Integrated Design Process (IDP)
The Integrated Design Process (IDP) is a high performance, holistic, method that mostly appear in conjunction with product or construction projects. It commonly refers to a process where the design is done in close collaboration, and with consideration for, the other disciplines from the start of the design phase. It is a process where the different design teams/disciplines (for example: Architect, Structural engineers, Building Services engineers, etc.) work closely to make sure the all of the aspects of the design is adapted to make it as high of quality and performance as possible. For this reason, the term “Whole building” is often seen in the context of IDP used in the construction industry. All of the subjects collaborate and focus on making the construction with each other and the users in mind.[1] [2] Compared to the traditional design process, where one team wins the offer and then outsource the other technical tasks to different teams after a design is made, the teams interact on the same authority level. They discuss issues and opportunities to best meet the client’s requirements. The goal is to be more efficient and ensure that the quality is not jeopardised in one or more decisions, and that the different designs are integrated for its overall purpose. [3]
IDP done successfully identifies slippage and problems before the production phase and saves the project cost, enhances quality, optimizes operations in production and after and facilitates for development of sustainability in contraction.
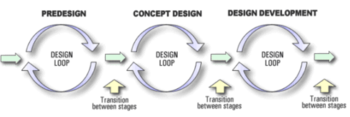
Contents |
Definitions
“Integrated design process is a process in which multiple disciplines and seemingly unrelated aspects of design are integrated in a manner that permits synergistic benefits to be realized. The goal is to achieve high performance and multiple benefits at a lower cost than the total for all the components combined” – R.M. Reffat, A.M. Radwan & M.A. Eid, (2012) [5]
Integrated design describes a design that has incorporated the different disciplines needed in a product, the operators and the client’s vision as the primary parameter for the design.[6]
“Concurrent Engineering (CE) is a systematic approach to integrated product development
that emphasizes the response to customer expectations. It embodies team values of cooperation, trust and sharing in such a manner that decision making is by consensus, involving all perspectives in parallel, from the beginning of the product life cycle” - Bandecchi, M., B. Melton and B. Gardini (2000).[7]
Theory/Basis of concept
The Integrated Design Process could be seen as an offspring or underlying category of the Integrated Process or Integrated Management. It is based on the same theory to enhance the collaboration and coordination of a program or project. In a program/project management view “Integration requires making choices as to where to concentrate resources and effort, anticipating issues and dealing with them before they become critical, and coordination work for the overall success (…)”. [8]. To fulfil these actions, the stakeholders must have clear contractual requirements and the project/program team must have a well-defined, common goal, not individual targets. The success of the project must be priority in every decision, this means that trade-offs and sacrifices must be made between teams, for the projects best. Every discipline must concede to work for the project’s success, not the glory of the discipline. This will give the needed basis to complete an integrated design process.
In project management, a synergy between disciplines could integrate seemly unrelated aspects to create high preforming and innovative benefits and solutions. In a program it would work similar. The different projects come together to achieve a common goal and long-term benefits, this is also the goal of the IDP. This requires coordination and collaboration between the projects and high preforming, overlaying management.
Concurrent Engineering (CE) is a concept that was introduced in the assembly line industry and are now used in the product development cycle across industries. The name implies the scope of this type of approach. Instead of handing down the work in a hieratic way, or collecting resources from different locations, it is concentrated and concurrent. This is a method that is more used than ever due to the technological development.[9] The possibility of concentrating knowledge and information without moving to the same location has facilitated and enhanced the way CE, and many other method, can be used.
CE is in later years been implemented in the IDP in an increasing degree. This method is called Integrated Concurrent Engineering (ICE) and is developed by NASA. It includes the same basis as IDP, but takes the collaboration aspect even further. In ICE, all the disciplines sit together throughout the planning.
Method
A project is divided in several phases, depending of what kind of project it is, but an overview of that is the four phases of the generic life cycle structure: Initiation, Planning, Execution and Closure of the project. The Integrated Design Process is mainly part of the Planning phase. Underneath that we often have an Early Design Phase and a Design Phase. Here the different disciplines have to work together with close communication and collaboration to meet the stakeholder’s requirement in the best possible, and sustainable, way.[10]
When the early design phase is started, the different disciplines meet to strategize how to fulfil the requirement within the contractual boundaries. They have to agree on the priorities in order to ensure a common philosophy and the best solutions for each other, the client and the operators of the product. After the baseline is determined, the Design Phase can start. One of the most important aspects of the IDP is to have frequent contact with the disciplines to discuss decisions and adaptable solutions. This can include daily/weekly meetings, a common work platform, dedicated project offices, LEAN-based platforms or other collaboration platforms.
Benefits
- Shorter project time
- Higher quality
- Innovative
- Knowledge sharing
- Lower costs
- Sustainability
Creating a synergy of specialist can open for new unconventional possibilities that better solves the objectives of the project/program. The schedule is one of the biggest focuses in today’s management. The disadvantages of falling behind are many and could be crucial for success. Integrated Design Process and its aspect of simultaneous collaboration will in get the product to the market more rapidly and not on the expense of quality. In bigger projects or programs, such as infrastructure projects or the Olympic games, you may see the benefits distinctly – The planning will decrease drastically if the projects/program groups have the same vision and are coordinated between themselves, rather than that the first in a hierarchy plan its task and sends it down to the next team.[11]
The quality of products, from the result of an IDP, is also higher than the ones that comes from a traditional design process. The integration between components ensures that you get better handling and function. The components are adapted to each other and a result of collaboration. In a laptop it will mean better performance, longer life, etc. In a construction project it means that you might have higher floors, better space management, or could utilise the structural parts with the technical installations.[12]
The solutions and results are more innovative – When consultants/specialists within different fields of technology have close collaboration and a common vision will it often result in a solution that is unconventional or deviates from the standard. When they adapt to each other the have to come up with solutions that may not have been use before and that could help further the development of fields. The constant feedback across teams and allows lessons to be learned.[13]
As stated, the time span is shorter when implementing IDP in a project due to the collaboration in the planning phase. In addition to that aspect, the production phase will also shorten. The well planned and integrated design will make production go smoother and lessen the time of fall-backs from bad planning or impossible practical execution. The production team or company will have a greater understanding of the project and how to execute it. They will then have more time to develop other projects and production.
In general, the production/execution is the most expensive phase in a project. The planning often demands a lot less staffing and resources. See figure 1. In addition, as figure 2 shows, the cost of changes increases drastically throughout the progress of the project. For this reason, a longer planning time, where the production team is involved could be highly beneficial and cost effective.[14][15]
Challenges
- Possible long planning phase
- Conflicts
- Urge to start production
- Different level of competence
- Shorter production
Even though the benefits are many and substantial, it could occur meaningful challenges. In some cases, the planning phase can be longer than in a non-integrated process. This is depending on the structure of the design phase and the amount of communication. If the project exceeds with these factors though the integration and the extent of cooperation this needs is neglected, the project might go more rapidly than with a IDP.
IDP requires abundant collaboration between various teams. Development of social crash or conflicts is consequently a risk that might have a big impact on the result and the integration. Conflict management is therefore an essential part and focus. Active conflict management can enhance the benefits of IDP by providing better collaboration and decision-making. If dealt with poorly, it can resolute in lack in progress and delays, motivation and diminishing quality. (10)[16]
The urge to start production is a common factor in some industries. The lack of tangible progress can create stress and demotivation for some people, and generate hasty production. This undermines the purpose of the IDP and prohibits the potential benefits. Hence it is important that all participants recognise the target and share the mind-set before evaluating the time of production.
In most design process, teams with divergent competence and experience appears. The risk of hiring teams with lower levels of competence will bring down the quality and might, upon replacement, lead to loss of finances.
As established, with shorter production time, the company producing will have increased time for new projects. In some cases, e.g. smaller establishments, the reduced project time might make it more challenging to be profitable. It could result in periods without projects and payment.
Contracts
A strong contractual agreement in the project is often a positive way to start of the integrated design process. To include processes and stakeholder responsibility ensures the commitment from the different parts. This commitment is essential since the Integrated Design Process relay on the continues collaboration and participation of the different stakeholders and their perception the targeted Level of Development (LOD).
As stated, to achieve success in a IDP it is essential with a shared vision, close collaboration and consistent communication. Due to the demand of the IDP and the difficulties of implementing new process in an already established and incorporated work-flow, is it a good idea to include the processes included as a project deliverable in the contracts. Without it, the project teams are likely to fall back to the comfort of routine. This would counteract the idea if IDP.
A process owner should be assigned to own the responsibility of the process, define the Key Performance Indicators (KPIs), follow up on the process as it progresses and make sure that the teams are aligned.
Appliance
Integrated design process (as a term) is mostly used in the construction industry, but is also seen in the aeronautics and space industry. Nevertheless, the basic idea and method of IDP can be applied in every design phase that includes more than one discipline and seeks high quality and performance of a product. From designing software, buildings or even student development projects. Coordination, collaborating and integrating disciplines can befit every project that has high demands.
In order to apply IDP successfully, the different disciplines must be organised with a flat structure. The hierarchy in a design phase complicates and decreases the progress of the integration and hinders the knowledge sharing.
If it is neglected in a IDP based project, the project falls back in time and prohibits the full potential. It will corrupt the vision and purpose of the project and not meet the requirements and demands of the client.
The theory of IDP can also be applied in Program Management. The responsibilities and disciplines in a projects are then moved to the owners of the various projects in the program. Coordination projects and possibly integrating them would give the same possible benefits as in a project. In addition, it can benefit the long-term vision of the program.
Bibliography
IEA SHC (2003). Task 23 – Integrated Design Process Guide - This report provides extensive insight into the practice and theory behind IDP.
Project Management Institute, (2008). A Guide to the Project Management Body of Knowledge (PMBOK® Guide), Fifth Edition. Publisher: Project Management Institute. - This book gives great insight in the theory and application of it in project management.
Natural Resources Canada, (2016). The Integrated Design Process - The Canadian guide of practical usage of IDP.
References
- ↑ [1] Public Service and Procurement Canada (2018). Integrated Design Process.
- ↑ [2] Project Management Institute, (2008).The Standard for Management - Second Edition. Publisher: Project Management Institute. Page 71
- ↑ [3] Moe, Kiel, (2008). Integrated Design in Contemporary Architecture. Publisher: Princeton Architectural Press.
- ↑ [4]IEA SHC, Task 23 accessed: 08.02.18
- ↑ [5] R.M. Reffat, A.M. Radwan & M.A. Eid, (2012). A utilization approach of BIM for integrated design process. Journal: Ework and Ebusiness in Architecture, Engineering and Construction - Proceedings of the European Conference on Product and Process Modelling 2012, Ecppm 2012 — 2012, pp. 535-541
- ↑ [6] Public Service and Procurement Canada (2018). Integrated Design Process.
- ↑ [7] Debackere, Koenraad, (undated). Concurrent Engineering. [Online]
- ↑ [8] Project Management Institute, (2008).The Standard for Management - Second Edition. Publisher: Project Management Institute. Page 71
- ↑ [9] Debackere, Koenraad, (undated). Concurrent Engineering. [Online]'
- ↑ [10] Project Management Institute, (2008). A Guide to the Project Management Body of Knowledge (PMBOK® Guide), Fifth Edition. Publisher: Project Management Institute. Chapter 2.4.1.
- ↑ [11] IEA SHC (2003). Task 23 – Integrated Design Process Guide. [Online].
- ↑ [12] IEA SHC (2003). Task 23 – Integrated Design Process Guide. [Online].
- ↑ [13] Natural Resources Canada, (2016). The Integrated Design Process. [Online]
- ↑ [14] Project Management Institute, (2008). A Guide to the Project Management Body of Knowledge (PMBOK® Guide), Fifth Edition. Publisher: Project Management Institute. Chapter 2.4.1.
- ↑ [15] Natural Resources Canada, (2016). The Integrated Design Process. [Online]
- ↑ [16] Project Management Institute, (2008). A Guide to the Project Management Body of Knowledge (PMBOK® Guide), Fifth Edition. Ch. 9.4.2.3. Publisher: Project Management Institute. [Online].