Location Based Scheduling
5.1 Article Type 1: Explanation and Illustration of a Method
[The articles are expected to adhere to the following structure:]
- Big idea: describe the tool, concept or theory and explain its purpose. The section should reflect the current state of the art on the topic
- Application: provide guidance on how to use the tool, concept or theory and when it is applicable
- Limitations: critically reflect on the tool/concept/theory. When possible, substantiate your claims with literature
- Annotated bibliography: Provide key references (3-10), where a reader can find additional information on the subject. Summarize and outline the relevance of each reference to the topic.
(around 100 words per reference). The bibliography is not counted in the suggested 3000 word target length of the article.
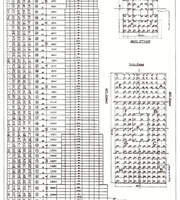
The Location Based Scheduling (LBS) method is developed to help the project managers in the construction industry with workflows and planning. The most common method in time and resource planning in construction is still today the Critical Path Method (CPM). CPM has been the most dominating method since it was introduced in the late 1950. It has been proved an effective method for time and resource planning of projects. Thus, some critics have been raised about the CPM-method in relation to construction projects, as it is not sufficiently supporting construction management during execution and not to create a continuous and thus economical flow of resources. The LBS method is developed for the planning and management of workflows and could therefore be expected to be a viable alternative to CPM. The construction industry struggles with the subsequent delays and budget overruns and hopefully the LBS can help the industry to meet these challenges. The main philosophy about LBS is to create a tact in the construction projects. The different tasks in the projects need to go along in the same flow to create a constant progression without wasting time.
The Location Based Scheduling (LBS) method is visualized by a graphical tool based on a technique developed by Karol Adamiecki in the early 20th century. [1] Karol Adamiecki developed a schedule tool named harmonogram. This tool includes the location as a key element in the scheduling, in contrast to the Gantt Chart. There has been historical examples of the application of Adamiecki's concept. The construction work of The Empire State Building was one of the first projects that used location as main unit of analysis. The results were ground-breaking due to the fact that around 380 m2 were build per day of construction. The 102 levels were completed in 18 mounts with a significant low number of accidents for its date and under the initial estimated budget. [2]
Contents |
About Location Based Scheduling
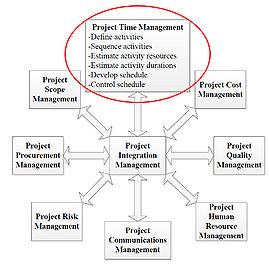
Location Based Scheduling is placed in the realm of Project Management. The main focus of the article is to describe LBS, a Project Time Management tool, used by project managers in the construction industry. As shown in Figure 2 from Project Management Body of Knowledge [3], Project Time Management is a crucial part of a project managers scope.
The overall idea in LBS is to create a schedule that can be used as followed: [4]
- The schedule should ensure that the main goal of the project is archived within the time-, resource,- and qualitative framework applicable to the project.
- The schedule works as an overview map of the project, showing the planned way from start to end.
- The schedule serves as a basis for analysis and decisions regarding choice of production methods, materials and supplies and other resources.
- The schedule serves as a communication tool to convey the structure of the production progress: what should be done when - which resources should be used - in which order should the tasks be carried out.
- The schedule serves as an foundation for running following-up on the produced part of the project. Therefore, it can be used as a basis for identifying possible deviations and the consequences of these.
LBS is based on the fundamental planning elements: activities, resources and the link between them. In addition to this, LBS also uses: locations, critical room to manoeuvre, location based activity links and resource flow to name a few. A central part of LBS is to create the right flow through the project. The right flow ensures that the resources in the independent activities flows smooth through the different locations of the project. A geographical location of the activities in the project is added in LBS. This makes it possible to identify where and when the different tasks should be carried out. Furthermore, it creates the possibility to draw the LBS-methods typical "time/place-diagram" or "Flow-line diagram" , which is the LBS-methods graphical representation. [4]
Flow-Line Method
Professor Shlomo Peer from Technion-Israel Inst. of Tech., Haifa, Israel, was one of the first contributors to the flow-line method. This method constituted a new way of displaying and handling activities in construction projects. One of Shlomo Peer's main points [5] was that scheduling and control in the construction industry should aim to complete the projects in the shortest possible time that is compatible within the financial limitations. The fastest time is not necessarily the most economical, nor is the relationship between available resources and construction time linear. Based on this statement, Shlomo Peer produced a construction planning process for the location-based methodology. The step is as follows [5]:
- Break down the project into constituent component processes.
- Divide realization of these processes between adequate production crews.
- Define technological connections between the crews and activity categories.
- Decide on the flow line that should dictate the progress of the project given financial or resource limitations.
- Estimate the resulting construction time and decide on the number of production units that should be employed in parallel.
- Balance the progress of noncritical flow lines with that of the chosen critical one, aiming to achieve working continuity.
- Within practical limits, check the possibility of shortening construction time by introducing planned breaks in continuity or changes in crew size.
- Analyze the entire process in terms of time and duration of activities and produce a plan.
When the eight steps above is carried out, one can start producing the flow-line diagram.
Flow-Line Diagram
The flow-line Diagram is the graphic tool in LBS. The different activities are illustrated as lines in a XY-coordinate system. The Y-axis in the flow-line diagram is divided into the physical locations of the project. The X-axis indicates the timewise progress of the project. The activities depicted as lines in the coordinate system. The combination of axis displaying time and locations, gives an overview of where and when activities has to be carried out. The duration of each activity is seen at each location by the length of the flow-lines. The activities can be scheduled in parallel to one another, so there in this manner will be obtained an even flow and a stable rhythm of the construction. This results, that there are no days with many activities and other days with very few activities. A rapid and short activity has a steep line, while a slow and time-consuming activity has a flatter line. In Figure 3, activity 1 and 3 have a duration of one day, and activity 2 a duration of eight days.
To create the flow-line diagram, the locations of the project has to be decided.
Identifying the locations
Identifying the locations of the project is a central element in LBS-method. The projects hierarchical location structure (e.g building - block - stairway - apartment) is shown in the flow-line diagram. Each activity in the schedule is planed in relation to a location. To decide the hierarchical location structure a Location Breakdown Structure (LBS) is performed. This hierarchical breakdown structure can be compared with the Work Breakdown Structure (WBS), used in activity-based scheduling. The logic behind LBS is that the sum of locations on a lover level counterbalances a location on a higher level, as shown in Figure 4. As activities can correspond to different levels of the hierarchy, one needs to make the following considerations when determining the location hierarchy:[4]
- What is the smallest site where repetitions will occur in the project?
- What is the smallest locality in which material resources for current activities can be distributed?
- Which is the largest locality in which there is only room for the execution of the current activity, i.e., which can not take place other activities at the same time?
E.g. preparation of the construction site will in Figure 4 corresponds to the building level in the hierarchy, whereas installation of kitchens would correspond to the apartment level in the hierarchy.
Optimization using flow-line diagram
When the different locations are identified and the internal hierarchy established, then the activities can be plotted. The optimization is generated through resources and activity-links. The activity-links helps reducing the length of the project, as the graphical representation in the flow-line diagram secures that multiply activities can be scheduled simultaneous. This without causing an accumulation of resources at a certain location. Other traditional scheduling methods and tools do not ensure this visual overview when the processes "squeezes together".
Location-Based activity-linkages
In addition to the traditional CPM-linkages, see Figure 5, LBS have further linkages in connection with the locations which is chosen for the schedule. These linkages is the essential in LBS. There is five different types, of levels of location-based activity-linkages:
- Activity-linkages between activities in the same hierarchy
- Activity-linkages between two activities in different hierarchies
- Internal activity-linkages
- Activity-linkages between two activities which creates a location slack
- Activity-linkages between two locations
Types of activity-linkages | ||
---|---|---|
Types of activity-linkages | Description | Figure |
Traditional CPM-linkages | The four types of activity-linkages in CPM | |
Level 1 - Activity-linkages between activities in the same hierarchy | Level 1 determines when an activity is to start, compared to the previous activity. The previous activity should be finished in the current location, before the next activity can begin. Figure 6 shows that Activity 2 can not start before Activity 1 is completely finished at this location. | |
Level 2 - Activity-linkages between two activities in different hierarchies | Level 2 differs from level 1 as the two activities are associated with different hierarchies. It is seen from Figure 7 that Activity 1 is assigned hierarchy "Block" while Activity 2 belongs to "Apartment". A link between these activities result that Activity 2 at the earliest can start when Activity 1 is completely finished in the hierarchy it is affiliated with. | |
Level 3 - Internal activity-linkages | Internal linkages activity is the binding location which determines the order in-house, in an activity. E.g., the order of an activity is performed, with respect to the locations of the project. Figure 8 shows that Activity 1 has an internal activity-link. First stairway A and B, then stairway D, back to stairway C, and then stairway F and E. | |
Level 4 - Activity-linkages between two activities which creates a location slack | This activity-link is use when it might be necessary to create a slack between two locations. For example, concrete prefabricated construction and outfitting. For safety reasons, there should always be a slack of at least 2 floors between installation of concrete and interior works. Figure 9 shows that Activity 2 at the earliest begin when Activity 1 is completed on the 2nd floor of staircase A. | |
Level 5 - Activity-linkages between two locations | The last level of activity-links are links that are independent of the order location. This links allows the user to select which locations to create links between. Figure 10 shows that Activity 2 can not start in stairway A - apartment 2. TL before Activity 1 is completely finished with apartment 2. TR in stairway C. This allows two alternatives for Activity 2. Either the activity can be divided so that there is a break in the activity after finishing apartment 2. TR in stairway A, as shown in Figure 10. Alternatively, the activity can start 1 day later, as shown in Figure 11, to achieve a continuous operation. |
Control of resources and linkages
Figure 12, 13, 14 and 15 shows a schedule where three different activities are interdependent. Figure 12 shows that following activities at the earliest can start when the previous activity is fully completed - a standard "Finish-Start" CPM-link (see table above). Figure 13 shows another situation. Here, the following activity can start immediately after the previous activity has finished the actual location, which in this case is a stairway. Note the difference in the length of the schedule between the two schedules.
The schedule has been optimized by changing the links from standard CPM-links to LBS-links. It is possible to optimize the schedule even more, due to the overview a flow-line diagram creates. Figure 13 above shows that there are multiple days where no activities are performed on some of the locations. There a two clear unused areas in the schedule. There is a big gap in Block 2 between Activity 1 and 2. Furthermore, a big gap between Activity 2 and 3 in Block 1 is obvious.
The schedule is further optimized by:
- adding resources to Activity 2 which results in a earlier end date. Thereby, Activity 3 can start earlier.
- deny Activity 3 a continuous working procedure. Thereby, Activity 3 starts as soon as Activity 2 is finished with a stairway.
The two initiative is visualized in Figure 14
Using the flow-line diagram, it is quickly determined what the most appropriate changes should be, in order to optimize the schedule. Both optimizing initiatives removes the holes in the schedule. Regulating the resources does not necessarily mean increasing staffing. By minimizing staffing in Activity 3, a similar optimization of the schedule is archived, without the work process becomes a discontinuous operation. This is called "synchronize" [4] activities. Figure 15 illustrates this. Note the length of the schedule now is below six days. The lenght of the schedule was 13 days in Figure 12.
LBS/Flow Line Diagram compared with CPM/Gantt Chart
CPM/Gantt Chart is the most used scheduling method in Denmark. The method was developed in the late 1950 to the american navy to planning of complex projects. It was fast adapted by the construction industry, due to its practicability in relation to construction projects. CPM only needs two types of input: the sequence of the activities and the length of them. The Gantt Chart creates a fast overview of a project but has it limitations compared to the flow-line diagram. [6] [7] An example of this is showed in the two figures below.
In Figure 16 is the same construction project illustrated in both a Gantt Chart and a Flow Line Diagram. Dependencies between the activities are not shown in this example but are defined in the underlying data. Only a minor portion of the schedule is illustrated in the Gantt chart. Similar activities are typically copied and repeated for each location in a construction project, which tends to make the CPM schedules elaborate. CPM schedules commonly comprise over 1000 activities, making them difficult to manage and communicate. In the flow-line diagram, similar activities are collected in tasks and displayed as a single line over multiple locations. [6] The red circles illustrates where the flow-line Diagram's extra input in form of locations makes a difference. The red circle on the left indicates vacant locations where no work is performed at a given time, while the red circle on the right indicates a location in which several activities are performed simultaneously. Working at the same time and in the same location negatively affects the work of construction crews because technical constraints are not respected. Logical dependencies that have to follow in succession fail. The location-based schedule illustrates areas not utilized for production (left red circle), allowing the project manager to exploit vacant areas of the build site by moving work crews to those locations. [6]
Current State of Art
Today, Location Based Scheduling is carried out by more and more contractors. Advanced software is used to create the most effective and efficient schedules as possible. The advantages generated from the LBS-method gets bigger when it is combined with BIM (Building Information Modeling) tools. To minimize the numbers of errors many projects are today designed in 3D BIM. These 3D-models are interconnected with the Location Based Schedules to create the best possible overview tool for project managers in construction. The construction sequences can be reviewed as a series of problems using 4D BIM, enabling users to explore options, manage solutions and optimize results. Furthermore, an extra dimension can be added. 5D BIM interconnects 3D models, time schedules and cost-related information to create the total overview of the construction projects. The LBS-method is applicable in all kinds of construction projects. Thus, it might be a more challenging task to make the right location breakdown in e.g. a bridge project than a apartment building project. [8]
Limitations
Critically reflects
LBS implies a new, or preferably unfamiliar, scheduling method which requires a new approach to scheduling and it involves new conceptions. For example, LBS requires the definitions of locations and there are different more or less appropriate ways of dividing the project into locations. One aspect is about finding a sufficient level of details required for the planning, scheduling and control of the project. It is possible, but very inconvenient, to change the level of detail once the scheduling has commenced. Another difficulty experienced in one of the cases concerned the definition of different kinds of locations, e.g. how to handle ground works in relation to the locations that are connected to the actual building. [8]
Another disadvantage with the LBS-method is the NOGET MED MANGLENDE VISNING AF KRITISK VEJ !
References
- ↑ Martinez, Natalia Rodriguez (2013) ‘Optimization of Flowline Scheduling vs.Balanced Resources and Task Continuity,
- ↑ Sacks, R. & Partouche, R (2009) ‘Empire State Building Project: Archetype of "Mass Construction", Journal of Construction Engineering and Management, 136(6), 702-710.
- ↑ 3.0 3.1 The Project Management Institute (2008) ‘A Guide to the Project Management Body of Knowledge (PMBOK(R)) Guide,
- ↑ 4.0 4.1 4.2 4.3 Andersson, N. & Christensen, K. ‘Location-based Scheduling: "Vurdering af LBS-metodens anvendelse i byggeprojekter",
- ↑ 5.0 5.1 Peer, S ‘Network analysis and construction planning, Journal of the Construction Division-ASCE, 100(NCO3), 203–210.,
- ↑ 6.0 6.1 6.2 Büchmann-Slorup, Rolf (2012) ‘Criticality in Location-Based Management of Construction,
- ↑ Rezael, A. (2015) ‘Location Based Scheduling In The Form Of Flow Line and Its Comparison to Cpm/Bar Chart Scheduling,
- ↑ 8.0 8.1 Jongeling, R. & Olofsson, T (2006) ‘A method for planning of work-flow by combined use of location-based scheduling and 4D CAD,