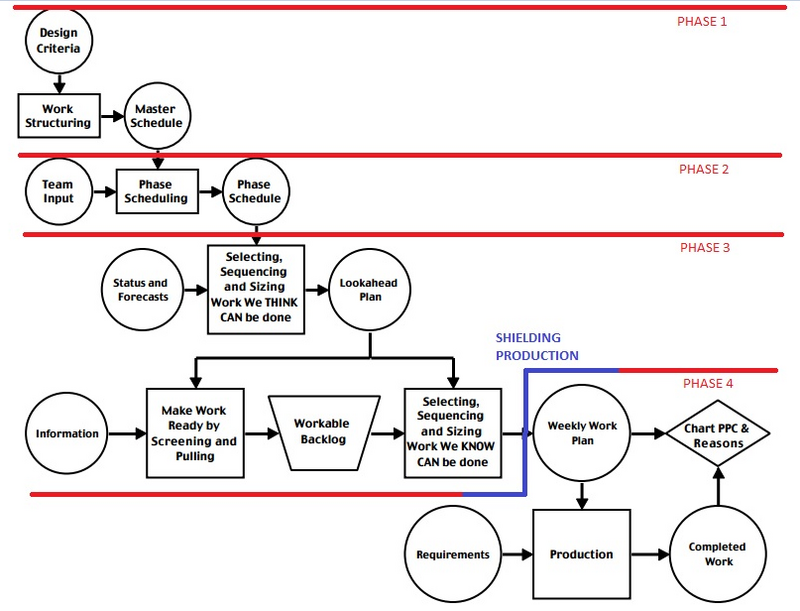
The shielding production, shown in Figure 2, is an important part of the LPS tool. It “shields” the weekly work plan from uncertainty by only letting tasks of good quality through to the weekly plan. Tasks that do not fulfill quality requirements go back to preparation. By doing this, weekly plans get more reliable and the work flow increases [6].
To use the LPS system, simple paper tickets are usually used and they are put up on a wall table where they are visible to everyone in the project. It is possible to use Excel forms and other computer programs but it is better to use them only for support and focus more on the simple paper ticket format. The next sub-chapters about the four phases will explain the method based on the paper ticket format.
Master Schedule
The master schedule is made from design premises that support the customer’s goal. The project is divided into big and important phases that are ranked in chronological order based on their internal connection [5]. The master schedule is usually done by using the critical path method and it shows major milestones and determines the overall project time [7]. It also helps with identifying what tasks have long delivery time that can affect the production. The main purpose of the master schedule is therefore to show that the contractor has the ability to finish the project on time. Production and management at the work place are not part of the master schedule, which makes it important to make a more detailed project plan[5]. That is done in phase 2.
Phase Schedule
Phase schedule, along with the look ahead plan (phase 3), works like a bridge between the master schedule and the weekly work plan. It affects daily management and production and it makes it possible to determine if the managers are performing the right work in order to reach the project’s goal[8]. In order to do the phase schedule right, those who do the work have to come together, collaborate, and plan the work. The work is planned backwards from a milestone in the master schedule. By pulling the work like that, more tasks become visible to the managers and ordering of them gets more efficient. Managers inform how they will perform the work, how long it will take and what resources they need in order to finish the task. This plan is often called pull plan, because the managers are pulling the work[7]. Making of the phase schedule/pull plan should be done at least 6 weeks before the actual work starts and even sooner if delivery times connected to the task are long[5].
To follow up on the project’s progress it is important to have pull plan meetings where the phase schedule is updated. All of those who are responsible for doing work connected to the milestone are supposed to attend the meeting. That is done so no critical tasks are forgotten. Figure 3 shows what information are given in the pull plan when using the paper ticket format. To begin with a crude time frame is put up and a milestone is made which the plan is supposed to be pulled from. The milestone tickets only have the name of the milestone and its finish date written on them. The planners break down the work needed to reach the milestone into phases. Each phase is written on a ticket that contains information about the name of the task to be done, number of days it takes to finish the task and what predecessors have to be done. The ticket is then put on the table in a chronological order. The tickets are in different colors depending on what project group is responsible for the task. The tasks are then connected depending on their predecessors, either by writing them on the tickets or drawing lines between them.
Lookahead Plan
As mentioned above, the lookahead plan is the other important part of the bridge that connects the master schedule and the weekly work plan. The role of the lookahead plan is to take a closer look at the tasks planned for the next couple of weeks so everything will be planned and ready when the production starts. This plan usually looks ahead for the next 6 weeks but it is essential to adjust the time as needed for each task. The phase schedule is often not detailed enough and therefore in the lookahead plan, tasks are broken down into smaller subtasks that are daily units suitable for the weekly work plan[5]. Figure 4 shows an example of how the lookahead plan is put up using the paper ticket format.
The subtasks are screened to make sure that everything is or will be ready when the work starts. e.g. the design has to be done, resources have to be available, predecessors have to be done, the work area has to ready for work with enough men power on site as well as all terms of the contract have to be fulfilled[5]. If it appears that one or more factor will prevent the task from starting on time, the factor is placed on the constraint log. The constraint log is supposed to solve constraints in a systematic way to ensure a steady production by making someone responsible for solving the constraint in time[4].
Another important part of the lookahead plan is to make detailed plans about how the work should be done in terms of safety, environment and quality issues[5]. So when a task is put on the lookahead plan, it has to be checked if this detailed plan exists. If not, then a first-run study has to be made by a cross functional team and those who do the work. The first-run study is based on the PCDA-method, a lean management tool, which is about going through four steps when performing work: planning, doing, checking and acting[4].
When tasks have passed the screening they are put on the workable backlog. There they are available for the managers to decide when to move them from the workable backlog to the weekly work plan[4].
Weekly Work Plan
The weekly work plan is the last and most detailed plan in the LPS system. It is the production plan that drives the production and is often called the commitment plan where the employees promise to perform a specific task on a specific day and place[7]. It is a list of tasks that are planned to do in a given week and shows how tasks in different parts of the project are connected. Figure 5 shows how a weekly work plan can look like using the paper ticket format for a 6 day work week.
The weekly work plan for the oncoming week is made on weekly production meetings. When all groups have made their individual plan, the whole plan is screened where the sequence of tasks is checked and changes are made if needed. Then the group has to promise that they will do what says on the plan and the meeting is not dismissed until all groups agree that the plan is achievable. Managers do have permission to do small changes to the plan before the end of the week as long as they inform all groups[5].
Dailly Stand-Up Meetings
Daily stand-up meetings were not part of the LPS tool when it was first introduced in 2000. But when the tool developed more it became a part of the tool and is now considered as important as other parts. The meetings should not be longer than 15 minutes and all managers are required to show up. The purpose of these meetings is to follow up on the weekly work plan and the production. The managers inform others about what was done the day before and what they will do today[9]. The meeting is often used to discuss safety matters and other issues that need to be solved in order to keep the production going.
Measurement of Performance
A big part of the LPS tool is to measure performance and examine what actually happened in terms of the weekly work plan. That is done in order to see how successful the plan was so it is possible to improve it. The performance measurement system used is called Percent Plan Complete (PPC) and it is the number of finished tasks divided by the number of tasks planned for the given week. The period of the PPC measurements is usually a week[5].
A task is not considered finished in the PPC measurement until it is completely done and ready for the next group to take over[5]. Tasks that are put in the weekly work plan from the workable backlog after the plan has been “locked” do not count in the PPC calculations. These are the most common rules but in fact there is no one correct way to measure PPC [4]. Therefore it is important that managers agree from the beginning how the measurements should be done and keep it the same during the whole project.
The PPC measurement indicates how reliable the managers are in delivering what they promised. It is not a direct measurement of productivity or progress but it is a good indicator[4]. Like mentioned above, the pull plan shows the total time of each task and what resources are needed to finish them. Therefore it is obvious if managers repeatedly get a low PPC that they are not producing what they promised in the pull plan making and will not reach the milestones in time with the resources available.
The goal is not to have the PPC ratio 100% but to create a working environment that supports learning and continuous improvements. Managers should seek for a PPC around 75-90%[9]. On this clearance, resources available are fully being used and problems arise so it is possible to learn from them and improve work processes in the project. A higher PPC indicates though that managers are doing more of good and well defined work with the resources they have and that of course leads to higher productivity and more efficient progress in the project based on the pull plan[4].
All tasks that are not completed are analysed separately. The managers have to give reasons for why the tasks were not completed, called reasons for non-completion. Examples of reasons for non-completion are:
- predecessor not done
- change in design premises
- work area not ready
- resources not available
- unforeseen circumstances.
After the managers have announced the reasons for con-completion a root cause analysis has to be made for all of them. This is done to make sure that the given reason is actually the reason that was responsible for delaying the task. The root cause analysis is supposed to find the real reason so it is possible to learn from the mistakes and prevent it from delaying other tasks in the future. Accumulated statistics of the reasons for non-completion indicate where improvements are most needed in order to improve processes, increase work flow and reduce waste[5].
Framework for Implementing the Last Planner System
The framework presented in this article comes from Hamzeh and Bergstrom. It is based on experience and research from other implementation of the LPS tool in construction projects. They found out that the most common barriers in implementing the LPS tool were lack of leadership, resistance to change and poor implementation planning. Their framework makes the implementation plan take more consideration to philosophical and social matters since the implementation process can be lingering and owners, top managers and all others are required to commit to the process.
- Get support from the project’s owner and top management of the construction organisation.
- Have a cross-functional group that is responsible for reaching the goal of the implementation.
- Evaluate and map the planning process to detect barriers and valuable step.
- Develop a go-to process.
- Challenges and benefits connected to the implementation have to be identified.
- The cross-functional team trains the future last planners and teaches them to use the LPS tool.
- Evaluate achievements made during the implementation and create a positive team experience.[7]
Benefits and Challenges in Implementation of the LPS Tool
By the year 2013, around 200 case studies had been made about implementation of the LPS system in construction projects all over the world. Fernandez-Solis and his companions selected 26 of these cases in order to study the benefits and challenges of LPS implementation. These 26 cases were picked because it was thought that they gave a good transection of different projects and overview of the LPS system.
The results for the benefits can be seen in Table 1 where the percentage show how many of the 26 projects considered it a benefit. It is important to keep in mind that it is not possible to measure all the benefits with numbers. When that is the case the benefits have been revealed with other methods, e.g. emotions and experience about the implementation[10].
Number | Benefit | Percentage |
---|---|---|
1 | Increased work flow reliability | 35% |
2 | Improved supply chain integration | 12% |
3 | Reduced project delivery or production time | 15% |
4 | Improved communication among project participants | 12% |
5 | Less firefighting or fewer day-to-day problems | 12% |
6 | Improvement in quality of work practice at construction site | 8% |
7 | Enhancement of managerial practices in construction projects | 8% |
8 | Knowledge expansion and learning among projects teams | 8% |
9 | Reduced stress levels on construction sites | 8% |
Other resources state that implementation of the LPS tool increase safety on the project site and help with managing costs since it gives a better perspective over the project’s progress[9].
Even though there are a lot of benefits that come with implementation of the LPS tool there are also a lot of challenges that need to be addressed. Results for the challenges can be seen in Table 2. It contains a short description of the challenge and a percentage of how often they were mentioned as a reason in the 26 case studies[10]. It is interesting to see that most of the challenges are connected to the users and managers but not the tool’s structure.
Number | Challenge | Percentage |
---|---|---|
1 | Organizational inertia or resistance to change or "This is how I've always done it" attitude | 62% |
2 | Lack of commitment to LPS implementation or negative attitude towards new systems | 46% |
3 | Lack of human capital: lack of understanding of new systems, difficulty in making quality assignments, or lack of skills, training, and experience | 50% |
4 | Lack of leadership or failure in management commitment or non-supportive organisational climate | 27% |
5 | Lack of stakeholder support | 19% |
6 | Lack of empowerment of field management or lengthy approval procedure from client and top management | 19% |
7 | Poor use of information generated during implementation of LPS | 15% |
8 | Contracting and legal issues or structure | 12% |
9 | Partial or late implementation of LPS | 12% |
10 | Bad team chemistry or lack of collaboration | 8% |
11 | Bad work ethics and cultural issues | 8% |
12 | Short term vision | 8% |
13 | Misinterpretation of PPC indicator | 8% |
Conclusion
As mentioned in the chapter above the most common challenges in implementing the LPS tool are lack of training, resistance to change, lack of leadership and human capital. This makes it clear that the problems are not connected to the structure of the tool itself but more to human factors. Therefore the framework presented in this article is suitable to use when implementing LPS since it seeks to get all managers and planners to understand and accept how the LPS tool works during the implementation.
Annotated Bibliography
Alarcon, L. (1997). Lean Construction. Rotterdam, Netherlands: A.A.Balkema.
- This book summarises the new and evolving conceptualisation of lean construction by collecting the work developed by members of The International Group of Lean Construction (IGLC). The members have different backgrounds, both from industry and academia. The result is a challenging exchange of ideas and experiences which include stories of success and failure.
Merschbrock, C. (2009). Lean Production Construction – Prospects for the Icelandic Construction Industry**. Reykjavík: Reykjavík University.
- A master thesis that seeks to identify the prospects and applicability of lean construction techniques at site level construction processes in the Icelandic construction industry.
Ballard, G. (2000). The Last Planner System of Production Control. Birmingham: The University of Birmingham.
- A doctor thesis that proposes a control system, the Last Planner System that had previously been successively applied to firms with direct responsibility for production management, e.g. speciality contractors. This theses extended the application through numbers of case studies. There were two questions that drove the research: “What can be done by way of tools provided and improved implementation of the Last Planner System of production control to increase plan reliability above the 70% PPC level?” and “How/Can Last Planner be successfully applied to increase plan reliability during design processes?”
Howell, G. A. (2002). A Guide to the Last PlannerTM for Costruction Foreman and Supervisors. Arlington, VA: Lean Construction Institute.
- This article serves as a guide for foremen and supervisors in construction organisations and explains both the operation of the planning system and the Last Planner’s role in it.
Hamzeh, F., & Bergstrom, E. (2010). The Lean Transformation: A Framework for Successful Implementation of the Last Planner System in Construction. Fort Collins, Colorado: Colorado State University.
- This reports discusses challenges and failures due to implementation of the LPS tool in three construction projects. It also provides a framework for implementing LPS in construction projects based on the research previously made. Then the implementation guidelines are tested on an ongoing construction project.
Fernandez-Solis, J., Porwal, V., Lavy, S., Shafaat, A., Rybkowski, Z., Son, K., and Lagoo, N. (2013). Survey of Motivations, Benefits, and Implementation Challenges of Last Planner System Users. J. Constr. Eng. Manage., 354-360.
- This article discusses the challenges and benefits of choosing LPS as a management tool. 26 cases studies on implementation of the LPS are deeply analysed in order to find the main challenges and benefits of the implementation.
References
- ↑ 1.0 1.1 [3] Aziz, R. F., & Hafez, S. M. (2013). Applying Lean Thinking in Construction and Performance Improvement. Alexandria Engineering Journal, 52, 679-695
- ↑ Alarcon, L. (1997). Lean Construction. Rotterdam, Netherlands: A.A.Balkema
- ↑ Merschbrock, C. (2009). Lean Production Construction – Prospects for the Icelandic Construction Industry. Reykjavík: Reykjavík University
- ↑ 4.0 4.1 4.2 4.3 4.4 4.5 4.6 Ballard, G. (2000). The Last Planner System of Production Control. Birmingham: The University of Birmingham
- ↑ 5.00 5.01 5.02 5.03 5.04 5.05 5.06 5.07 5.08 5.09 5.10 5.11 Howell, G. A. (2002). A Guide to the Last PlannerTM for Costruction Foreman and Supervisors. Arlington, VA: Lean Construction Institute
- ↑ Ballard, G., & Howoll, G. (1998). Shielding Production: An Essential Step in Production Control. Journal of Construction Management, 124(1), 11-17
- ↑ 7.0 7.1 7.2 7.3 Hamzeh, F., & Bergstrom, E. (2010). The Lean Transformation: A Framework for Successful Implementation of the Last Planner System in Construction. Fort Collins, Colorado: Colorado State University
- ↑ Ballard, G., & Howell, G. A. (2004). An Update on the Last Planner System. LCI
- ↑ 9.0 9.1 9.2 Mossman, A. (2014). Last planner: 5+1 crucial and collaborative conversations for predictable design and construction delivery. Stroud, UK: The Change Business Ltd.
- ↑ 10.0 10.1 10.2 10.3 Fernandez-Solis, J., Porwal, V., Lavy, S., Shafaat, A., Rybkowski, Z., Son, K., and Lagoo, N. (2013). Survey of Motivations, Benefits, and Implementation Challenges of Last Planner System Users. J. Constr. Eng. Manage., 354-360