Increasing performance with Value Stream Management
Contents |
Abstract
This article describes Value Stream Management and how it can help to optimization of supply chain network and hereby ensuring a high level of customer satisfaction. In continuation of Value Stream Management, a definition of Value Stream and a description of the tools Value Stream Storyboard and Value Stream Mapping (VSM) will be introduced. The article will dive into Value Stream management approaches of delivering value and streamlining the workflow. This will include a walkthrough of the theory behind Value Stream and the lean tool of VSM. Along the article, Lean philosophy will be descripted to some degree. The application of Value Stream Management will be discussed, and a guidance of the tools Value Stream Storyboard and VSM will be given. Lastly the article will deliver a reflection on the challenges which Value Stream Management faces, when it comes to developing and maximizing value for both company and business. This reflection will also touch on the benefits and disadvantage of value stream management. The article should in some sense give an understanding of how to use Value Stream Management and also apply it, so it is easier to get products out the door. [1] [2] [3]
Big Idea
Introduction to value stream management
To maintain high levels of customer satisfaction it is important to prevent, address or solve collaboration and communication issues and also eliminating complications across the value chain can be a significant effort, especially at the supply chain interfaces where flow of information or physical goods are exchanged. So where does Value Stream Management come into the picture and why? The following quote states todays view on the value Stream Management approach: “Value stream management is that next step of engagement that looks at how to more effectively drive ongoing continuous improvement and drive more customer value”. Value Stream Management is a management approach which focuses on delivering value from customer request to customer delivery. The approach consists of measuring and improving flow as well as eliminating waste in each step along the way.
Because Value Stream Management relates to driving more customer value, the approach has to be put in the context of Lean (insert link about Lean). Big parts of Value Stream management come from Lean thinking and practices and therefor leans on the five principles of Lean transformation as seen in figure x.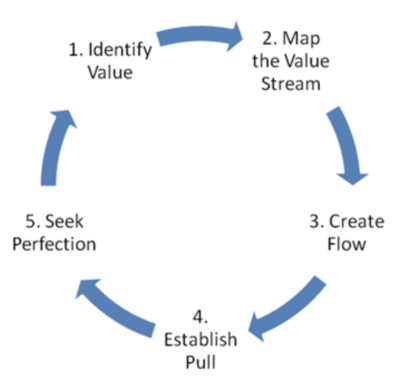
Value Stream Management facilitates the transformation of an organization into a lean enterprise by providing a framework to ensure the effective functioning of Lean implementation teams. This does not mean that Value Stream Management is a way of telling people to do their job more effectively, but an approach that allows people to plan and implement improvements that makes it easier to meet customer demands.
Value Stream Management serves not only as a management tool, but also as a planning process to make improvements that enable a company to adopt a Lean approach.
Value Stream Management consist of Eight steps:
- 1. Commit to Lean
- 2. Choose the Value Stream
- 3. Learn about Lean
- 4. Map the Current State
- 5. Identify Lean Metrics
- 6. Map the Future State
- 7. Create Kaizen Plans
- 8. Implement Kaizen Plans[5]
The application will dive into the eight steps of Value Stream Management.
Agile aspect – state of the art
Today ‘s modern businesses require a lot of agility due to for example digital transformation, higher business complexity and especially after Covid-19 more hybrid work. Throughout the crisis, innovative and adaptational thinking has accelerated. This means that organizations have to reconsider the processes, tools, and the people behind the business so they can remain competitive and also focus on high-value impactful work. This is where Value Stream Management comes into the picture. Focus on value stream management is essential when building bridge between agile practices and realizing agility in businesses. Also, value stream relates to the ongoing shift of focusing on value vs. economies of scale or cost, in that way, that you try to update and develop what gives value to the customer and hereby the business instead of trying to produce the highest quantity the cheapest way.
In addition, to better understand once value stream, Value Stream Management makes it possible for organizations to bridge silos and enable collaboration across company borders. This provides foundation for supply chain optimization and with the current digitalization it will impact cross-enterprise interfaces, through that giving more transparency as for information. [6] [7]
Definition of Value Stream
The term value stream originally come from Lean manufacturing and explain the flow of material and information to create value. Value is seen from the customers point of view and is measured in performance. A value stream is the set of activities or services an organization takes to add value to a customer or customer need. [8] The customer is willing to pay for this add-value. These value-added activities can be achieved by eliminating non-value-adding activities and then replacing them with value-adding activities.[9] In most organizations there are two primary value stream categories, which is operational value streams and development value streams. The operational value streams reflect the flow of the business and the core functions and provides an ongoing customer value as long as the company offers products and services. It is supported by the development value stream and forms the foundation of the effective measurement for objectives and key results. The development value stream creates and operates the systems and capabilities that enable operational value. It can also provide systems that interact with customers or internally facing systems. Then it helps operational value stream by improving systems and capabilities. Both operational – and development value streams helps to create value, whether it is an external customer or an internal stakeholder.[10] Lastly, it is worth understanding customer demand, when about to map the current state or map the future state. By analyzing customer demand, it makes it easier to choose the target value stream.[11]
Value Stream Management tools
With Value Stream Management comes visual management tools, where the most essential ones are Storyboards and Value Stream Mapping. These tools enable you to identify specific activities occurring along a value stream for a product.
The Value Stream Management Storyboard
The use of storyboards is an important reason why Value Stream Management has a such a big impact on achieving Lean effectiveness. A Value Stream Management storyboard consist of a visual representation of a value stream, in terms of a Value Stream Map. The visual representation outlines the complete process from start to finish. Typically, it is holding key information’s for planning Lean implementation, consisting of details about the flow of materials, information and the activities used to create or deliver value, which is shown in figure X. (Insert figure of full storyboard and corporate it into the text) With visual management it is ensured that everyone understands the enterprise’s goals and that all necessary information to enable people to work as efficiently as possible is available. Storyboards are daily used by Toyota Production System and enables people to see and understand the “big picture”, which furthermore contributes to the overall strategy.[12]
The main purpose of the storyboard is to facilitate communication and collaboration among teams and align goals and objectives and drive continuous improvement. Some other attributes of Value Stream Management Storyboard are that it provides a clear and concise communication between management and teams as for the lean expectations as well as material and information flow. It contributes to team recognition and ownership through the hole value stream, also making it possible for management to review and incorporate reporting into the storyboard. Lastly, the storyboard reflect changes and updates hereby provides a good form of visual communication.[13] Through the application it will be stated when information is being added to the storyboard.
Value Stream Mapping
The visual representation of the value stream in the storyboard is made from the value stream mapping and is probably the most used as well as the most powerful tool within Value Stream Management. Figure x is an example of a value stream map, where the different types of information – and material flow is shown.[14] (Reference of figure) The tool is used to visualize, analyze, and improve all steps from customer request to customer delivery. It is mainly known for mapping the flow of materials and information from supplier to customer. Additionally, it is also used to highlighting areas of waste, inefficiency, and bottlenecks within the value stream, taking a clear picture of opportunities for improvement, and delivering value from start to finish. With our previous knowledge about the definition of value, some parts of the value stream may not always bring direct value to the customer when mapping a value stream, all though it will bring value to the final product or services provided. An example of this could be quality inspections, which the customer is not paying you for, but without these inspections of the final product or service, the quality standard might not meet their expectations. This will entail the customer to no longer buy products from you again.[15]
To create a Value Stream Map, require knowledge about the design and key figures used, such as the display of processes, information, inventory, suppliers etc. I will not go into a deeper explanation of how to create a Value Stream Map. See further information about creating a Value Stream Map here.[16]
Application
Many organizations find value stream management overly complex, but with the following steps explained in the application teams and managers can have a better foundation of how to establish a culture of continuous improvement. Also, getting a better understanding of managing value streams and leverage from it, hereby increasing the performance of the business.
The eight steps of Value Stream Mangement
Commit to Lean
When applying Value Stream Management, the first action is to commit to Lean in the entire organization, from management to all levels of the organization. With starting point in figure X, you want a worker pull system instead of a traditionally management push. This means employees are the ones pulling the resources and training, due to the motivation factor of improving the value stream, which they are the backbone of every day. Although, management guidance and support are needed for the overall commitment.
There are a few key activities top management should take in becoming lean. Top management should communicate the importance of meetings, pricing comparisons, sharing customer feedback, and establishing administrative teams.
To secure this you have to invest in the people. They are the experts of the organization and know how to improve the different parts of the value stream, so the management part required is to structure and encourage communication, as well as support their ideas for improvement. This way you also get buy-in and support from your employees.
Here we also get the first detail on the storyboard started with each team member’s name written in.[17]
Choose the value stream
With all the different value streams in an organization, you must identify and eliminate the non-value adding part of the value stream. As explained in the definition of value, the customer defines your value stream, so you have to select the product families that provides value. The selection can be made from two methods:
Product quantity analyses is used to identify the high-volume product that are the most critical to success of a business. The method makes it possible to optimize for example operations and supply chain to reduce costs.
Product-routing analysis addresses to the flow of a product and is used to identify the most efficient route of a product from start to finish. Here bottleneck and opportunities of improvement is identified.
The chosen product family enters the value stream box in the storyboard.[18]
Learn about Lean
Before going into the next steps of mapping both current and future state, it is important for everyone to improve their knowledge about Lean. A training plan for each member has to be established based on the required skills compared to the current skills. Hereafter make a schedule and evaluate on the effectiveness of the training. The training must consist of all the key concepts of Lean. The lean observations done by the team is added to the storyboard.
Map the current state
By value stream mapping the current state, you are to identify all the occurring activities in a product or family. To do so you must map the material – and information flows. Common measurements:
- The time it takes to go from product conception to launch
- The time it takes from raw materials to finished product shipping
- The time it takes from order placement to cash received
When mapping the current state, you are to highlight the areas of customer and internal pain and along that process create problem statements and findings of your root cause analysis. The details that need to be displayed on the map is the points which are to be improved, also referred to as Kaizen bursts.[19]
Once the core team agrees on the map incorporate it on the VSM storyboard for all to view.
Identify Lean Metrics
With the current state mapped you must now identify the metrics to help you form the future state map. Metrics’ will help people understand the impact of their efforts, when they plan the improvement, implementing them, checking results, and adjusting. See figure x of the PDCA metric, which can be used a useful tool to follow, when striving for continuous improvement and waste reduction. Your chose of metrics and the ones which suits your organization depends on the details of the situation. A few common metrics which can be helpful is total lead time, total cycle time, on-time delivery, days of inventory on hand etc.[20]
After doing the measurements and agreeing on the most valuable data it is transferred to the storyboard.
Map the Future State
In this step you are to identify the opportunities to design a value stream with less waste and hereby more efficient value stream. There are three stages to go through, when mapping the future state, all of them is a part of the lean training:
Customer demand, understanding what the customer want when it comes to quality, lead time and price. Flow, implementing a continuous flow in manufacturing, with the purpose of delivering the right product to the customer both internal and external, at the right time and in the right quantity. Leveling, distribute work to reduce inventory and enable customers to place smaller orders.
If you have difficulties with thinking creatively about transforming different parts of the business, here are some ways of thinking:
- Simplify – can you process improve, take out the waste?
- Eliminate – can you eliminate the need for the process in the first place
- Consolidate – can you merge some processes or the capacity that is delivering that?
- Automate – can technology support your delivery?
- Reallocate – should somebody else be doing this work? [21]
When these future improvements are agreed on, the future state map is incorporated in the storyboard, which also makes it a full storyboard, see figure X.
Create Kaizen Plans
To create continuous improvements for your plan, use the same stages as in the future state as planning sequence: customer demand, process flow and level production. If you follow these steps, it will be an effective and cost-efficient implementation. By following the kaizen plan, you must review the future state map and create a monthly kaizen plan. Here it is scheduled when implemented elements are to be accomplished in the future state map.
You complete the storyboard by adding the proposed monthly kaizen plan.[22]
Implement Kaizen Plans
With the review of the previous steps, you can now proceed to the implementations phase. Nevertheless, it is important to keep in mind that during the implementation, the kaizen activities will affect everyone who are involved with targeted value stream.
To wrap up the application of Value Stream Management, you must commit to Lean and its principles, use visual management to ensure everyone understand the goal of the organization and for people to work more effectively, make information easily accessible to them. The team will enter data on the storyboard, as well as drawing the value stream maps with the purpose of having a shared detailed document to show finished and planned implementations. Use the storyboard how you prefer it, then it will be most effectively.[23]
Limitations
Value Stream Management has its limitations or common pitfalls. Effective implementation of a value stream requires a systematic effort to adjust and improve the processes. However, some organizations have a hard time adopting or implementing value stream due to various reasons.
One thing can be upsetting the status quo. There will be a resistance to change, because of the concerns about what the change might reveal. The process of building a value stream can help you to uncover misaligned priorities, identify inefficiencies and getting insights to customer needs. This exercise can potentially disrupt status quo of a business and challenge its leaders’ understanding of their organization. In the end this might also lead to lack of buy-in from stakeholders, management, and employees.
There is also the resistance to change when it comes to work environment. Lean methodologies have the framework of in-person work and with the change in how we work after the pandemic, organizations must change to these new workplaces and its dynamics. It is worth considering, because it will have an effect on how value streams are mapped and managed. This means that the digital transformation is a limitation. It plays a big role when it comes to mapping the value stream, so members can align and collaborate no matter where they are working. [24]
Cite error:
<ref>
tags exist, but no <references/>
tag was found