Quality Gates in Project Management
(→Abstract) |
|||
(46 intermediate revisions by one user not shown) | |||
Line 1: | Line 1: | ||
[[File:5Ws.png| right |thumb|400px|Figure 1: 5Ws and 1H of Quality Gates (own figure)]] | [[File:5Ws.png| right |thumb|400px|Figure 1: 5Ws and 1H of Quality Gates (own figure)]] | ||
− | + | by Thore Uwe Aye (s202746) | |
== Abstract == | == Abstract == | ||
− | Projects are temporary | + | Projects are temporary, unique endeavors and require active management of their integration, scope, schedule, cost, quality, resources, and communication according to the Project Management Institute ''(PMI)''. <ref name="1-PMI"> Project Management Institute, Inc.. (2017). Guide to the Project Management Body of Knowledge (PMBOK® Guide) (6th Edition). Project Management Institute, Inc. (PMI). </ref> <br /> |
+ | |||
+ | One tool to control project management is the stage gate approach that divides projects into stages with gates and tracks their progress and success. In the 1990s a modification to focus on especially schedule, cost, and quality was established known as Quality Gates ''(QG)''. | ||
+ | A quality gate represents a checkpoint of predefined criteria set by the project manager to evaluate the current progress of a project. Herein the focus lies on the three aspects of time and cost, both resource-related and quality. After assessing the specified benchmarks and standards, an evaluation of passing or failing the gate is made. The case study representing practical findings from an Airbus production plant provides the reader with a tangible example how quality gates can successfully be implemented and managed. | ||
− | + | This article sets the quality gate model into the picture with the stage gates as another phase gate model and points out its differences, benefits, and limitations. One of the takeaways is that in the quality gate model more emphasis lies on the quality criteria,its control in project management and its lifecycles. Besides the article mentions how four main tenets set, assess, and complete gates and form the setup advisory for project managers which includes detailed gate decision governance. <ref name="2-PMI-Sym">Aaron, J. M., Bratta, C. P., & Smith, D. P. (1993). Achieving total project quality control using the quality gate method. In proceedings of the annual seminar symposium-project management institute (pp. 120-129). </ref> Furthermore, a brief overview of quality management tools and techniques which include TQM, EFQM and (Lean) Six Sigma is given to sort the quality gate model. | |
− | + | The article also explains the required steps a project manager needs to take in order to implement quality gates in projects together with the Quality Gate Process ''(QGP)'' and management in operative and conceptual levels. A proposal of applying the quality gates by segmenting projects into the three stages of front-end, middle, and back-end gates for different project stages is elaborated. <ref name="2-PMI-Sym"></ref> <ref name = "3-TUMBat">Schnell, J., & Reinhart, G. (2016). Quality management for battery production: a quality gate concept. Procedia CIRP, 57, 568-573.</ref> | |
− | + | Finally, in the section of limitations and challenges more examples from practice are evaluated and suggestions are made in terms of selecting projects for applications of quality gate models more carefully. Further only projects with considerable size and low uncertainty are found eligible for quality gate processes. | |
− | + | Last but not least this article focuses heavily on practical applicability precisely for projects and thus provides tips and tricks for practitioners. | |
− | + | The annotated bibliography outlines major literature that is relevant but also suggests papers, which provide profound insights to reader who can study quality gates more in-depth through this suggested literature. | |
− | + | ||
− | + | ||
− | + | ||
− | + | ||
== Keeping Projects on Track with Quality == | == Keeping Projects on Track with Quality == | ||
− | The technique of applying quality gates and their control process after each phase is a useful tool and is often applied by project managers or owners and process managers. | + | The technique of applying quality gates and their control process after each phase is a useful tool and is often applied by project managers or owners and process managers. It provides designing, embedding and checking quality criteria after the development of a project reaches a new phase, e.g. from developing an IT software to its deployment. Before deploying the software a gatekeeper, for instance the project manager, assesses whether the quality of the previous phase satisfies the quality gate criteria. The process of defining, embedding and checking quality criteria are underlying the entire project’s lifecycle.<br /> Quality gates reach from initiation of a project until its final closing after deployment. Most applications take place in industrial circumstances where development takes place, such as in new product development (NPD), production (manufacturing and assembly) and also very commonly in IT software development. Often quality gates are the chosen tool to assess these processes because it enables practitioners to gain control over the quality development, its status and the current project’s state of the art in terms of quality. This is done by defining the quality criteria in the initiation and planning of a project, setting milestones and gates assessing the set criteria along the way. |
=== Phase Gate Models === | === Phase Gate Models === | ||
Quality gates are a comparable form of the stage gate model and also other phase gate models. It is suggested to separate projects in terms of quality gates into the four different categories of ''planning, design, development'' and ''deployment''.<br /> | Quality gates are a comparable form of the stage gate model and also other phase gate models. It is suggested to separate projects in terms of quality gates into the four different categories of ''planning, design, development'' and ''deployment''.<br /> | ||
− | Also in the stage gate model projects are separated into phases because the outcome is often unknown and controlling can therefore take place after each phase. Setting gates after each phase, which must be passed before continuing to the next, allows control. Further, it enables early identification of potential risks and provides increased visibility. | + | Also in the stage gate model projects are separated into phases because the outcome is often unknown and controlling can therefore take place after each phase.<ref name="Cooper"> Cooper, R. G. (1990). Stage-gate systems: a new tool for managing new products. Business horizons, 33(3), 44-54. </ref> Setting gates after each phase, which must be passed before continuing to the next, allows control. Further, it enables early identification of potential risks and provides increased visibility. |
[[File:qualitygf.png| center|thumb|750px|Figure 2: Quality Gates after each Phase of a Project]] | [[File:qualitygf.png| center|thumb|750px|Figure 2: Quality Gates after each Phase of a Project]] | ||
− | According to PMI a project has the dimensions of integration, scope, schedule, cost, quality, resources, and communication and Cooper’s | + | According to PMI, a project has the dimensions of integration, scope, schedule, cost, quality, resources, and communication and Cooper’s stage gate model intends to include all aspects in its model.<ref name="Cooper"> </ref> |
− | Contrary, the Quality Gate model focuses specifically on the factors of time (schedule), cost and quality – all three of them are essential for a project’s quality outcome. In this way, it differs to the | + | Contrary, the Quality Gate model focuses specifically on the factors of time (schedule), cost and quality – all three of them are essential for a project’s quality outcome. In this way, it differs to the stage gate model. The gates are set timely independent and flexible, but in a sequential order – whereas its criteria to pass a gate are defined very specifically. More information about the stage gate model can be obtained by another DTU wiki called [[The Stage-Gate Model|The Stage-Gate Model]]. |
Quality gates as a project management tool have been established because practitioners felt that in our rapidly changing world and disrupting time there is less focus on quality due to a downside in order to increase time-to-market. | Quality gates as a project management tool have been established because practitioners felt that in our rapidly changing world and disrupting time there is less focus on quality due to a downside in order to increase time-to-market. | ||
− | Scholars therefore point out that “Quality gates […] are supposed to increase the confidence stakeholders have in a release” <ref name="QGCont"> | + | Scholars therefore point out that “Quality gates […] are supposed to increase the confidence stakeholders have in a release”. <ref name="QGCont">Schermann, G., Cito, J., Leitner, P., & Gall, H. C. (2016, May). Towards quality gates in continuous delivery and deployment. In 2016 IEEE 24th international conference on program comprehension (ICPC) (pp. 1-4). IEEE.</ref> It is one of the solutions to introduce more quality control in project management surroundings. |
=== Quality Management & Control === | === Quality Management & Control === | ||
[[File:2x2.png| right |thumb|250px|Figure 3: 2x2 Comparison Matrix of Project and Quality Management Tools (own figure)]] | [[File:2x2.png| right |thumb|250px|Figure 3: 2x2 Comparison Matrix of Project and Quality Management Tools (own figure)]] | ||
− | Quality management consists of four basic pillars, its planning, assurance, control and improvement <ref name="QGWWH"> | + | Quality management consists of four basic pillars, its planning, assurance, control and improvement. <ref name="QGWWH"> Rose, K. H. (2005). Project quality management: why, what and how.</ref> In project management, quality is of relevance in order to achieve the intended outcome and function of the endeavour. Already Cooper pointed out in his stage gate model in 1990 <ref name="Cooper">Cooper, Robert G. (1986). Winning at new products. Addison-Wesley.</ref> that many newly launched products lack quality inspection processes. |
To achieve control over quality management in projects several tools evolved over the years and gained publicity. | To achieve control over quality management in projects several tools evolved over the years and gained publicity. | ||
− | '''Total quality management (TQM):''' " | + | '''Total quality management (TQM):''' In one of the works of comparing quality management practices, Pfeifer describes TQM as "a management approach of an organisation centered on quality, based on the participation of all its members and aiming at long-term success through customer satisfaction and benefits to all members of the organisation and society." <ref name="QGMunich"> Pfeifer, T. (2002). Quality management. Strategies, methods, techniques, Hanser, München, Wien.</ref> TQM aims for establishing an organisational culture where quality is the main criteria for success and requires cultural implementation. More information on the topic can be found in the DTU wiki [[Total Quality Management|Total Quality Management]]. |
− | '''European Foundation for Quality Management (EFQM) model:''' “The EFQM Model is a globally-recognised management framework which allows organisations to achieve success by measuring where they are on the path towards transformation, helping them understand the gaps and possible solutions available, and empowering them to progress and significantly improve their organisation’s performance.” <ref name="EFQM"> | + | '''European Foundation for Quality Management (EFQM) model:''' According to the foundation itself they summarize its model as the following: “The EFQM Model is a globally-recognised management framework which allows organisations to achieve success by measuring where they are on the path towards transformation, helping them understand the gaps and possible solutions available, and empowering them to progress and significantly improve their organisation’s performance.” <ref name="EFQM"> European Foundation for Quality Management, Retrieved from : "https://www.efqm.org/index.php/efqm-model/" [Accessed: 28. February 2021]</ref> It helps to define purpose, create culture, forge strong leaders, transform organisation, foster agile practices, address unique organisational challenges, forecast the future. More information on the topic can be found in the DTU wiki under [[Quality assurance methods in project management|EFQM and the European Quality Award]]. |
− | '''(Lean) six sigma:''' The combination of the principles from lean principles/management and six sigma is called lean six sigma. Lean management focuses on continuous process improvement based on small, incremental changes with the overall goal to improve efficiency and quality. Together with six sigma it aims for improving processes and performance by narrowing resources and variations down to the minimum required. More information on the topic can be found in the DTU wiki under [[Lean 6 Sigma in project management|Lean Six Sigma]]. | + | '''(Lean) six sigma:''' The combination of the principles from lean principles/management and six sigma is called lean six sigma. Lean management focuses on continuous process improvement based on small, incremental changes with the overall goal to improve efficiency and quality. Together with six sigma it aims for improving processes and performance by narrowing resources and variations down to the minimum required.<ref name=" "> Arnheiter, E. D., & Maleyeff, J. (2005). The integration of lean management and Six Sigma. The TQM magazine. </ref> More information on the topic can be found in the DTU wiki under [[Lean 6 Sigma in project management|Lean Six Sigma]]. |
Compared to quality management tools quality gates focus on specific quality aspects at specific times, the gates, in contrast to non-stop iterative quality management perspectives. It sets and later assesses quality criteria and intervenes when errors occur in the project’s development. Thus, it becomes obvious that quality gates are rather different to prevalent and common quality management and control techniques. Using these argumentations project managers can justify its presence and application for endeavours where quality-heaviness is key. | Compared to quality management tools quality gates focus on specific quality aspects at specific times, the gates, in contrast to non-stop iterative quality management perspectives. It sets and later assesses quality criteria and intervenes when errors occur in the project’s development. Thus, it becomes obvious that quality gates are rather different to prevalent and common quality management and control techniques. Using these argumentations project managers can justify its presence and application for endeavours where quality-heaviness is key. | ||
Line 43: | Line 42: | ||
=== Airbus Case Study === | === Airbus Case Study === | ||
− | [[File:a350.jpg| right |thumb|150px|"A350 First Flight" by Matthieu Luna is licensed under CC BY-NC-ND 2.0 ]] | + | [[File:a350.jpg| right |thumb|150px|[https://www.flickr.com/photos/25859982@N07/9040956572 "A350 First Flight"] by [https://www.flickr.com/photos/25859982@N07 Matthieu Luna] is licensed under [https://creativecommons.org/licenses/by-nc-nd/2.0/?ref=ccsearch&atype=rich CC BY-NC-ND 2.0] ]] |
− | One major industrial player adopting the quality gate is Airbus. The multinational aerospace company incorporates quality gates approximately since 2015 and implements it as a quality management tool to handle and control the quality of supplier products. End-to-end ''(E2E)'' quality gates are nowadays an essential part of Airbus’ Quality Management System. <ref name=" "> | + | One major industrial player adopting the quality gate is Airbus. The multinational aerospace company incorporates quality gates approximately since 2015 and implements it as a quality management tool to handle and control the quality of supplier products. End-to-end ''(E2E)'' quality gates are nowadays an essential part of Airbus’ Quality Management System. <ref name="Airbus"> Sciannamea, I. (2017). Quality Gates. In Supply Chain Integration Challenges in Commercial Aerospace (pp. 193-207). Springer, Cham. </ref> |
− | Airbus implemented quality gates from the designs over parts up to a final aircraft and therefore considers them end-to-end gates. Every single time a project or product from a supplier is supposed to proceed to the next stage Airbus assesses the quality specifications and decides on the proceeding. They have implemented these gates because lack of quality concerns their Final Assembly Lines ''(FAL)'' and have found that these concerns especially arise from parts by external supplier. The quality requirements stated at the gates | + | Airbus implemented quality gates from the designs over parts up to a final aircraft and therefore considers them end-to-end gates. Every single time a project or product from a supplier is supposed to proceed to the next stage Airbus assesses the quality specifications and decides on the proceeding. They have implemented these gates because lack of quality concerns their Final Assembly Lines ''(FAL)'' and have found that these concerns especially arise from parts by external supplier. The quality requirements stated at the gates have even become part of their Customer Supplier Agreements and since then their supply chain efficiency improved since the amount of incomplete products decreased together with cost and visibility, cooperation and on-time delivery increased. Airbus and the supplier degree on targets and deliverables which they can measure, control and review at handover meetings. |
− | In particular one example turned into a success story and | + | In particular, one example turned into a success story and showcased the strength quality gates have. Airbus had one supplier who supplied their production facility in St. Nazaire who always lacked documentation when delivering parts that were also in poor quality. This supplier and his low quality led to required manual corrections by Airbus in their FAL. Thus, customer and supplier integrated end-to-end quality gates for these particular sub-parts. The first time, the products came in the same quality again with no documentation, however, Airbus refuse to accept the delivery. Causing delivery delay and financial inconveniences at the supplier, they reviewed the products and documents and delivered at the requested quality three days later. Since then there have been no more issues with the supplier and products and documentation come at the quality level asked for. |
− | == | + | == Applying Quality Gates Right== |
+ | Handling the complexity between successful project governance and thoughtful quality criteria is the challenge in applying quality gate. In case of successful application, quality gates are passed in time and according to defined requirements. | ||
+ | The following section describes both levels of processing gates, the conceptual and the operative. Further, it includes recommendations for the project owner and equips him with know-how about governance and quality criteria. Last, it is points out how vital categorizing projects into three different gate segments is. | ||
=== Quality Gate Process === | === Quality Gate Process === | ||
[[File:QGDec.png| right|thumb|500px|Figure 4: Quality Gate Process, own figure modified from Salger et alii <ref name = "Salger"/>]] | [[File:QGDec.png| right|thumb|500px|Figure 4: Quality Gate Process, own figure modified from Salger et alii <ref name = "Salger"/>]] | ||
− | Operating quality gates | + | Operating quality gates requires iterative management and is an ongoing process. According to Salger et alii <ref name="Salger"> Salger, F., Bennicke, M., Engels, G., & Lewerentz, C. (2008, October). Comprehensive architecture evaluation and management in large software-systems. In International Conference on the Quality of Software Architectures (pp. 205-219). Springer, Berlin, Heidelberg.</ref> it can be grouped into the conceptual and operative level and is described in the QGP. <br />Figure 4 illustrates the iterative application of the processes. |
− | '''Conceptual level:''' On the conceptual level quality gate management takes place. First, the initial definition of quality gates and | + | '''Conceptual level:''' On the conceptual level quality gate management takes place. First, the initial definition of quality gates and their criteria are required. Further, coaching and support of the project in the three aspects (cost, time and quality) takes place. Afterwards, the criteria defined for the quality gates is gathered and consolidated and results in the lessons learned. In this stage, a gate is ready for the pass or fail assessment. Last but not least adjustment and controlling of the quality gates takes place when assessing the criteria and deciding to go or not go into the next project phase. |
− | '''Operative level:''' The operative level describes the operations executed by the project manager along the project’s process. First is the initialisation where quality gates are set up for the project. Next is their active application of the initialized gates. The project manager is responsible for the active execution | + | '''Operative level:''' The operative level describes the operations executed by the project manager along the project’s process. First is the initialisation where quality gates are set up for the project. Next is their active application of the initialized gates. The project manager is responsible for the active execution of the project’s deliverables. Last is the finalization where results are defined and lead to lessons learned. |
=== Setup Advisory for Project Managers === | === Setup Advisory for Project Managers === | ||
− | To successfully implement and assess quality gates four tenets are of essential relevance which are performance standards and gate governance, criteria | + | To successfully implement and assess quality gates four tenets are of essential relevance which are performance standards and gate governance, criteria benchmarks and standards, criteria control and tracking. |
'''Performance standards and gate governance:''' To reach the quality gates, milestones have to be completed successfully otherwise a quality gate will very likely not be passed at the gate deadline. <br /> These milestones already inhabit single criteria relevant for later quality gates. | '''Performance standards and gate governance:''' To reach the quality gates, milestones have to be completed successfully otherwise a quality gate will very likely not be passed at the gate deadline. <br /> These milestones already inhabit single criteria relevant for later quality gates. | ||
[[File:QGDeci.png| right |thumb|550px|Figure 5: Modern Gate Governance, own figure modified from Olechowski et alii <ref name = "Olechowski"/>]] | [[File:QGDeci.png| right |thumb|550px|Figure 5: Modern Gate Governance, own figure modified from Olechowski et alii <ref name = "Olechowski"/>]] | ||
An assessment of the project’s status is evaluated based on the actual performance of intermediate milestones. Each criteria must be met successfully by each party. When a quality gate is not met, the project cannot proceed to its successive milestones and gates. A project evaluation is required based on the governance decisions traditional gate decisions of ''go'', ''kill'', ''recycle'' and ''hold''. | An assessment of the project’s status is evaluated based on the actual performance of intermediate milestones. Each criteria must be met successfully by each party. When a quality gate is not met, the project cannot proceed to its successive milestones and gates. A project evaluation is required based on the governance decisions traditional gate decisions of ''go'', ''kill'', ''recycle'' and ''hold''. | ||
− | In a go decision, the criteria | + | In a go decision, the criteria are met and a quality gate is passed, thus the project proceeds to the next phase. The opposite, when gate criteria are not fulfilled, is the kill decision, which implies the failure of required quality criteria to proceed from phase X to phase X+1. The kill decision further implies the stop of the whole project. An option to work with insufficient and not met criteria at a quality gate but still not killing the whole project is the recycle decision. In this case, the gatekeeper, e.g. the project manager, decides to revise the project and return to phase X and re-align. This decision is made when a project is still considered meaningful and worthwhile to rework, the criteria why the gate was not passed should not be of significance. The last option is the hold decision, which comes into play when a project is put on hold. This decision is useful when other project-dependent processes are not at the current stage to be sufficient for a gate go. A hold decision can end up in recycling or killing a project. |
− | In more recent research there is however also other suggestions for realistic options at gates which this article proposes and strongly encourages project manager to apply. These gate decisions include the options of ''go'', ''waiver'', ''waiver with re-view'', ''back-up plan'', ''kill'' and ''delay'' <ref name="Olechowski"> | + | In more recent research there is however also other suggestions for realistic options at gates which this article proposes and strongly encourages project manager to apply. These gate decisions include the options of ''go'', ''waiver'', ''waiver with re-view'', ''back-up plan'', ''kill'' and ''delay''.<ref name="Olechowski"> Olechowski, A., Eppinger, S., & Joglekar, N. (2017). Assessment of back-up plan, delay, and waiver options at project gate reviews. In DS 87-2 Proceedings of the 21st International Conference on Engineering Design (ICED 17) Vol 2: Design Processes, Design Organisation and Management, Vancouver, Canada, 21-25.08. 2017 (pp. 317-326). </ref> |
− | The go option implies the same as in the traditional way and proceeds into the project’s next phase. The same traditional decisions from above apply to the kill and delay option and granting a waiver at a quality gate is similar to the recycle decision. But the waiver with re-view and back-up plan decisions are novel. A waiver with a re-view introduces a review of the project at an interim date that is before the next quality gate is set. This approach assesses and controls the lack of quality, but allows procedure to the next phase while not delaying the project. The back-up plan decision is made when a project is either uncertain in its outcome and an alternative is required. When evaluating a quality gate this back-up plan can be made until its risk, development and quality | + | The go option implies the same as in the traditional way and proceeds into the project’s next phase. The same traditional decisions from above apply to the kill and delay option and granting a waiver at a quality gate is similar to the recycle decision. But the waiver with re-view and back-up plan decisions are novel. A waiver with a re-view introduces a review of the project at an interim date that is before the next quality gate is set. This approach assesses and controls the lack of quality, but allows the procedure to the next phase while not delaying the project. The back-up plan decision is made when a project is either uncertain in its outcome and an alternative is required. When evaluating a quality gate this back-up plan can be made until its risk, development and quality are assessed and a decision to either go or kill is finite, these plans are only temporary. Figure 5 represents the suggested available decisions for quality gates according to Olcheowski et alii.<ref name="Olechowski"></ref> |
− | '''Criteria | + | '''Criteria benchmarks and standards:''' Quality gates and milestones require evaluation criteria. Benchmarks and standards are utilized in quality gates to make the project’s status measurable and assessable. However, criteria must not necessarily be numbers but can also be of Boolean (Yes/No) character. |
− | Some good examples for quality indicators that can be used throughout the project stages are given by PMI<ref name = " | + | Some good examples for quality indicators that can be used throughout the project stages are given by PMI.<ref name = "2-PMI-Sym"/> They include the number of errors found on drawings, defects found in design reviews, requests to fix bugs, customer field failures, customer complaints and failures during test. Further, PMI mentions the rate at which requests to make fixes or changes come into the system and at which fixes or changes are being discharged. Lastly, the institute also suggests criteria on warranty costs.<br /> |
These examples above represent the three axes of time, cost and quality respectively, provide good examples for project managers with less knowledge about the field, and provide a decent head start. | These examples above represent the three axes of time, cost and quality respectively, provide good examples for project managers with less knowledge about the field, and provide a decent head start. | ||
− | However, it shall be noted that the suitable quality indicators differ from the application field, e.g. manufacturing | + | However, it shall be noted that the suitable quality indicators differ from the application field, e.g. manufacturing and IT. |
'''Criteria control:''' Quality gates require implementation and control during the whole project life cycle. Every gate and several milestones should continuously assess and track the three aspects of project time, cost and quality. Every development project has planned and precisely scheduled quality gates, which is a project manager’s responsibility. | '''Criteria control:''' Quality gates require implementation and control during the whole project life cycle. Every gate and several milestones should continuously assess and track the three aspects of project time, cost and quality. Every development project has planned and precisely scheduled quality gates, which is a project manager’s responsibility. | ||
Introducing a quality gate criteria checklist or matrix is beneficial in this case, an example is given [http://wiki.doing-projects.org/index.php/File:QGChecklist.png here]. | Introducing a quality gate criteria checklist or matrix is beneficial in this case, an example is given [http://wiki.doing-projects.org/index.php/File:QGChecklist.png here]. | ||
− | '''Tracking:''' Along the project development and thus its milestones and quality gates, a project manager is obliged to track its progress. When assessing the milestone and gate criteria, deductions in terms of potentially necessary resource shifts are necessary. Thus, the information requires not only evaluation in terms of whether the project can proceed or not, inspection for possibly needed changes and alterations of the current or upcoming milestone and gate criteria | + | '''Tracking:''' Along the project development and thus its milestones and quality gates, a project manager is obliged to track its progress. When assessing the milestone and gate criteria, deductions in terms of potentially necessary resource shifts are necessary. Thus, the information requires not only evaluation in terms of whether the project can proceed or not, but inspection for possibly needed changes and alterations of the current or upcoming milestone and gate criteria are mandatory. |
=== Phasing Quality Gates and Objectives === | === Phasing Quality Gates and Objectives === | ||
Line 89: | Line 90: | ||
At least one quality gate is suggested to cover these aspects. | At least one quality gate is suggested to cover these aspects. | ||
− | '''Middle Gates: ''' This phase covers implementation, integration and validation readiness. It usually requires first prototyping and actual product/service development processes. Here project requirements are tested against their potential solutions. When the milestones and gates are passed one can assume all | + | '''Middle Gates: ''' This phase covers implementation, integration and validation readiness. It usually requires first prototyping and actual product/service development processes. Here project requirements are tested against their potential solutions. When the milestones and gates are passed one can assume all stakeholders are satisfied with the project’s first solution. The phase covers the aspects of both solution and readiness acceptance. In other words, the project’s design and development take place here. |
At least two quality gates are suggested to cover the two main aspects of design (solution) and development (readiness). | At least two quality gates are suggested to cover the two main aspects of design (solution) and development (readiness). | ||
Line 98: | Line 99: | ||
The following section describes the quality gate tool's limitations by the means of practical examples. It points out that its concrete '''gate decisions''' can have a serious negative impact on a company's performance, the technique is less applicable to '''smaller projects''' and that endeavors with '''high uncertainty''' are less desirable application fields for quality gates. | The following section describes the quality gate tool's limitations by the means of practical examples. It points out that its concrete '''gate decisions''' can have a serious negative impact on a company's performance, the technique is less applicable to '''smaller projects''' and that endeavors with '''high uncertainty''' are less desirable application fields for quality gates. | ||
− | Rewinding to the Airbus example from earlier, the company mentions that the quality gate model is not necessarily applicable to every situation, sometimes requires modification and is definitely not the solution to every problem a company might face. Airbus mentions they have to manufacture ten | + | Rewinding to the Airbus example from earlier, the company mentions that the quality gate model is not necessarily applicable to every situation, sometimes requires modification and is definitely not the solution to every problem a company might face. Airbus mentions they have to manufacture ten aircraft per FLA per week and if a gate is not passed, a delay in terms of project hold (stop and fix) is not acceptable. They mention that only in 2% of their cases a stop and fix decision at a gate has been made,<ref name="Airbus"></ref> however this has already had a huge impact, how much in particular is not stated though. Nevertheless, these tough decisions that imply passing or failing a gate apply to all phase gate models and their processes. Phase gate models are not the perfect and/or only solution to every faulty process. Quality gates are thus not an exemption but rather the rule when it comes to their decisional impacts. |
− | Other scholars and practitioners mention that the project at which quality gates should be applied to must have a certain size and be meaningful. Thus, quality gates are not necessarily applicable to smaller projects, for instance in manufacturing. Studies from practice show from two cases, one at a job-shop manufacturing and another in clocked assembly line, both placed in industrial surroundings, quality gates were beneficial for processes when they had a certain capacity. There is little to no experience for production setups with smaller batch sizes. This is mainly due to the fact that the benefits of quality gates increase when the process happens more often since otherwise the continuous improvements and learnings from the technique cannot be implemented and become meaningless instead. It is further mentioned that phase gate models accordingly find implementation in OEMs such as General Motors or Daimler. The researchers from the case studies summarize that “another limitation is that whereas the model seems suitable for productions with sufficient batch sizes in order to allow continuous update processes and learning, the benefit for small batch productions has to be investigated.” | + | Other scholars and practitioners mention that the project at which quality gates should be applied to must have a certain size and be meaningful. Thus, quality gates are not necessarily applicable to smaller projects, for instance in manufacturing. Studies from practice show from two cases, one at a job-shop manufacturing and another in clocked assembly line, both placed in industrial surroundings, quality gates were beneficial for processes when they had a certain capacity. There is little to no experience for production setups with smaller batch sizes. This is mainly due to the fact that the benefits of quality gates increase when the process happens more often since otherwise the continuous improvements and learnings from the technique cannot be implemented and become meaningless instead. <ref name="TwoEx"> Wuest, T., Liu, A., Lu, S. C. Y., & Thoben, K. D. (2014). Application of the stage gate model in production supporting quality management. Procedia Cirp, 17, 32-37. </ref> It is further mentioned that phase gate models accordingly find implementation in OEMs such as General Motors or Daimler. The researchers from the case studies summarize that “another limitation is that whereas the model seems suitable for productions with sufficient batch sizes in order to allow continuous update processes and learning, the benefit for small batch productions has to be investigated.” <ref name="TwoEx"></ref> |
− | The application of quality gates requires an early on definition of criteria and benchmarks. Therefore, for projects with very high uncertainty of the outcome or a desired unplanned development quality gates are not the favourable technique to apply. Often the process of quality gates is thus implemented in software development where the outcome of a particular piece of software is known from the very beginning on | + | The application of quality gates requires an early on definition of criteria and benchmarks. Therefore, for projects with very high uncertainty of the outcome or a desired unplanned development quality gates are not the favourable technique to apply. Often the process of quality gates is thus implemented in software development where the outcome of a particular piece of software is known from the very beginning on. FedEx for example started to implement quality gates to assess and further develop their enterprise IT production process. <ref name="EnterpriseIT">Ambartsoumian, V., Dhaliwal, J., Lee, E., Meservy, T., & Zhang, C. (2011). Implementing quality gates throughout the enterprise it production process. Journal of Information Technology Management, 22(1), 28-38. </ref> They have defined the early on targets in the very beginning and set requirements for sub-targets throughout the whole process. They have formed an internal department named the “Software Quality Assurance” team, which was responsible to develop key quality standards for software development lifecycles. This highlights again that the implementation of quality gates requires very early target setting and devotion by a team that aims for a particular goal. It is not beneficial to apply the process of quality gates into projects where deliverables are uncertain. |
To summarize, it is important to understand that the decisions made at quality gates can have a huge impact. When specific requirements are demanded the no go or a stop and halt decision at a quality gate can e.g. affect a production company’s output and lead-time significantly. Project managers should wisely consider where the implication of quality gates is reasonable and applicable. | To summarize, it is important to understand that the decisions made at quality gates can have a huge impact. When specific requirements are demanded the no go or a stop and halt decision at a quality gate can e.g. affect a production company’s output and lead-time significantly. Project managers should wisely consider where the implication of quality gates is reasonable and applicable. | ||
− | Also, the quality gate process is not necessarily | + | Also, the quality gate process is not necessarily adaptable to smaller projects. Its relevance in consideration of the continuous improvement of processes becomes more meaningful for larger endeavours. Last but not least, the implementer should have a very clear and concise goal for his or her project. When the desirables and the outcome are not clear it is hard to define quality criteria, which is necessary to control at the quality gates and must be defined when setting up a project. |
== Tips and Tricks for Practitioners == | == Tips and Tricks for Practitioners == | ||
− | For the successful application of | + | For the successful application of quality gates, McKinsey & Company and others<ref name="McK"> Giebel, M., Essmann, H., Du Preez, N., & Jochem, R. (2009). Improved innovation through the integration of Quality Gates into the Enterprise and Product Lifecycle Roadmaps. CIRP Journal of Manufacturing Science and Technology, 1(3), 199-205.</ref> have defined best practices, which project managers are strongly encouraged to utilize as well: |
{| cellspacing="0" cellpadding="0" style="margin:0 0 1em; width:100% background:white;" | {| cellspacing="0" cellpadding="0" style="margin:0 0 1em; width:100% background:white;" | ||
Line 117: | Line 118: | ||
The correct positioning of quality criteria especially in the development process is key for successful quality gate application. | The correct positioning of quality criteria especially in the development process is key for successful quality gate application. | ||
− | II. ''Apply E2E quality gate architecture''<br />[[File:M2.png| right |thumb|700px|Figure 6: Parallel Milestones in Different | + | II. ''Apply E2E quality gate architecture''<br />[[File:M2.png| right |thumb|700px|Figure 6: Parallel Milestones in Different Functional Groups to Quality Gate Representation (own figure)]] |
Ensure that quality gates cover the whole project lifecycle and do not only cover a particular part. The example from Airbus showed that their end-to-end architecture was the vital part to improve the supplier quality and decrease FLA downtime. | Ensure that quality gates cover the whole project lifecycle and do not only cover a particular part. The example from Airbus showed that their end-to-end architecture was the vital part to improve the supplier quality and decrease FLA downtime. | ||
Line 124: | Line 125: | ||
IV. ''Add actual names to the quality gate checklist and not only a department.''<br /> | IV. ''Add actual names to the quality gate checklist and not only a department.''<br /> | ||
− | Put the responsible people, e.g. the department’s manager (John Doe, Morten Menigmand, Erika Mustermann) into the column for deliverable responsible instead of the department (HR, IT, R&D). Otherwise, afterwards discussion can come up when a target is not met and who was responsible for it. | + | Put the responsible people, e.g. the department’s manager (John Doe, Morten Menigmand, Erika Mustermann) into the column for deliverable responsible instead of the department (HR, IT, R&D). Otherwise, afterwards, a discussion can come up when a target is not met and who was responsible for it. |
V. ''The amount of four quality gates is advised for small to medium-sized projects''<br /> | V. ''The amount of four quality gates is advised for small to medium-sized projects''<br /> | ||
However always assess the amount of quality gates needed and required according to the project lifecycle, its characteristics, scope and the company’s general procedure and quality standard. | However always assess the amount of quality gates needed and required according to the project lifecycle, its characteristics, scope and the company’s general procedure and quality standard. | ||
− | VI. ''You cannot | + | VI. ''You cannot manage what you cannot measure''<br /> |
It is desirable to have measurable criteria, however this is not mandatory. It can also be in the Boolean form of yes or now. Nevertheless, all sub-criteria must be met before passing on in quality gates. | It is desirable to have measurable criteria, however this is not mandatory. It can also be in the Boolean form of yes or now. Nevertheless, all sub-criteria must be met before passing on in quality gates. | ||
VII. ''One quality gate for each transition from one project phase to another''<br /> | VII. ''One quality gate for each transition from one project phase to another''<br /> | ||
− | See section ''Phasing Quality Gates and Objectives'' | + | See section ''Phasing Quality Gates and Objectives''. |
VIII. ''Milestones can also be in parallel''<br /> | VIII. ''Milestones can also be in parallel''<br /> | ||
Line 143: | Line 144: | ||
== Annotated Bibliography == | == Annotated Bibliography == | ||
− | (1) PMI | + | The following section mentions relevant literature and academic research related to quality gates and its processes. This selected annotated bibliography focuses on both, project management and quality management. |
+ | |||
+ | (1) '''Stage-gate systems: a new tool for managing new products''' by ''Cooper, R. G.'' (1990) <ref name="Cooper"> </ref> is available in the journal [https://www.sciencedirect.com/science/article/pii/000768139090040I Business Horizons]. | ||
+ | |||
+ | Being one of the most influential phase models this article builds the early foundation for the stage gate model and its underlying subsystems. Cooper wrote this book to establish new ways for strategic solutions to issues in new product management. The article provides the reader with a profound understanding why phase gate models were established and how they work, the principles of gate decisions, setting, reviewing and assessing gates is described in this article. | ||
+ | |||
+ | (2) '''Achieving total project quality control using the quality gate method''' by ''Aaron et alii'' (1993) <ref name="2-PMI-Sym"> </ref> is available under [https://www.projectrimms.com/Downloads/Whitepapers/Achieving%20Total%20Project%20Quality%20Control.pdf Project Rimms]. | ||
+ | |||
+ | This article is one of the earlier and first works on quality gates. It originates from the Project Management Institute itself and was first published at one of their symposia in 1993. The paper considers the Project Management Body of Knowledge (PMBOK) and quality management measures and describes how one can gain control over project quality. Furthermore introduces the paper the principle of quality gates and illustrates its application in the example of Tellabs Operations, Inc. | ||
+ | |||
+ | (3) '''Quality Gates''', a chapter (pp. 193-207) in the book ''Supply Chain Integration Challenges in Commercial Aerospace'' by ''Sciannamea, I.''(2017)<ref name="Airbus"> </ref> is available under [https://www.springer.com/de/book/9783319461540 Springer Nature Switzerland AG]. | ||
− | + | This book chapter is included in the annotated bibliography due to its illustrational example of implementing quality gates in practice. The chapter about the case study at Airbus provides the reader with a clear understanding of how to successfully implement quality gates in industrial companies. Further, it also provides a concise understanding of when quality gate processes are less applicable. | |
− | ( | + | (4) '''Towards quality gates in continuous delivery and deployment''' by ''Schermann, G. et alii'' (2016) <ref name="QGCont"> </ref> is available under [https://ieeexplore.ieee.org/abstract/document/7503737/ IEEE Xplore]. |
+ | This article from the Institute of Electrical and Electronic Engineers (IEEE) is comparably short to other annotated bibliography above provides the raison d'être for quality gates. It focuses on the learning outcomes delivered by applying the technique and points out its advantages for decreased risk of faultiness in processes and products. Even though the article is only cited once in this Wiki, it is worth reading since also introduces the reader to the trade-off between quality and time-to-market when applying quality gates. | ||
== References == | == References == | ||
<references /> | <references /> |
Latest revision as of 22:56, 21 July 2021
by Thore Uwe Aye (s202746)
Contents |
[edit] Abstract
Projects are temporary, unique endeavors and require active management of their integration, scope, schedule, cost, quality, resources, and communication according to the Project Management Institute (PMI). [1]
One tool to control project management is the stage gate approach that divides projects into stages with gates and tracks their progress and success. In the 1990s a modification to focus on especially schedule, cost, and quality was established known as Quality Gates (QG). A quality gate represents a checkpoint of predefined criteria set by the project manager to evaluate the current progress of a project. Herein the focus lies on the three aspects of time and cost, both resource-related and quality. After assessing the specified benchmarks and standards, an evaluation of passing or failing the gate is made. The case study representing practical findings from an Airbus production plant provides the reader with a tangible example how quality gates can successfully be implemented and managed.
This article sets the quality gate model into the picture with the stage gates as another phase gate model and points out its differences, benefits, and limitations. One of the takeaways is that in the quality gate model more emphasis lies on the quality criteria,its control in project management and its lifecycles. Besides the article mentions how four main tenets set, assess, and complete gates and form the setup advisory for project managers which includes detailed gate decision governance. [2] Furthermore, a brief overview of quality management tools and techniques which include TQM, EFQM and (Lean) Six Sigma is given to sort the quality gate model. The article also explains the required steps a project manager needs to take in order to implement quality gates in projects together with the Quality Gate Process (QGP) and management in operative and conceptual levels. A proposal of applying the quality gates by segmenting projects into the three stages of front-end, middle, and back-end gates for different project stages is elaborated. [2] [3]
Finally, in the section of limitations and challenges more examples from practice are evaluated and suggestions are made in terms of selecting projects for applications of quality gate models more carefully. Further only projects with considerable size and low uncertainty are found eligible for quality gate processes. Last but not least this article focuses heavily on practical applicability precisely for projects and thus provides tips and tricks for practitioners. The annotated bibliography outlines major literature that is relevant but also suggests papers, which provide profound insights to reader who can study quality gates more in-depth through this suggested literature.
[edit] Keeping Projects on Track with Quality
The technique of applying quality gates and their control process after each phase is a useful tool and is often applied by project managers or owners and process managers. It provides designing, embedding and checking quality criteria after the development of a project reaches a new phase, e.g. from developing an IT software to its deployment. Before deploying the software a gatekeeper, for instance the project manager, assesses whether the quality of the previous phase satisfies the quality gate criteria. The process of defining, embedding and checking quality criteria are underlying the entire project’s lifecycle.
Quality gates reach from initiation of a project until its final closing after deployment. Most applications take place in industrial circumstances where development takes place, such as in new product development (NPD), production (manufacturing and assembly) and also very commonly in IT software development. Often quality gates are the chosen tool to assess these processes because it enables practitioners to gain control over the quality development, its status and the current project’s state of the art in terms of quality. This is done by defining the quality criteria in the initiation and planning of a project, setting milestones and gates assessing the set criteria along the way.
[edit] Phase Gate Models
Quality gates are a comparable form of the stage gate model and also other phase gate models. It is suggested to separate projects in terms of quality gates into the four different categories of planning, design, development and deployment.
Also in the stage gate model projects are separated into phases because the outcome is often unknown and controlling can therefore take place after each phase.[4] Setting gates after each phase, which must be passed before continuing to the next, allows control. Further, it enables early identification of potential risks and provides increased visibility.
According to PMI, a project has the dimensions of integration, scope, schedule, cost, quality, resources, and communication and Cooper’s stage gate model intends to include all aspects in its model.[4] Contrary, the Quality Gate model focuses specifically on the factors of time (schedule), cost and quality – all three of them are essential for a project’s quality outcome. In this way, it differs to the stage gate model. The gates are set timely independent and flexible, but in a sequential order – whereas its criteria to pass a gate are defined very specifically. More information about the stage gate model can be obtained by another DTU wiki called The Stage-Gate Model.
Quality gates as a project management tool have been established because practitioners felt that in our rapidly changing world and disrupting time there is less focus on quality due to a downside in order to increase time-to-market. Scholars therefore point out that “Quality gates […] are supposed to increase the confidence stakeholders have in a release”. [5] It is one of the solutions to introduce more quality control in project management surroundings.
[edit] Quality Management & Control
Quality management consists of four basic pillars, its planning, assurance, control and improvement. [6] In project management, quality is of relevance in order to achieve the intended outcome and function of the endeavour. Already Cooper pointed out in his stage gate model in 1990 [4] that many newly launched products lack quality inspection processes. To achieve control over quality management in projects several tools evolved over the years and gained publicity.
Total quality management (TQM): In one of the works of comparing quality management practices, Pfeifer describes TQM as "a management approach of an organisation centered on quality, based on the participation of all its members and aiming at long-term success through customer satisfaction and benefits to all members of the organisation and society." [7] TQM aims for establishing an organisational culture where quality is the main criteria for success and requires cultural implementation. More information on the topic can be found in the DTU wiki Total Quality Management.
European Foundation for Quality Management (EFQM) model: According to the foundation itself they summarize its model as the following: “The EFQM Model is a globally-recognised management framework which allows organisations to achieve success by measuring where they are on the path towards transformation, helping them understand the gaps and possible solutions available, and empowering them to progress and significantly improve their organisation’s performance.” [8] It helps to define purpose, create culture, forge strong leaders, transform organisation, foster agile practices, address unique organisational challenges, forecast the future. More information on the topic can be found in the DTU wiki under EFQM and the European Quality Award.
(Lean) six sigma: The combination of the principles from lean principles/management and six sigma is called lean six sigma. Lean management focuses on continuous process improvement based on small, incremental changes with the overall goal to improve efficiency and quality. Together with six sigma it aims for improving processes and performance by narrowing resources and variations down to the minimum required.[9] More information on the topic can be found in the DTU wiki under Lean Six Sigma.
Compared to quality management tools quality gates focus on specific quality aspects at specific times, the gates, in contrast to non-stop iterative quality management perspectives. It sets and later assesses quality criteria and intervenes when errors occur in the project’s development. Thus, it becomes obvious that quality gates are rather different to prevalent and common quality management and control techniques. Using these argumentations project managers can justify its presence and application for endeavours where quality-heaviness is key. Thus, quality gates is one of the solutions to control quality in the way of a phase gate model. It takes the advantages of quality management and combines it with the upsides of continuous project control by applying the project management techniques from phase gate processes.
[edit] Airbus Case Study
One major industrial player adopting the quality gate is Airbus. The multinational aerospace company incorporates quality gates approximately since 2015 and implements it as a quality management tool to handle and control the quality of supplier products. End-to-end (E2E) quality gates are nowadays an essential part of Airbus’ Quality Management System. [10]
Airbus implemented quality gates from the designs over parts up to a final aircraft and therefore considers them end-to-end gates. Every single time a project or product from a supplier is supposed to proceed to the next stage Airbus assesses the quality specifications and decides on the proceeding. They have implemented these gates because lack of quality concerns their Final Assembly Lines (FAL) and have found that these concerns especially arise from parts by external supplier. The quality requirements stated at the gates have even become part of their Customer Supplier Agreements and since then their supply chain efficiency improved since the amount of incomplete products decreased together with cost and visibility, cooperation and on-time delivery increased. Airbus and the supplier degree on targets and deliverables which they can measure, control and review at handover meetings.
In particular, one example turned into a success story and showcased the strength quality gates have. Airbus had one supplier who supplied their production facility in St. Nazaire who always lacked documentation when delivering parts that were also in poor quality. This supplier and his low quality led to required manual corrections by Airbus in their FAL. Thus, customer and supplier integrated end-to-end quality gates for these particular sub-parts. The first time, the products came in the same quality again with no documentation, however, Airbus refuse to accept the delivery. Causing delivery delay and financial inconveniences at the supplier, they reviewed the products and documents and delivered at the requested quality three days later. Since then there have been no more issues with the supplier and products and documentation come at the quality level asked for.
[edit] Applying Quality Gates Right
Handling the complexity between successful project governance and thoughtful quality criteria is the challenge in applying quality gate. In case of successful application, quality gates are passed in time and according to defined requirements. The following section describes both levels of processing gates, the conceptual and the operative. Further, it includes recommendations for the project owner and equips him with know-how about governance and quality criteria. Last, it is points out how vital categorizing projects into three different gate segments is.
[edit] Quality Gate Process
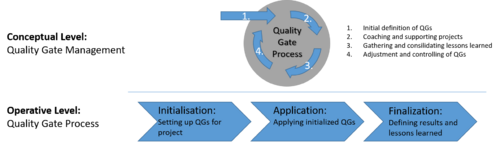
Operating quality gates requires iterative management and is an ongoing process. According to Salger et alii [11] it can be grouped into the conceptual and operative level and is described in the QGP.
Figure 4 illustrates the iterative application of the processes.
Conceptual level: On the conceptual level quality gate management takes place. First, the initial definition of quality gates and their criteria are required. Further, coaching and support of the project in the three aspects (cost, time and quality) takes place. Afterwards, the criteria defined for the quality gates is gathered and consolidated and results in the lessons learned. In this stage, a gate is ready for the pass or fail assessment. Last but not least adjustment and controlling of the quality gates takes place when assessing the criteria and deciding to go or not go into the next project phase.
Operative level: The operative level describes the operations executed by the project manager along the project’s process. First is the initialisation where quality gates are set up for the project. Next is their active application of the initialized gates. The project manager is responsible for the active execution of the project’s deliverables. Last is the finalization where results are defined and lead to lessons learned.
[edit] Setup Advisory for Project Managers
To successfully implement and assess quality gates four tenets are of essential relevance which are performance standards and gate governance, criteria benchmarks and standards, criteria control and tracking.
Performance standards and gate governance: To reach the quality gates, milestones have to be completed successfully otherwise a quality gate will very likely not be passed at the gate deadline.
These milestones already inhabit single criteria relevant for later quality gates.
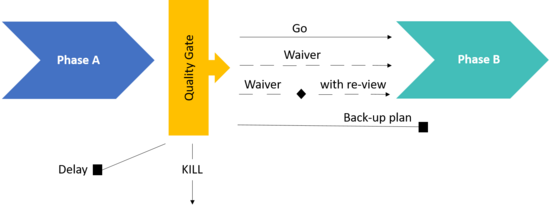
An assessment of the project’s status is evaluated based on the actual performance of intermediate milestones. Each criteria must be met successfully by each party. When a quality gate is not met, the project cannot proceed to its successive milestones and gates. A project evaluation is required based on the governance decisions traditional gate decisions of go, kill, recycle and hold. In a go decision, the criteria are met and a quality gate is passed, thus the project proceeds to the next phase. The opposite, when gate criteria are not fulfilled, is the kill decision, which implies the failure of required quality criteria to proceed from phase X to phase X+1. The kill decision further implies the stop of the whole project. An option to work with insufficient and not met criteria at a quality gate but still not killing the whole project is the recycle decision. In this case, the gatekeeper, e.g. the project manager, decides to revise the project and return to phase X and re-align. This decision is made when a project is still considered meaningful and worthwhile to rework, the criteria why the gate was not passed should not be of significance. The last option is the hold decision, which comes into play when a project is put on hold. This decision is useful when other project-dependent processes are not at the current stage to be sufficient for a gate go. A hold decision can end up in recycling or killing a project.
In more recent research there is however also other suggestions for realistic options at gates which this article proposes and strongly encourages project manager to apply. These gate decisions include the options of go, waiver, waiver with re-view, back-up plan, kill and delay.[12] The go option implies the same as in the traditional way and proceeds into the project’s next phase. The same traditional decisions from above apply to the kill and delay option and granting a waiver at a quality gate is similar to the recycle decision. But the waiver with re-view and back-up plan decisions are novel. A waiver with a re-view introduces a review of the project at an interim date that is before the next quality gate is set. This approach assesses and controls the lack of quality, but allows the procedure to the next phase while not delaying the project. The back-up plan decision is made when a project is either uncertain in its outcome and an alternative is required. When evaluating a quality gate this back-up plan can be made until its risk, development and quality are assessed and a decision to either go or kill is finite, these plans are only temporary. Figure 5 represents the suggested available decisions for quality gates according to Olcheowski et alii.[12]
Criteria benchmarks and standards: Quality gates and milestones require evaluation criteria. Benchmarks and standards are utilized in quality gates to make the project’s status measurable and assessable. However, criteria must not necessarily be numbers but can also be of Boolean (Yes/No) character.
Some good examples for quality indicators that can be used throughout the project stages are given by PMI.[2] They include the number of errors found on drawings, defects found in design reviews, requests to fix bugs, customer field failures, customer complaints and failures during test. Further, PMI mentions the rate at which requests to make fixes or changes come into the system and at which fixes or changes are being discharged. Lastly, the institute also suggests criteria on warranty costs.
These examples above represent the three axes of time, cost and quality respectively, provide good examples for project managers with less knowledge about the field, and provide a decent head start.
However, it shall be noted that the suitable quality indicators differ from the application field, e.g. manufacturing and IT.
Criteria control: Quality gates require implementation and control during the whole project life cycle. Every gate and several milestones should continuously assess and track the three aspects of project time, cost and quality. Every development project has planned and precisely scheduled quality gates, which is a project manager’s responsibility. Introducing a quality gate criteria checklist or matrix is beneficial in this case, an example is given here.
Tracking: Along the project development and thus its milestones and quality gates, a project manager is obliged to track its progress. When assessing the milestone and gate criteria, deductions in terms of potentially necessary resource shifts are necessary. Thus, the information requires not only evaluation in terms of whether the project can proceed or not, but inspection for possibly needed changes and alterations of the current or upcoming milestone and gate criteria are mandatory.
[edit] Phasing Quality Gates and Objectives
Quality gates can, nevertheless the total quantity, be grouped into three main categories, which are described by the following. These groups provide orientation to phase quality gates and suggest topics to cover quality management and control successfully. They follow the suggestions of PMI [2].
Front-end Gates: For this stage investigation of the project, its internal commitment, investing issues (time and money) and general project design are determined. Relevant criteria for milestones and the gates for this topic must be set. Later in gates, their status is evaluated accordingly. During this phase stakeholder, agree to the scope of the project as well. This stage is also known as project planning or verification. At least one quality gate is suggested to cover these aspects.
Middle Gates: This phase covers implementation, integration and validation readiness. It usually requires first prototyping and actual product/service development processes. Here project requirements are tested against their potential solutions. When the milestones and gates are passed one can assume all stakeholders are satisfied with the project’s first solution. The phase covers the aspects of both solution and readiness acceptance. In other words, the project’s design and development take place here. At least two quality gates are suggested to cover the two main aspects of design (solution) and development (readiness).
Back-end Gates: Finally, the field trial, controlled introduction and the general availability (release) of the project are covered in the back-end gates. For passing this gate the project manager needs to assure all stakeholders agree the project is complete and the project’s execution is now compliant with all requirements and faces no more risk. This is thus the project’s deployment. The gate is also known as the Go-Live phase. It is suggested to have at least one quality gate covering the final deployment check.
[edit] Limitations and Challenges
The following section describes the quality gate tool's limitations by the means of practical examples. It points out that its concrete gate decisions can have a serious negative impact on a company's performance, the technique is less applicable to smaller projects and that endeavors with high uncertainty are less desirable application fields for quality gates.
Rewinding to the Airbus example from earlier, the company mentions that the quality gate model is not necessarily applicable to every situation, sometimes requires modification and is definitely not the solution to every problem a company might face. Airbus mentions they have to manufacture ten aircraft per FLA per week and if a gate is not passed, a delay in terms of project hold (stop and fix) is not acceptable. They mention that only in 2% of their cases a stop and fix decision at a gate has been made,[10] however this has already had a huge impact, how much in particular is not stated though. Nevertheless, these tough decisions that imply passing or failing a gate apply to all phase gate models and their processes. Phase gate models are not the perfect and/or only solution to every faulty process. Quality gates are thus not an exemption but rather the rule when it comes to their decisional impacts.
Other scholars and practitioners mention that the project at which quality gates should be applied to must have a certain size and be meaningful. Thus, quality gates are not necessarily applicable to smaller projects, for instance in manufacturing. Studies from practice show from two cases, one at a job-shop manufacturing and another in clocked assembly line, both placed in industrial surroundings, quality gates were beneficial for processes when they had a certain capacity. There is little to no experience for production setups with smaller batch sizes. This is mainly due to the fact that the benefits of quality gates increase when the process happens more often since otherwise the continuous improvements and learnings from the technique cannot be implemented and become meaningless instead. [13] It is further mentioned that phase gate models accordingly find implementation in OEMs such as General Motors or Daimler. The researchers from the case studies summarize that “another limitation is that whereas the model seems suitable for productions with sufficient batch sizes in order to allow continuous update processes and learning, the benefit for small batch productions has to be investigated.” [13]
The application of quality gates requires an early on definition of criteria and benchmarks. Therefore, for projects with very high uncertainty of the outcome or a desired unplanned development quality gates are not the favourable technique to apply. Often the process of quality gates is thus implemented in software development where the outcome of a particular piece of software is known from the very beginning on. FedEx for example started to implement quality gates to assess and further develop their enterprise IT production process. [14] They have defined the early on targets in the very beginning and set requirements for sub-targets throughout the whole process. They have formed an internal department named the “Software Quality Assurance” team, which was responsible to develop key quality standards for software development lifecycles. This highlights again that the implementation of quality gates requires very early target setting and devotion by a team that aims for a particular goal. It is not beneficial to apply the process of quality gates into projects where deliverables are uncertain.
To summarize, it is important to understand that the decisions made at quality gates can have a huge impact. When specific requirements are demanded the no go or a stop and halt decision at a quality gate can e.g. affect a production company’s output and lead-time significantly. Project managers should wisely consider where the implication of quality gates is reasonable and applicable. Also, the quality gate process is not necessarily adaptable to smaller projects. Its relevance in consideration of the continuous improvement of processes becomes more meaningful for larger endeavours. Last but not least, the implementer should have a very clear and concise goal for his or her project. When the desirables and the outcome are not clear it is hard to define quality criteria, which is necessary to control at the quality gates and must be defined when setting up a project.
[edit] Tips and Tricks for Practitioners
For the successful application of quality gates, McKinsey & Company and others[15] have defined best practices, which project managers are strongly encouraged to utilize as well:
I. Pay special attention to the positioning of deliverables, milestones and gates Ensure that quality gates cover the whole project lifecycle and do not only cover a particular part. The example from Airbus showed that their end-to-end architecture was the vital part to improve the supplier quality and decrease FLA downtime. III. It is suggested to call milestones according to the quality gate IV. Add actual names to the quality gate checklist and not only a department. V. The amount of four quality gates is advised for small to medium-sized projects VI. You cannot manage what you cannot measure VII. One quality gate for each transition from one project phase to another VIII. Milestones can also be in parallel |
[edit] Annotated Bibliography
The following section mentions relevant literature and academic research related to quality gates and its processes. This selected annotated bibliography focuses on both, project management and quality management.
(1) Stage-gate systems: a new tool for managing new products by Cooper, R. G. (1990) [4] is available in the journal Business Horizons.
Being one of the most influential phase models this article builds the early foundation for the stage gate model and its underlying subsystems. Cooper wrote this book to establish new ways for strategic solutions to issues in new product management. The article provides the reader with a profound understanding why phase gate models were established and how they work, the principles of gate decisions, setting, reviewing and assessing gates is described in this article.
(2) Achieving total project quality control using the quality gate method by Aaron et alii (1993) [2] is available under Project Rimms.
This article is one of the earlier and first works on quality gates. It originates from the Project Management Institute itself and was first published at one of their symposia in 1993. The paper considers the Project Management Body of Knowledge (PMBOK) and quality management measures and describes how one can gain control over project quality. Furthermore introduces the paper the principle of quality gates and illustrates its application in the example of Tellabs Operations, Inc.
(3) Quality Gates, a chapter (pp. 193-207) in the book Supply Chain Integration Challenges in Commercial Aerospace by Sciannamea, I.(2017)[10] is available under Springer Nature Switzerland AG.
This book chapter is included in the annotated bibliography due to its illustrational example of implementing quality gates in practice. The chapter about the case study at Airbus provides the reader with a clear understanding of how to successfully implement quality gates in industrial companies. Further, it also provides a concise understanding of when quality gate processes are less applicable.
(4) Towards quality gates in continuous delivery and deployment by Schermann, G. et alii (2016) [5] is available under IEEE Xplore.
This article from the Institute of Electrical and Electronic Engineers (IEEE) is comparably short to other annotated bibliography above provides the raison d'être for quality gates. It focuses on the learning outcomes delivered by applying the technique and points out its advantages for decreased risk of faultiness in processes and products. Even though the article is only cited once in this Wiki, it is worth reading since also introduces the reader to the trade-off between quality and time-to-market when applying quality gates.
[edit] References
- ↑ Project Management Institute, Inc.. (2017). Guide to the Project Management Body of Knowledge (PMBOK® Guide) (6th Edition). Project Management Institute, Inc. (PMI).
- ↑ 2.0 2.1 2.2 2.3 2.4 Aaron, J. M., Bratta, C. P., & Smith, D. P. (1993). Achieving total project quality control using the quality gate method. In proceedings of the annual seminar symposium-project management institute (pp. 120-129).
- ↑ Schnell, J., & Reinhart, G. (2016). Quality management for battery production: a quality gate concept. Procedia CIRP, 57, 568-573.
- ↑ 4.0 4.1 4.2 4.3 Cooper, R. G. (1990). Stage-gate systems: a new tool for managing new products. Business horizons, 33(3), 44-54.
- ↑ 5.0 5.1 Schermann, G., Cito, J., Leitner, P., & Gall, H. C. (2016, May). Towards quality gates in continuous delivery and deployment. In 2016 IEEE 24th international conference on program comprehension (ICPC) (pp. 1-4). IEEE.
- ↑ Rose, K. H. (2005). Project quality management: why, what and how.
- ↑ Pfeifer, T. (2002). Quality management. Strategies, methods, techniques, Hanser, München, Wien.
- ↑ European Foundation for Quality Management, Retrieved from : "https://www.efqm.org/index.php/efqm-model/" [Accessed: 28. February 2021]
- ↑ Arnheiter, E. D., & Maleyeff, J. (2005). The integration of lean management and Six Sigma. The TQM magazine.
- ↑ 10.0 10.1 10.2 Sciannamea, I. (2017). Quality Gates. In Supply Chain Integration Challenges in Commercial Aerospace (pp. 193-207). Springer, Cham.
- ↑ 11.0 11.1 Salger, F., Bennicke, M., Engels, G., & Lewerentz, C. (2008, October). Comprehensive architecture evaluation and management in large software-systems. In International Conference on the Quality of Software Architectures (pp. 205-219). Springer, Berlin, Heidelberg.
- ↑ 12.0 12.1 12.2 Olechowski, A., Eppinger, S., & Joglekar, N. (2017). Assessment of back-up plan, delay, and waiver options at project gate reviews. In DS 87-2 Proceedings of the 21st International Conference on Engineering Design (ICED 17) Vol 2: Design Processes, Design Organisation and Management, Vancouver, Canada, 21-25.08. 2017 (pp. 317-326).
- ↑ 13.0 13.1 Wuest, T., Liu, A., Lu, S. C. Y., & Thoben, K. D. (2014). Application of the stage gate model in production supporting quality management. Procedia Cirp, 17, 32-37.
- ↑ Ambartsoumian, V., Dhaliwal, J., Lee, E., Meservy, T., & Zhang, C. (2011). Implementing quality gates throughout the enterprise it production process. Journal of Information Technology Management, 22(1), 28-38.
- ↑ Giebel, M., Essmann, H., Du Preez, N., & Jochem, R. (2009). Improved innovation through the integration of Quality Gates into the Enterprise and Product Lifecycle Roadmaps. CIRP Journal of Manufacturing Science and Technology, 1(3), 199-205.