Kanban in Project Management
*** work in progress - some sources are still missing and of course the list in the end, so no need to comment on this :) ***
Kanban(看板 signboard from Japanese) aims to provide visibility, highlight bottlenecks and improve communication and work flow throughout a project, a process or similar. The Kanban system was originally an inventory control system developed by Taiichi Ohno, an industrial engineer at Toyota. The vision then was that the system would reduce the waste (muda) in the production line and improve the manufacturing efficiency. Kanban is a flowcontrol system for pull-driven JIT (just-in-time) production, the upstream processing activities are triggered by the downstream demand signals[1][1]. The Kanban system is now, with some alterations, applied as an agile project management tool. It is argued that the system offers improved project visibility, product quality, team-motivation, communication and collaboration [2].
The basis of the Kansan system is to have a board with cards attached. Different parts of the board represent different stages of the development which all work items go through. The cards represent the different work items in the project, and move from left to right on the board. The board and the cards can be arranged and divided however the user would like. Nonetheless the main concept of Kanban is always the same, and can be summarized by these six points[2]:
- Limit WIP (work in process): The board is divided in parts, and each part can only have a pre defined number of work items, WIP limit, thus this don't need to be the same for every part. This is true for all parts except the “backlog” and “done” part, which is always unlimited
- Cards : Each work item is represented by a card (sticky note or similar)
- Flow: The work items on the board are moved from left to right between the different parts. The person performing the work, is also the one moving the card
- Team: The team working with the Kanban board agree on some rules for when the cards can be moved
- Kaizen (constant improvement)
- The team working with the Kanban board have to get together on a regular basis to analyze the flow, focusing on work items that are stuck on the board
- There is no Kanban police - and if you need to alter the board or break the rules that's ok, but inform the rest of your team
Kanban in Project Management
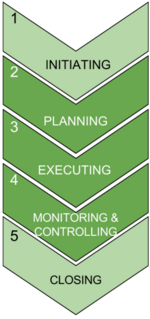
The goal of project management is to improve the total quality of project results. This include on time delivery, stakeholder satisfaction and financial results.[3] In otder to do so one have to poperly execute the five processes of project management, see figure 1.
The Kanban project management tool can help in regards of the planning, executing and monitoring and controlling aspect of project management by solving the questions stated below.
- How can workflow be visualized in real time?
- How can team members and stakeholders get a sense of understanding of the whole project?
- What is the bottleneck in the workflow of this project?
- How can we improve day-to-day openness in the project?
- How can a project be lean and agile at the same time?
How each of these questions is solved is explained throughout this article and subsequently summarized in the benefit section.
History
Kanban is now a popular system used by teams practicing agile and lean project work. In recent years Kanban has become a popular framework for managing software development teams, and is now often implemented to complement Scrum or other agile software development methods[4]. Kanban is considered to be a prominent and relatively new framework, it was first introduced (to this use) in the early 2000’s. Nonetheless the Kanban methodology dates back more than 50 years.
1953: Kanban was first implemented in the Toyota factory by Taiichi Ohno and can be summerised in these points[3]
- Inspired: by the grocery store model, the concept was that grocery stores was stoking just enough product to meet customers demand. This practice enables the inventory levels to match the customer pattern and therefore be at a minimum without affecting the customers in a negative manner. Thus the store can gain efficiency in inventory management by decreasing the amount of excess stock.
- Vision: to align Toyota's massive inventory with the actual consumption of materials.
- Communication: capacity levels at the different workstations on the factory floor would be communicated in real-time. Workers passed a card with capacity information between workstations.
- Re-stock: When the batch of materials used at one point in the production line was emptied, a card with this information was sent to the warehouse. Here it would be a new batch ready to be transported to the production line.
The Kanban framework for production lines is still very much used today, though it has been developed in line with the the technology to a faster and more agile version of the same system. Kanban was introduced as a project management tool for software development by Microsoft in 2004, now the workstations were replaced by parts of a Kanban board and the cards was replaced with sticky notes. Other than that, the concept, value and advantages remained the same [4]
Cite error:
<ref>
tags exist, but no <references/>
tag was found