4D-Planning in Construction Management
(→Site management) |
(→Quality of schedule) |
||
Line 46: | Line 46: | ||
===Quality of schedule=== | ===Quality of schedule=== | ||
− | Undeniably, 4D planning enhances the overall quality of the schedule and consequently of the project. The schedule consists of numerous activities that their relationship and construction sequence is not always well planned <ref name="value"></ref>. Missing activities or relationships between them can be tracked through simulations, verifying the reliability of the schedule and [[Minimizing Risk and Uncertainties in Construction Projects]]. In addition, the construction progress is swiftly identified, with a direct and visual method, instead of the traditional bar charts <ref name="acep"></ref>. Hence, the productivity can | + | Undeniably, 4D planning enhances the overall quality of the schedule and consequently of the project. The schedule consists of numerous activities that their relationship and construction sequence is not always well planned <ref name="value"></ref>. Missing activities or relationships between them can be tracked through simulations, verifying the reliability of the schedule and [[Minimizing Risk and Uncertainties in Construction Projects]]. In addition, the construction progress is swiftly identified, with a direct and visual method, instead of the traditional bar charts <ref name="acep"></ref>. Hence, the productivity can be improved. Finally, 4D BIM is considered as an additional management asset that offers an innovative promotional advantage comparing to other companies, for instance, in tender periods. |
==Challenges and Barriers== | ==Challenges and Barriers== |
Revision as of 22:21, 21 June 2017
4D-Planning in construction management is a method of visualizing the schedule [1]. This method is based on Building information modeling (BIM) which is a process that came to revolutionize the work -flow of the Architecture, Engineering and Construction (AEC) Industry. The fourth dimension of BIM focuses on linking the 3D geometrical models with time and scheduling. The visualization of the schedule using 4D planning methods if combined with other scheduling methods facilitates communication and decision making throughout planning and construction phase. The opportunities of 4D planning also improve procurement management and spatial constrains reinforcing and supplement the location-based scheduling. Another approach that gains more and more ground is the linkage of 4D BIM with the Lean construction practices [2]. This article investigates the values and benefits that 4D Planning intends to create simultaneously with the barriers and constrains that need to be addressed to minimize the cost and time of construction projects and maximize the benefits and effectiveness; how 4D planning supports some of the most common scheduling practices is also a matter of interest.
Contents |
Framework
Background
At the moment, more than half of construction projects overcome their agreed time schedules deadlines [3] while using the conventional means of planning. Nowadays AEC Industry is in a transitional phase, where it tries to shift from "2D-based documentation and staged delivery processes to a digital prototype and collaborative work-flow" [2]. The enhancement of CAD capabilities intends to link design information with business processes [2]. Building information modeling is a digital representation of physical and functional characteristics [4] and a key process for this achievement. BIM process consists of seven distentions that designate a more efficient way not only to design but also to plan, construct and manage buildings through a holistic approach and model-based information. Figure 1. shows the 7-dimensions of BIM.
4D-BIM Context
The rapid evolution of technology in conjunction with the high demand for an efficient time and cost planning of buildings, introduces BIM as one of the most promising implementations concerning Time management in AEC industry. 4D-Planning is a rising technique that combines the 3D CAD models with construction activities [5] in order to adequately bridge the gap between design, construction and scheduling. It is quite common by using the traditional methods of planning like Gantt Chart and The Critical Path Method (CPM) to address difficulties regarding synchronization either with the design or with the real-time construction. BIM supports such methods of planning reinforcing the reliability of the schedule and creating accurate and detail Work Breakdown Structure (WBS) based on one source.
Three approaches have been developed utilizing the contribution of BIM in planning. The first is related to the association of time in the already existing building elements during design phase. More specifically, this can be achieved by specifying the construction phase of each individual element creating a construction sequence that can be easily visualized by virtual simulations of schedule [2]. Second, analysis tools can be used incorporating BIM components and construction method information with the view to enhance the activity sequence [2]. The last approach, concerns the association of 4D- planning with the Lean construction and especially in the Last Planner System [2].
Analysis
This section investigates the benefits and challenges of BIM implementation focusing on planning and scheduling. In addition, it explains how 4D-BIM affects and improves some of the most common planning techniques, such as Location Based Scheduling and The Last Planner System in Construction Projects
Advantages and Benefits
The concept of Building Information Modeling is already in use from the AEC industry especially in design and construction sector, for some time now. However, for the Time Management sector is a relatively new concept. How BIM achieves to improve the project planning can be divided in the following subsections.
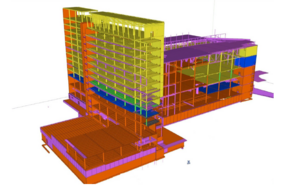
Communication
The visualization advantage that 4D- Planning provides, makes it one of the most important tools in terms of efficient communication among all the project stakeholders [2]. Exploiting the possibilities of capturing both temporal and spatial aspects of a schedule, contributes to an insight understanding of the time flow, minimizing misunderstandings. Furthermore, the different installation sequence can be easily simulated, creating animations [2]. Consequently, given the fact that a picture paints a thousand words, 4D tools can significantly enhance decision making as it becomes easier to identify and evaluate the currents situations. The jobsite coordination is also improved through visualization as it is quite common in the AEC industry, different terminologies to be used. A common language through models and pictures may reduce these kinds of inconsistencies. Owners and building users adequately understand the project milestones and the construction plans [7] . An example [6] can be found in Figure 2. that shows a visual representation of a BIM-based schedule using color coding, where Orange = completed/installed, blue = this week, green = next week, yellow = scheduled, in over two weeks, purple = scheduled.
Site management
Site logistics is undeniably a challenging sector in construction management. 4D-Planning let planners efficiently manage the site area. More specifically, the locations of large equipment, trailers and other, either permanent or temporal facilities can be evaluated through the model-based schedule [2] [7]. Through the connection of the 3D models with the construction activity schedules, the manager is able to identify the critical spaces and sequencing requirements [7] . Figure 3. shows how the building and the site can be simulated in order to ensure site access, trades stacking and storage locations [8]. With a site-space conflict analysis, the special constrains are identified and activities that my occur the same time in the same place can be avoided [2].
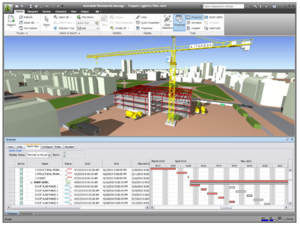
Time and cost
If 4D-planning is successfully used, this tool is proved to be a valuable asset in terms of time and cost. It can reduce the time spend in rework [5] as the model can aggregates all the necessary information in one source and identify the unforeseen time conflicts beforehand minimizing the cost [8]. Therefore, 4D BIM is directly pertinent and imperative condition for 5D BIM which links the cost estimation. The changes during the construction can be quickly incorporated in the model and then simulated for analysis and review [8].
Procurement
The Material requirements planning and management, demand an accurate time schedule in order to achieve a successful material purchasing and tracking. Using a four-dimension BIM model, the related task schedule and the building elements are linked to predict the dates when elements have to be on site [7] . Apart from planning ahead the procurement method, tracking the status of services and materials by using additional parameters to the elements, associates the design with the procurement activities [2]. As a result, the impacts in the construction process due to procurement delays can be visually identified and the time and cost consequences can be forecasted.
Safety management
Human resources play a vital role in projects [8] [2]. A proper schedule as it has already mentioned, allows 4D simulations to influence the spatial constrains for people and protect them from possible accidents. The critical unsafe areas are recognized creating a safe environment for the workers.
Quality of schedule
Undeniably, 4D planning enhances the overall quality of the schedule and consequently of the project. The schedule consists of numerous activities that their relationship and construction sequence is not always well planned [5]. Missing activities or relationships between them can be tracked through simulations, verifying the reliability of the schedule and Minimizing Risk and Uncertainties in Construction Projects. In addition, the construction progress is swiftly identified, with a direct and visual method, instead of the traditional bar charts [8]. Hence, the productivity can be improved. Finally, 4D BIM is considered as an additional management asset that offers an innovative promotional advantage comparing to other companies, for instance, in tender periods.
Challenges and Barriers
As in every breakthrough there are challenges that need to be addressed in order to achieve a successful implementation. One of the most important prerequisites is the initial investment cost that is required. The set up of 4D-planning considered a relatively expensive investment at the beginning both in terms of software and implementation. Although, the final result expected to compensate the company [2]. Research have shown that the successful implementation of 4D-planning, results into 5% savings in cost growth, 4% savings in schedule growth and 65% reduction in rework [10]. However, companies still seem to hesitate due to lack of experience and knowledge pertaining to BIM technology [3]. Furthermore, it worth noting that 4D-BIM cannot improve the quality of a project planning if the initial planning competences of the corresponding team are lacking.
Additionally, common targets need to be decided at the beginning of the project, creating a basis concerning the Level of detail of the model. Even if the AEC industry convinced to develop a better communication scheme, there are interoperability problems due to the different tools that the stakeholders use to create the model. An integral part of this chain is the creation of standards. The lack of determination concerning the required level of detail, the type of the exchanged BIM files and of a common process than need to be followed for information exchange, impedes the efficiency. Little did we know regarding limitation and barriers of 4D BIM, by virtue of the fact that only few surveys have been conducted specialized on this topic [10]. Considering the limited research, a summation of the expected barriers is listed below[10]:
Expected Barriers in Projects | ||
---|---|---|
Availability of competent staff | Cost of software | |
Cost of implementation | Prevailing perception of lack of benefits for parties involved | |
Limited universal use within projects | Software interoperability issues | |
Insufficiency of coding protocols for objects within the models' deficiency | Luck of coding standards for coding BIM software | |
Lack of integrated models | Time consuming [11] | |
Unrealistic cost for small projects [11] | Difficulties on keeping the models always updated in large and complex projects [11] |
4D-Planning and Lean Construction
Location-Based Scheduling
Location Based Scheduling (LBS), is a location-based technique of scheduling and planning the workflow in construction projects[12]. It is considered a promising alternative to activity-based scheduling method, such as CPM, combining the time of an activity with the location that this activity is expected to take place. Different techniques of LBS already exists, such as ‘Line-of-Balance’, ‘Flowline’, ‘Construction Planning Technique’etc. but their use remain limited.
Research revealed that the value of LBS, can be reinforced, implementing the 4D oriented planning approach. 4D-models offer a spatial insight in planning of construction activities that cannot be achieved for instance, if 2D drawings combined with the the LBS method [12]. The sequences of construction activities can be analyzed, taking into account the work crews, reducing time, conflicts and location inaccessibility[7]. Considering that LBS requires a location break down, which is a quite challenging process especially in large and complex projects, 4D simulation can identify the overlapping, in several locations,of the building elements [12]. However, the successful application of this combined method is demanding, as the different parties have to early decide and agreed in a location decomposition and the building elements need to be designed in pieces following the real-time construction process [7]. Last but not least, 5D BIM can be incorporated for quantities take off, creating a complete overview of the project. Figure 5, shows an overview of the described integrated process as captured from VICO software.
Last Planner System
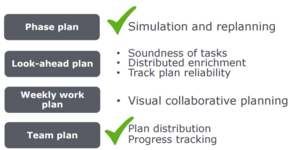
The Last Planner System in Construction Projects is part of the Lean construction approach, inspired by Lean manufacturing. It is a practical method that aims to enhance performance[14] minimizing the waste and inefficiency. The increase of managers' effective cooperation is a target that achieved through four project planning levels; the Master plan, the Phase schedule, the Lookahead plan and Commitment planning [14].
A research was conducted in order to identify how BIM supports LPD method. Two case studies were compared, the one was using LPS and the other has integrated LPS and BIM [14]. It was confirmed that in the second case, the comprehension of project progress was significantly increased among the parties. The amount of Request for information applications was decreased as well. Furthermore, current studies have shown that 4D planning provides multiple benefits in each phase. Figure 6, presents an overview.
Tools
The following tools can be used for linking the 3D model with the schedule [8].
Additionally, MS Project Professional can directly be linked to BIM software like Revit and extract the required information.
Reflection
Summarizing the aforementioned, BIM came to revolutionize the work-flow in the AEC Industry and Time Management is part of it. Through the implementation of standards and specifications the process can smoothly developed and the final product will be a provision of high quality services to the client. 4D Planning, optimizes the way of communication, contributing to an insight understanding of the schedule through simulations for all the different parties involved. The significant advantage is the ability to examine what-if scenarios of different sequence of activities and choose the most appropriate one. Furthermore, the efficient creation of a project schedule utilizing 4D BIM, affects the total cost and time of execution of the project, improves the time needed for decision making and collaboration, enhances site and safety management, procurement and resolve conflicts and clashes while the planners have the visual advantage to identify inconsistencies and errors in the time schedule easier. The linkage with the other scheduling practices creates an effective combination that reinforces the planning process and may achieves the maximum clients satisfaction.
Currently, this visualization method is still at the early phase of adoption since the barriers and challenges regrading cost of implementation, competent staff, lack of integrated models, and these are only some of the argues, make managers to hesitate about it. Further investigation needs to be made and people should be convinced about the positive impacts on this field.
References
- ↑ Winch, G. M. (2010), "Managing Construction projects". Second edition
- ↑ 2.00 2.01 2.02 2.03 2.04 2.05 2.06 2.07 2.08 2.09 2.10 2.11 2.12 Eastman C., Teichholz P. Sacks R. and K. Liston (2011). "BIM Handbook". Second edition, John Wiley Sons, Inc. United States of America"
- ↑ 3.0 3.1 Barry J. Gledson, David J. Greenwood, (2016). "Surveying the extent and use of 4D BIM in the UK". ITcon Vol. 21, Gledson & Greenwood [URL: http://www.itcon.org/papers/2016_4.content.02642.pdf]
- ↑ National Institute of Building Services (2014). "Frequently Asked Questions About the National BIM Standard-United States, National Standards-United States". Pat. [URL: https://web.archive.org/web/20141021154645/http://www.nationalbimstandard.org/faq.php]. Retrieved on 9 June 2017.
- ↑ 5.0 5.1 5.2 Dawood, N. and Sikka, S., (2006) "The Value of Visual 4D Planning in the UK Construction Industry".University of Teesside, Middlesbrough
- ↑ 6.0 6.1 COBIM Markku Jokela, Tuomas Laine Reijo Haanninen (2012). "Common BIM Requirements 2012, Use of Models in Facilities Management".
- ↑ 7.0 7.1 7.2 7.3 7.4 7.5 AU Workshop, Autodesk Univercity. "4D Simulation and Construction Planning". [URL: http://auworkshop.autodesk.com/library/bim-curriculum-construction/4d-simulation-and-construction-planning], (Retrieved on 12 June 2017)
- ↑ 8.0 8.1 8.2 8.3 8.4 8.5 acePLP, "Basics of 4D BIM". [URL: http://www.aceplp.com.sg/bim-cad/4d-bim-services] (Retrieved on 10 June 2017)
- ↑ 10.0 10.1 10.2 10.3 S. M. Ahmed, H. H. Emam AND P. Farrell, (2014). "Barriers to BIM/4D Implementation in Qatar". 1st Int’l Conference on Smart, Sustainable and Healthy Cities [CIB-MENA-14, Abu Dhabi, UAE] [URL: file:///C:/Users/PC/Downloads/BIM%204D%20Barriers.pdf]
- ↑ 11.0 11.1 11.2 Mohamad Kassem, Trevor Brogden, Nashwan Dawood, (2012). "BIM and 4D planning: a holistic study of the barriers and drivers to widespread adoption"
- ↑ 12.0 12.1 12.2 Jongeling, R. & Olofsson, T (2006). A method for planning of work-flow by combined use of location-based scheduling and 4D CAD. Luleå University of Technology.
- ↑ Skeie G., 2017. "Last Planner Powered By 4D". Part of Synchro Conference presentation (URL: https://cdn2.hubspot.net/hubfs/209864/Articles%20and%20Resources/Gunnar%20Skeie%20Last%20Planner%20Powered%20By%204D.pdf) "
- ↑ 14.0 14.1 14.2 Toledo M., Olivares K., González V., (2016). "Exploration of a Lean-BIM Planning Framework: A Last Planner System and BIM-Based Case Study". Boston, MA, USA
Annotated bibliography
- 1. Winch, G. M. (2010), "Managing Construction projects". Second edition
- Summary: The book presents a holistic approach of construction management from inspection to completion. The basic principles of construction project management are presented along with different tools and techniques that aims to improve construction performance. The use of information and communication technologies is also a point of interest in the book.
- 2.Eastman C., Teichholz P. Sacks R. and K. Liston (2011). "BIM Handbook". Second edition, John Wiley Sons, Inc. United States of America
- Summary: The book investigates and presents a new approach of designing, constructing and handling facilities management through a revolutionary process called Building Information Modeling. It explains how BIM implementation possessively affects the life-cycle of an activity comparing to other traditional approaches, providing an insight understanding of BIM value in AEC industry.
- 3.Barry J. Gledson, David J. Greenwood, (2016). "Surveying the extent and use of 4D BIM in the UK". ITcon Vol. 21, Gledson & Greenwood
- Summary: This report investigates how 4D BIM, when supporting the existing planning techniques, improves project delivery and time schedules. A survey was conducted in the UK in order to identify to what extend 4D BIM is currently used and the predominant perceptions regarding its value. The study presents the areas where 4D BIM considered a more effective tool, its benefits and barriers.
- 4.Dawood, N. and Sikka, S., (2006) "The Value of Visual 4D Planning in the UK Construction Industry".University of Teesside, Middlesbrough
- Summary: This paper investigates how 4D planning enhances project performance. A set of non-financial Key Performance Indicators is developed in order to determine 4D performance not only in quantitative but also in qualitative levels.
- 5.S. M. Ahmed, H. H. Emam AND P. Farrell, (2014). "Barriers to BIM/4D Implementation in Qatar". 1st Int’l Conference on Smart, Sustainable and Healthy Cities [CIB-MENA-14, Abu Dhabi, UAE]
- Summary: This conference paper, through surveys conducted in Qatar construction industry, reveals the current consciousness and the level of knowledge and skills regarding 4D planning. It also focuses on identifying the possible challenges and barriers od 4D BIM implementation.
- 6.Mohamad Kassem, Trevor Brogden, Nashwan Dawood, (2012). "BIM and 4D planning: a holistic study of the barriers and drivers to widespread adoption"
- Summary: The paper provides a holistic map of the challenges and barriers of 4D BIM implementations. A survey of contractors and consultants from the UK was conducted in order to address the missing linkage between technology, construction industry and processes.
- 7.Jongeling, R. & Olofsson, T (2006). A method for planning of work-flow by combined use of location-based scheduling and 4D CAD. Luleå University of Technology.v
- Summary: This report suggests that the combination of 4D CAD and location-based scheduling enhances and reinforces both of these methods, adding extra value on them.
- 8.Skeie G., 2017. "Last Planner Powered By 4D". Part of Synchro Conference presentation
- Summary: The presentations is part of the Synchro Conference, where the Last PLanner System is presented; especially its association with 4D BIM is depicted. Examples of LPS simulations are also part of the presentation.
- 9.Toledo M., Olivares K., González V., (2016). "Exploration of a Lean-BIM Planning Framework: A Last Planner System and BIM-Based Case Study". Boston, MA, USA
- Summary: Two similar construction projects were used, following different planning approaches. More specifically,in the one case study only Last Planner System was used while on the other, Last Planner System together with BIM. The two cases were compared regarding meetings, request for information and LPS metrics and the final result had shown that the combination of LBS and BIM, facilitates the workflow of the project.