Quality Control and Safety During Construction
Summary
Construction sites has through the years been subjected to injuries, accidents and faults. Budgets and deadlines are not kept, because of inadequate planning, errors, and poorly executed work. To satisfy customers requirements and to emphasise the importance of security, construction firms are now dedicating increasingly amounts of resources to prevent this. Political and private initiatives have made quality control a separate field in construction. [1][2]
This article will look at how quality control is used, the benefits and values of it and which supporting activities are used. The Quality Control concept is wide and are used in many areas and industries. Thus, the article will mainly focus on the overall basics of the Quality Control and discuss the tools directed at the construction industry. The article will first present some of the very basic consepts before describing some tools commonly used, like, Quality Plans, Cause and Effect Diaagrams, Check Sheets and Cost of Quality. Finally the article will discuss the limitations of the Quality Control.
Contents |
Definition: Quality Control
Quality Control is often associated with Quality Assurance (QA) and Quality Management Systems (QMS). They all correlate and depend on each other all thought there are different definitions. The American Society of Quality have made the following definitions of the terms:[3]
Quality Assurance is: “All the planned and systematic activities implemented within the quality system that can be demonstrated to provide confidence that a product or service will fulfil requirements for quality.”
Quality Control is: “The operational techniques and activities used to fulfil requirements for quality.”
Thus, the difference between them is mainly that the QA is everything involving the QC such as documentation, planning and the supporting activities around QC, while QC is the actual controlling part. Together QA and QC are parts of the QMS. The concept of Total Quality Control (TQC) emphazises the use of the tree to provide the best possible quality in every part of the company. [4]
Background
Until the mid-20th century the conventional way to make sure products were up to standards was with post-production controls, where the defect products would be repaired or thrown away. After the second world war companies started to rethink the idea as factories and production became more efficient and the demand bigger. Toyota introduced the Toyota Production System which later influenced the Lean-philosophy. In the 50’s the Demin-circle was introduced by W. Edwards Deming and is considered the origin of the total quality management (TQM). In the end of the 60’s the term Quality management systems arises. This was the first time where they would look at the entire process of making a product, not just the production in itself. The management and the service provided to the customers would be taken into account just as the quality of the product. [5]
Plan - Do - Check - Act
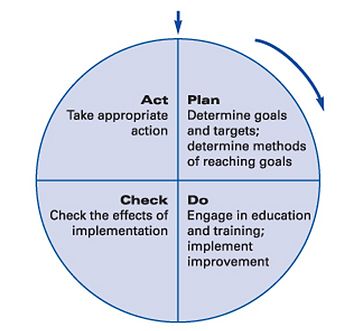
One of the most basic ideas of the QC and especially the TMC is the theory behind Plan - Do - Chech - Act (PDCA). It is based on the Deming Circle introduced by W. Edwards Deming in the 1950's. The concept has influenced the construction industry and many others since. PDCA is based on four parts, each shown in figure 1.
- Plan: The first step of the PDCA is the planning part. At this level the company will create an overview of the project and use the information they got in combination with previous experience they have acquired. Planning implementation of new methods and tools is a sentral part to the PDCA.
- Do: This is the execution of the production or the construction. With on-going supervision of the quality process the results of the planning will be used to provide the best possible quality for the customer. Keep in mind, keeping timelimits, costs and safety regulations is just as important as the actual product delivered. At this point it is important for every part project team are alligned and keep improving on every level of the organization.
- Check: Evaluating the initiatives and meausers implemented is important to keep improving a business. Do they improve the quality provided and does it justify the cost to accomplish the wanted quality. The evalutation of the progress should be a consistent process
- Act:: Once the results are evaluated, actions will be made to perfect the strategies. Auditing the information acquired to implement the knowledge in the upcomming projects and the continous PDCA circle is the intention. At this stage the adjustements are taking into account the information created during the first stages of the PDCA, and will be used as the circle starts over again.
The most crucial aspect of the PDCA is the continious evaluation of the performed work. Every time a process is done the company will have to chech the quality and document deviations. Necessary steps will be taken to meet required standards. The documentation will be used in future projects to provide a confidence that errors will not reappear.
The practical use of the PDCA is many, but mostly it is the idea that has influence other teqnicues and tools, some of them will be discussed during this article.
https://advisera.com/9001academy/knowledgebase/plan-do-check-act-in-the-iso-9001-standard/
https://www.lean.org/lexicon/plan-do-check-act
ISO 9001:2015
The concept of the QMS was originally based on assembly line productions, where there would be identical products produced repeatedly. Transferrin this into the construction industry, where the nature of each project would be totally different was a bigger challenge. One of the strongest initiatives to help this along was made by the International Organization for Standardization (ISO). They developed standards for implementing QC in the industry. The most commonly used is the ISO 9001:2015, which is also the only one amongst the ISO Standards which can be certified to. It is not required to certify, but there are more then one million companies wolrdwide with certification.[7]
Acquiering an ISO 9001 certification has become a way to prove the company's credibility, and in some industries it is even legally mandated to optain one. The ISO 9001 standard uses several tools and ideas in their standards to provide their users with the following benefits:
- Organize processes
- Improve the efficiency of processes
- Continually improve
Performing the Quality Control
What differs the modern QC from the traditional is the supporting activities alongside the project, but also before and after. Thus, many of the tools and methods are used prior to the actual construction.
In the initial phase of the project, planning is important to utilize the benefits of QC. Identifying the potential issues and making a strategy is one of the first steps in QC. There are different tools to use for the planning, e.g. Benchmarking, Flowcharting, Cost-to-benefit Analysis or Cause and Effect Diagrams. Using these brings predictability to the project, using preious knowledge, overviews and analycis of the project to plan the QC to be as efficient as possible, thus applying the concept of PDCA.[8]
Quality Plan
ASQ defines Quility Plan(QP) like this:
"A quality plan is a document, or several documents, that together specify quality standards, practices, resources, specifications, and the sequence of activities relevant to a particular product, service, project, or contract."
Thus the intention of the QP is specifying the use of and which goals to achieve with the QC. As well as creating a guidance for the QC it will also create a verification for the customer who have to rely on the contractor to provide the required quality. The QP should integrate the overall goals and strategic plans in the organization to the individual project, to provide an ongoing progress. It concerns aspects from top organizational level to the lower levers where the actual QC on site is executed. The subsequent sections will all be a part of the information provided in the QP.[9]
Cost of Quality
When a company is working with QC it is important to look at what is called Cost of Quality(COQ). The intetion with this tool is to look at the difference in cost between a project with failures and the costs of a project that runs according to plan with no deveations or failures. Thus, the goal is to eliminate all actions and processes that do not add value or improve the quality of the project. This is also one of the most basic ideas of the Lean philosophy which is trending in the construction industry today. It has also been an important part of the production industry since the mid 20th century. The COQ encourages all parties to reach towards a "zero-default-attitude". Second it is a way to measure the effectivenes of the Quality management. Does the implemented strategies work and is the QC good enough to fully utilize the value of their product.
Adding increased quality to a product traditionally adds more expences too, increasing the cost. To provide the added quality without the extra costs the COQ is divided into four parameters to classify the costs:
-External Failure Cost
-Internal Failure Cost
-Inspection (appraisal) Cost
-Prevention Cost
Identefying the sources to the costs will help distributing the resources to where they are most valuable. Thus improveing the effieciency of the quality management and also the areas where QC will give the geatest benefit. In the end, intentionally, the increased quality will not give extra costs. [10] <Torill Evy Thune, Kvalitetssikring og internkontroll i bygg og anlegg, Opplag 4(2017), Byggnæringens forlag</ref>
Cause and Effect Diagram
The Cause and Effect Diagram is also called The Fishbone Diagram or the Ishikawa Diagram. First the method addresses a problem. The intention is to find the causes and effects of the current problem. The processes affecting the problem are categorized and for each category the potential causes are listed. Visualized in figure 2, the typical setup for a Fishbone is shown. Usually the diagram is drawn on a whiteboard while the team members will discuss the situation and try to come up with a solution together.
https://qualitycontrolarticles.wordpress.com/2011/09/19/cause-and-effect-diagrams/
https://www.smartdraw.com/cause-and-effect/
http://asq.org/learn-about-quality/cause-analysis-tools/overview/fishbone.html
Basic Quality Control
Check Sheets
One of the most common ways to perform QC is by Check Sheets also referred to as Checklists. They give directions about what to control and how to do it. Using the construction of a concrete wall as an example. Typically parameters can be e.g. placement, height, reinforcement, formworks etc. The sheets are created and adapted to each individual project. All controlled areas will be documented and stored for later auditing. The controls are directed towards areas where the companies know faults occur, often a result of the risk assessment prior to the project start. The Check Sheets is a combination of preventive and corrective QC. It is also considered one of the most basic and simple ways of QC, with only small amounts of planning required. On the other hand processing the information acquired from the Check Sheets requires a sufficient amount of work. Using the knowledge gained from the controls are important in future work.[11] [12] [13]
Limitations
To keep the progress in a company, reaching towards their goals, QC can be a good measure. However, QC has to be used correctly. As many of the different sections in the article has discussed, handeling the information acquired is very important. If the company cannot take avantage of their new knowledge and transfer this to future projects, the developent will not continue and the QC is not fully utilized. The modern form of QC is yet very dependent on the evalutation and planning, thus emphasises the importance of handeling it correctly.
Communicaton is important in any company, especially when it comes to meeting their customers. Defining what is good quality and what is not, can be essential to the success of a project. If the company's perception of good quality do not fit the customers requirements for quality, the QC would be worthless. It is therefore important for all parties to communicate what their expertations are beforehand to avoid any dissagreements. Communicating these standards withing the company is equally important.
A third limitation is the costs of QC. Using extended QC with the accompanying methods and tools can be very expencive. If company spend more money and time on the QC then they make up for in failures the implementation will just act against its purpose. Before implementing the different tools and methods there should be done researh by the company to decide the benefits of the QC. After all, the company has to make money.
Having systems and methods to provide a good QC would in many cases be benefitial for the company. However, the idea that quality is important has to be implemented in the mindset of every employee in the company. Just following standards like the ISO 9001 or other tools without the understanding of why they are used does not engage in progress. Everyone involved in the process has to be commited and reach for their common goals.
Annotated Bibliography
References
- ↑ Arbeidstilsynet, http://www.arbeidstilsynet.no/artikkel.html?tid=250636, access 20.09.17
- ↑ Project Management Institute, The High Cost of Low Performance How will you improve business results?, http://www.pmi.org/-/media/pmi/documents/public/pdf/learning/thought-leadership/pulse/pulse-of-the-profession-2016.pdf access: 19.09.17
- ↑ American Society of Quality,http://asq.org/learn-about-quality/quality-assurance-quality-control/overview/overview.html, access: 22.09.17
- ↑ Chris Hendrickson, (2000), Project Management for Construction Fundamental Concepts for Owners, Engineers, Architects and Builders, Department of Civil and Environmental Engineering, Carnegie Mellon University, Pittsburgh
- ↑ [1], American Society of Quality
- ↑ https://www.lean.org/lexicon/plan-do-check-act
- ↑ [2], International Organization for Standards, uploaded 21.09.17
- ↑ [3], uploaded 26.09.17
- ↑ http://asq.org/learn-about-quality/quality-plans/, American Society for Quality, access 27.09.17
- ↑ American Socciety of Quality, http://asq.org/learn-about-quality/cost-of-quality/overview/overview.html, access: 29.09.17
- ↑ http://www.niskolen.no/pil/Medlem/Kurs/Dokumentasjonogkvalitet/data/downloads/10_dokumentasjon-og-kvalitetssikring.pdf, uploaded 16.09.17
- ↑ http://asq.org/learn-about-quality/data-collection-analysis-tools/overview/check-sheet.html
- ↑ https://www.intouch-quality.com/blog/quality-control-inspection-checklists-and-how-to-use-them