Lean in Project Management
Developed by Lea Greiling
The article handles the topic of Lean Management within Project Management with a focus on the Relay Racer theory. As Lean has been in important in Manufacturing processes since Taiichi Ohno developed the Toyota Production System, it has been applied to more than just production. Lean nowadays is applied throughout all departments in a company in order to eliminate as much waste as possible and thus increase profits.
First the thinking behind Lean will be explained. Afterwards the subject of Lean Project Management will be introduced by giving an overview of the idea, key principles, waste types and where Lean affects the process and knowledge areas of Project Management. Lean Project Management will further be described by looking at Lawrence Leach’s “8 Principles for Success”. It incorporates the standards of the PMI while giving guidance on where to focus when being lean and setting up a Lean Project. The article then focuses on the Relay Racer Theory which is crucial for eliminating waste within Lean Project Management such as wrong understood requirements and approval delays. Finally, the applicability and limitations of the theory will be discussed.
Contents |
Lean thinking
Taiichi Ohno who developed the Toyota Production System is considered the founder of Lean manufacturing.[1] He was the first one to consistently and thoroughly eliminate waste and thus accelerate production efficiency. Lean manufacturing relies on 5 key principles which are:[1]
- Identify and define value;
- Identify and map the value stream;
- Create Flow;
- Establish Pull;
- Pursuit perfection.
Within these principles the focus lies on eliminating waste. The different types of waste, called Muda in Japanese, which can occur were defined by Womack and Jones[2]:
- Defects in products;
- Overproduction of items no one wants;
- Inventory waiting to be processed;
- Unneeded processing;
- Unnecessary transport of goods;
- People waiting for input to work on;
- Design of goods and services that do not satisfy customer needs.
Lean manufacturing’s core issue is to identify and reduce waste and become more effective and efficient. Cusumano and Nobeoka[3] start to extend Lean ideas to multiple project systems. Projects should be linked strategically through product portfolio planning, technologically through the design of common core components and organizationally through overlapping the responsibilities of project managers which is the beginning of thinking about Lean Project Management.
Lean Project Management
Lean tries to improve established methods and standards in project management. There is no one way definition of how a project can be made Lean but the existing methods are a support to develop Lean Project Management. [4]
Lean Project Management is trying to optimize the process by reducing the non-value adding activities and optimizing the value adding ones. [5] Usually there are more non-value adding activities than value adding, this moves the focus from the optimization of the value generation to the reduction of waste. Looking at the key principles of Lean, waste is usually defined as waiting time. Waiting in project based productions or enterprises does not primarily have to be a disadvantage. Buffers, for example, were found to rather support Project Management than to hold up the project. [5]
Reusch[4] expanded the 5 key principles of Lean and adjusted them to Lean Project Management. The key principles for Lean Project Management were identified as:
- Specify what creates value from the customer´s perspective;
- Identify all the steps along the process chain;
- Make those processes flow;
- Identify waste – based upon needs and expectations of customers;
- Eliminate waste – based upon needs and expectations of customers;
- Make only what is pulled by the customer;
- Strive for perfection by continually removing wastes;
- Amplify learning;
- Make decisions at the right time;
- Empower the team;
- build integrity;
- See the whole.
Furthermore, Reusch identified examples of waste in projects in relation to the categories of waste introduced above. The results are shown below.
Waste type in projects | Cause |
---|---|
Lack of effectiveness in projects | Ignoring available products services standards, ignoring innovations |
Lack of efficiency | Communication problems, lack of information, ignoring information, missing skills, weak organization (waste of time in meetings, needless meetings), collecting redundant or useless information, not considering standards |
Waiting | Communication problems, lack of information, lack of resources |
Over-production in projects | Wrong definition of requirements, overlapping and not harmonized processes |
Rework | Wrong specifications, missing competencies, insufficient or not effective control |
Motion | Lack of resources |
Over processing | Overburden of regulations |
Inventory related waste | Planning errors, lack of resources |
Transport related waste | Planning errors, lack of resources |
These waste types have to be identified alongside the process of Project Management. The standard process of project management is defined by PMI (Project Management Institute) in their Project Management Body of Knowledge (PMBOK).[6] The process is:
- Initiating
- Planning
- Execution
- Closing
- Monitoring and Controlling
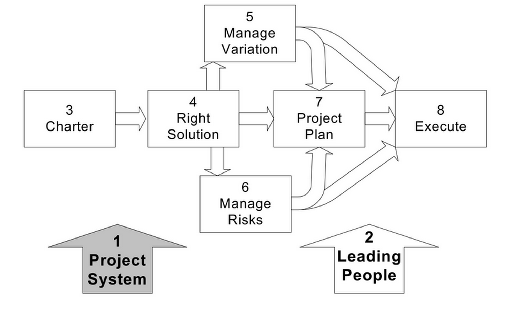
The PMI has also defined nine knowledge areas for project management which are crucial for a successful delivery of a project. These knowledge areas include Integration, Scope, Time, Cost, Quality, Human resources, Communication, Risk, and Procurement. Looking at the process and knowledge areas, Lean Project Management has to focus on eliminating waste within these areas. Leach[1] narrowed this thinking down by saying that “each task is a process”. Each process requires inputs and outputs. The outputs then go to the successor and the sum of them create the project result. Waste has to be eliminated in the entire process, in each task and among the interfaces of input and output.
As Lean Project Management is a broad topic and different interpretations for “How to make a project more lean” exist, this article focuses on Lean Project Management identified by Lawrence Leach who adapted PMI standards and Lean Thinking to Project Management in order to develop eight principles which can support a project leader or organization on its way to eliminating waste.
Lean Project Management by Leach
Leach[1] introduced 8 principles which can lead to successful project results by using lean tools and critical chain management. (see Figure 1) A short overview of each step will be given below.
Principle 1: Project System
The project system is defined as the interaction of People, Process and Product that the project will produce. The system defines how the project will be executed and whether it will be successful. Further, each project is different. In order to act Lean, one should not rely on standards but adjust to the environment. The project leader has to identify the system, the inter-relationships and its sub-processes and evaluate what is essential in order to be successful.
The next step is to make sure to create a critical chain with resource leveling and using buffers. Resource leveling means that one person only works at one job and not on three jobs at the same time while other people have to wait for that person to finish. Figure 2 shows how waste can be reduced through resource leveling and buffers. With the critical path (left) Larry is assigned 3 tasks at the same time. With the critical chain (right) he is assigned 3 tasks but in different time slots. With the critical chain the project ends in the beginning of March and has a buffer until the end of March. With the critical path there are no buffers and the project only ends at the end of March. (More information on critical chain: Critical Chain Project Management to cope with uncertainty)
Leach shows that these tools allow projects to not having to finish all tasks on time to finish a project on time, that sometimes one can finish sooner by starting later and that adding buffers can reduce total project duration and cost. All of this can only be accomplished if one knows the system and the interrelationships.
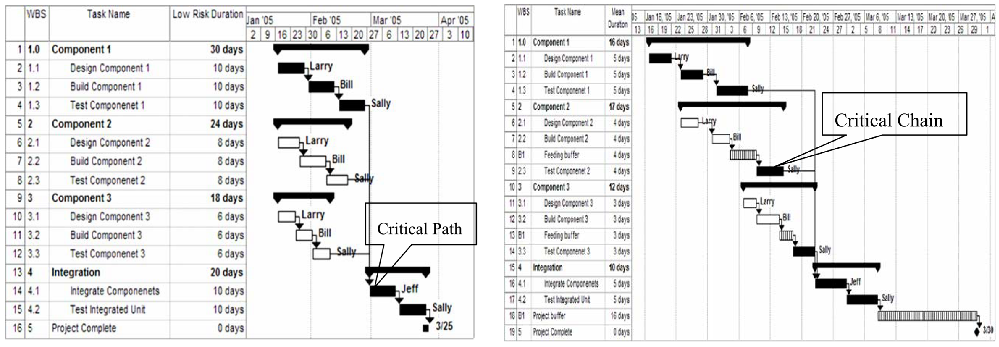
Principle 2: Leading People
Stakeholder Analysis and Management is one of the most critical and important issues for success. One has to remember that project team members are also stakeholders and one of the most important ones. Leaders who are able to keep stakeholders supporting the success of the project will confront less obstacles. Furthermore, an effective team leader guides the team through predictable team development phases, uses win/win problem solving methods to smoothen conflicts, allocates responsibilities to each member to support performance and matches skills with tasks.
Principle 3: Charter
The project charter helps to achieve the project goal through financial, customer, process or employee results. It established a project vision. The charter allows the team to create a project plan. This process should be used to identify and resolve issues and actions that will and could arise during the project. Not all issues can be resolved right in the beginning but knowing about them and appointing one person to one issue will lead to faster resolution in the future.
Principle 4: Right Solution
One of the waste types in Lean are products or services that do not meet the customer’s needs. Requirements thus are the basis for the design of the solution. The idea what success looks like by stakeholders has to be incorporated in the modelling of the solution. Leach proposes to develop more than one solution and in the end select the one that reflects the stakeholders needs the most. Tools that support the team on the way of executing the solution practically are the Work Breakdown Structure (WBS), Milestone Sequence Chart and work packages.
Principle 5: Manage Variation
Two different kind of variations are introduced. The common-cause variation and the special-cause variation. Common-cause variation repeatedly occur within a project whereas special-cause variations are usually caused by factors outside the system and are rather not predictable. Special-cause variations are hard to predict but common-cause variations exist in every project. Common-cause variations can be minimized by using buffers. There are four different buffers which can be applied in order to manage variation.
The project buffer: This is a time buffer at the end of a project and assures that there in general is “room left” when something goes wrong.
The feeding buffer: These are time buffers in order to fill the time between a non-critical part of a project with a critical one. (see principle 1)
Capacity constraint buffer: This is a resource capacity buffer which makes sure that the resource that is occupied the most during a project gets appointed a buffer in order to handle common-cause variations.
Cost buffer: This is a monetary buffer which gives room for cost variations within the project.
Principle 6: Manage Risk
Risk management is the tool to manage special-cause variations in a project. Risk management has to be an ongoing process in order to identify variations, therefore the project leader and the team members have to take action for risk management in order for it to be effective. The ongoing process of risk management involves identification of risks, analysis, monitoring and controlling. Risk Management not only is one of the nine Knowledge areas of the PMBOK but through the actions of monitoring and controlling, actively contributes the fifth process step of project management “Monitoring and Controlling”.
Principle 7: Project Plan
The Project Plan is defined as how the project is executed, monitored and controlled, and closed.[6] Tools for creating the plan include the project vision, a Work Breakdown Structure, key milestone sequence chart, action list, work package assumptions, risks. In Lean Project Management the focus has to be put on resource leveling and task assignment. A smooth project plan can be assured when the total number of resources demanded in one time slot never exceed the total number of resources available. Task assignment should be managed by at least assigning one resource to one task and matching the resource skills with the needed skills for the task.
Principle 8: Execute
The execution of a Lean Project Management takes place efficient, effective, straight forward, without loops, pulled by the customer and executed to the needs of the customer. In order to assure these the relay race theory or metaphor can be used. It will be explained in the next section.
The relay race theory
The relay race and Lean Project Management
This theory or metaphor is important for lean project management as it can describes the most Lean way of how dependent tasks should follow each other. It enables efficient hand overs of tasks and makes predictable schedules possible. Looking at the relay race we can link the actions of the runners to actions within projects. In a project one ideally would want to have:[7] [1]
- early collaboration to ensure understanding of requirements of the customer (practicing the handover of the baton);
- a period of collaboration at the end of a task/project to ensure that the task team and the customer are on the same page (matching the speed with the second runner);
- a well-executed transaction process and passing on the results as soon as the task is done (placing the baton into the other runner’s hand);
- an agreement of the customer that the task has been fulfilled successfully (making sure that the runner has the baton firmly in his hands;
- a start of the task as soon as the input is available (the runner would never stop once he holds the baton in his hands);
- to work 100% on the task in order to avoid delays (the runners are fully focused trying to win the race)
Every meeting, every support task, every funded activity should have a tangible output. In project management, for example, decisions are outputs of meetings. If a task does not have an outcome, it wouldn’t contribute to the project and thus be waste. Further, every task has a customer and this customer does not have to be external but can also be internal (department or a colleague).
Looking at the relay racer in Lean Project Management one wants to link dependent tasks as lean as possible without creating waste. This method is a pull method and can be compared to Toyotas Kanban system where products are “pulled” through the production through Kanban cards which tell the predecessor the exact quantity of items that are needed.[7]
The traditional working method is just task dependency. Here Task B is dependent on Task A. When Task A is finished, the results or output is handed over to Task B.
In Lean Project Management one tries to link the tasks. Just as in a Pull Production, tasks are dependable on each other. Task B is the customer of Task A. The customer determines when the previous task is complete, the customer is involved at an early stage and there has to be an early definition of the content and format of the deliverable.
By doing this the project leader will be able to eliminate waste types like overshoot and undershoot of information/content, delays and errors in project. This method can be used for internal projects, for external projects, for program management and portfolio management.
Application of Relay Race Theory
The implementation of lean linkages between dependent tasks involves the definition of requirements and deliverables, successful handovers of outputs and the elimination of approval delays. [7]
Define Deliverables and requirements
Sometimes it is not easy if for example an internal customer doesn’t know yet what his requirements are or what the deliverable should look like. In order to support the process some actions can be taken to refine the understanding of the output.
- Use deliverables from earlier projects to inspire needs;
- Produce prototypes and ask for feedback;
- Make sure that everyone uses the same or compatible information technology. For example Word and Latex.
This approach is less wasteful than into-the-blue hand-offs. Furthermore, does this early involvement of customers, internal or external, lead to enhancement of relationships and team building. Unused prototypes can be used for other project to inspire needs and requirements for projects. Even realizing what is not a requirement is constructive since this is yet an elimination of waste.
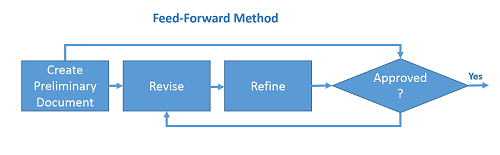
Successful hand-off
Hand-offs usually fail because requirements are not met and iterations have to be initiated. The closer one gets to the completion of a task, the more urgent it becomes to involve the customer for approval. This leads to the ability to still adjust to changes and decrease the time of the final approval by only approving the last changes that have been made since the first approval. The feed-forward method [7] can be used for this task. Before the project is completed a preliminary document of approval is send to the customer. The unapproved steps can then be revised, refined and in the end only the changes have to be approved (see Figure 3).
Eliminate Approval delays
Approval delays can be subject to waiting time for example because of a missing signature. The project leader has to make sure that not too many obligatory signatures exist. Furthermore, internal deliverables should rely on trust and discipline and not have to be approved by hierarchical authorities. Deadlines for feedback allow the task keeper to move the output to the next customer.
Application of Lean Project Management
Application of the relay racer theory has been discussed in the chapter above. Now follows the general applicability of Lean Project Management.
As can be seen from the application of the relay race theory, knowledge and involvement are crucial for a successful output. Reusch[4] found out that Project Management Guides should not be treated as the plus ultra. For a Lean Management, standards are not the solution but the access to knowledge is more important. Knowledge can reduce waste and supports stakeholder management. A high level of transparency leads to higher opportunities to reduce waste.
It is important to not hold up information to be able to take correcting steps. Riis [8] states that a Lean Project can only be efficient if cooperative attitudes are created within the group and people are willing to learn from experience. By succeeding in this, there are more opportunities to identify wasteful activities and eliminate them.
Riis[8] summed up focus areas for Lean Project Management well by stating that one needs to focus on
- leadership rather than management,
- the nature of uncertainty and the definition of attention areas rather than standard plans,
- organizational learning than standard procedures,
- adjustment of success criteria,
- development of project culture in the organization.
Limitations
As the application refers to relying not so much on standards and believing in transparency and knowledge, these are also limiting factors. Organizations rely on standards in order to be faster by time through the repetition of these standards. To be very open-minded and share a lot of information is also challenging for some departments. The limits for being Lean within a project thus lie in the ability of all stakeholders to share information and get involved. This has to be efficiently managed through the project leader (Principle 2 of Leach).
Furthermore, Lean has been widely accepted in Production but organizations have been negligent to adopt this thinking to technical-administrative activities.[8] Creating a common knowledge about what is Lean and what purpose it is, is important in order to implement Lean Project Management.
The article shows that Lean Project Management is a wide topic and that waste can be created during the execution of Projects. Leach’s 8 principles show how important preparation is and the relay race theory reveals the essentials of early customer involvement and information sharing.
Annotated Bibliography
Leach, L. P. (2005): This was the main book used for the article. It gives an overview of the Lean topic and relates it then to the 8 principles which Leach has developed. It is a good introduction into the topic and has a high focus on the Critical Chain Management. It leads the practitioner to understanding what he or she has to do in order to start a Lean project.
Reusch, P. J. A., Reusch, P. (2013):The article by Reusch is quite short, but summarizes the topic of Lean Project Management very well. It is a good starting point for someone who quickly wants to get an overview of the main issues like processes, waste reduction, potential areas for improvement, future perspectives. The article has to be read including the articles of the bibliography since many key words are not explained and the author only refers to other articles.
Mascitelli, R. (2002): This book focuses more on the enterprise and how to set up the organization in a more project and lean oriented way. Mascitelli introduces 12 methods which help the practitioner to create a Lean environment for projects by giving situation based examples. He also gives guidance on how to measure each of these steps. The book closes with a thorough chapter about how to implement Lean Project Management within an enterprise.
References
- ↑ 1.0 1.1 1.2 1.3 1.4 1.5 1.6 Leach, L. P. (2005) “Lean Project Management: Eight Principles for Success. Combining Critical Chain Project Management [CCPM] and Lean tools to accelerate project results” Boise, Idaho.
- ↑ Womak, J., Jones, D. (1996) “Lean thinking: Banish waste and create wealth in your corporation” New York. Simon and Schuster.
- ↑ Cusumano, Nobeoka (1998) “Thinking beyond Lean” New York, The Free Press.
- ↑ 4.0 4.1 4.2 Reusch, P. J. A., Reusch, P. (2013) “How to develop Lean Project Management?” The 7th IEEE International Conference on Intelligent Data Acquisition and Advanced Systems. Berlin, Germany.
- ↑ 5.0 5.1 Bertelsen, S. „Bridging the gaps – towards a comprehensive understanding of Lean Construction” The international Group for Lean Production.
- ↑ 6.0 6.1 PMI. (2004) „A guide to the project Management Body of Knowledge, Third Edition.” Newton Square, PA, PMI.
- ↑ 7.0 7.1 7.2 7.3 7.4 Mascitelli, R. (2002) “Building a Project-Driven Enterprise: How to Slash Waste and Boost Profits Through Lean Project Management” California, Technology Perspectives.
- ↑ 8.0 8.1 8.2 Riis, J. O. (1993) “Lean Project Management” International Journal of Project Management. Vol 11, Issue 1, Feburary.