Lean principles in the construction industry
The construction sector is one of the main pillars of economic growth and country development for all nations across the globe and a link in the chain of dependencies between all industries in terms of consuming inputs and providing products. Nonetheless, it is estimated that 50% or more of the required resources and effort as to deliver the built environment consists in waste, or non-added value effort from the customer's perspective. The same lack of effectiveness of the labor hour in the past 50 years has caused for the construction industry to fall behind in the terms of major advancements while the other industries continue to expand and develop. Over time, the workforce landscape has also changed due to demographic and labor shifts, reducing the labor availability and consequently increasing the relative cost of a built environment. [1]
Lean construction is a robust approach that attempts to reduce waste in the construction projects, enhance performance and cut down cost for the industry and the society at large. [2] The concept first emerged in the 80's after gaining full acceptance in the West due to the major improvements displayed in the manufacturing operations and has its roots in Toyota's production management principles. [3]
Essentially, it aims to meet the same value creation criteria as the classical project management, meaning project delivery within time and budget and the production of a building according to the customer's requirements which concurrently contributes economically and socially to the area. The core novelty of this methodology, according to the Lean Construction Institute, comes from the replacement of monitoring results throughout the project execution with a solid planning phase and its continuous learn-improve loop. This should assure a certain level of system performance that sustains a reliable workflow and controllable outcomes. Another difference comes from the focus on minimizing waste and maximizing value at a project level and the use of concurrent engineering to prevent wasteful redoes.
This article showcases how implementing the Lean project practices in construction firms is a continuous process of learning and enactment, involving both internal and external actors. In this sense, it analyzes how the construction projects differ from the manufacturing operations and how that affects the Lean principles' migration. Subsequently, it discusses what limitations need to be considered before seeking to include elements of this methodology in the planning phase and ultimately what are some recommended directions and tools that can be included.
Its structure will take the reader through a brief history of the concept by presenting the Toyota story, the takes from it and the key differences between manufacturing and construction projects, the five traditional core principles of the Lean management and the waste sources in the targeted projects, implementation directions and limitations.
Contents |
Big idea
History
The concept of Lean stems from Toyota's Lean production, also known as Toyota Production System (TPS), which fundamentally applied precast construction principles to their manufacturing processes with the end goal of creating a leaner organization.
The Toyota Motor Corporation is a prominent player in the automotive industry, alongside with other widely known automakers such as Ford Motor Company and General Motors Company. What had made their production methodology an attractive research target is its massive impact on their profit, production output and sales volume and, consequently, their competitive advantage since it was founded.
The core concepts of TPS and their intercorrelation can be visualized in a structured manner through the TPS house, consisting of two pillars supporting a roof and a foundation. A good understanding of this is essential for developing and improving a lean system which will subsequently aid the company in removing waste and non-value adding effort, resulting in increased efficiency and maintenance of superior value and quality. [4]
-insert figure- [4]
As it can be observed, the procedure puts much emphasizes on the supply chain's speed. The underlining trend is to shorten the lead time by reducing or completely eliminating waste at each step in the process to produce the best quality, at a low cost, delivered on-time, while also enhancing safety and morale, principles known as QCDSM. [5] The techniques and procedures can be further researched on the indicated article in the Annotated Bibliography section.
Nonetheless, a successful implementation of TPS requires more than adopting and applying a set of tools, methods and techniques. It demands a pervasive and intensive cultural transformation at a company level and the development of a strong collaborative relationship with the suppliers, which will lead to quality materials being delivered consistently and productively. Toyota itself took decades to instill this, and its improvement is still possible.
Lean core concepts and principles
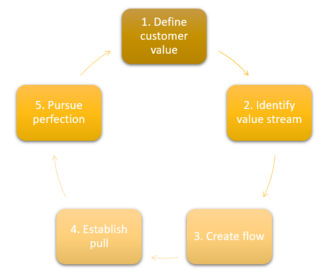
Toyota's methodology was subsequently disseminated and researched on by multiple authors, Womack and Jones proposing 5 core principles [6]:
- Value: defined through discussions with the ultimate customer. The complexity of identifying it increases in construction projects where there is not a single ultimate customer, but the construction client and multiple end customers alongside to be taken into consideration. Additionally, understanding the customer's needs implies both defining the end product or service and the preferred procedure for obtaining it.
- Value stream: analyzes three types of actions - activities that generate value, non-value adding activities which remain unavoidable due to current technological and production constrains and non-value adding activities that can be avoided.
- Flow: after reducing or completely eliminating waste, all the remaining steps of every process need to flow, so the product can be delivered from concept to client without delay or interruption. This involves eliminating batch and queue, and some recommended methods are restructuring the production, training the employees to be skilled in multiples areas and adaptive, delegating the workload to more than one asset.
- Pull: close to TPS's original pull system, this principle aims to tailor the production to the customer's requirements in terms of quantity and delivery time and save inventory space and materials in the process.
- Pursue perfection: through the application of the previous four principles in a continuous loop, the company can identify and reduce hidden waste, highlighting the need to adopt the Lean principles as an integrated part of the work environment.
The relation between these steps can be visualized in Figure 2.
In essence, Lean production takes place at both a strategic and an operational level. Strategically, it equips the organization with a structured approach of defining the customer value and identifying the value stream and, at an operational level, it provides multiple tools and practices for eliminating waste and integrating permanent improvement.
From manufacturing operations to construction projects
Fundamentally, transferring these Lean principles from the manufacturing production to the construction industry has its limits since the two domains operate on different grounds. The manufacturing processes are performed in a factory-controlled environment in which the production line follows a clear flow with easy to identify steps and constraints, there is a mass-produced with little variation output and minor fine-tuning from one project to another.
Whereas the construction projects involve a much higher level of complexity as each one of them presents a unique frame of physical, social and environmental traits. Moreover, the planning phase takes into account a more dynamic context, as opposed to the previously described isolated system, with often concurrent activities that need to be scheduled accordingly, with considerations of the weather and required resources. Time is an important constraint that does not leave space for errors in the allocation of different types of professionals as the construction is time bound and generates additional cost if the date for completion is overdue. The learning curve opportunity is also missed in most cases because the workers change frequently.
Another distinction between the two fields is the more considerable amount of waste generated by the construction industry. Traditionally, waste can be defined as non-value adding activities for the final output, meaning activities that consume time, money, material resources and manpower and bring no value to the ultimate customer.
Although the focus usually lies on the material waste, Ohno [7] described 7 types of waste. An overview is provided for understanding the full implications:
- Overproduction (unnecessary work): The production of a greater than necessary amount with the aim of building up the inventory or keeping the equipment running and attaining outstanding resource utilization. Done on a continuous basis, it causes quantity and quality problems, and it is difficult to identify without making a deliberate comparison between what is being produced and what is being sold and shipped. The usage of the mistake proofing approach and an extensive understanding of the production machines' capacities are recommended for addressing it.
- Time on hand/waiting (delays): Commonly described as idle time, it is easy to identify when the products are not being processed or moved, and it refers to the intervals spent waiting between processes/activities for different resources to become available. A possible solution is to create a sustainable flow.
- Inventories (storage waste): Stocking inventory causes monetary loss as the capital is being tied up and the space is occupied with materials susceptible to being inadequately stored on the site, deteriorated, stolen or vandalized. The issue stems from companies ordering more materials than required to fulfill an order as a direct result from an insufficient resource planning and/or uncertain quantity estimation.
- Transportation (materials movement): Mostly visible in the construction projects where resources need to be processed or moved inside of the construction site and it can be attributed in most of the cases to the layout of the working environment or to a lack of process flow, which results in multiple starts and stops in the transportation process and their correlated cost and waste of working hours, energy, space on the site. A method for addressing it is mapping a more optimized site layout.
- Movement: This type of waste stems from the way the resources and equipment are being placed around the site by the employees during the working hours which leads to more unnecessary motion, time and effort to perform tasks. The same inadequate site layout or the lacking work methods and insufficient equipment might be its root cause. An additional consequence is the increased rate of accidents and injuries and associated cost. Identifying and redesigning the jobs that produce this type of waste would reduce motion and cost.
- Over processing: It is described as additional processing of the product beyond the client's requirements which does not add further value from his perspective. A concrete example can be seen in the surface finishes. The waste of workforce potential falls under this category as well when the opportunity of making efficient use of their skills and knowledge is missed. Corrective measures consist of applying tools and methods such as the 5 whys and statistical process control or shifting the equipment used for construction.
- Defective products (unsatisfactory work): It occurs when final or intermediate products do not rise to the quality specifications and requires rework or the usage of poor quality materials. Reasons for which these rejects happen are numerous, some of them being improper integration between the design and production phases, loose planning and/or control, unqualified workforce. Mitigation directions include methods for their identification and removal such as the six sigma.
Lean construction
There are multiple perspectives in literature on what the Lean construction concept means, but this article will focus on the wide understanding that it is the application of the lean production principles and methods in the construction industry, with the Last Planner approach as a widely known example. Moreover, summarizing from the previous section, the two industries have different implications, therefore, a direct transfer of these principles is not possible without a considerable effort in changing the culture and management tools of the construction industry.
Similarly to Lean production, it promotes the timely delivery of projects, within the allocated budget and with the production of the demanded quantity and quality, and its techniques have the potential to remove unpredictability and enhance the ability to handle complexity and uncertainty.
Application
Although Lean construction is still in its early phase in terms of development, there is a set of principles that has been proposed, implemented and tested, and this section is going to cover them, together with widely known tools and techniques that have been successfully adapted or inspired from Lean production. Nonetheless, the aim is to obtain a lean culture, not the fragmented usage of tools and techniques to increase the project performance.
Implementation framework
The aim of the proposed approach is to facilitate the adoption of the lean methodology as a new business model, as described by Arbulu and Zabelle [8]. The absence of an entirely successful implementation case has at its root the intrinsically different business philosophy that Lean construction introduces. The clash with the existing business approach from the construction industry makes it challenging to perform the transformation and turns it into a business problem rather than an issue with applying tools and techniques.
An organization can typically be seen as a mix of core elements, such as culture, structure, values, people and systems. The transformation process targets this configuration with the goal of changing the current way the organization operates by redesigning the characteristics of these elements, so a lean project delivery and competitive advantage become possible. In other words, it takes the company from a current state to an envisioned future state.
As opposed to the wide top-down transformation approach that is most commonly adopted in which the leadership takes the decision of going Lean without solid and consistent stakeholder engagement, by applying it to more than one project at a time and setting the initiative to failure, a narrow bottom-up model will be described (Figure 3).
Contrary to the first impression, the construction industry holds a key advantage over the other industries when it comes to a sustainable transformation approach, that being its projects. They have the potential to simulate a viable environment for creating a new business model based on the opportunity they provide for designing and implementing temporary business systems. Inside the project setting, the organization can have a clearer view on the performance assessments and monitor what changes should be made on the structure, processes etc. Done on a continuous loop (by taking one project at a time), it will enable the disconnection from old systems, a more fine-tuned process flow, the provision of more well-aligned incentives and a solidly reinforced vision with the committed contribution of the leadership component.
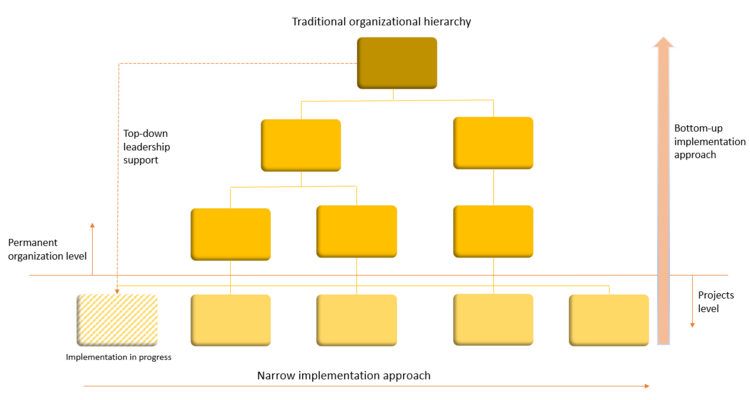
- Benefits of this model
- 5 success elements model
- additional aiding suggestions
- explanation + image of the 4 phases of change which depict how resistance is experienced by the different stakeholders
Tools and techniques
According to Picchi and Granja [9], so far, the construction industry has seen three implementation scenarios of Lean construction tools:
- Scenario 1: Fragmented tools application and lack of integration
- Scenario 2: Integrated tools application on the job site
- Scenario 3: Company-wide lean transformation
Therefore, sticking to the goal of creating a leaner organization is vital. An account of tools and techniques will be provided in the following table:
- A table with the most common tools will be provided here, together with brief descriptions and what area of the project lifecycle they are operating at (and what value can they provide)
Limitations
Whereas the implementation of Lean construction practices can bring visible benefits in the construction industry and aid in achieving sustainability, there are a number of hindrances in the process. The most notable ones are the unwillingness of the project partners to embrace change, the lack of knowledge about the Lean construction practices, their complexity in itself and the absence of policies and legislation to support them. Other reasons involve the extensive knowledge and amount of time required to adopt them, the lack of an expert for directing their implementation and financial constraints. [10]
More specific research focuses on how a proper implementation is constrained by the level of commitment from the senior management's side as they have a high impact on the organizational culture and are also responsible for selecting the supply chain assigned to the construction projects. An adequate supply chain for this purpose is one trained in Lean construction. [11]
Annotated bibliography
- Joy Ong, Low Sui Pheng, Lean Construction Implementation, 2021, pg 45-74: details about the TPS house techniques and procedures
- Gao Shang, Sui Pheng Low, From Lean Production to Lean Construction, 2014, pg 27-48:
- Roberto Arbulu and Todd Zabelle, Implementing lean in construction: how to succeed:
References
- ↑ Lean Construction Institute, Lean Construction Defined
- ↑ Richard Hannis Ansah, Shahryar Sorooshian and Shariman Bin Mustafa, "Lean construction: an effective approach for project management", 2016
- ↑ Joy Ong, Low Sui Pheng, Lean Construction Implementation, 2021, pg 45-74
- ↑ 4.0 4.1 Gao Shang, Sui Pheng Low, From Lean Production to Lean Construction, 2014, pg 27-48
- ↑ Liker Jeffrey K, The Toyota way: 14 management principles from the world's greatest manufacturer, 2004
- ↑ James P Womack, Daniel T Jones, Lean thinking, 1997
- ↑ Ohno T., Toyota production system: Beyond large-scale production, 1998
- ↑ 8.0 8.1 Roberto Arbulu and Todd Zabelle, Implementing lean in construction: how to succeed
- ↑ Fhivio Augusto Picchi, Ariovaldo Denis Granja, Construction sites: Using lean principles to seek broader implementations, 2004
- ↑ Olusegun Aanuoluwapo Oguntona, Clinton Ohis Aigbavboa and Gloria Ndalamba Mulongo, An Assessment of Lean Construction Practices in the Construction Industry, 2019
- ↑ Ruan Ximing, Ochieng Edward, Zuofa Tarila and Yang Miying, An appraisal of lean construction project delivery application of lean construction, 2016