Failure Mode and Effects Analysis in Various Project Stages
Magnusheld (Talk | contribs) |
Magnusheld (Talk | contribs) |
||
Line 1: | Line 1: | ||
− | Defects, downtime, injuries and delays can be extremely costly and often directly interfere with a company’s objective of delivering quality and reliability<ref name="Numberone">'''D. H Stamatis, 2003, 2. Edition, "''Failure Mode and Effect Analysis – FMEA from theory to execution''", ASQ Quality Press.''' - Step-by-step approach for implementing FMEA | + | Defects, downtime, injuries and delays can be extremely costly and often directly interfere with a company’s objective of delivering quality and reliability<ref name="Numberone">'''D. H Stamatis, 2003, 2. Edition, "''Failure Mode and Effect Analysis – FMEA from theory to execution''", ASQ Quality Press.''' - Step-by-step approach for implementing FMEA and overview of phases the method is applicable to. Also includes ISO references and Six Sigma practices.</ref>,. So how can these events be prevented from occurring? |
Extensive testing in the later phases of product development project could for instance be a preventive measure. However discovering the faults at this stage can be very costly and mean even further delays. Instead, it is ideal to take preventive measures, which can be achieved through applying the risk management tool “Failure Modes and Effects Analysis (FMEA)”. FMEA is a systematic step-by-step approach for identifying, analyzing and preventing product and process failures. The tool is often applied in the early stages of a project, but can be used throughout in different variations. | Extensive testing in the later phases of product development project could for instance be a preventive measure. However discovering the faults at this stage can be very costly and mean even further delays. Instead, it is ideal to take preventive measures, which can be achieved through applying the risk management tool “Failure Modes and Effects Analysis (FMEA)”. FMEA is a systematic step-by-step approach for identifying, analyzing and preventing product and process failures. The tool is often applied in the early stages of a project, but can be used throughout in different variations. | ||
Line 6: | Line 6: | ||
In this article, a “product” is often referred to as a “system” consisting of sub-systems and components | In this article, a “product” is often referred to as a “system” consisting of sub-systems and components | ||
− | |||
= FMEA = | = FMEA = | ||
Line 12: | Line 11: | ||
== Definition == | == Definition == | ||
− | FMEA is a qualitative tool that investigates how a product or process might fail (failure mode) in delivering its intended function and the consequences of this. The tool applies with the standards of Qualitative Risk Analysis defined by the PMBOK guide, which shortly can be summed up as a prioritization of risks for further investigation by assessing their probability of occurrence and severity | + | FMEA is a qualitative tool that investigates how a product or process might fail (failure mode) in delivering its intended function and the consequences of this. The tool applies with the standards of Qualitative Risk Analysis defined by the PMBOK guide, which shortly can be summed up as a prioritization of risks for further investigation by assessing their probability of occurrence and severity<ref name="Numbertwo">'''Project Management Institute, 2013, "''Project Management Body of Knowledge''", 5th edition''' - identifies that subset of the project management body of knowledge that is generally recognized as good practice. “Good practice” means there is general agreement that the application of the knowledge, skills, tools, and techniques can enhance the chances of success over many projects.</ref>. In practice the tools objective and compliance with the standards can be formulated as: |
*Identification and understanding of failure modes and their causes, and the effects of failure on the system or end users, for a given product or process. | *Identification and understanding of failure modes and their causes, and the effects of failure on the system or end users, for a given product or process. | ||
Line 18: | Line 17: | ||
*Implementation of corrective actions for the most critical failure modes along with evaluation after implementation. | *Implementation of corrective actions for the most critical failure modes along with evaluation after implementation. | ||
− | FMEA can be categorized as a proactive risk reduction tool that after initiation becomes a dynamic factor of improvement. This I due to the iterative nature of risks identification where new risks may evolve or existing risks becomes revealed as the project advances through its lifecycle. | + | FMEA can be categorized as a proactive risk reduction tool that after initiation becomes a dynamic factor of improvement. This I due to the iterative nature of risks identification where new risks may evolve or existing risks becomes revealed as the project advances through its lifecycle. <ref name="Numbertwo"></ref>. |
− | The motive for implementing risk identification followed by risk reduction derives from the objective of changing characteristics of the system, without significantly increasing cost. This ability to do so is highest at the projects start and decreases at the project progresses. | + | The motive for implementing risk identification followed by risk reduction derives from the objective of changing characteristics of the system, without significantly increasing cost. This ability to do so is highest at the projects start and decreases at the project progresses<ref name="Numbertwo"></ref>. A general rule of thumb for the phenomenom is the Factor of 10 rule, which states that changing characteristics of a product in a development project multiplies by a factor 10 for each time the project progresses in to a new phase. The factor of 10 rule I illustrated in the figure below.<ref name="Numberthree"></ref> |
+ | |||
+ | |||
+ | |||
+ | [[Image:factor10.jpg|frame|center|Figure 1: Factor of 10 rule<ref name="Numberthree">'''C.S. Carlson, 2012, ''"Effective FMEAs: Achieving Safe, Reliable, and Economical Products and Processes Using Failure Mode and Effects Analysis"'', John Wiley & Sons, Inc.''' | ||
+ | - procedures for doing FMEAs and how to successfully apply them in various phases</ref>.]] | ||
+ | |||
+ | == The Tool == | ||
+ | FMEA is usually created within a spreadsheet, which enables the user to get an overview over complex systems with multiple components being inspected. | ||
+ | |||
+ | [[Image:fmeasheet.png|frame|left|Figure 2: FMEA spreadsheet example<ref name="Numberthree"></ref>]] | ||
+ | |||
+ | |||
+ | |||
+ | |||
+ | |||
+ | |||
+ | |||
+ | |||
+ | |||
+ | |||
+ | |||
+ | |||
+ | |||
+ | |||
+ | |||
+ | |||
+ | |||
+ | |||
+ | |||
+ | |||
+ | |||
+ | |||
+ | |||
+ | |||
+ | |||
+ | |||
+ | The spreadsheet example consist of 11 descriptive categories that defines the FMEA investigation. These are outlined below:<ref name="Numberthree"></ref> | ||
− | + | '''1. Item''' | |
+ | The system, subsystem, component or process step chosen for investigation. | ||
+ | '''2. Function''' | ||
+ | The intended function of the system, subsystem, component or process. | ||
+ | '''3. Potential failure modes and identifying these''' | ||
+ | Failure modes are the possible ways the intended function of the system, subsystem, component or process fails. These are the backbone of the FMEA tool and identifying these lay the foundation for a successful and broad inspection of how a process or product might fail. When identifying these the necessity for a cross-functional team is heavily underlined since stakeholders have different interpretations and views of possible failure modes. Therefore selecting a team with a broad field of experience relevant to the subject is crucial for the success of the FMEA. This could for instance be designers, production workers, end users, suppliers etc. As a baseline for the identification of failure modes Murphy’s law is introduced as a guiding statement: “Whatever can go wrong, will eventually go wrong”. | ||
+ | Once the team are assembled, the brainstorming of potential failure modes can be initiated.Different variations of brainstorming can be applied in order to explore as many failure modes as possible. | ||
+ | '''4. Potential effect(s) of failure''' | ||
+ | Consequence of the failure on the system, subsystem, component or process level. | ||
+ | '''5. Severity (S)''' | ||
+ | Ranking of the most serious effect for a given failure mode. The severity is often scaled from 1 to 10, where 10 is the most severe. The ranking can be a product of an assessment based on experience or supported by data. | ||
+ | '''6. Potential Cause(s) of failure''' | ||
+ | Specific reason(s) for the failure modes to occur (root causes). | ||
+ | '''7. Occurrence (O)''' | ||
+ | Describes the likelihood of a failure mode occurring and is often scaled from 1 to 10, where 10 is the most likely. It is important to use data (if available) to validate the occurrence ranking. This could be from current design controls. | ||
+ | '''8. Current design controls (prevention/detection)''' | ||
+ | Methods or actions already in place to prevent or detect failure modes. These are linked to the ranking of the occurrence (prevention) and the ranking of detection. | ||
+ | '''9. Detection (D)''' | ||
+ | Ranking scale of the possibility of detecting the cause of failure modes. Is often scaled from 1 to 10, where 10 is the least likely. It is important to use data (if available) to validate the detection ranking. This could be from current design controls. | ||
+ | '''10. RPN (Risk Priority Number)''' | ||
+ | Ranking of failure modes according to severity, occurrence and detection. The RPN value is found by multiplying these three values. RPN = S x O x D | ||
+ | '''11. Recommended actions''' | ||
+ | Task recommended by the FMEA team with the objective of reducing or eliminating the risk associated with the failure modes. | ||
+ | ==Execution== | ||
+ | In order to conduct an FMEA effectively it is highly recommended to follow a systematic step-by-step approach. D. H Stamatis recommends an eight-step method consisting of the following steps<ref name="Numberone"></ref>: | ||
+ | = Annotated references = | ||
<references/> | <references/> |
Revision as of 08:48, 19 February 2018
Defects, downtime, injuries and delays can be extremely costly and often directly interfere with a company’s objective of delivering quality and reliability[1],. So how can these events be prevented from occurring?
Extensive testing in the later phases of product development project could for instance be a preventive measure. However discovering the faults at this stage can be very costly and mean even further delays. Instead, it is ideal to take preventive measures, which can be achieved through applying the risk management tool “Failure Modes and Effects Analysis (FMEA)”. FMEA is a systematic step-by-step approach for identifying, analyzing and preventing product and process failures. The tool is often applied in the early stages of a project, but can be used throughout in different variations.
This article aims to inform the reader on how to facilitate FMEA, how it can add value in different phases of a product development process and its limitations.
In this article, a “product” is often referred to as a “system” consisting of sub-systems and components
Contents |
FMEA
Before discussing the use of FMEA in different project phases, the general concept of the tool and its application will be outlined.
Definition
FMEA is a qualitative tool that investigates how a product or process might fail (failure mode) in delivering its intended function and the consequences of this. The tool applies with the standards of Qualitative Risk Analysis defined by the PMBOK guide, which shortly can be summed up as a prioritization of risks for further investigation by assessing their probability of occurrence and severity[2]. In practice the tools objective and compliance with the standards can be formulated as:
- Identification and understanding of failure modes and their causes, and the effects of failure on the system or end users, for a given product or process.
- Risk assessment associated with the identified failure modes, effects, and causes, and prioritizing of issues for corrective actions.
- Implementation of corrective actions for the most critical failure modes along with evaluation after implementation.
FMEA can be categorized as a proactive risk reduction tool that after initiation becomes a dynamic factor of improvement. This I due to the iterative nature of risks identification where new risks may evolve or existing risks becomes revealed as the project advances through its lifecycle. [2]. The motive for implementing risk identification followed by risk reduction derives from the objective of changing characteristics of the system, without significantly increasing cost. This ability to do so is highest at the projects start and decreases at the project progresses[2]. A general rule of thumb for the phenomenom is the Factor of 10 rule, which states that changing characteristics of a product in a development project multiplies by a factor 10 for each time the project progresses in to a new phase. The factor of 10 rule I illustrated in the figure below.[3]
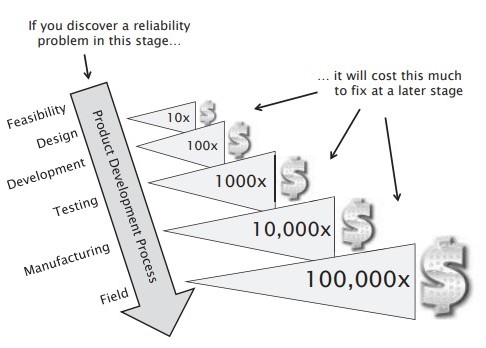
The Tool
FMEA is usually created within a spreadsheet, which enables the user to get an overview over complex systems with multiple components being inspected.
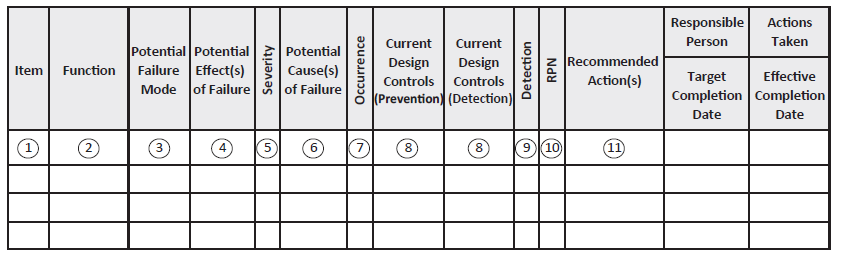
The spreadsheet example consist of 11 descriptive categories that defines the FMEA investigation. These are outlined below:[3]
1. Item The system, subsystem, component or process step chosen for investigation.
2. Function The intended function of the system, subsystem, component or process.
3. Potential failure modes and identifying these Failure modes are the possible ways the intended function of the system, subsystem, component or process fails. These are the backbone of the FMEA tool and identifying these lay the foundation for a successful and broad inspection of how a process or product might fail. When identifying these the necessity for a cross-functional team is heavily underlined since stakeholders have different interpretations and views of possible failure modes. Therefore selecting a team with a broad field of experience relevant to the subject is crucial for the success of the FMEA. This could for instance be designers, production workers, end users, suppliers etc. As a baseline for the identification of failure modes Murphy’s law is introduced as a guiding statement: “Whatever can go wrong, will eventually go wrong”. Once the team are assembled, the brainstorming of potential failure modes can be initiated.Different variations of brainstorming can be applied in order to explore as many failure modes as possible.
4. Potential effect(s) of failure Consequence of the failure on the system, subsystem, component or process level.
5. Severity (S) Ranking of the most serious effect for a given failure mode. The severity is often scaled from 1 to 10, where 10 is the most severe. The ranking can be a product of an assessment based on experience or supported by data.
6. Potential Cause(s) of failure Specific reason(s) for the failure modes to occur (root causes).
7. Occurrence (O) Describes the likelihood of a failure mode occurring and is often scaled from 1 to 10, where 10 is the most likely. It is important to use data (if available) to validate the occurrence ranking. This could be from current design controls.
8. Current design controls (prevention/detection) Methods or actions already in place to prevent or detect failure modes. These are linked to the ranking of the occurrence (prevention) and the ranking of detection.
9. Detection (D) Ranking scale of the possibility of detecting the cause of failure modes. Is often scaled from 1 to 10, where 10 is the least likely. It is important to use data (if available) to validate the detection ranking. This could be from current design controls.
10. RPN (Risk Priority Number) Ranking of failure modes according to severity, occurrence and detection. The RPN value is found by multiplying these three values. RPN = S x O x D
11. Recommended actions Task recommended by the FMEA team with the objective of reducing or eliminating the risk associated with the failure modes.
Execution
In order to conduct an FMEA effectively it is highly recommended to follow a systematic step-by-step approach. D. H Stamatis recommends an eight-step method consisting of the following steps[1]:
Annotated references
- ↑ 1.0 1.1 D. H Stamatis, 2003, 2. Edition, "Failure Mode and Effect Analysis – FMEA from theory to execution", ASQ Quality Press. - Step-by-step approach for implementing FMEA and overview of phases the method is applicable to. Also includes ISO references and Six Sigma practices.
- ↑ 2.0 2.1 2.2 Project Management Institute, 2013, "Project Management Body of Knowledge", 5th edition - identifies that subset of the project management body of knowledge that is generally recognized as good practice. “Good practice” means there is general agreement that the application of the knowledge, skills, tools, and techniques can enhance the chances of success over many projects.
- ↑ 3.0 3.1 3.2 3.3 C.S. Carlson, 2012, "Effective FMEAs: Achieving Safe, Reliable, and Economical Products and Processes Using Failure Mode and Effects Analysis", John Wiley & Sons, Inc. - procedures for doing FMEAs and how to successfully apply them in various phases